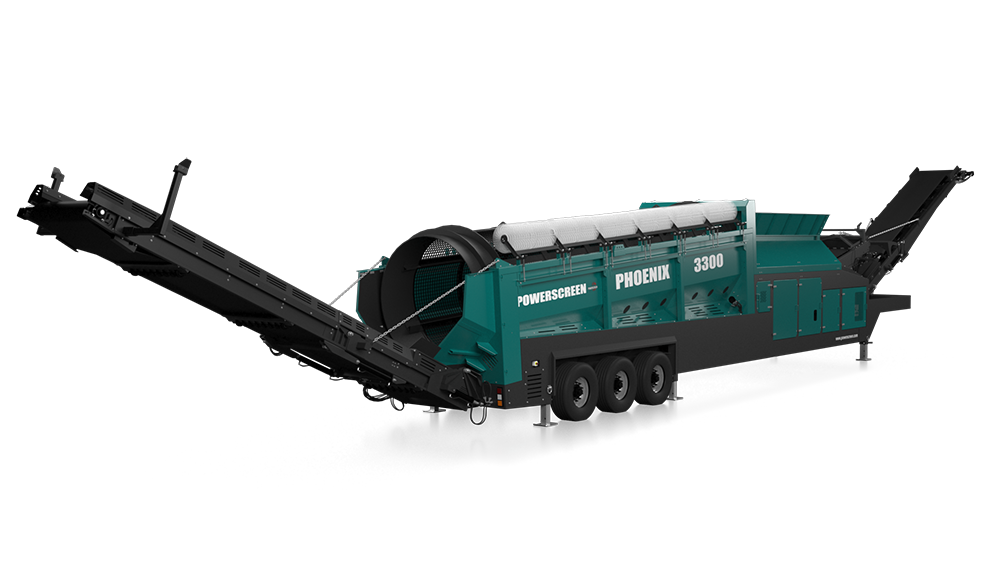
Northern Ireland-based Powerscreen is re-introducing its Phoenix mobile crushing and screening range.
Phoenix, one of the original machine ranges in Powerscreen's product portfolio, is a collection of trommel machines that are predominantly used in recycling applications such as construction & demolition (C&D) waste, wood chippings, top soil, compost and green waste.
Through the processes of screening and separation, material is extracted to create recycled useable products, resulting in increased profits for the customer while being better for the environment.
Commenting on the decision to bring back this range to the Powerscreen portfolio, Powerscreen product manager Neil Robinson said: “The global waste management market is becoming more and more prevalent as government initiatives are geared toward better environmental practices, so it is an ideal time to bring back the Phoenix range with its proven track record in recycling applications."
The re-introduced Phoenix range includes the Powerscreen Phoenix 1600, which comes in both tracked and wheeled versions, the mid-size Powerscreen Phoenix 2100 and the larger flagship Powerscreen Phoenix 3300.
The Powerscreen Phoenix 1600 tracked- and wheeled-trommel screens have been designed to provide excellent fuel efficiency and low operating costs, whilst also reducing emissions and noise levels due to the machine running at a low engine RPM. With a 4.9m x 1.54m drum, unrivalled production throughput is guaranteed due to the screening area which is the largest in its class.
Powerscreen says the Phoenix 2100 trommel screen is designed to offer unrivalled production throughput and application flexibility. The robust design with optional features such as a heavy-duty tipping grid or double-deck vibrating grid makes the Phoenix 2100 the most versatile trommel on the market today. The machine performs equally well in heavy C&D applications as it does in high-volume compost production. The 180° swivel fines conveyor, with a 5.7m discharge, means the machine can generate massive stockpiles. This swivel feature can be controlled via a radio remote while the machine is in operation, minimising downtime.
The Powerscreen Phoenix 3300 trommel screen is also designed to offer unrivalled production throughput and application flexibility. Key features include having the largest screen area within the Phoenix range, a 180⁰ swivel fines conveyor, with a 5.8m discharge and a powerful four-wheel drive system with high-performance friction grip wheels which is used to turn the trommel drum giving operators the ability to run bi-directionally. Options include a heavy-duty tipping grid or double-deck vibrating grid.
The Phoenix 3300 is claimed to be highly efficient in the separation and processing of wood chippings, top soil, compost, green waste and aggregates.
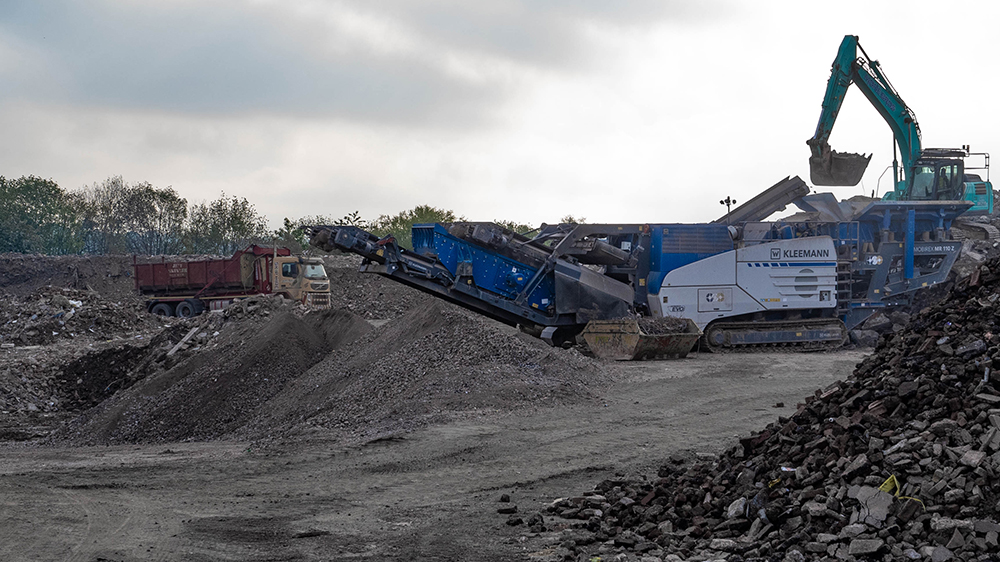
Powerscreen Pulse Intelligence is available on the Phoenix range of machines anywhere at any time, on a PC, tablet or smartphone. The system provides comprehensive information on the GPS location, start and stop times, fuel consumption, tonnages, cone settings, wear ratings, operating hours, maintenance status, engine faults and much more.
The Phoenix range is now available to purchase from Powerscreen distributors worldwide.
At Mone Brothers’ Fireclay recycling centre to the west of Leeds in North-West England, a powerful Kleemann MOBIREX MR 110 Z EVO2 impact crusher is said to be proving its worth as it’s kept busy recycling brick and concrete rubble.
With several quarries and recycling centres around Leeds, Mone Brothers has a long tradition in mineral recycling. Since it was founded in 1965, the business quickly developed from a simple plant hire company into one of the principal providers of construction materials and recycling services in West Yorkshire.
In minute intervals, dumper trucks drive into the near 2.5-hectare Fireclay recycling centre site, bringing mixed rubble from demolition work and construction sites and taking back crushed and cleaned material. On average, more than 300,000 tonnes of this material are processed here every year. While broken bricks are recycled into hardcore according to British Standard 6F2 and used primarily as a capping layer in road construction, the recycled concrete is used as a higher quality Type 1 layer for sub-base purposes.
Furthermore, Mone Brothers works a great deal with the local utility industry and supports the expansion of the electricity, water and gas network with its material. The companies deliver their mixed rubble and drive away again with recycled Type 1.
The different feed materials and required quality standards have an impact on the production process. Thanks to a higher permissible oversize grain content, it is possible to dispense with a closed circuit for 6F2 and, in doing so, increase the feed capacity. In this configuration, the MOBIREX MR 110 Z EVO2 of Mone Brothers has a capacity of 280 tonnes per hour.
For the recycled Type 1 material, the system changes its location in just a few minutes and the secondary screening unit is mounted in around 15 minutes. With the integrated oversize grain return conveyor, the capacity for this classified product is still 250 tonnes per hour while also meeting the highest standards in British road construction.
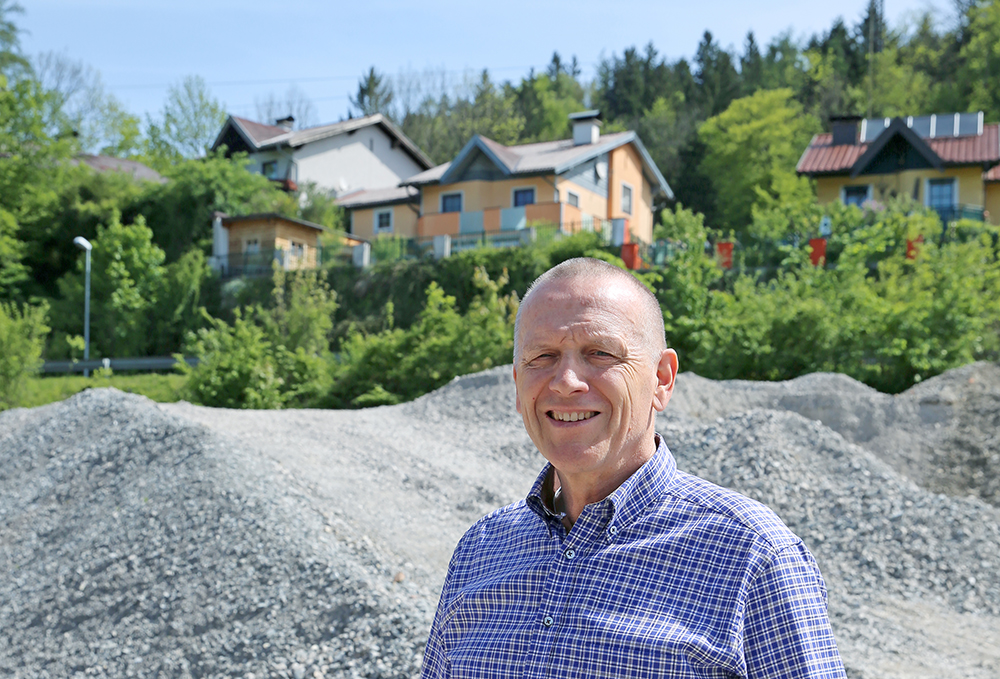
These products are typically produced in the UK with jaw crushers, and Mone Brothers also has one from Kleemann working on quarry applications. However, the decision to opt for an impact crusher for use at Fireclay recycling centre was made for a good reason.
Michael Coleman, managing director at Mone Brothers, says the final product quality has significantly increased. The impact crusher achieves a grain shape in one crushing stage that a jaw crusher could not come close to without a second crushing stage. The slightly higher fine content helps to bind the material during later use and therefore also equates to the required quantity.
In addition to product quality, the higher performance of the MOBIREX is also a highlight. While jaw crushers offer a recommended crushing ratio of 7:1 in recycling, impact crushers can achieve a ratio of 15:1 and thereby a greater feed size, which facilitates significantly higher performance.
"The output is truly mesmerising, and it has been a real benefit to the business," said Coleman.
It is therefore easy to work out why Mone Brothers replaced two of its jaw crushers with just one impact crusher. Thanks to the diesel-direct-electric drive concept of the MR 110 Z EVO2 impact crusher, this is said to reduce what were already low operating costs by another 15%.
Despite many years of cooperation and positive experiences with the aftersales service, Coleman said the decision to invest in a Kleemann impact crusher was not a matter of course. "We did try other machines but actually they could not produce enough of the product at the right speed and they were much more expensive to operate.”
The 2,750-metre-long runway at Salzburg airport has been around for almost 60 years. Following a total shutdown of five weeks, Salzburg airport opened again on 28 May 2019. RUBBLE MASTER made a considerable contribution to the general renovation with a compact crusher from the Linz, Austria-based company, enabling 8,500 tonnes of material to be crushed on site and immediately reused.
"This job was a challenge due to its tight time schedule," says Klaus Weickl, managing director of Weickl Erdbau. "We only had four weeks to complete all the work."
The rented compact RM 100GO! crusher only needed just under a week to crush all the material from the almost three-kilometre-long Salzburg airport runway into a recyclable final aggregate. This value aggregate was used for the sub-structure of the new runway. Weickl is convinced of the sustainable use of resources: "The recycling of C&D waste creates a loop in which transport and material costs are saved and environmental impact is reduced."
The core business of Weickl Erdbau, which is based in Hallein, a city less than 20kms south of Salzburg, is earthmoving and demolition. Due to the wide range of jobs they cover, it makes sense for the company to rent a compact crusher for certain contracts. Weickl has been using this rental concept for several years. "In our case, the volume we process is too small to justify the purchase of a crusher. The rental system is perfect for us for processing materials directly at construction sites," he said.
Swedish recycling giant Swerock is using a Rockster R1000S compact mobile impact crusher to provide innovative solutions for the efficient reuse of construction waste.
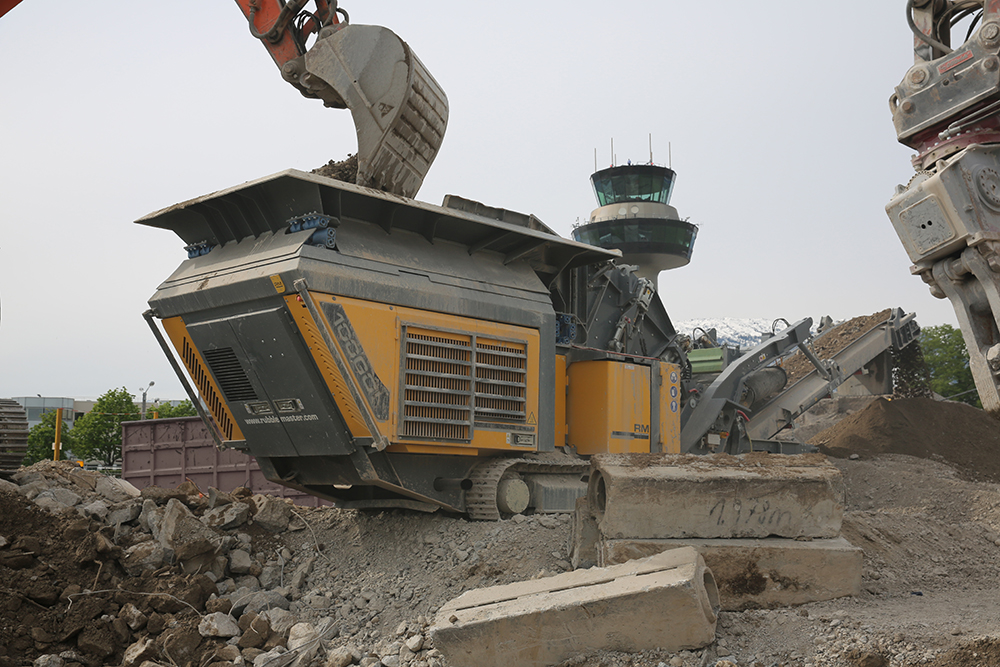
It was Rockster's Swedish sales partner Niklas Johansson of Biocare Svenska who first introduced the R1000S plant to Andreas Pettersson, the area manager of Swerock Recycling.
“High throughput of this compact machine, perfect transport dimensions and excellent access for maintenance have convinced my customers that the Rockster crusher is the right one for them," said Johansson.
The machine’s hydraulically lowerable screen box, swivelling catwalk and swivel-up doors mean that service work, maintenance and the replacement of screen meshes can be carried out quickly and easily.
Due to the R100S impact crusher’s hydrostatic drive, which ensures a constant crushing power, the diesel consumption per tonne is claimed to be noticeably reduced.
Johannson added: "With Rockster's hydrostatic system, the diesel engine always stays in the optimal RPM range, only the hydraulic pump adapts to the crusher's power requirements, which results in lower fuel consumption per tonne of final material.
“Additionally, the Volvo Tier4f engine, with AdBlue, ensures very low NOx emissions."
Swerock is one of Sweden's largest suppliers of building materials and services for the construction and civil engineering industry. The company has approximately 950 employees and is part of the Peab Group construction company.
Mike Broad, who retired from the aggregates and quarrying business in September 2018, has been reflecting on a remarkable 48 years in the industry which he spent with just one company.
In October 1970, a 17-year-old Broad was fresh out of education at Wigan Grammar School in North-West England. He secured his first job with family-owned quarrying business Gaskell Bros, which is based in nearby Ashton-in-Makerfield.
In his years as a director, Broad worked alongside Gaskell Bros. MD Mark Gaskell and the pair carved out a new path for the company. Venturing into the recycling sector in 1999, its primary focus was building and demolition waste from Manchester and the neighbouring counties.
Working alongside the Gaskell family, Broad forged a successful relationship during this period with wet processing equipment company CDE.
“First, we began operations in dry recycling, procuring a licence to process material that was destined for landfill," said Broad. "Though it did have its limitations. We weren’t the only player in the market at the time, and this was a challenge. We had to identify and produce a product that others weren’t yet producing, so we ventured into wet screening – or ‘wet recycling’ – adding water to clean the recycled aggregate. This also presented challenges for us as it was taking up to three days, in some cases, to fully remove moisture content from drying sand.
“It was a learning process and, evidently, not without its challenges."
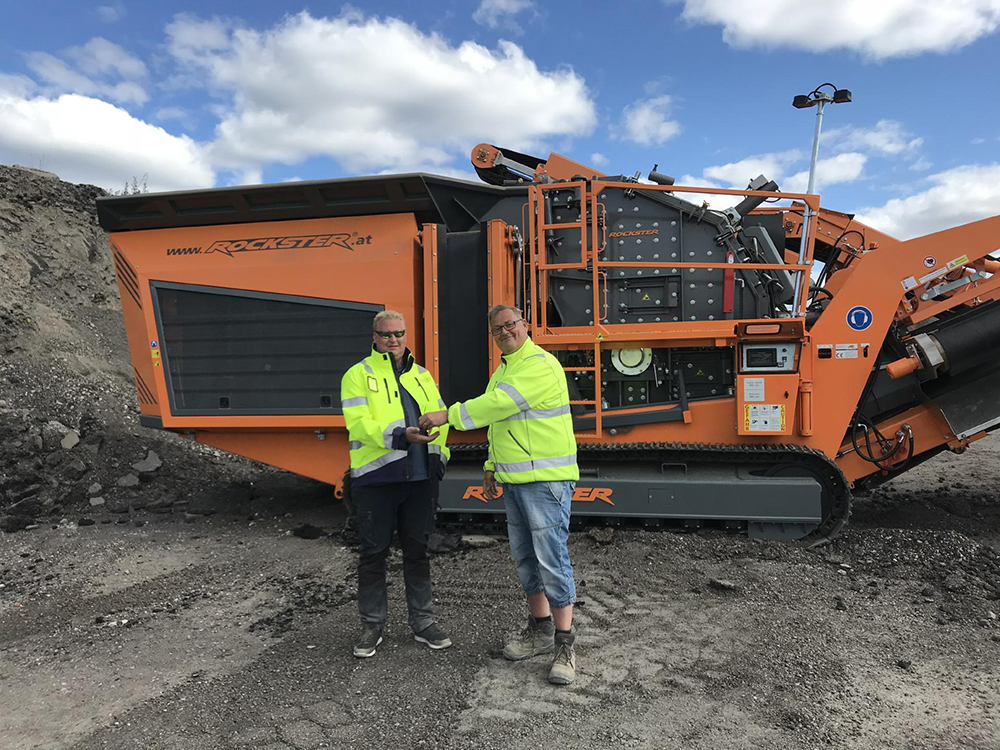
This set the course for what was to become a long-running partnership between CDE and Gaskell Bros., leading to one of the first full-installation sand-washing and recycled aggregate systems in the UK.
“Enda Ivanoff, who is now CDE group business development director, was fresh out of university at the time we first made contact with CDE,” Broad explained. “He came over to see our operation and we explained the challenges we were facing; extracting moisture from the sand and excessive fines losses. Enda and the team at CDE implemented a sand plant that integrated seamlessly with our then current operation.”
CDE supplied its 40-tonnes per hour Compact Sands plant to Gaskell Bros. in 2002. Broad said: “The plant was a massive boost to our operation, significantly reducing our fines losses and expediting recycled sand aggregate dewatering.
“When we thought we had it all figured out, other issues in our plant would start to surface. The log washer just wasn’t up to the job."
“CDE told us they had log washers, so Mark and I booked our flights to come over and see the plant. That was a formative trip for us. We visited and reviewed several installations. We were so impressed by what we encountered on the trip that we began preparations to invest in a complete plant to be fully installed by CDE.”
The turnkey solution CDE supplied Gaskell Bros. in 2004/05, a complete overhaul of the company’s recycled aggregate system, was the single biggest investment ever made by the company.
Gaskell Bros. began processing reclaimed materials at a much faster rate. As little as 10% of materials was now destined for landfill. “We were processing materials we didn’t before, and the built-for-purpose plant resulted in a significant upturn in new business contracts. Efficiency meant we had a volume of product to fulfil almost any customer contract,” Broad said.
With an improved product base, Gaskell Bros. carved a reputation for producing some of the highest-rated recycled aggregate in the UK.
Ivanoff said Gaskell Bros. remains one of CDE’s pioneering customers: “From working with Mike and Gaskell Bros. to commission the first tailor-made C&D wash plant in the UK to commissioning the world’s largest C&D waste recycling wet processing plant in Norway, CDE is supporting companies around the world to extract value from C&D waste material destined for landfill.
“Every day, CDE wet processing solutions divert 63,000 tonnes from landfill, totalling over 15 million tonnes per year. As this figure continues to grow, and as CDE continues to expand and innovate, Gaskell Bros. will remain one of our pioneering customers and an important part of that sustainability-driven growth story."