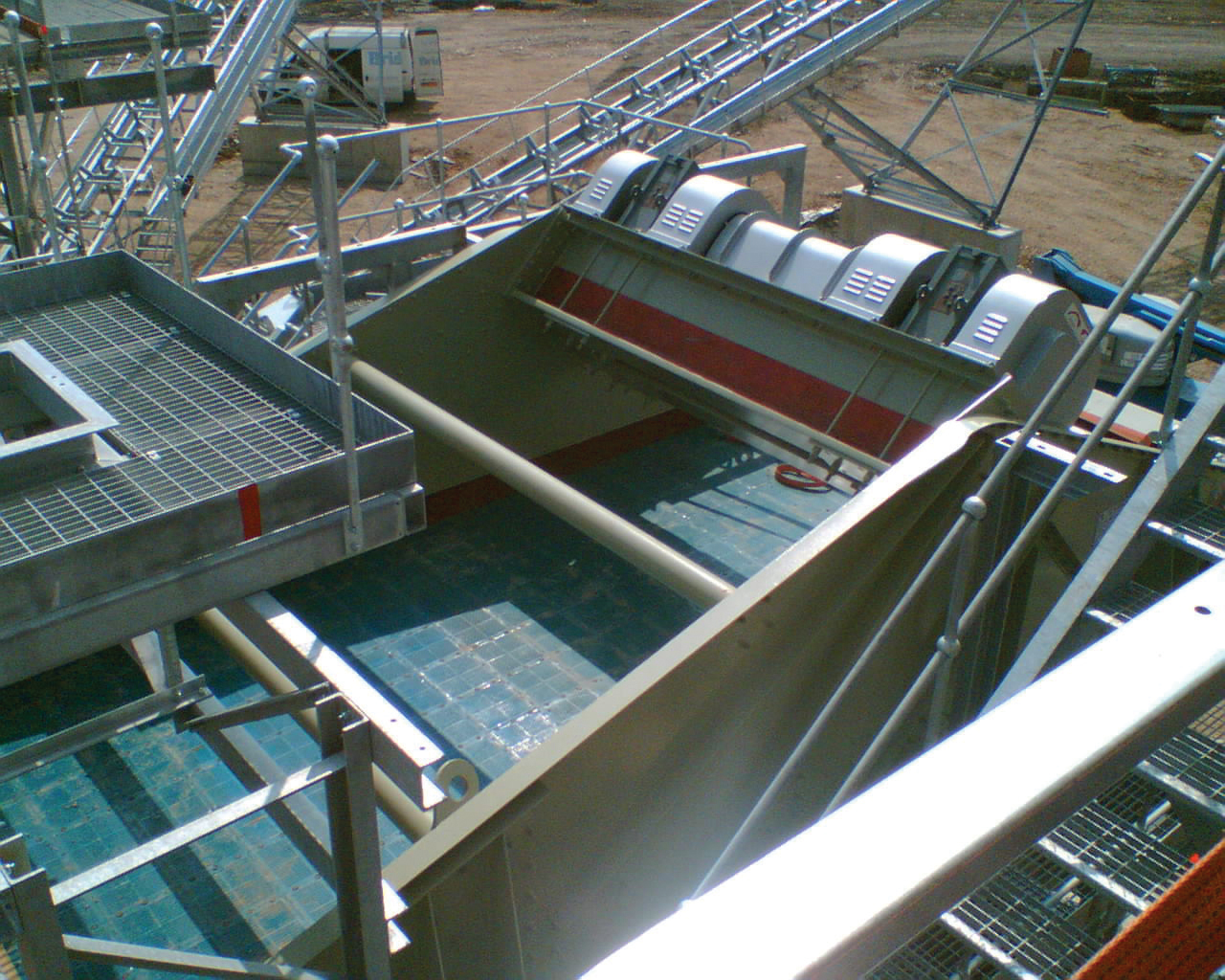
Separating raw materials into products of different specific grades is a crucial and fundamental part of almost every quarrying process. Screening is one of the most commonly used and lowest-cost methods.
Fundamentally, a screen is sheets of material containing holes of a specific aperture, allowing mixtures of different-sized particles to be separated into marketable products.
This process is typically expedited by agitating the mixture with a rapid vibratory motion, says Russell Lafford, product manager, screens at
“Screens can be designed in circular or elliptical formats, with a circular or elliptical motion applied to the media, or in a linear format, with unidirectional motion applied to the material,” says Lafford, whose company produces a wide range of screens under its Linatex brand always using linear-motion units. This arrangement is favoured by company engineers who say it is easier to control the speed at which the media flows across the screen thus increasing efficiency and reducing pegging problems (particles become lodged in the apertures requiring intervention by an operator).
According to Lafford, the simplified in-feed and out-feed arrangement of a linear-motion screen also allows the units to be lower in height, potentially a key concern where space is at a premium.
He says that because every aggregates production operation is different, there is no one-size-fits-all solution. At each screening stage (a typical process can involve ten or more) the flow rate; the specific mixture entering the screen and the amount of space available all determine the dimensions and motion required.
Screens are divided into three categories: dewatering, banana and horizontal screens with dewatering screens designed to remove excess moisture to aid in producing a stackable end product.
These screens feature a sloping back deck section fitted with slotted aperture panels and slurry is fed uniformly along the top of this back section which acts as a vibrating drainage panel. The main deck then slopes upward at 3°- 5° and is also fitted with slotted apertures.
The development of banana screens has been a major innovation in screening, allowing exceptionally high throughput per unit area. They are a high-capacity, high-velocity machine with low-bed depth leading to greater efficiencies and throughput by allowing quicker stratification of the material bed.
Horizontal screens are used for a wide range of applications including coal sizing and dense media separation, drain and rinse applications. They range from 0.3m to over 4m wide and can be up to 10m long.
Double-deck arrangements are available for both the banana and horizontal screen designs.
“Weir Minerals employ two methods for driving vibrating screens: off-balance motors and, for larger units, geared exciters where an eccentric weight is driven by a separate motor.
“The frequency and amplitude of the vibration needs to be tailored exactly to the nature of the media being separated, so it is essential that the motors and exciters are built to exacting tolerances.”
Among a number of recent developments is Metso Minerals's new Lokotrack ST3.5 mobile screen, which classifies difficult, rock-based recycle materials at about 1,000tonnes/working day.
It has been working in a demanding screening project involving such materials at Pollenza, south of Rimini, Italy, where family-owned company Re.i.cal operates a stationary quarry producing aggregates needed for concrete.
“We plan to use our Lokotrack ST3.5 both in recycling and quarrying. Thanks to its compact size, the unit can be easily transported on a normal trailer, which is a big plus for us,” says Andrea Renzi, managing director of Re.i.cal.
An optional vibrating grid is available for the Lokotrack ST3.5, and in quarrying the result is quicker feeding and a reduction in the need to tilt the grid for cleaning. In recycling, the main benefit is the cleanness of the end products.
“The vibrating grid effectively separates wood, plastic and other scrap from the feed, giving us much cleaner screened end products. By choosing different grid mesh sizes, we can also easily adjust and control the feed size to the screen,” says Massimo Renzi, responsible for recycling.
On the ST3.5 mobile screen, the upper screen deck houses a 30mm mesh size and the lower deck 5mm. Oversized materials separated by the grid are returned to the crushing stage. Fed by the small Italian shredder, the output in recycling is about 130tonnes/hour.
Representatives from the Kelston Sparkes Group visited France to see Terex Finlay’s next-generation 984 before specifying it for its screening operation in Frome, County Somerset, south-west England, where the company is contracted by Tarmac to handle dry stone production at Halecombe Quarry. Screening limestone, it is the first installation of the 984 in England and Wales.
Supplied by Finlay Plant SW, the machine currently operates at a rate of 300tonnes/hour, although Terry O’Callaghan, general manager of Kelston Sparkes Group, says it could run up to 320tonnes/hour if required. The 984 has removed the need for two screens and is also producing 50tonnes/hour more than was previously achieved on the site.
To aid productivity, Kelston Sparkes Group worked with Gareth Johnson, managing director of Finlay Plant SW, to develop a larger hopper to shovel-load 75mm aggregate in.
“The 984 does the tonnage and has accomplished what we set out to achieve. The need for two screeners, used to take out the dust on 4mm decks, has also been taken out as this new machine takes out the dust sufficiently well,” says Terry O’Callaghan. The 984 high-volume screening technology is a horizontal three-deck screener incorporating the 6100mm x 1930mm Terex Cedarapids 6203 triple shaft screen, enabling the screening of four sizes of products.
An oval-throw action is said to make the horizontal screen virtually non-plugging, and the ability to fine tune stroke angle, amplitude and the speed of the screenbox allows throughput of materials up to 800tonnes/hour.
“Sustainability is an important consideration for Tarmac, and the 984 has had a big impact on this by allowing us to dispense with two other machines, improving our specific energy consumption and reducing our carbon footprint,” says Garry Wason, Tarmac’s Halecombe unit manager.
With around 25% of the Danish market, Nymølle Stenindustrier is one of Denmark’s largest suppliers of gravel and with 30 facilities in Fyn, Jutland and Själland kitscombined annual production is 7-8 million tonnes of sand and aggregate.
The Nymølle Stenindustrier facility at Røde Kro in Jutland produces some 250,000tonnes of material each year (110,000tonnes are washed sand, the remainder being aggregate), and it needed to replace the screening media in one of the primary screens (a Svedala VFS 48/21), which also operates as a washing screen.
Sites production manager, Jens Rasmussen, contacted
“We wanted to reduce the proportion of undersize particles further, and were open to try a new solution. Immediately after the Sandvik WR Modular Screening Media had been installed the improvement was considerable, and, additionally, the production capacity of the screen increased, which was a real bonus,” says Rasmussen.
“There are no blind areas or joints in the length of the screen to which undersize particles can move without being screened out,” says Elna Hovén, product manager screening media, Sandvik Construction.
Screen cloths made of a newly-developed thin, fibre-reinforced rubber screen membrane for dry screening or polyurethane for wet screening, are mounted crosswise across the screen instead of along it, with the flexible modules creating a cascade effect when the rock material is transported forwards: the “billowing” movement hastens stratification, ensuring any undersize particles are more rapidly screened out.
After the changeover, Rasmussen noted that the proportion of undersize particles, which had been 23%, had reduced to 9%, and that capacity increased to 350tonnes/hour, a 15% improvement.
The 1400X’s reduced engine running speed and enhanced hydraulics are said to offer 15% reduction in fuel consumption compared to its predecessor.
Improved versatility and design specifications are said to be other key achievements of the Warrior 1400X, with the screening angle range increasing by 50% from 4° to 6°.
Standard stockpiling capacity on all conveyors has increased by up to 25%. With the chassis riser option and the telescopic side conveyor option, the fines and mid-grade stockpiling capacity is increased to more than double that of a standard Warrior 1400.
Time required for set-up and shutdown is faster than the previous model, and serviceability features include a screen box raise function and the ability to raise the collection conveyor. Optimal chute design in conjunction with the new feeder under-tray slide-out feature “will minimise any potential spillage and reduce any harmful material build-up around the machine.”
The Warrior 1400X now boasts improved mobility with a two-speed tracking system as standard. The high-speed mode is further enhanced with automatic engine speed ramp-up.
The Warrior 1400X can be fitted with either a Tier 3/Stage 3A Caterpillar C4.4 ATAAC four-cylinder diesel engine or a Tier 4i/Stage 3B Caterpillar C4.4 four-cylinder diesel engine developing 82kW at 1,800rpm.
A
Production has increased from 5,000tonnes/day to 7,000tonnes, and wear is said to be reduced in the downstream impact crusher while water for the washing process is also saved.
Depending on the season the quarry supplies rocks in different qualities: dry in summer and very moist and cohesive in winter. Pre-crushed material of 0/300mm as well as muck pile of 0/2,000mm is fed onto the existing crushing plant. Due to a high amount of clay-silt of 10-12% (peak periods up to 40%) especially in winter, considerable problems occurred with the previous vibrating screen used for pre-screening.
Clogging resulted in soiling of the final product as well as in a substantial reduction of the plant system rating to 300tonnes/hour.
Plant operator Christian Lay decided to apply the VARIOwobbler fitted into the existing plant between apron conveyor and impact crusher. To bridge the existing height it was manufactured with three stages, an advantage because the material is circulated on these three stages, thus considerably improving the screening result.
On feeder grates the screening area comprises several rotating shafts between the open spaces which the fines fall through. Triangular-shaped discs are mounted on the shafts to support movement of the material.
The new DF512 tracked screener from
“The DF512 is certainly a move up the scale in terms of machine size.
“The success of our other products has given the market confidence in what we can design, build and export, and, coupled with the high level of sales and service back up from our network of dealers around the globe, end users are requesting larger machines from Anaconda. This feedback from dealers has been instrumental in our R&D plans,” says Con Gallagher, sales and marketing director.
The DF512 has a 3.66m x 1.52m double-deck screenbox; a CAT 4.4 water-cooled engine; belt or apron feeder option; three integral stockpiling conveyors and a crawler track chassis for ease of movement around/off site.
Other features include hydraulic folding hopper sides as standard; hydraulic screen angle adjustable from 15-19°; hydraulic screenbox raise/lower for ease of mesh change and wired remote as standard (radio remote optional).
CDE Global’s Prograde P275 double-deck rinsing screen is part of a C&D waste recycling plant recently bought from
Material is delivered to CDE’s M2500 and after ferrous material is removed a wash box fluidises the material before it is delivered to the integrated Prograde P275 5m x 1.5m screen, which is fitted with wire mesh on the top deck with a 40mm aperture that delivers the +40mm material to the oversize stockpile via one of the four integrated 9m stockpile conveyors. This material is then crushed before being sent back to the M2500 for further classification.
The Prograde screen has an independent washing system which is said to ensure it is entirely separated from the vibration of the screen minimising the risk of plant failure.
“This is a feature of the Prograde rinsing screen in that it has been designed with washing in mind” explains Eunan Kelly, regional sales manager in Scotland for CDE Global.
The lower deck of the Prograde screen is fitted with polyurethane screen media (5mm aperture) and the 5-40mm material is then sent to the Aggmax 83R, which integrates several processing phases including attrition, trash removal, dewatering and sizing of the clean recycled aggregate.
After aggregates have gone through the Rotomax RX80R logwasher they are discharged to the dewatering and sizing phase, where a triple-deck dewatering screen is used to allow production of a 5-10mm, 10-20mm and +20mm recycled aggregate which are sent to stockpile via three 15m mobile conveyors.
The configuration of this dewatering and sizing phase can be altered with the option of single-deck, double-deck or triple-deck screen.
“If there is an existing mobile dry sizing screen on site this can be employed at this stage allowing for specification of the single-deck dewatering screen on the Aggmax,” says Eunan Kelly. “The advantage of the two or three-deck screen is that it can save considerable space on site by removing the requirement for an additional dry sizing screen.”
The -5mm material liberated from the 5-40mm fraction is sent back to the Evowash sand washing plant integrated on the M2500 to be combined with -5mm fraction from the initial screening phase, and this is delivered from the Prograde sump to the Evowash dewatering screen, which is split to allow production of two sands.
German manufacturer
This is why they are usually left in the background. “Nevertheless, they play a very important role in the preparation of mineral raw materials and that’s why we offer such a large selection.”
With its Mobiscreen series (screening areas from 3.4m2-18.4m2), similar to its mobile crusher plants, Kleemann makes a distinction between plants for the contractor market (Contractor Line) and Quarry Line, plants designed especially for the needs and conditions in the tough quarrying business.
“The Contractor Line screen plants can be used very flexibly, both with regard to the material to be screened, and to the operating location,” says Kleemann. For example, the smallest plant, the double-deck Mobiscreen MS 12 Z, is designed for coarse material; has a screening area of 1,220mm x 2,750mm (upper deck) and can handle feed capacities of up to 200tonnes/hour, while larger models the MS 14, MS 16 and MS 19 are traditional classifying screens and are available in a double-deck and triple-deck version (only MS 16 and MS 19). With screening areas from 4.2m2-9.3m2 material removal capacities of up to 500tonnes/hour are said to be possible.
Kleemann says its Quarry Line plants are particularly interesting for linked machine combinations: similar to the crushing plants in the Kleemann Quarry Line they have diesel-electric drives, and it is possible to install an electrical interlocking device with upstream crushing plants.
Its MS 23 D’s screening area of 18.4m2 across the upper, mid and lower deck allows it to achieve total screening outputs of up to 800tonnes/hour.
Major Wire has produced Flex-Mat 3 Double-Wire self-cleaning screen media technology which it says has been used in more than 20,000 applications worldwide.
A side-by-side wire design “adds a slight spring to the wire that absorbs impact from heavy material or when it is dropped from a longer distance,” and the product’s vibrating wire technology combined with the side-by-side wire design is said to help eliminate pegging on top decks and the “popcorn effect often seen when single wire is used to screen high-impact and heavy materials.”
“Distinctive lime-green polyurethane strips bond individual wires as they run from hook to hook and allow them to vibrate independently at different frequencies, eliminating blinding, pegging and clogging,” says Major Wire.
Flex-Mat 3 Double-Wire is available in wire diameters up to 9.5mm and opening sizes up to 101.6mm.
TASK FOR HERCULES
Stelex Construction Equipment has completed the installation of its first HT182M heavy duty mobile Hercules trommel in Australia.
The deal was completed in conjunction with Stelex’s Australian representatives
The customer’s ongoing material supply contract requires very high daily tonnages on strict time deadlines and so reliability was a key issue when purchasing the machine.
The trommel also had to be very hard-wearing due to the tough material conditions on site.
The new HT182M trommel, mounted on a steel skid frame, consists of a 1.8m diameter x 8m long barrel and is producing clean sized stone for a range of applications from contaminated as-dug material and current waste material at a rate of up to 500tonnes/hour. The wear resistant hopper is being fed via excavator and the feed rate and barrel rotation speed is variable to suit the customer’s individual material characteristics. Fines material is removed from under the trommel via conveyor for further site processing.
Different barrel aperture sizes were made available to the customer so that alternative sizes of stone can be recovered to suit other future projects.
“Additional products are now also being produced on site over previous working methods along with reduced waste and this has given added value to the customer since the installation of the trammel,” says Stelex.