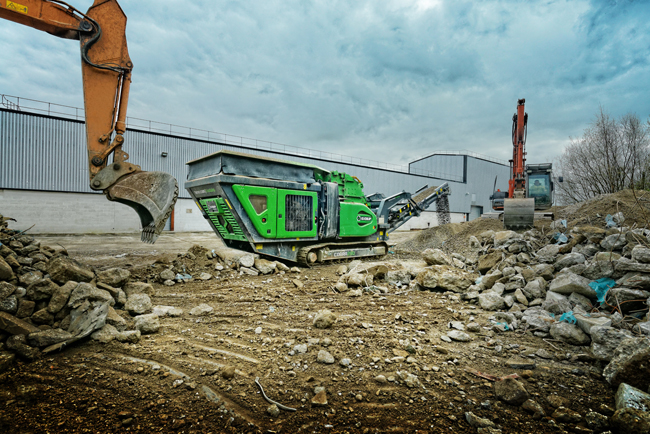
Global demand for recycled aggregates is rising, creating attractive business opportunities for international crushing and screening plant manufacturers. Guy Woodford reports
In March 2019,
The site purchased for the new facility, which will be operational later this year, consisted of an existing building and ground area that needed redeveloping to meet Terex’s operational and manufacturing requirements. This included the processing of construction and demolition waste which resulted from site clearance of old blockwork and building rubble from internal walls, and concrete and plinths from the yard.
This waste material provided EvoQuip’s Cobra 290 impact crusher with the perfect opportunity to demonstrate its capabilities by crushing the material to be reused instead of sending it to landfill—saving money and reducing the environmental impact.
The material was initially broken up by an excavator and rock hammer and then processed through the Cobra 290 to create a usable product, which was then used as a base layer on the site for new concrete roads that are strong enough to handle the expected number of trucks.
Kieran Devlin, operations manager at Terex Campsie, said: “The Cobra eliminated the need to purchase new material for the road base layer and also meant we did not have to pay to send material to landfill, resulting in great financial savings for us and reduced the environmental impact.”
The Terex Campsie site clearance generated over 650m³ of inert waste material—material that would have ended up in landfill if it had not been processed by the Cobra 290.
The environmental impact as a result of processing on site was greatly reduced, as it eliminated the need for virgin raw materials, significantly reduced the number of lorry movements, and avoided the need to dispose of it in landfill, causing land pollution.
Compared to the cost of disposing unwanted material in landfill, including the landfill tax that would generate, lorry hire and importing stones for blinding, hiring a Cobra 290, stockpiling rubble, loading the crusher, depositing material on site, separating out rebar, salvaging rebar, removing non-crushed concrete for disposal, and reusing surplus, generated financial savings of around £9,000 (US$11,440).
Alongside being better for the environment, this short project proved to be better on the pocket.
Successful recycling requires both process efficiency and fuel economy to become a profitable operation. German recycler H. Scheer boosted its competitiveness by changing an old, portable plant to a modern combination of
“Both fuel economy and crushing efficiency have taken giant steps ahead during the past 20 years. Our NW100 portable plant consumed more fuel than our new units, LT106 jaw plant and ST3.5 mobile screen together,” comments Markus Scheer, machine operator at the German recycler H. Scheer.
“We are happy to run the new Metso Lokotracks that seem to function well. As a bonus, we are reaching now 20-30% more capacity using modern, track-mounted Metso equipment,” he adds.
H. Scheer, based in the picturesque village of Spenge in North Rhine-Westphalia, can be described as a full-blooded family company. Founded in 1979 by Harald Scheer, the company has been expanding its activities from transporting of materials and container service to a complete offering for recycling.
Today, the company is steered by three women. Christel Scheer has the managerial position, and her daughters Bianca Scheer works as accountant and Christina Eckel as operations manager.
In addition, the family’s two brothers Markus and Volker Scheer work as machine operator and truck driver within the company.
H. Scheer used a Nordberg NW100 portable jaw unit for almost 20 years. as their main crusher for recycling. During the time, over 18,000 crushing hours were accumulated.
In April 2017, the swift changeover from the old, portable plant to new, tracked units was made. To carry on the recycle crushing and screening process, a LT106 jaw plant and ST3.5 mobile screen were selected. Both units were sold by Fischer-Jung Aufbereitungstechnik, Metso’s distributor in Germany.
In the recycle process, the feed material including concrete blocks and bricks, is fed to the LT’s C106 jaw crusher. A closed side setting of 30mm is used. After crushing, a steel wire mesh-equipped ST3.5 unit screens the material. A second mobile screen is used for fine screening when needed.
The end product range of H. Scheer includes 0-8mm, 3-7mm, 8-16mm, 0-45mm and 40-80mm grades. The clean, recycled products are used as different kind of base materials for building purposes.
The combination of LT106 and ST3.5 only consumes about 28 litres of fuel/hour while the NW100 alone took over 30 litres. Average capacity has grown 20-30% up to 150 tonnes/hour, respectively.
“In addition to the good fuel economy, we are very pleased with the Metso IC700 process automation. Before, everything had to be adjusted manually. Now, the only thing we need to do is to push a couple of buttons at the IC system, and everything is done automatically,” Markus Scheer notes.
SJ Walchester, a leading specialist recycler of construction and demolition waste from Stoke on Trent, central England, say its has received a major boost in its operational productivity and efficiency after acquiring a QJ341 tracked jaw crusher from
“We’ve used various crusher brands over the years, but from the initial demonstration the QJ341 was very good. It did more than I was expecting it to do, and we got a lot greater output with it,” says SJ Walchester managing director Steve Walchester. “The different functions on the crusher are very easy to flick between making it a very user-friendly machine.”
No matter how good a crusher is, it is only as good as its support. Here Walchester found again that Sandvik exceeded his expectations. “If the crusher was to break down it would cost us hundreds if not literally thousands of pounds in lost downtime, wages and revenue. That is not to mention the damage to our reputation which is based on supplying customers with a high-quality product, when they need it, at a fair price.”
With that in mind, Walchester decided to take the Sandvik Security+ Gold service agreement when he purchased the machine. This is Sandvik’s extended warranty programme offered through a service agreement which lasts for a duration of two years with the Gold+ package. Through four inspections throughout the year, preventative maintenance and inspections are carried out by a qualified engineer to ensure the unit is running at peak performance.
“My service and support experience are that Sandvik is second to none. We had a problem the other week; I phoned Sandvik and within three hours Sandvik was on site and had fixed the problem.”
The company currently produces 2-3,000 tonnes of 6F2 or Type 1 each day from a variety of sources. The arisings mainly come from demolition work, with the materials consisting of demolition waste, reinforced concrete, bricks and 300mm lumps of asphalt. Much to Steve’s and his teams delight, even the latter has proved not to be a problem for the QJ341.
“I’ve used crushers from other manufacturers on asphalt and tarmac, and the QJ341 is the only jaw crusher I’ve experienced which will process it without problems. This is by its very nature sticky – especially when it melts in summer – with the hot conditions we experienced last summer being a case in point. Our previous crusher wouldn’t touch it and kept jumping the jaws. The QJ341 is simply able to be put into reverse and crushes as well as it does when set ‘forward’.
“We are the only company in the city (Stoke-on-Trent) with a crusher that is able to deal with asphalt and tarmac. This has meant other demolition and road maintenance companies bringing their asphalt and tarmac to us for recycling. The Highways Agency is one of our regulars!”
Austrian compact mobile crushing plant manufacturer RUBBLE MASTER has built up a strong global recycled aggregates customer business. Gerald Hanisch, the company’s chief executive officer, believes the next few years will see a worldwide increase in onsite aggregates recycling. “There are smaller sites and especially remote sites where it pays to recycle onsite. Laws and legislation also influence recycling substantially. Regulations will support aggregate recycling and establish a stable market which will lead to further growth.”
To crush increasing amounts of asphalt, concrete and natural rock to meet rising customer material demand, Swedish company Tommy Nordbergh Maskin & Transport AB (TNMT) has switched from using RUBBLE MASTER’s RM 80GO! impact crusher to the larger RM 120GO! fitted with an RM MS125GO! screen.
The company’s new RM 120GO! with RM MS125GO! is also fitted with the RM GO! SMART digital solution, an optional hydraulic hammer changing system and a steep conveyor belt.
The RM MS125GO! is a mesh deck screen featuring a hydraulically pivoting refeeding belt, giving customers greater flexibility in daily operation. This allows TNMT’s RM 120GO! with RM MS125GO! to crush and screen in a single pass.
The RM MS125GO! model’s hydraulically pivoting refeeding belt transports oversize grain either to the stockpile or back to the crusher in a closed circuit. With the aid of a handling frame, RUBBLE MASTER says the screen can be fitted to the machine in less than 15 minutes. The added presence of an RM screen tensioner allows rapid changing of the screen when other grain sizes are required. Owing to the frequent changes between types of feed material, the use of a hydraulic hammer changing system is also said to be proving a worthwhile option for TNMT.
The RM GO! SMART digital used by TNMT while operating its RM 120GO! is making the firm’s performance analysis, crusher maintenance and spare parts management even easier. This intuitive tool provides live data at any time on the machine’s status, daily reports and, in the event of problems, instructions on remedying the fault direct to a smartphone or tablet.
Around 40% of the material crushed and screened by TNMT’s RM 120GO! is concrete and 40% is asphalt, while natural rock accounts for the remaining 20%. Since recycling asphalt and concrete is the company’s main business, TNMT’s choice of an optional even more wear-resistant crusher lining and a steep conveyor belt for the RM 120GO! is said to be paying off. The steep conveyor belt improves the separation of steel from the feed material and the lower wear extends the service life of the belt.
TNMT’s vision and business concept are very similar to those of RUBBLE MASTER. Both aim to always be first choice when orders are placed and to always exceed customers’ expectations. To deliver on this in Sweden, RUBBLE MASTER relies on its sales partner, OP System.