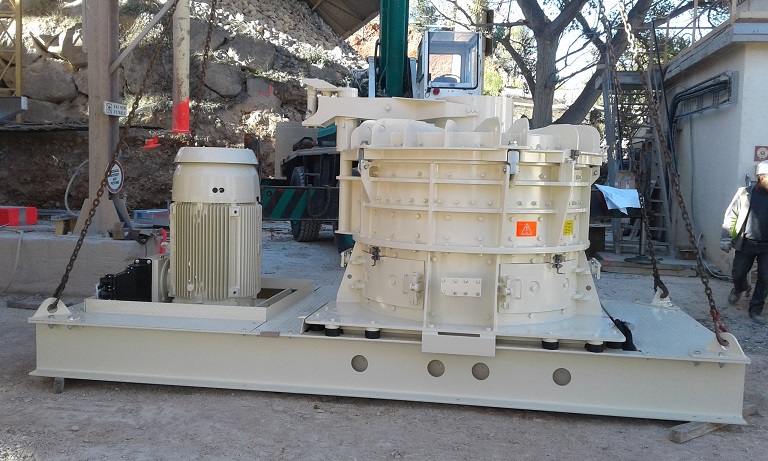
To get the maximum from limestone at the Carrière de Saint-Colombe (CMSE) quarry near the city of Perpignan and produce more valuable fine sand, Colas Group is utilising a BHS RPMF rotor impact mill.
BHS-Sonthofen says this high-performance crushing technology helps Colas achieve high reduction ratio and excellent particle shape. The fine sand is used for asphalt production.
BHS adds that no naturally formed rock is as versatile as limestone. When crushed down to a fine particle size, the material is particularly suitable as a component of asphalt mixtures. A few years ago, the French Colas Group, a major international player in road construction, researched how to extract even more valuable sand from the existing rock for its own asphalt production site at Perpignan.
The rock comes from a quarry in the proximity of Thuir and Saint-Colombe. The quarry that extracts a hard limestone has been established for more than 50 years. In 1979, the quarry was equipped with a crushing plant under the name of Roussillon Agrégats, allowing the materials to be used for construction. In the early 1990s, the Colas Group became the owner of the extraction and production sites.
Since then, the company has made many investments into the technology used at the quarry now known as CMSE - Carrière de Saint-Colombe. It employs big impact crushing machines that produce sands in different categories. In the course of time, new technical options became available - also through consulting of BHS-Sonthofen. To improve the material even further and get more valuable sand from the limestone, Colas decided to add another stage to the crushing process. “The target was to crush the non-valuable grain sizes of limestone 3/6 mm and 6/12 mm to produce fine sand with grain size 0/3 mm in high quantity”, explains the customer.
For this crushing step, Colas turned to BHS-Sonthofen. “Together with the customer, we carried out several tests with the original material at the test center in Sonthofen,” says Alexandre Bernabé, sales director for the French market at BHS-Sonthofen. “This helped us find out how the machine must be configured and what performance we can actually achieve with our crushing mill.”
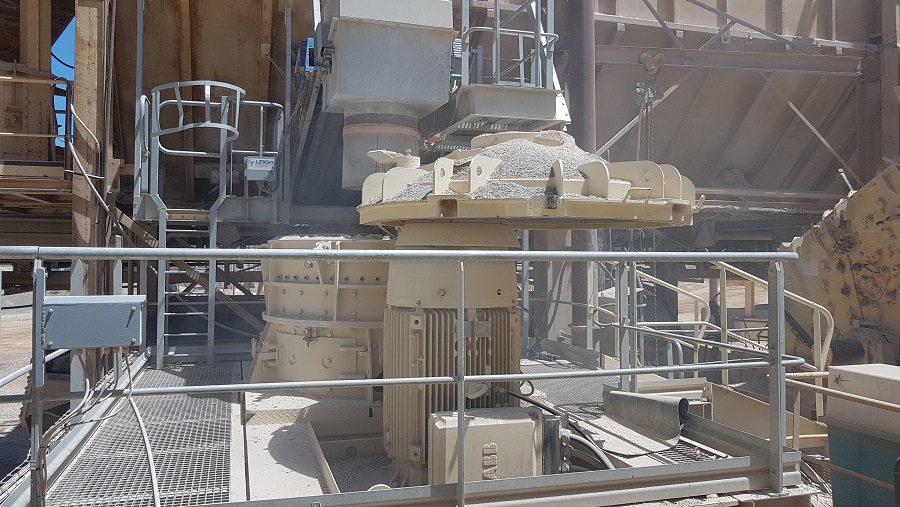
Colas opted for the RPMF 1516 rotor impact mill because of the machine’s unique operating principle. The high-performance crusher has a vertical shaft that is suitable for crushing all low to moderately abrasive minerals and is therefore used predominantly in the production of sand for the concrete, asphalt and dry mortar industries. The machine enables Colas to achieve a high reduction ratio and excellent particle shape.
The impeller rotor of the BHS rotor impact mill is the only one of its kind worldwide. Due to the high circumferential speed of the rotor, there is an almost permanent gap between the tips of the horseshoe-shaped hammers and the anvil ring. The small gap width and the high energy input due to the circumferential speed result in a very high, targeted crushing ratio. Thanks to the narrower milling gap and the higher circumferential speed of the rotor, the material in the RPMF rotor impact mill is exposed to more intense stress. This distinguishes the RPMF, also called 'the pulveriser', from the RPM, which operates the same crushing principle.
“With its crushing principle, the RPMF really stands out from competition. Besides particle shape, the high productivity in the manufacturing of fine materials was another main argument for Colas to choose this machine,” Bernabé says. “Compared to other crushing technologies such as rotary mills, the ratio of tons and kilowatt is superior. For instance, we reach 50 tons per hour on average compared to 10-20 tons per hour with different technologies that consume much more power.” The rotor speed lies in the 80-90 m/s range.
The RPMF 1516 also provides low and uniform wear, which is based on the reverse rotation of the rotor. Every week the operator changes the direction of rotation. This way, a balance is achieved for all wear parts. With the effective dedusting system, operators can handle the wear of the machine easily.
BHS-Sonthofen says that, the result in percentage terms, is a higher proportion of fine sand. While grain size of the input material is 3/6mm and 6/12mm, the grain size of output is 0/3mm with a high share of grains smaller than 1mm. The product is internally used for asphalt production at Perpignan.
“Production has been running for some time, as the machine was put into operation in December 2017," says Bernabé. “The customer is very satisfied with the result and we are very pleased to have been able to help the Colas Group successfully implement this new crushing step.”