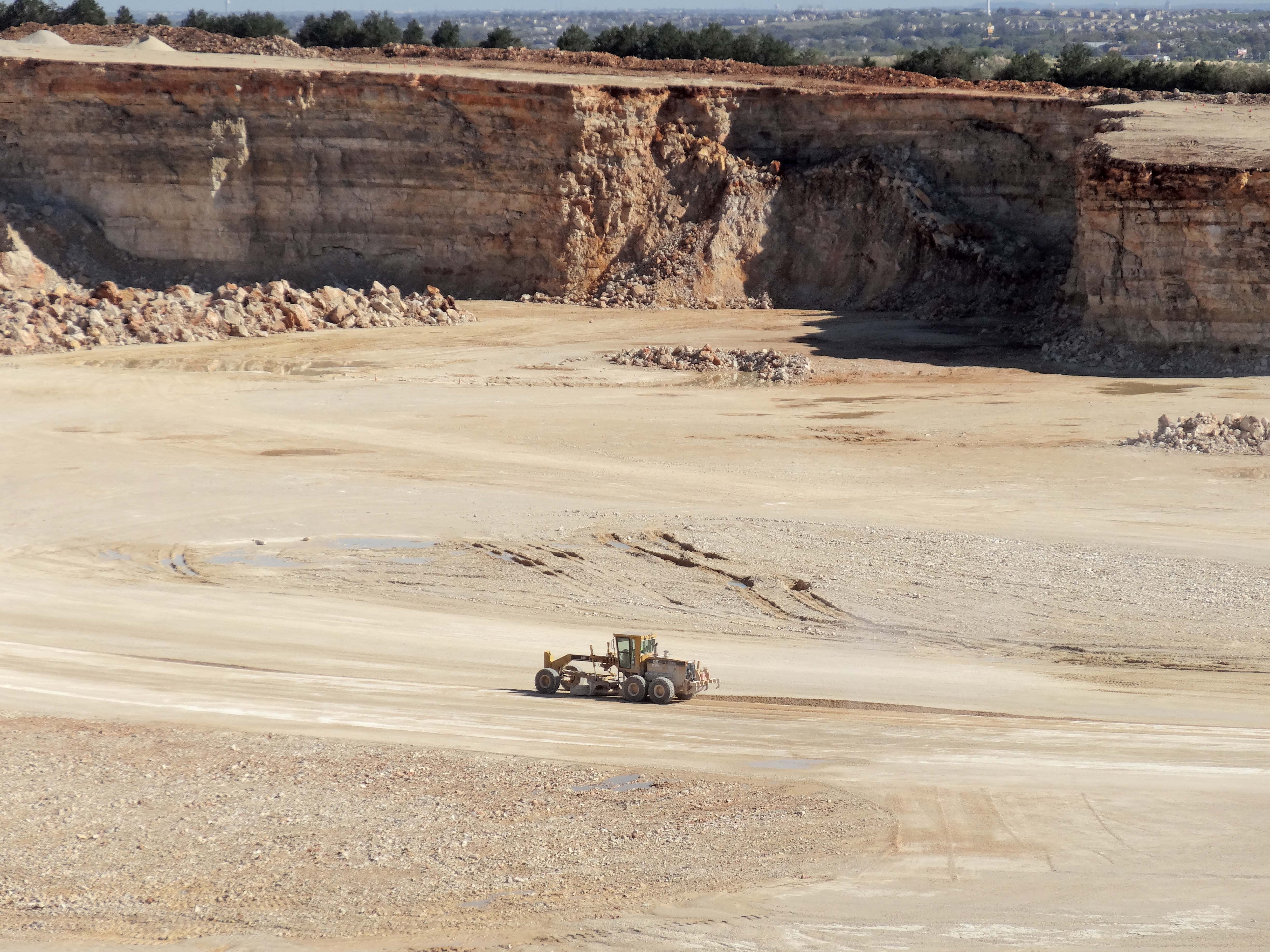
More than 130 quarry operators and contractors from across the world came to San Antonio, Texas, USA for the 10th Sandvik Construction-Dyno Nobel Quarry Academy from 17-19 November 2015. Aggregates Business editor Guy Woodford joined those taking part
Watching the constant stream of trucks and other vehicles going in and out of
Processing up to 250,000tons/week (11.5 million tons/year) of limestone aggregates, with a load out of up to 1,000 trucks/day, and a mining operation up to 200ft deep across three levels, the late 1960’s opened site was acquired by Cemex in 1994 – with the Mexican construction materials’ giant’s ongoing investment in the Quarry supporting its huge aggregate production flow. Covering an impressive 2,400 acres, Balcones Quarry is also packed with the latest materials processing technology – including two Sandvik CH660 cone crushers.
It’s the third and final day of the 10th
The Quarry Academy’s fascinating practical afternoon session had been preceded by two-and-a-half days of presentations and workshops centred around optimising a quarry operation’s planning; crushing; loading and hauling; drilling and blasting; and screening and sizing. Meanwhile, safety, productivity, cost minimisation, and profit were the key overarching themes of the landmark 10th anniversary event staged at San Antonio’s Omni La Mansion del Rio Hotel.
Among those taking in the impressive Balcones Quarry operation was Dustin McAuley, 35, Site Manager for Mainline Sand & Gravel, based in Vancouver, British Columbia, Canada, who was attending his first Quarry Academy. “I’ve got lots out of it. I’ve been a site manager since April and I’ve been learning about all the operation costs. I’ve learnt from the Academy that if you’ve got a great drilling and blasting process, you’ll get great sales. I’ve found everyone delivering the presentations and workshops to be very knowledgeable. The speakers have been involved in quarrying for years.”
Of Balcones Quarry, McAuley added: “It’s awesome and it’s highly efficient – which you can tell by just looking around.”
Kyle Brashear, 26, a Management Training Associate at Martin Marietta, based in Raleigh, North Carolina, USA, was another Quarry Academy attendee enjoying the Texan sun-soaked afternoon session at Balcones Quarry. “I’ve been very impressed with the Quarry Academy so far. I’ve enjoyed the diversity of the speakers. There’s been very little product pitching. For me being new to the industry, it’s been good to come here and learn a bunch of expertise. For me, the plant optimisation presentations and the Lean Six Sigma [management tools and techniques] presentation are a good take home.”
On Day One of Quarry Academy and in a presentation on the Chemical Crushing concept, Bill Hissem, Sandvik Construction’s Senior Mining Engineer in North America, and Larry Mirabelli, Senior Manager – Explosives & Blasting Technologies at Buckley Powder, a joint venture company of Dyno Nobel, talked about how the latest advanced technologies combined with improved design and disciplines now offer a great way for drilling and blasting to improve a quarry or mine’s productivity at the primary crusher, while also aiding waste minimisation at both the pit and plant. Advanced technologies highlighted by the pair included cutting-edge blast design software, improved survey equipment, more accurate and precise rock drills, and state-of-the-art bulk emulsion explosive loading systems.
Hissem and Mirabelli stressed how adopting Chemical Crushing can, crucially, control and influence rock particle size distribution, while, at the same time, adhering to the normal drill and blast aims of achieving zero harm, full regulatory compliance, controlled boundaries of blast/excavation, uniform breakage and winning material that is easy to dig, load, haul, dump and feed.
Also on Day One, David Nus, Global Key Accounts Management for
One example cited by Nus and Spake was how one of five Volvo L110 wheeled loaders at a sand plant operation was using 1.2 gallons/hour more fuel than the others. This was costing the business an extra US$9,600 (€9,035) more each year, and $48,000 (€45,170) additional cost over five years. After agreeing an action plan with their Volvo equipment dealer, the sand plant’s management and the dealer checked the machine and its operating conditions, and provided operator training. This led to the wheeled loader’s fuel burn being reduced to the fleet norm, without any reduction in productivity.
Nus and Spake also highlighted the significant cost savings that can be had by reducing loading and hauling model idle time. The pair cited a typical case of a model racking up 2,000 engine hours/year, despite the model spending 50% of its time idle, leaving only 1,000 hours worked. The model would require 20 x 500 hour servicing or 40 if at 250 hour intervals. Compared to this was an improved scenario of a machine racking up just 1,500 engine hours/year, while reducing idling time to 33% and achieving the same 1,000 hours worked. The reduced machine wear would see the model require only 15 x 500 hour servicing or 30 if at 250 intervals. The reduced fuel use and less model wear, preserving residual value and engine and component life, would, said Nus and Spake, be worth at least $35,000 (€32,940) a year.
On Day Two of Quarry Academy, George Fensome, Sandvik Construction’s Area Manager for the Americas, gave a presentation on understanding the dynamics and function of HSI and VSI crushers in order to reduce waste, lower energy consumption, and optimise productivity. Fensome highlighted how due to advances in metallurgies, traditionally limestone and other less abrasive rock-suited HSI crushers can now handle more abrasive rock, increasing their application potential, while also offering 10 to 1 reduction ratios – far greater than the usual 3 to 1 of jaw crushers. Fensome also stressed how $37 (€34.80) an hour in energy costs can be saved by quarry operators and contractors through single rather than two stage crushing, by reusing their HSI primary crushers rather than automatically sending primary crushed material to a secondary cone crusher. Energy conservation will become increasingly important in the future, said Fensome, as “we are moving towards a sellers’ market for many sources of energy”.
Of VSI’s, Fensome praised their suitability as a quick and efficient third or fourth stage crusher for hard or soft rock applications. The VSI, said Fensome, was also ideal for producing manufactured sand, of which there is an increasing need due to the depletion of natural sand resources. Fensome also highlighted how VSI processed product gradation remains constant, even when rotor parts wear.
Also on Day Two, Daniel Daoust, Sandvik Construction Crushing & Screening Sales Manager responsible for product and dealer network in the US, Canada, Mexico, Central America, and the Caribbean, gave a presentation titled Making the Right Stuff: Screening & Sizing. Daoust spoke of how the correct selection, installation and maintenance are critical to product quality and the operation of a safe and efficient plant. He offered advice on practical controls, troubleshooting tips to avoid problems such as pegging, binding, abnormal wear at a screen’s discharge end, and stressed how side feeding should be avoided as it encourages uneven spread across a screen deck.
Other presentations over the course of the three days included Quarry Planning & Metrics; Mobile Crushing & Screening, and A Reality Check – an often entertaining two-part take by Alabama-based lawyers Mike Bowling and Jeff Friedman on the serious issue of how quarry operators can best defend potential blast management-linked litigation by investing in regular seismograph tests and keeping accurate and thorough blast management records.
Popular workshops run on Days 2 and 3 of Quarry Academy included Drilling & Blasting in Depth; Crushing & Screening Do’s & Don’ts; Putting the Plant Together – using Sandvik’s PlantDesigner software; and Process Improvement – Tools & Methods.
Meanwhile, many Quarry Academy attendees took part in Volvo excavator and Sandvik drill simulator challenges during breaks in presentations and workshops over the course of the three-day event.
For the 10th anniversary Quarry Academy, the traditional key note address was given by Keni Thomas. The popular country music singer shot to fame as a former United States Army Task Force Ranger involved in Operation Restore Hope in Somalia and the Battle of Mogadishu, immortalised in the book and movie Blackhawk Down. During his gripping recollection of his unit’s part in the famous battle, Thomas stressed the importance of teamwork to achieving success and how any organisation or business, such as a quarrying operation, is only as good as its weakest link.
Summing up the key aims of the Sandvik Construction-Dyno Nobel Quarry Academy since its formation, Jeff Heinemann, Vice President, Construction for Sandvik Construction North America, said: “Since 2005 Sandvik Construction and Dyno-Nobel in the USA have offered the Aggregates Industry an opportunity to educate team members to safely increase productivity, minimise cost and increase profit in their operations.
“As the industrial boom began its historical climb from 1945 to the unprecedented drop in 2008, business was good and the day to day challenges were not as severe as we are seeing today in the ‘New Normal’. The New Normal market requires that we focus on key metrics for a predictable and sustainable outcome. Value Chain Management - Planning, Drilling, Blasting, Load & Haul, Crushing, and Screening & Sizing – is key to this process. All interconnected, these are the key components essential to a predictable and planned outcome. Businesses must be able to adapt and connect these operational links to economic links. Like a symphony, all items in the value chain must be properly balanced for effect, success and overall sustainability.”