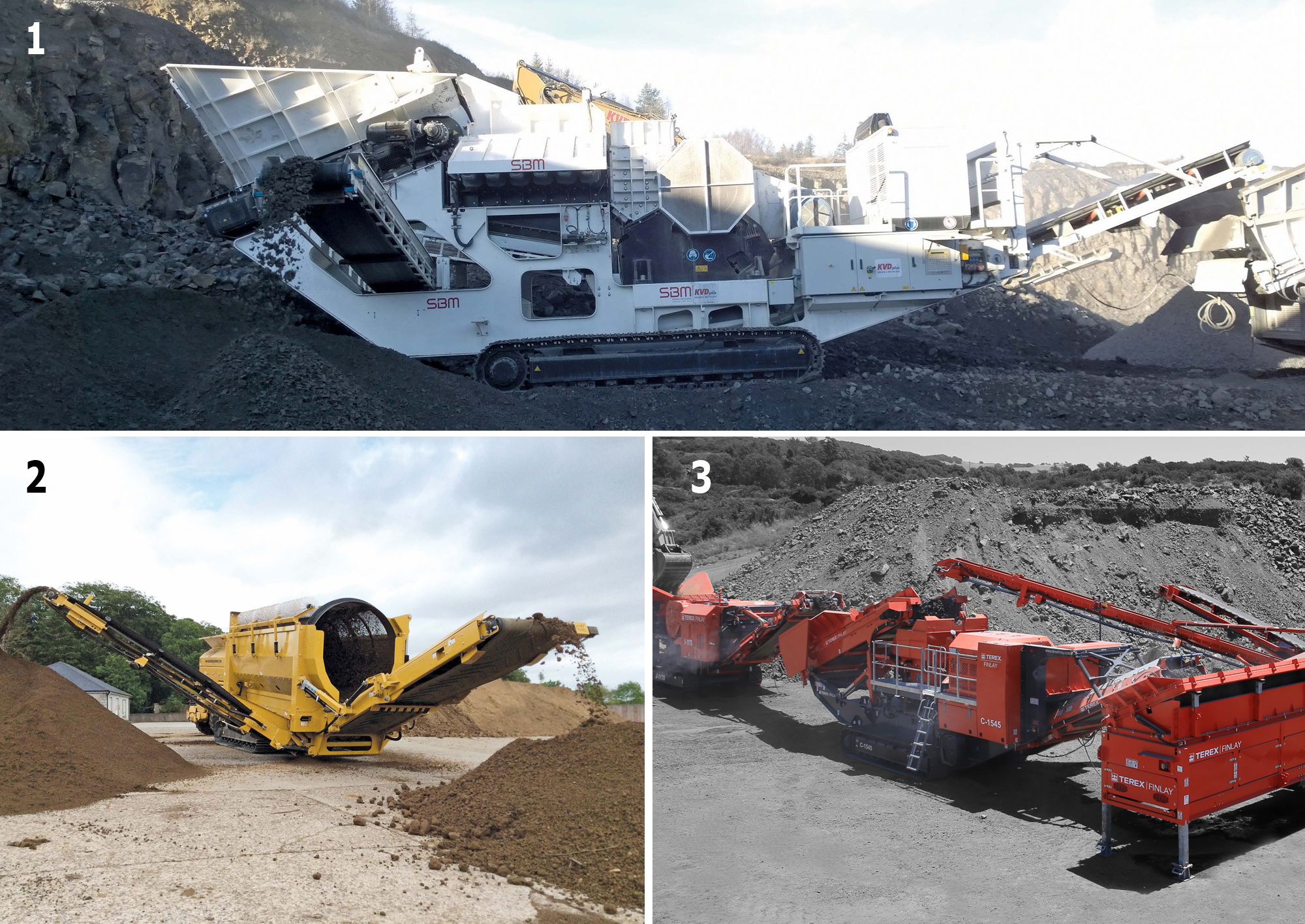
Players in the crushing and screening industries continue to launch new and updated models to help operators run their quarries smoothly.
Quick set-up times, productivity and recycling abilities are among attributes being listed by buyers of equipment, and manufacturers have delivered.
A recent development, the global introduction of the
The company claims the NW Series is the first wheel-mounted crushing plant on the market that fits compactly into standard 40ft (12m) containers to be shipped overseas or by railway transportation.
A combination of Metso’s NW106 primary jaw crushing plant and the NW220GPD secondary cone crushing plant with a large dual-slope screen have been optimised to be relocated regularly. Hydraulically fine-adjustable support legs, hopper walls and screen lifting facilitate fast installation and dismantling.
“Setting up a conventional portable crushing and screening plant often requires preparations with foundations and other site conditions. The new Metso NW Series plant solution is designed to avoid all these challenges, and only minimal preparations on site are required,” says Eric Lavieville, global product manager, portable plants, Metso.
Increased capacity is mainly achieved by the Nordberg GP220 cone crusher and the new dual-slope screen, and the whole process can be precisely adjusted by Metso’s new IC50C process control system, which is standard with the NW Series crushing/screening plant. It is designed to form a seamless combination between the primary crushing stage and the secondary crushing/screening stage. The process can be started and stopped by the push of a button.
Meanwhile, South African environmental waste management company Mfangano Solutions, based in Johannesburg, is working with municipalities and contractors to deliver recycling machinery.
Mfangano, the new
“Mfangano has trained Pikitup operators and keeps spare parts available at its premises. These measures prevent avoidable downtime and allow Pikitup to manage our building rubble and green waste more effectively,” says Christa Venter of Pikitup.
In another waste recycling application, bulk excavation and recycling company M.A.C. Contracting, based in Nuneaton, county Warwickshire, UK, is using
Over the last three years the family-owned business has focused closely on recycling and the supply of recycled aggregate in addition to the supply of quarried aggregates, now boasting this as its key business activity.
In the construction/demolition industries items such as concrete, sand and brick comprise 70–95% of discarded material arising from a residential or commercial site development. Often discarded, the materials can be recycled into new products, or used in many new ways, being financially beneficial to the company and environmentally beneficial.
In order to recycle this material M.A.C. currently operates a Sandvik Construction QJ341 jaw crusher; QA451 triple-deck Doublescreen; a QE141 and two QE341 scalping screens.
“The QJ341 Crusher is feeding the QA451 screen which is working in a four-way split separating the material into various different aggregates. These include pipe bedding, 6F2 crushed concrete, concrete fines and 10mm pea gravel. The QE341 screens predominantly road planes back down to 20mm. Grab loaders return to site with a truck load of soil, brick and general garden waste, the soil is separated out and the rest is fed into the crusher,” says Marcus Clay, managing director.
M.A.C. recently won a three-year contract to supply materials for use on a major road project, the A46 Toll Bar End, near the City of Coventry, due for completion in 2016.
In Scotland a
The Powerscreen 1000 Maxtrak features the well-proven 1000 Automax cone crusher technology at the core, and offers potential outputs of up to 230tonnes/hour, depending on the material being processed. The crusher maintains excellent and consistent product shape with a high reduction ratio, and has been specifically developed for the larger end user. It can accept an all-in feed, eliminating the need for pre-screening, which would reduce the cubicity of the finished product.
Another mobile jaw crusher, the STE 108.75 T RR PB, was delivered to Czech company KVD by Austrian manufacturer
It is operating near Libá where it faces special geological challenges as the hard rock to be crushed (mainly basalt/granite) is interstratified with loamy zones.
The SBM plant has an apron feeder in the 5m³ feed hopper that provides continuous material supply, with pre-screening carried out by an integrated six-row roller grizzly that separates the loam from the hard rock.
Basalt is fed into the machine, which has a feed size of 0-800mm, and the STE 108.75, with a gap opening of 1,080x750mm, crushes the material down to 0-250 mm at a throughput capacity of 250tonnes/hour. The crushed final product is used to produce mineral wool.
“A diesel-electric drive with 350kVA allows for environmentally-friendly operation of the complete crushing plant and the secondary screening plant at a diesel fuel consumption of less than 30litres/hour,” says SBM.
As
The C-1545 offers “a high capacity and aggressive cone crusher for the surface ore mining and aggregate industries,” and incorporates the new Terex TC1150 cone crusher with direct variable speed clutch drive, automatic tramp relief and on-the-fly hydraulic adjustable closed side setting (CSS) adjustment.
The large hopper/feeder’s automated metal detection and purge system protect the cone and reduce downtime by removing metal contaminants via the purge chute.
Additional benefits are said to include rapid set-up time, ease of maintenance, high reduction ratio, advanced electronic control system, high output capacity and excellent product cubicity.
A new mobile Terex Finlay J-960 jaw crusher is being used by RB Haigh to crush concrete as part of recycling operations, processing the material down to 50mm and below to be used by local builders and developers.
The crusher was delivered to RB Haigh, based in county Essex, south-east England, by Finlay Plant South East, and is supporting the company’s on-site processing service for hard-core and soil products. The company also runs two Terex Finlay screens.
The Terex Finlay J-960 incorporates a proven Terex direct drive single toggle jaw crusher which gives high capacity with large reduction capacities.
Leon Sheehy, managing director of Finlay Plant South East, says: “The J-960’s compact size, quick set-up times, ease of transport and user-friendly operational features make it an ideal choice for operators. Its ease of mobility and compact size also enable RB Haigh to hire the machine out locally as required.”
A prototype direct-drive I-140 horizontal impact crusher was among a number of new crushing and screening solutions showcased by Terex Finlay at a recent Customer Day in Doncaster, northern England.
Offering a high level of fuel efficiency, the 1270mm x 1240mm I-140 model from the Northern Irish-based manufacturer is ideal for recycling and quarrying applications.
Among other models on show in Doncaster were the C-1545 and C-1540S cone crushers, the J-1170AS jaw crusher, the 694+ inclined screen, and the 883+ Spaleck heavy-Duty screen.
Austrian manufacturer of mobile crushing and screening machines dsb Innocrush is celebrating its tenth anniversary with the promise of big future plans to be announced at bauma 2016.
“At the beginning it was not easy to gain ground,” says Dieter Durstmueller, general manager of dsb Maschinenbau.
“In the course of time we succeeded with much input, engagement, continuity and best know-how, and convinced our customers of our offerings. Our philosophy is to build simple, compact machines, to be always near the customer; to offer best service and highest output. We are proud of that.”
Initially the company focused on impact crushers but the product range has widened with further innovations such as the patented Innodrive and the new Innoscreen 2.
The Innodrive drive concept works without coupling and is said to be “almost wearless,” while the new Innoscreen IS2 has a big 1,500mm x 2,800 mm screen for oversized grain and is driven hydraulically from the crusher.
Indeed, other new screen media has been introduced to the industry, with materials washing specialists CDE launching its R-Series primary screens, designed to optimise feed to the turnkey wash plants it provides and to reduce the requirement for a dedicated operator to feed the processing plant.
The new range includes two new machines. The R1500 has a maximum feed capacity of 200tonnes/hour while the larger R2500 machine offers a maximum feed capacity of 500tonnes/hour. Both are suitable for use in the pre-screening of a range of materials including sand and gravel; crushed rock; C&D waste; topsoil; coal; salt; iron ore, and other mineral ores.
The R-Series combines a feed hopper, screen and conveyors in a variety of different configurations. The feed hopper on the R1500 has a maximum capacity of 7tonnes when fitted with the optional extendable hopper sides while the hopper capacity on the R2500 unit rises to 20tonnes.
“The R-Series allows for a constant, even flow of material to be delivered to the integrated screen before being sent for additional screening, washing and sizing. The hopper capacity, particularly on the R2500 machine, allows for charge filling of the hopper which frees up an operator and vehicle to complete other jobs on site, ultimately reducing the level of operator intervention required with a processing plant,” says Stewart Cusick, product development engineer at
Kevin Vallelly, product development manager at CDE explained that the R-Series was developed as an efficient delivery system when more difficult materials are being processed.
“A key part of ensuring a processing plant performs at maximum efficiency with minimum operator intervention is getting the feed system right and we spent over two years developing the R-Series which included extensive testing at sites in Ireland, UK, Germany and Scandinavia on a wide variety of different materials.”
Company owner Roger Kieswetter bought the machine through local Tesab Dealer, Tesab Ontario, along with the help of Bob Bloomfield, Tesab America.
Kieswetter’s experience with Tesab goes back 18 years when he bought his first Tesab 623 wheeled crusher, and that was used in a variety of applications, including road granular production and asphalt and concrete recycling while putting over 15,000 hours of operation on the unit.
When Kieswetter decided to upgrade this machine late last year, the old 623 was sold to another business in Ontario where it still runs on a daily basis.
It has been replaced with the same 623 wheeled model still being manufactured by Tesab Engineering today, and Kieswetter took possession of the machine after Tesab Ontario had exhibited it at the Heavy Equipment Show in Toronto in March, 2015.
Fitted as standard with a Tier 3B, 93kW JCB444 Ecomax engine, the 620 has been designed with an optional dual power system, thus reducing fuel consumption, emissions and noise levels. Tier III and Tier IV and fixed speed genset power units are available.
The load-sensing material feed is said to enable an optimum utilisation of the large screening surface.
Anaconda says that the overall 20tonne weight and dimensions of the TD620 allow for easy transport to anywhere in the world, and for maximum mobility and on-site flexibility it is available in both wheeled and tracked versions.