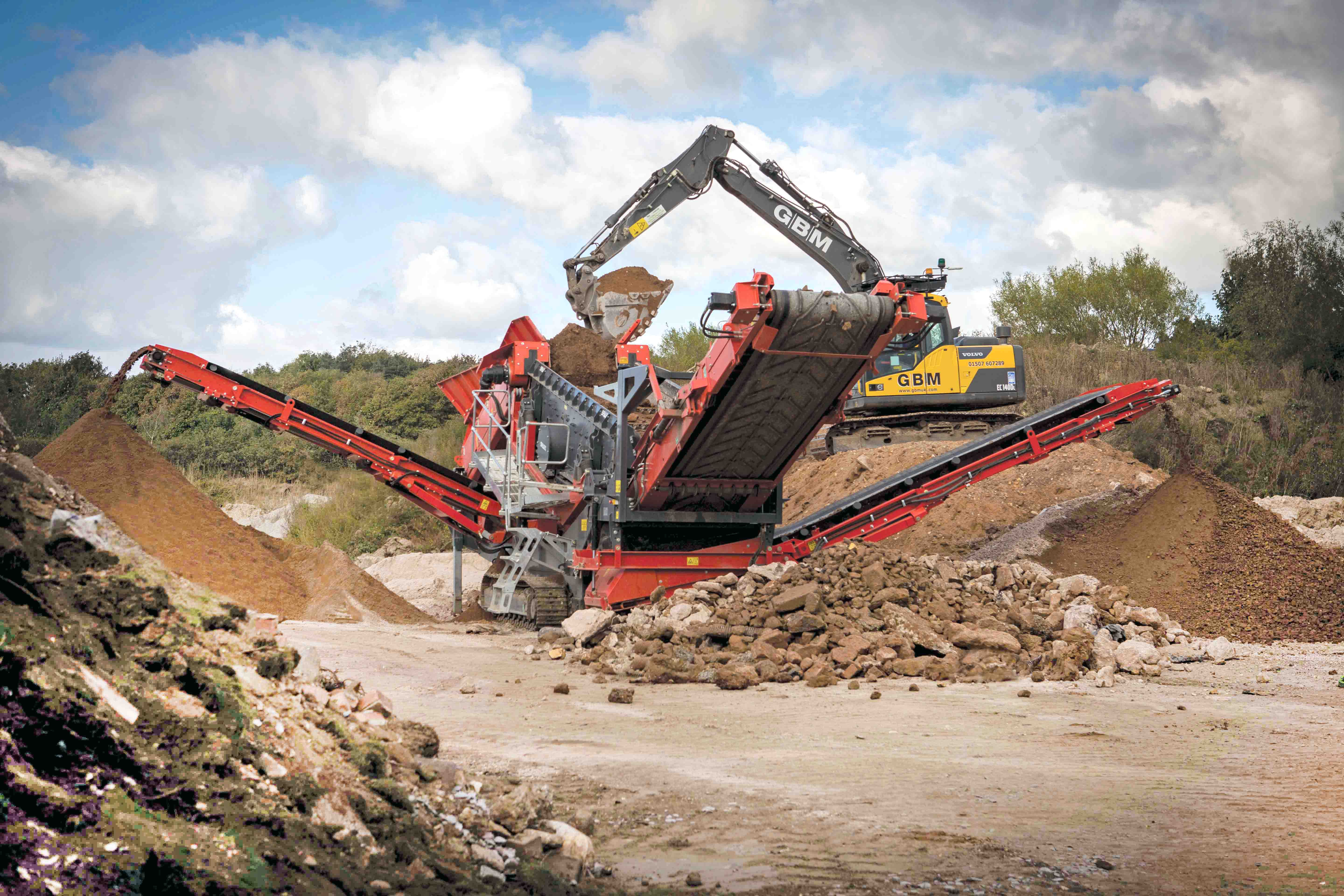
RSSA German company is using the first-of-its-kind crushing plant to produce high-quality aggregates from limestone. Patrick Smith reports.
There are a variety of elements that go into quarrying, but it is the final or end product by which many are judged.This process is down to the crushing and screening equipment, and how it is used, with operators having an array of recipes at their fingertips.
For example, the crushing of especially hard limestone to a required size and quality with a constant capacity, and moving it smoothly via mobile conveyor may be seen as a challenge.
For German company, Lanwehr Naturstein in Sauerland, the end product range contains 50% of 0-45mm road base and 50% of so-called Edelsplitt aggregates grades, crushed and screened to different sizes for concrete and asphalt materials.
To achieve this, the company is using the first fully-electric
Since 2007, the company’s primary crusher has been a Lokotrack LT125 jaw plant (now removed), connected to a LL12 series mobile conveyor.
“We are very pleased with our new LT130E. It has 15% more capacity than its predecessor and seems to be able to crush almost any sized feed. We used to have to hammer oversized boulders for at least an hour per day, but not any more, thanks to the C130 jaw’s large intake,” says Thomas Lanwehr, managing director of Lanwehr Naturstein.
“The fully electric drive using external power clearly adds to our competitiveness among the regional aggregates producers. And by using electric power, we receive a tax reduction of €6,000-7,000/ month.”
From the mobile conveyor, material is transported to the stationary plant via a 1km-long field conveyor, and by mid-2016, after crushing over 10 million tonnes of hard limestone, the switchover from the old to the new primary crushing plant was made.
The final cubical shape of the products is produced using Metso’s Barmac vertical shaft impact crusher.
“The Metso IC process steering [on the LT130E] is modern and easy to use. The C130 crusher chamber geometry is well-designed, providing a good product shape for further processing. The hydraulic setting adjustment of the jaw is safe and quick to use for keeping an accurate setting,” says Thomas Lanwehr.
Meanwhile,
The first ten Hammer units (a crusher for roadbed and backfill) are at work in different countries, including Albania, Greece, Turkey, Tunisia and Peru.
The machine is equipped with a crawler truck capable of working on steep slopes of up to a 70% gradient, and the company says the Hammer crusher is able to crush large pieces of rock and turn them into fine sand, which is then deposited directly in the excavation.
“The main features of our new Hammer are the rate of production that can reach as high as 150m³/hour, without the presence of an expert operator; the small size of the output, with minimum granulometry of 0-15mm, and maximum rock input size of up to 500mm” says Marco Laurini, President of Laurini Officine Meccaniche.
In the UK, a recycling company has taken delivery of a
“Soil production accounts for 75% cent of saleable products from our Doncaster site, but we’ve previously been forced to stop production between November and February because our machines kept clogging up with wet material,” says Paul Waite, area sales manager at GBM UK.
“The Terex Finlay 883+ Spaleck copes well with the soil, even in wet weather, and that means we’ll be able to screen constantly throughout the year with increased throughput as well.”
The company’s recycling centre turns material brought to the site into oversize, 75mm-10mm and sand.
The plant, which has a processing range of 1mm-120mm, has a two-deck screen with a rubber mat top deck and state-of-the-art Flip-Flow technology below.
Belgian recycling specialist Gyro, is using its
“With the combination of a MC 125 Z and the MF 16 S we achieve the best result, with high cubicity and 30% content of fines. At the same time, we have a high hourly output of 350 tonnes,” says Guy Kempeneers, managing director of Gyro.”
The rough grain sizes of 300-900mm are used as armourstones, while finer material is crushed in the primary phase by the MC 125 Z jaw crusher, and the grain size of 0-125mm is then fed to the MF 16 S by direct loading. There, the fine material 0-4mm is thoroughly classified by the triple-deck vibrating screen and the oversize grain is crushed to 4-28mm. Both are used for concrete applications instead of gravel and sand.
Britaniacrest Recycling, with three sites across the counties of Surrey and West Sussex in southern England, has added a
Sourced from appointed distributors Blue London, the R400 features hydraulic release and a patented hydraulic crusher overload system. It is said to be ideal for Britaniacrest’s recycling applications where un-crushable materials, such as tramp metals, can enter the in-feed. The machine’s hydraulic crusher setting adjustment also provides total control of end product size.
The tracked Premiertrak R400 has an output potential of up to 400tonnes/hour with predominantly hardcore, concrete and demolition debris. It is currently processing around 3,500 tonnes/week.
The crushing process produces a variety of sized and specified end-products, largely type 1 aggregate and 6F2.
Britaniacrest Recycling runs two modern waste transfer stations near Gatwick and Horsham, capable of processing and recycling a combined total of around 480,000tonnes/year of waste and also exporting some 52,000tonnes of RDF to Germany annually.
Keestrack says that most of its crushers, screeners and stackers are available today as conventional diesel-hydraulic units, but also as e-versions with on-board diesel engines and flanged generators to supply electric motors on screens, conveyors, compressors and other components.
The company says that with a plug-in option, these hybrid plants can be externally supplied via mains, another machine in the processing line (for example, a crusher) or via a separate genset.
“The obvious reason for replacing numerous hydro drives on conventional mobile plants, and reducing with that, to a large extent, hydraulic power needs, oil volumes and pipework on machines, is direct cost-cutting,” says Keestrack.
“And indeed, Keestrack is reporting for the e-versions up to 30 % lower fuel consumption compared to the same models with modern load-sensing hydraulic systems.”
Keestrack’s 35tonne H4 tracked cone crusher, developed in close cooperation with a cone specialist, features an electrically driven cone crusher (132kW, maximum 200tonnes/hour). The hybrid version debuted at bauma 2016, and now Keestrack has presented the full-hybrid H4e. The company says that according to emission regulations both machines feature 328/346kW on-board diesels powering the 330kVA on-board generator for the crusher drive and ancillary components, such as side conveyors and magnet.
For full electric operation from mains or external genset the new H4e is equipped with an additional electric motor/hydro pump unit to supply the hydraulic driven feeder; the large after-screen module; the tracks, and all hydraulic cylinders.
“The brand-new tracked mobile jaw crusher, Keestrack B4/B4e, operates on a similar principle. Completely re-designed, it follows the successful Apollo/B4,” says Keestrack.
McCloskey International’s new China distributor, Shanghai Shibang Machinery (SBM), says it will look to increase the crushing and screening company’s presence in that country’s quarrying and construction markets, having recently acquired its first McCloskey machine, an S190 triple-deck screener.
“McCloskey has a very good reputation in the industry,” says Libo Fang, SBM’s vice general manager.
“Our customers’ needs derive from certain global trends, urbanisation and the growing demand for minerals. These are what drive us.”
Paschal McCloskey, president and CEO of