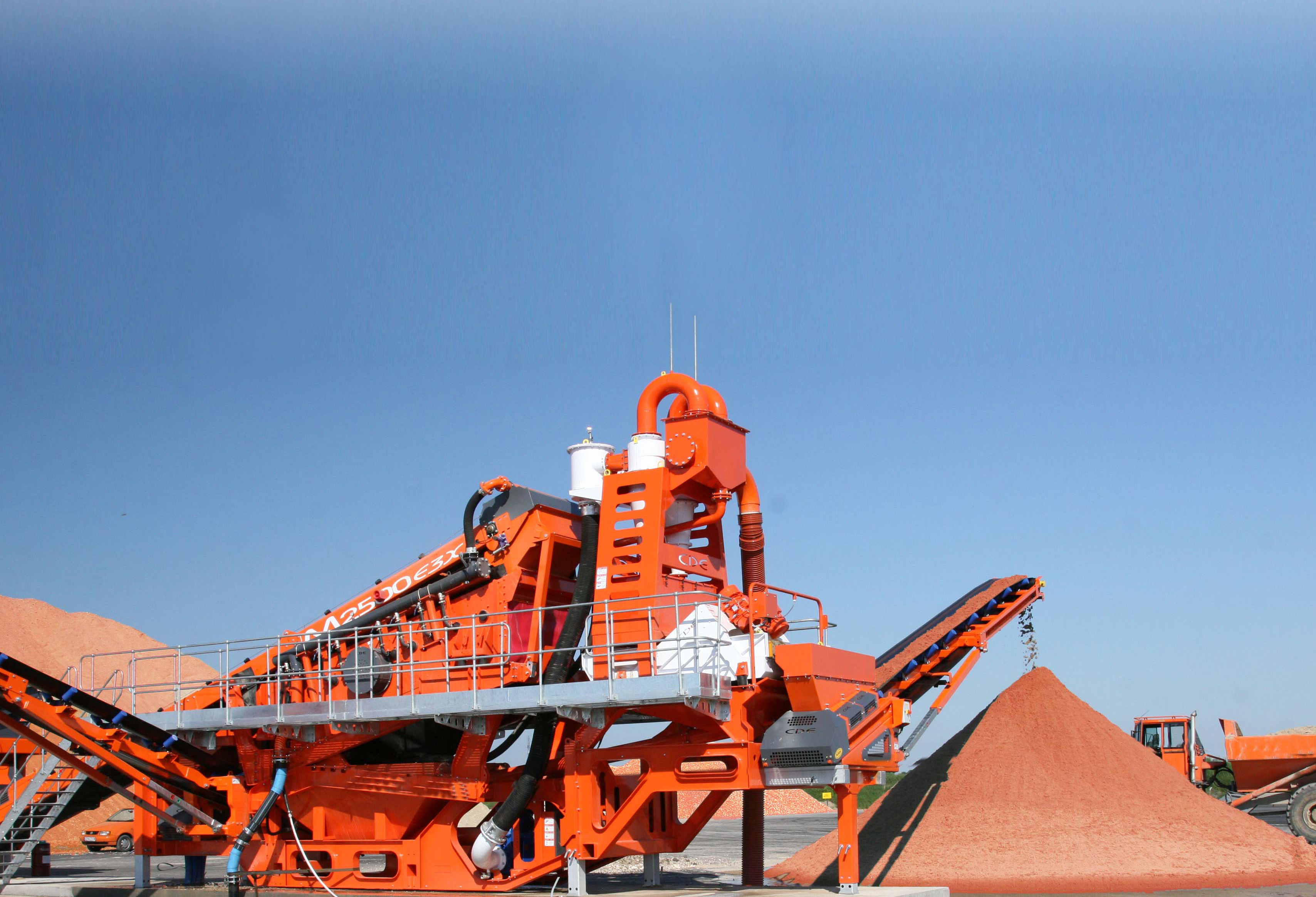
In their latest opinion piece for Aggregates Business, Aggregate Research Ltd, providers of strategic and operational advisory services across aggregates and related industries, look at whether innovation in the aggregates industry is a threat or an opportunity, focusing specifically on manufactured sand.
In today’s world we embrace change on a daily basis. Just a few decades ago we were still sending greeting cards by post, driving around with paper maps and using printed address books to store our contacts’ details. Look at us now: our tiny smartphones are packed with applications that make our lives easier, and almost all the information in the world is accessible instantly on the web. This change happened so fast that there is now a growing perception that cultural and behavioural change is needed for almost everything we have ever done (communication, health and safety, business process, continuous improvement, sales, environment etc). What does this all mean for the Aggregates Industry?
On the one hand, the aggregates industry is a mature and seemingly sustainable business from a medium-term perspective: Nobody really doubts that the world will need at least some aggregates to produce concrete and asphalt in ten years’ time. Despite that, high entry barriers and extended development horizons make investment in aggregates rather unattractive: The permitting process is usually long, arduous and not guaranteed, the product is sold at typically very low margins, the industry seems reluctant to embrace technology, and its workforce is ageing. Almost every aspect of our business is conservative! In addition to that, we suffer from increasingly aggressive lobby groups, an image of environmental unfriendliness, and an ever-growing threat from recycling, both of construction materials, and recycling of materials from outside of the construction materials’ vertical to be used in competition with our products (e.g. recycling plastic bags as a substitute for sand in concrete ¹).
On the other hand, this pressure pushes the industry to get more and more sophisticated as the demands on our products become ever greater. There is definitely room for innovation that smart aggregates producers could embrace. A perfect example of this is the increasing specification of single-sized aggregates. Obviously, producing these aggregates is more expensive, and typically it results in the production of greater quantities of lower value fines. A great, and ultimately inevitable, area for innovation is manufactured sand, but unfortunately this is another opportunity that the aggregates industry has never really understood.
“The aggregates’ industry typically has branded any crushed product that is less than 4 mesh (4.75mm) as ‘manufactured sand’. This of course is not the case. Manufactured sand should be a product that you have intentionally produced, not merely the waste fraction of a process that is targeting larger aggregate sizes.” ²
We reproduce this quotation to argue that not much has changed in the fifteen years since it was written: Quarries are still trying to palm off crusher dust, sometimes after spending a great deal of money fruitlessly washing it, onto ready-mix units that still don’t want it, but are forced to consider it because it’s so cheap. To produce sands from crushed rock, whether to replace ever-dwindling supplies of naturally occurring sands, or simply to reduce the huge amounts of unsaleable crushed rock fines generated in many quarries, there are several key characteristics with which we should be concerned. Those related to the suitability of the source rock, perhaps best loosely described as chemical properties, may be addressed by using admixtures in the concrete-making process, but, apart from the elimination of certain specific size ranges in which deleterious material may be concentrated, there is little the crushing and sizing process can do. Other factors, however, are well within the influence of existing process technology, and chief among these are particle size distribution, shape, and surface texture.
The particle size distribution of manufactured sand is controlled by screening or sometimes by other methods of classification, the latter usually involving water, which brings its own problems. Until recently, this grading was usually governed to a great extent by the output of the crusher(s), and the breaking characteristics of the rock, but in the last few years, more interest has been shown in means of modifying the natural pattern of breakage, in particular to increase the sub-1mm particle population at the expense of coarser sizes, in order to improve packing density in concrete mixes.
The classification process has no effect upon either particle shape (or indeed on surface texture, as this is a property of the parent rock), so it is necessary to impose improvement with the use of suitable processing. Traditional rock crushers, whether compression (cone) type, or impact (blow-bar or hammer) type, can be made to produce adequate shape in coarse aggregates, but typically product below about 6mm (¼inch) contains a high proportion of flaky or elongated particles, resulting in many of the problems inherent in using such material as a sand substitute. Grain shape is a function of the crushing process (and, of course, the natural cleavage and fracture characteristics of the parent rock). Suitable shape is generally described, unhelpfully, as cubical, the ultimate expression of which would be a shape enclosed by six identical square faces. In contrast, we should try to produce a shape that has good volume to surface area ratio, and an easily-packed form, to minimise the amount of binder we need to stick it together in the form of concrete. Given these attributes, it will automatically tend to assist workability, unlike our cube! The ideal form can perhaps be described as equally dimensional, and without sharp corners and edges.
REFERENCES and ACKNOWLEDGEMENTS:
¹ http://www.aggregateresearch.com/article.aspx?id=30898
² Hudson B P. “Crushers affect Product Quality”, Quarry magazine, April 1999
³inter alia ICAR Research Report 102-1FManufactured sand need not mimic the natural product: in fact manufactured sand can have some advantageous properties entirely due to its dissimilarity to natural sands. For instance, natural sands must have nearly all of the microfines (which would otherwise be beneficial) removed because of what they might contain, where there is normally no reason for such restriction on crushed rock. Much successful research has been carried out on the inclusion of high levels of microfines in manufactured sand (but rarely adopted in practice as yet)³.
And while none of the above is new, there still is a general reluctance, in Europe at least, to invest in equipment or processes, and quarries still want to “lose” their most costly product at low prices to concrete customers that hate the stuff but can’t afford to ignore it. We could do so much better.