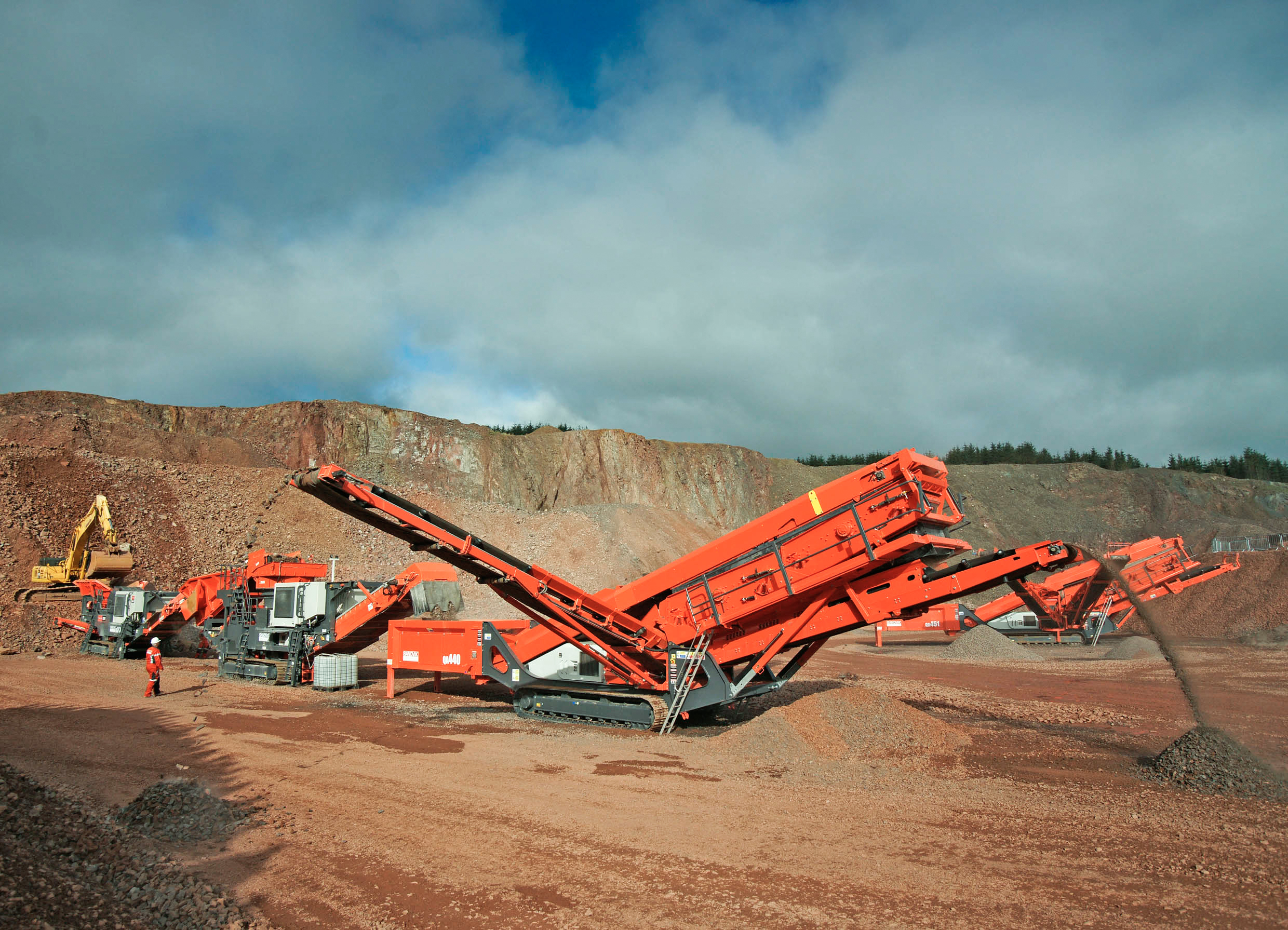
As the demand for crushed rock in many parts of the world shows increases, equipment manufacturers are responding. Patrick Smith reports.
The recent unveiling of new highly productive and fuel efficient machines bears testimony to this.
Major shows such as
Following his company’s recent international open event, attended by customers and distributors from 21 countries, Colin Clements,
It introduced three new models, the Premiertrak 300 jaw crusher, the Trakpactor 320SR impact crusher and the Warrior 2100 screen, as well as showcasing well-established products.
Similarly, over 100 customers and distributors joined
Earlier in the year
Meanwhile, at the Sandvik event, visitors saw how the S-type gyratory cone crusher, proven in stationary applications for over 30 years, has now been incorporated into self-contained, diesel driven, track-mounted plant.
The two models marking the launch of the new mobile range comprise the larger QS441, 56tonne unit featuring the CS440 cone, and the more compact 36tonne QS331, incorporating the CS430 cone crusher.
“The launch of the new mobile S-type gyratory cone crusher range, which will enable customers to benefit from Sandvik’s expertise in cone crushers, but now in a mobile platform, required a launch event to match these exciting developments,” says Sandvik.
In advance of its launch, the Powerscreen Premiertrak 300 crusher was tested extensively in the UK, including at J. Gourley and Sons’ site in Northern Ireland where medium hard quarry rock is crushed for local building contractors and farmers.
“As a family-run company we are a relatively small team and any time and money savings can make a big difference,” says company representative Thomas Gourley.
“When producing 63mm road base material it gave us an excellent tonnes per hour output to fuel efficiency ratio.”
He claimed that in terms of fuel consumption the plant outperformed some crushers by around 30%, in addition to the time saved by not having to stop production to refuel.
“In this industry saving time is saving money, allowing us to do what we do best, keep producing quality material to meet our customers' needs.”
He said the size of the machine for transport (weighing approximately 32,400kg and featuring two-speed tracking for optimum mobility) was another “benefit” and with the same output tonnage and finished product quality as some other crushers, up to 70% in transport costs was saved when moving the Premiertrak 300 between sites.
Powerscreen says the Premiertrak 300 crusher uses a 1,000mm x 600mm jaw chamber and is capable of producing up to 280tonnes/hour of crushed material, having been developed with the option of a vibrating grizzly feeder or a large fully independent hydraulically driven pre-screen, which improves fines removal and reduces chamber wear costs for the customer.
To coincide with the independent pre-screen feature, an optional hydraulically folding extended side conveyor with a stockpile height of 3.1m has been added to the machine to improve stockpile capacity.
The new bypass chute design incorporates a flap gate to allow the operator to switch between using the side conveyor or sending the material to the main belt without the need to fit a blanking mat on the bottom screen deck.
The Powerscreen jaw chamber has hydraulically adjustable closed side setting (CSS), which can be adjusted in minutes by one operator. The hydraulic release chamber option (Premiertrak R300 crusher) incorporates the proven hydraulic release mechanism to allow the chamber to ‘dump’ and pass uncrushable material which is ideal for recycling applications. A hydraulically adjustable deflector plate is also an option for recycling applications, and the machine’s new lock-out function allows the operator to work in hard rock quarry applications with the same chamber.
The new hopper’s complete hydraulic fold and lock system removes the need for manual wedges and can be raised/ lowered from ground level removing the need to work at height and providing rapid setup times. Full hopper extensions are an option to further increase capacity.
The Premiertrak 300 jaw crusher features a hydraulically lowering product conveyor with 3.5m discharge height for easy removal of trapped metal in recycling applications and features full tunnelling to reducing snagging of rebar.
An intuitive control panel allows machine settings to be changed easily and provides excellent diagnostics for fault finding if required.
The Premiertrak 300 can be powered by a Tier 3/Stage IIIA-compliant Cat C9 Acert 205kW engine or a Tier 4 Final compliant
In common with other manufacturers,
Crushing contractor Banner Contracts put its two new Lokotrack LT106 mobile crushing plants into operation at the quarry, where it does all the crushing, in December 2012.
“Each one of our LT106s consumes 9litres less fuel per hour than its predecessor LT105. That’s a 35% difference,” says Jo Banner, company director.
After six months in operation at the quarry, the machines’ fuel consumption is said to average around 15.5litres/hour. According to Jo Banner, these figures make them the most fuel-efficient mobile crushers in his company’s fleet.
“Not only have fuel prices increased, they now vary considerably in a matter of days, meaning that fuel costs are hard to predict,” says Banner.
The quarry produces kiln feed, which onsite customer
These products require a chemistry consistency within the clients set parameters: low values of silica, sulphur and alumina, with a minimum value of magnesium oxide of 18%. The quarry also makes several co-products, including sub-base, capping, and aggregates and sand, for concrete making.
“The nature of the process lends itself to having multiple smaller plants instead of one large one,” says Jo Banner.
“Lokotrack is good on tracks and easy to move. It only takes around 30 minutes to move the machine, tidy up the spot and start crushing again.”
Banner Contract placed an order for a third Lokotrack in May 2013, and this is in operation at one of the company’s other customer sites.
The new tracked Terex Finlay I-100RS direct drive ø860mm x 860mm horizontal impact crusher with variable speed is aid to give operators high levels of fuel efficiency and production in both recycling and quarrying applications. “The robust and proven Terex chamber gives excellent reduction ratios and high consistency of product shape,” says Terex Finlay.
“The machine features an on-board 2.44m x 1.2m single-deck screen for sizing and recirculating oversize material back to the crushing chamber. The sizing screen can be quickly detached for applications that do not require resizing or recirculation of materials for further processing.”
Terex Finlay says the I-100RS features hydraulic folding of all conveyors, providing rapid set-up times and easy point-to-point moves when operating on multiple sites, while an advanced electronic control system monitors and controls the speed of the rotor and regulates the heavy-duty vibrating feeder (VGF) with integrated pre-screen to maintain a consistent feed of material into the impact chamber for optimal crushing conditions.
Material from the integrated pre-screen can be diverted to a stockpile via the optional bypass conveyor or it may join the crushed product on the main belt. The standard hopper capacity is 2.3M³ .
“Start-up time for the I-100RS is minimal, with the machine ready for crushing in less than 15 minutes. The heavy-duty crawler tracks, and optional radio remote control unit, make on site mobility very easy. A key additional benefit is the in-built hydraulic assist apron adjustment for the impact chamber,” says Terex Finlay, which has just released its 694+ diesel/electric inclined screen to dealers.
“The screen provides customers with the option of running this machine by either diesel or electric mode depending on the resources available at each particular site. In territories with wide disparities in the quality of fuel or where the price of fuel is an issue versus electricity prices the machine will also have particular advantages,” says the company.
As standard the screen uses 2 x 37kW IE2 electric motors which operate at 50Hz and are suitable for most regions. However, a 60Hz and/or IE3 set-up can be configured to suit particular regions such as the USA.
“The intuitive and user friendly electrical and hydraulic system allows the customer to switch between diesel and electric mode at the flick of a switch. The primary operation and controls of the machine remain the same regardless of the selected power.”
Featuring a 6.1m x 1.52m triple-deck inclined screen giving a total screening area of 28m², the screenbox offers quick wedge tensioning, access holes and bottom deck hydraulic tensioning system to reduce time required for mesh changes.
“This is the first diesel/electric machine to be built by Terex Finlay, which will ultimately culminate in the ability to offer customers the option to operate a fully electric-powered crushing and screening train comprising the J-1175 jaw crusher, C-1540 cone crusher and 694+ inclined screen,” says Terex Finlay.
One of
The all-new mobile jaw crusher, specially developed to meet the requirements of contract crushers, was presented at the Bauma 2013 exhibition.
“Easy transport and plant versatility are important for this target group. Furthermore, such plants must also be extremely efficient and operating costs must be kept as low as possible,” says Kleemann, a
The plant is primarily used in the recycling of demolition material.
“We mainly process mixed rubble and concrete, some of which is strongly reinforced. In such applications the plant simply has to complete its task reliably," says managing director Nadine Grathwohl.
“Some of our applications often contain substantial amounts of fine material, so effective pre-screening is particularly important to us.”
The company selected the Z version, which is said to be ideally equipped for the task thanks to its active double-deck pre-screen.
“We feel we are in the best possible hands with the responsible sales offices of Wirtgen Windhagen,” says Nadine Grathwohl.
In another application, the Décremps company, based in Amancy, France, has been operating in the structural and civil engineering field of for over 40 years and is also active in earthwork and demolition. This mainly involves the fast and efficient crushing of concrete.
In most cases, feeding material with a maximum feed size of 600mm is crushed to a final product of approximately 0/60mm. Because the material often has a high iron content, it is important that there is sufficient space under the crusher to prevent blockages caused by the exposed reinforcement bars. The MC 110 offers a generous clearance and if a blockage should occur, this area is very easily accessible.
In south-west England, Glendinning, a supplier of concrete, asphalt and aggregate materials for many years, operates two quarries, and was searching for a new mobile jaw crusher in the 1,100mm class.
As a completely new development, a plant demonstration of the MC 110 was arranged and carried out.
“The test material was very coarse sandstone, in part sticky. In the directly following crushing stage it was further processed by a cone crusher for subsequent screening of different end products. Because it was followed by the cone crusher, very good pre-screening was particularly important,” explains Michael Schwarz, Kleemann sales manager Europe.
After demonstration, Glendinning bought a plant of this type a few weeks later.
Austrian mobile crushing and screening machine manufacturer dsb innocrush is again highlighting its new Innodrive, a drive system at present used on the company’s smallest machine, the innocrush 30.
The crusher, with a rotor diameter of 1m, is directly driven with V-belts by an 186kW
The innocrush 30, which weighs under 30tonnes, is said to have an output of 300tonnes/hour.
Announcing its biggest mobile screen to date,
“This is yet another step up to the mark in terms of machine size and the overall results are very good,” says Martin Quinn, Anaconda operations director.
“Demand is driving us to design and manufacture larger units and so far, our distributors have supported that demand with sales orders.”
The SR514 has a 14x5 triple or double-deck screen; a 14ft (4.2m) feed hopper; main conveyor and either three or four hydraulically folding stockpiling conveyors. The third/fourth product transfer is done by way of a reversible transfer belt to improve efficiency and remove the build-up problems.
Weighing almost 29,000kg for the triple deck, the unit is powered by a Caterpillar 4.4 water-cooled engine developing 75kW.
According to Anaconda, the screen can be running within 45 minutes with hydraulic controls to aid the setting of all conveyors, screenbox and landing legs.
“The SR514 has variable speed controls to set the belt speeds to suit each application and the screenbox can be set between 20-34ᵒ to ensure maximum screening efficiency,” says the company.
French screening for Hercules trommel
The customer has been operating a
The new HT182 has been installed at another site and is helping to produce clean, sized products from a 900mm contaminated feed material. The recovery of more stone from the feed material is also reducing waste in the quarry. This gives added value to the customer’s existing quarry reserves for future years to come.
The HT182 is rated up to 500tonnes/hour and is producing two sizes plus oversize from the feed material. The trommel is mounted on a steel frame with access platforms on both sides for safe routine inspections, and the large heavy-duty feed hopper is receiving material directly from a dump truck.