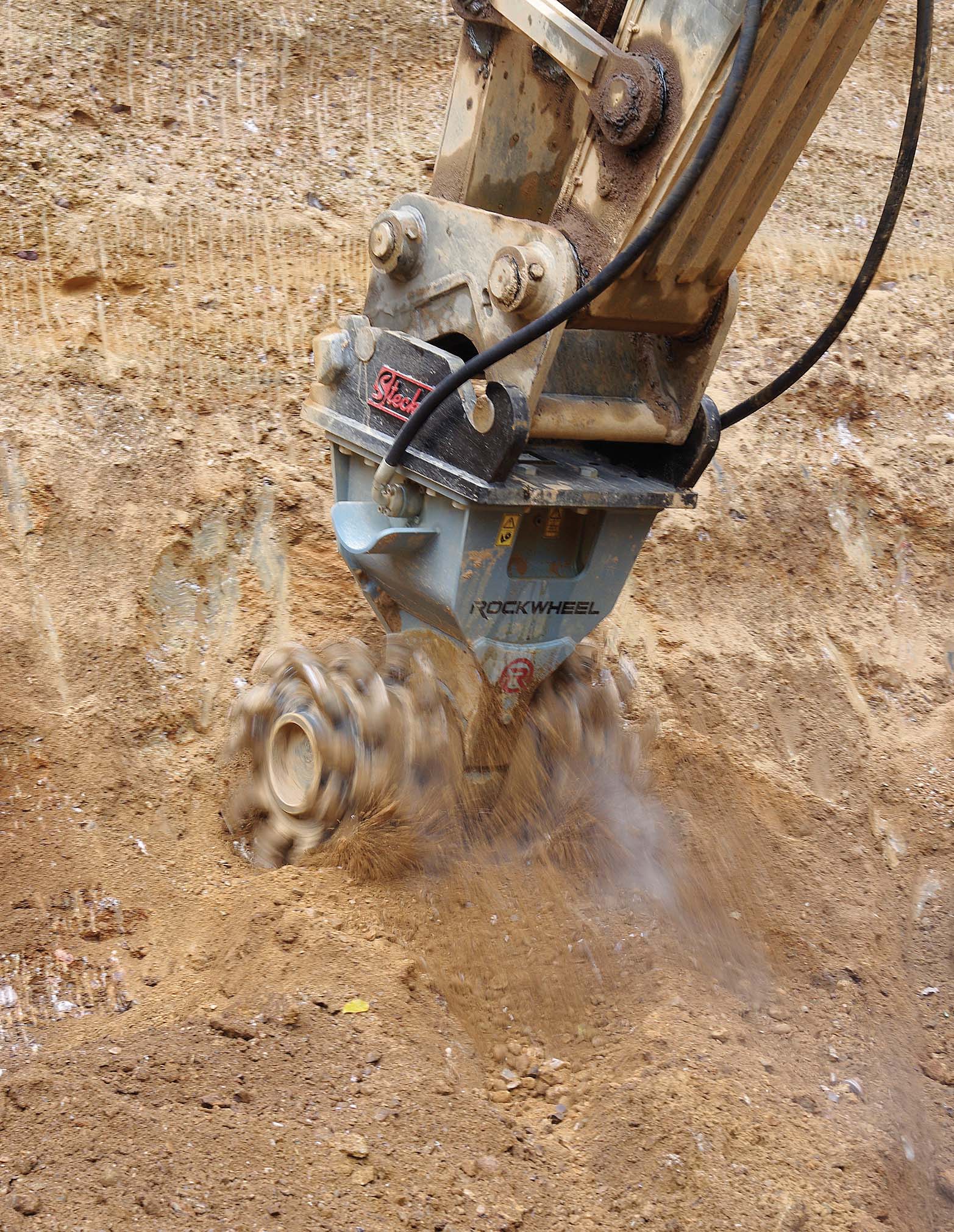
A German sand-gravel quarrying operation says it has doubled, and in some cases tripled, output using innovative cutting technology.
For some time, Saarland-based Kies-Hector has been mining ‘natural concrete’ with a Rockwheel D30 cutting unit on a 36tonne
The gravel-sand conglomerate in the middle bunter sandstone is being mined in the open-cast mine belonging to August Hector near Saarlouis-Lisdorf.
“We are mining the oldest gravel in Germany in the Erika field,” says Andreas Fink, technical manager, who points out that the bed, laid down some 150-240 million years ago at the edge of the Paris Basin, has a thickness of 60m and below it are layers of carbon.
For decades scarifiers were used to mine the highly abrasive material in the open-cast mine but the wear and tear was enormous, and Kies-Hector looked for an alternative excavation method.
Fink’s attention turned to the innovative cutting technology provided by cutting unit attachments, and in particular the Rockwheel provided by the Baden-Württemberg-based Rokla.
“Our mid-sized and medium output cutting units have an extremely short construction and only three main components: housing, motor, and cutting heads equipped with picks,” says Robert Piasecki, Rokla’s managing director.
Ian Webster, who works exclusively for Rokla, is convinced that a gearbox simply offers no benefits at outputs between 30 and 110kW, yet costs money and makes the cutting units heavier. He is said to have the reputation in the industry for being the world’s most innova tive developer of cutting and hammer technology.
A gearless 1,200mm wide Rockwheel D30, with direct drive output of 110kW, was delivered to Kies-Hector in November 2013. Its two excavating drums are equipped with 60 wear-proof special picks for use in highly abrasive gravel-sand conglomerate.
After a few hours of operation the benefits of the cutting technology were clear to Michel Weisse, the driver of the excavator, and Fink says that “cutting is clearly the better solution for removing rock from the steep face of the quarry.”
“The bolts on the excavator boom are exposed to much less mechanical stress. And for Michel Weisse, the vibrations of the cutting unit are significantly less physically strenuous and exhausting than the powerful impacts he felt using the scarifier. It is absolutely clear which technology the driver prefers: the cutting unit, without a doubt,” says Fink.
The Rockwheel D30 and the special pick equipment for abrasive rock now quarries 15tonnes/hour of natural concrete at Lisdorf. With a scarifier fitted to the same Volvo excavator, the output in the conglomerate layer, containing an extremely high proportion (95%) of quartz (silica), was only 4tonnes/hour. However, the company will initially continue using a scarifier on a bulldozer on the flat Lisdorf, although in future the Rockwheel will be used for removing rock from the vertical faces and for profiling in the 80º steep faces.
“This cutting technology enables us not only to work faster, but also to work much more accurately,” says Michel Weisse.
“Using the cutting unit, you can see precisely what you are removing and where overhangs still need reworking. That is not the case with a scarifier.”
Material extracted from the Erika field is also processed in Lisdorf. Gravel sand 0/4mm and coarse aggregates are obtained from the open pit and gravel and/or gravel chipping 4-8, 8-16 and 16-32mm. Gravel sand and gravel from Lisdorf are generally used as the main additive to fresh concrete.
The cooperation between Kies-Hector and Rokla was completely straightforward and open from the outset.
The Rockwheel D30 with the Verachtert CW45S quick-change system, was selected with the sales expert Robert Piasecki. It is the most powerful of the four direct-driven Rockwheel cutting units: D10 (29kW for excavators, 7-15tonnes operating weight); D15 (44 kW, 12-18tonnes); D20 (70kW, 16-26tonnes); and D30 (110 kW, 26-38tonnes).