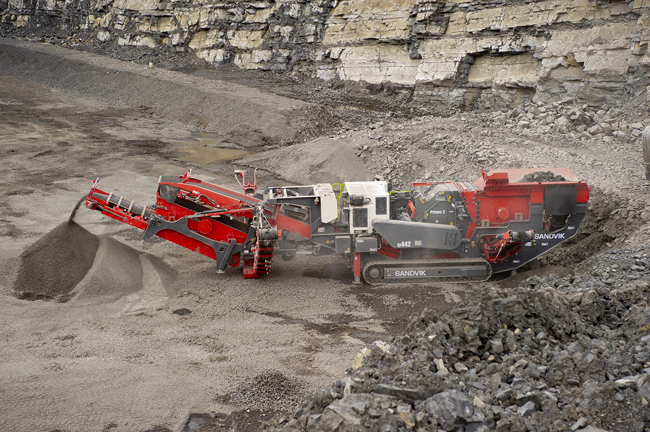
New plant and production hubs are making the crusher and screener market within the aggregates production business as vibrant as ever. Guy Woodford reports
Recently, the Swedish quarrying equipment giant has unveiled the latest upgrade in its 2 Series plant range with the launch of the new QI442 tracked-mobile impact crusher.
The new model includes the new CI621 Prisec impactor which comes with a host of innovations for improved efficiency and greater safety during maintenance.
Like previous Sandvik Prisec impact crushers, the new CI621 can be configured to work as either a primary or secondary crushing machine, while the plant’s two hydraulically assisted curtains can be readily adjusted to produce a wide range of high-quality product sizes.
The new CI621 includes further enhancements primarily focused on increased safety during maintenance and serviceability. These include a new rotor position and locking device, new hammer locking wedges for quicker removal and fitting, and a new wedge removal tool to provide safer installation and removal. The model’s rotor bearings have also been upgraded for easier assembly and clearance setting.
An eye-catching optional feature of the QI442 is the modular hanging screen system. Recently launched on Sandvik’s mobile cone crushers, the system is interchangeable and offers the flexibility for the crusher to operate in open or closed circuit. The innovative design enables set-up in less than 30 minutes and can be fitted without the use of additional lifting equipment. The patent-pending hanging screen option delivers multi-functionality as a one, two or three-way split screener, as well as a highly productive and efficient impact crusher.
The double-deck hanging screen enables the machine to produce two screened products and recirculate the oversize back into the feed conveyor. The oversize conveyor may be hydraulically rotated 90° for stockpiling up to three products on the floor, or 180° for removal. The tail section can be raised hydraulically to give improved ground clearance for transport when loading or unloading.
The QI442 comes with a Sandvik My Fleet remote monitoring system as standard. My Fleet has been developed to help Sandvik customers know exactly how their equipment is being utilised. Through the collection and accurate monitoring of a wide array of parameters, this is said to facilitate accurate production forecasting, ensuring that the most efficient use is obtained from equipment, thereby maximising return on investment.
The QI442 comes equipped with a range of customer-focused features designed to improve the return on investment and experience for the operator. A pre-screen is fitted to ensure maximum scalping capability and to prevent any undersize material passing through the impactor, maximising throughput and reducing wear costs. This also allows a specifically sized product to be produced from the natural fines’ conveyor. The pre-screen also has a choice of grizzly or punch plate top deck and mesh bottom, providing the flexibility to suit any application.
The move to the 10,000m² site in Matzelsdorf, Neumarkt im Mühlkreis, Upper Austria, was made in mid-June 2019. Rockster says the step is necessary due to the company’s continuous expansion, an extended product line and shorter delivery deadlines.
Established 15 years ago in the town of Enns, Rockster has since developed two patented systems for mobile crushers and expanded its distribution network worldwide. A new head office with a 7,000m² warehouse was set up in Ennsdorf, Lower Austria, in 2008, and subsidiaries Rockster North-America, Rockster China and Rockster Germany were established between 2013 and 2016.
The new Rockster site in Matzelsdorf was acquired in January this year. The first machine to be produced at the new assembly line will be the track-mounted impact crusher R1000S.
“It is our most technologically advanced mobile crusher and we are highly motivated to deliver one of our bestsellers as the first crusher produced in Neumarkt this fall,” said Rockster chief executive officer (CEO) Wolfgang Kormann.
As part of the relocation, the company name Kormann Rockster Recycler has also been changed to Rockster Austria International. The company says the name change will accentuate and better define the international nature of its operation, needs and future goals.
As part of the move Rockster plans to hire up to 20 new employees, and Kormann says the relocation will offer improved company growth potential due to the availability of a larger space.
“Standstill means regression. Continuous development is not only essential in the construction of our machinery, but also the infrastructure has to be adapted according to the innovations and an increased demand.”
Serge Raymond, manager-product technology at MAJOR, an innovative Québec, Canada-headquartered manufacturer of wire screens for the global aggregates, mining and recycling industries, says choosing screen media for a screen box isn’t as simple as it used to be.
“What once was just woven wire now includes a variety of alternative options, such as rubber, polyurethane, metal plates, high-vibration wire, combinations of different materials and more. With each type comes countless new options for customisations of a screen deck to provide enhanced efficiency and throughput — whether by using one type of media or blending multiple.
“Standard woven wire is often the cheapest — at first sight — option, but that’s no reason for these alternative options to be passed over without careful consideration. Depending on the application, these innovative products can improve wear life; reduce pegging and blinding; speed up the stratification process and better remove fines, increasing the overall quality of the screened product.”
Raymond offers a few reasons why one should consider high-performance screen media.
“Most types of specialised screen media offer a much longer wear life than traditional woven wire. Thick rubber and steel plate media clearly mean greater durability, but sometimes sacrifice open area. High-performance media is made up of highly engineered wires held together with polyurethane strips, which eliminate cross wires with high wear spots that are common to woven wire and a few types of self-cleaning media. This results in optimal open area and a wear life as much as five times longer than wire alone.
“High-performance screen media can offer exceptional open area — in some cases 30% more than traditional woven wire and 50% more than traditional polyurethane and rubber panels. It is often a good solution for issues such as pegging, blinding or material contamination. Some media is tapered to help solve these problems, while others use unique designs to allow wires to vibrate independently from hook to hook under material contact. The result is high frequency vibrations from the wires, in addition to the vibration from the screen box. This virtually eliminates near-size pegging on the top decks and fine material blinding and clogging on the bottom decks. It also means less risk of material contamination and cleaner retained product through the middle decks.”
Raymond argues that because screeners are often placed at both the beginning and end of production, the right screener media can be key to the quality and volume of production. High-performance media, says Raymond, can offer the necessary efficiency boost because some kinds accelerate stratification and increase material separation.
He continues: “High-vibration wire screens operate at a high frequency to accelerate the stratification process. That frequency can be as high as 8,000 to 10,000 cycles per minute, as much as 13 times higher than the standard vibration of a screen box. The increased screening action spreads material over the entire screen’s surface area on all decks. This moves the material faster, while maximising contact to ensure optimal throughput with no carry-over. The result is a higher-quality end product.
“This type of screen media can also be extremely effective in removing fines. The result can be less water needed to wash material or, sometimes, a complete elimination of necessary water use.
“One type of screen media isn’t always the option, and the answer isn’t immediately obvious. Consult with a dealer and manufacturer to determine the best type of media to solve screening problems and improve performance. The right solution could mean turning a screen that was a bottleneck into a profit maker.”