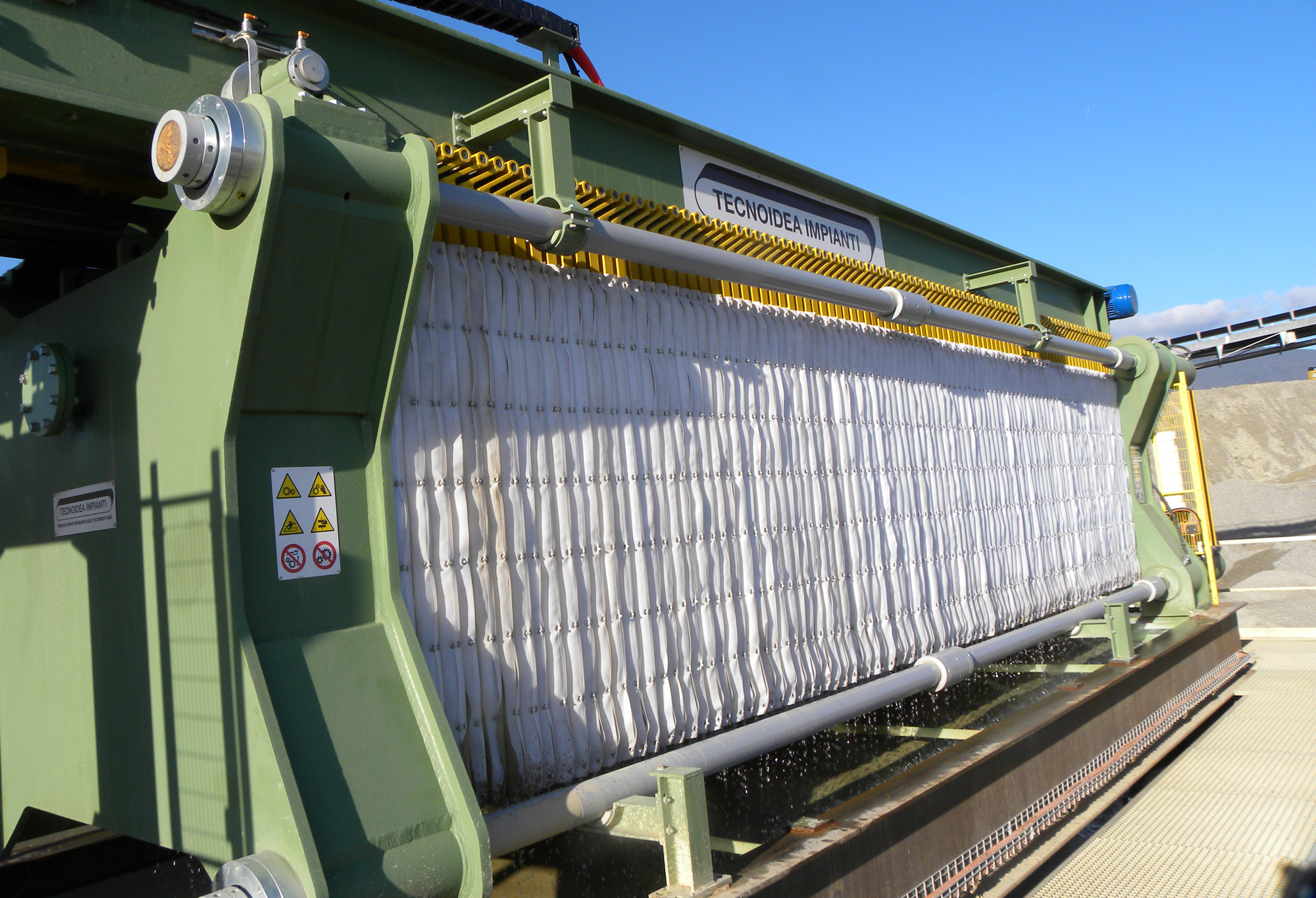
Innovative water recycling, management and filtration solutions are in demand in Europe and further afield, as Guy Woodford reports.
The G:Max gully waste processing plant from
The West Midlands-headquartered firm, who installed the G:Max plant in January 2013, are renowned at their east London facility for handling a variety of tankered waste including gully waste, road sweepings and wastewater from utility companies.
“With our scale of national coverage and in particular for our waste management services from liquid treatment centres to recycling centres, it’s imperative that our plants run to the absolute optimum capacity at all times where possible,” says John Edwards, Operations Director of RWR. “The CustomCare offering from CDEnviro has allowed us to achieve this at our Stratford site through regular on-site visits, excellent response times, professional and knowledgeable engineers and even ongoing telephone support if and when required.”
Edwards says that the CDEnviro CustomCare team have been a “pleasure to work with” and the engineers have always been responsive to RWR employee requests, regardless of when and how soon their assistance is required.
He adds: “The fact that we purchased a second plant from CDEnviro is testament to the solid working relationship that we have developed since the initial install. We have regular communication with their team of engineers and their approach is very much proactive. They also take on board any ideas that we may have ourselves with regards to any specific results that we want to achieve from the plant.”
CDEnviro CustomCare Manager Fergal Campbell says that with approximately 15 tankers being delivered to RWR’s Stratford site daily, taking in on average 350-400m³ per day, it was vital for the company that the CDEnviro G:Max plant performed to the maximum level of productivity. “Not only does our design allow us to achieve this on behalf of the customer, but the service and support provided following commissioning is just as imperative to ensure the highest volume of reclassified waste recovery, which ultimately allows RWR to significantly reduce costs associated with landfill tax,” explains Campbell.
A network of CDEnviro CustomCare service engineers throughout the UK are said by Campbell to be on hand to offer on-site assistance and maintenance support should the need arise. At each individual site visit, a plant audit and report is generated and this is shared with the customer to give them full visibility on the condition of their plant and any potential recommendations for future operations. The site visits also provide the perfect opportunity for CDEnviro to carry out any practical improvements or calibration checks.
RWR prides itself on the fact that 0% of the waste it handles is sent to landfill. The introduction of the G:Max system from CDEnviro means the system can now take in a much wider range of wastes to be processed without the problem of blockages. Overall 40-50% of the incoming material is sand which is recycled through this process and diverted from landfill, representing a huge saving overall. The G:Max recycling system is said to be suited to any waste handlers operation regardless of plant size as the equipment is compact enough to fit in an area the size of a single car parking space.
CDEnviro is said to have tailored the G:Max system specifically to RWR’s requirements by designing a system that could receive solid/liquid waste fed from an excavator bucket to suit their existing equipment on site. CDEnviro can also tailor service support packages for customers following plant commissioning.
Italian water filtration solution firm
The firm has sold a FB/2000-160 four-piston filter press to a south-east US-based aggregate quarry company which was due to be shipped in September 2014. Another firm in the same aggregate quarry company group is also said to be keen to order its own F&B filter press. These and other US-based sales are being led by Phoenix, F&B’s new North American dealer.
“Previously, many quarry sites did not have water recycling facilities, which is surprising given that there are tonnes of material needing to be processed each hour. The situation has changed as the US has discovered the filter press,” says Andrea Giglioli, F&B North America area manager. Giglioli says that the embracing of filter press technology was part of a wider debate on greener quarrying taking place within the US. The new FB/2000-160 filter press for F&B’s south-east US aggregate quarry customer was designed to allow it to be shipped in a container, reducing shipping costs and set-up time on delivery. Giglioli says that the FB/2000-160 filter press also offers easy maintenance.
In South America, F&B is looking to increase sales of its filter presses to mining businesses in Ecuador, Peru, Colombia and Chile. Copper and gold mines in Chile and Colombia are among those who could benefit greatly from F&B’s water recycling technology. Before each filter press is manufactured by the firm, the material quarried or mined by each potential F&B customer is checked to ensure that suitable water recycling with a filter press can take place. Nicola Zago, F&B’s South America area manager, says that some filter presses for South American customers are also adapted so that they can work efficiently many thousands of feet above sea level. In South America, says Zago, there are also new rules aimed at improving water drainage and recycling in mines.
In Europe, Zago says F&B sees big possibilities in the French quarrying market. “The quarries are still working well there. Italy represented around 65-70% of our filter press sales five years ago, now it’s 10%. In France, we’re talking with companies about recycling water from ready-mixed concrete.”
Another potentially strong market for F&B is Russia. “It’s growing very strong on water recycling. At the end of 2013, we sold two big filter presses through an Italian engineering company to a mine in South Russia. We’re also working with companies in Australia involved in road construction and tunnelling projects,” says Zago.
Tecnoidea Impianti, another Italian water filtration system company, sees growth in manufacturing bigger sludge washing plants, as quarries expand in size and shift to longer daily production hours. The firm has traditionally manufactured plants for small to medium sized quarry firms.
“We’ve noticed a lot of smaller quarries closing in Switzerland, Germany and Italy,” says Fiorenzo Baietti,
Mainly used as a processing site, the Vitali Quarry has a Tecnoidea plant capable of processing 6,000m³ of water/day and Baietti says the site, along with other larger quarries, has seen great operational and environmental gains by deploying the latest water filtration plants.
“The quarry is based here because of the amount of new roads being built north of Milan. It’s typical of an operation like this close to an Italian city. This site only uses one water recycling plant. Around 2,500 tonnes/day of sand and 1,000 tonnes/day of concrete is produced here. Two to three hundred trucks arrive a day with material that needs to be washed and processed.”
The latest Tecnoidea water recycling plants are, says Baietti, proving popular among quarry operators outside Italy. “One of the latest plants is being used at a quarry near Geneva [Switzerland]. I think 70% of our business is around waste-water treatment in quarries,” he adds.