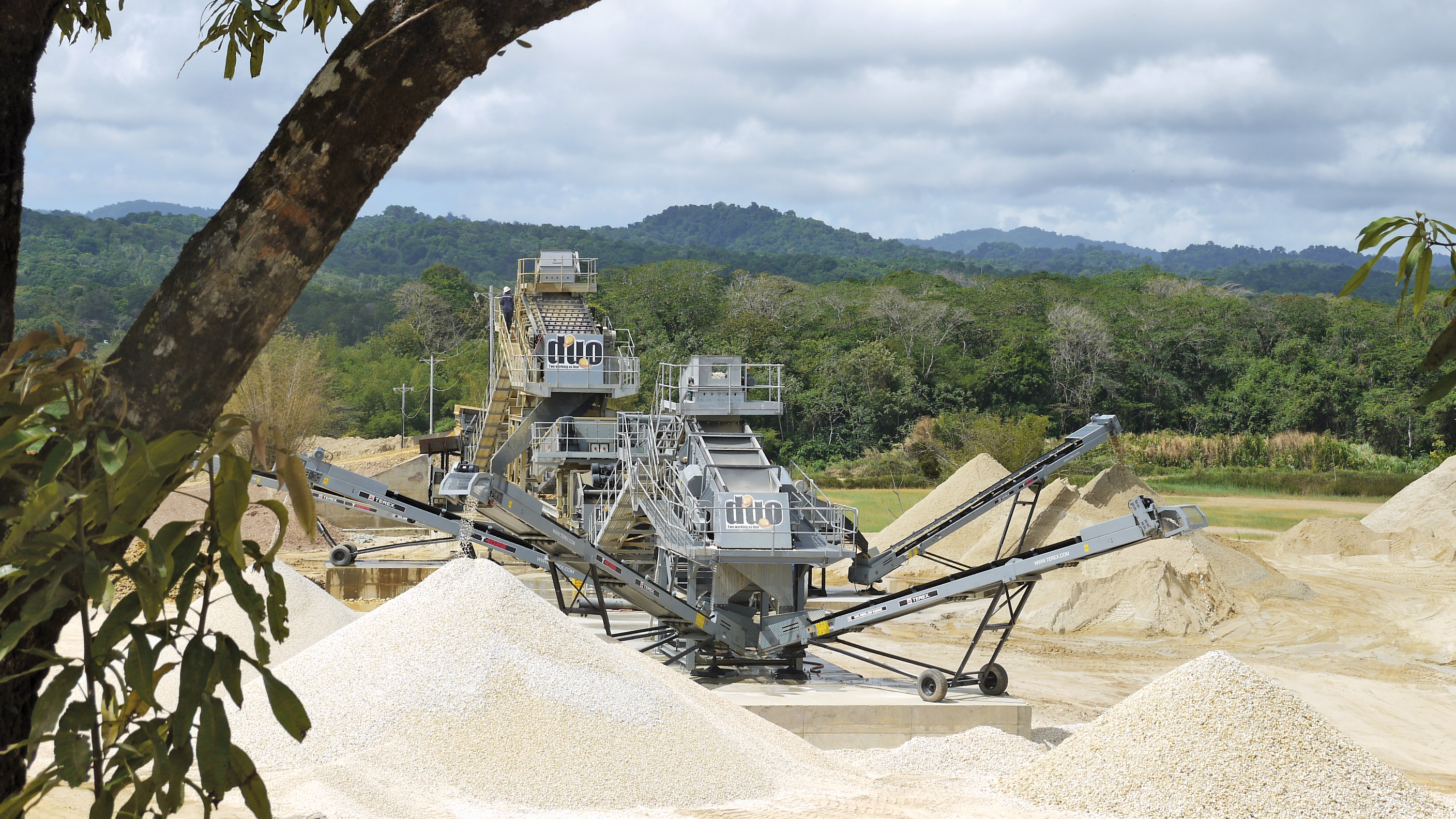
A custom-built Terex Washing Systems’ sand and gravel wash plant has been installed at a site in the Caribbean. The plant was installed for the Northern Ireland company by its global distributor, DUO, at the Readymix West Indies (W.I.) site in Valencia, Trinidad.
“The Trinidad sand and gravel wash plant is a demonstration of another complex plant offered by DUO and TWS. Both DUO and TWS carefully considered the customer’s specific needs and manufactured a custom plant. This is supported by DUO’s specialist team of engineers, applications and after sales technicians from initial conception through to final commissioning, all of which receives support from our engineering team,” says Sean Loughran, director of TWS.
The company chose to work with DUO, and after analysis of Readymix’s specific requirements, and paying particular attention to the varied high silt feed material, DUO proposed a custom
At the 210.5 hectare site, 60% of production is sand; 30% is aggregate and 10-15% is waste (silts pond).
“DUO and Terex thoroughly investigated the product to be processed, analysing it thoroughly, and from this designed a bespoke plant most suited to our individual needs,” says Ravi Singh, quarry manager for Readymix (W.I.).
“In addition it provided a dedicated team of engineers, sales and after-sales technicians to support throughout the plant installation and commissioning process.”
The plant, currently operating at 200tonnes/hour, consists of an H 9 feeder; 206R screen box; FM 200 C cyclone; 146 dewatering screen; PS 200R logwasher; 165D dry screen; two lattice frame feed conveyors and four TC 4026 conveyors to achieve the customer’s desired grades.
The natural clay-bound sand and gravel feed material is delivered to an H 9 feeder vibrating grid which removes the 100m+ material. The inclined lattice frame feed conveyor, designed and built by DUO’s manufacturing division, then delivers the material to a 206R two-deck rinsing screen to get an initial effective grading. At this stage, the top deck removes the +75mm material which is stockpiled using a TC 4026 conveyor. The bottom deck removes the 6mm–75mm material, while the material below 6mm is pumped into a FM 200C cyclone, where a 0-6mm instantly saleable sand is produced.
The Terex FM 200C cyclone is a sand recovery unit with a centrifugal slurry pump, twin hydrocyclones, a collection tank and a dewatering screen. It can produce two grades of sand but in this plant the customer opted for one grade.
The high and varied levels of silt content in the material means the aggregates need additional scrubbing to be cleaned to specification, and this is achieved through the PS 200R washer unit. Dewatering screens are fitted to either end of the machine, which consists of a trough and two spiral axles, counter rotating to each other, with exchangeable blades to intensively scrub the feed material. Friction from this process breaks down clay conglomerates and allows scrubbed material to be stockpiled.
After passing through the washer, the aggregates are discharged onto a second DUO lattice frame conveyor. These 6mm–75mm aggregates are delivered onto a 165D two-deck dry screen to achieve a three-way split, classifying material into the customer’s desired grades, 6–10mm, 10–20mm and 20–75mm.
Dirty water from the FM plant, containing material below 75 micron (silts/clays), is sent to a series of ponds which are set up so the silt drops to the bottom and clean water weirs over the top, producing clean, reusable water.
The entire plant is controlled and monitored from a central PLC electrical control panel housed in an ISO 20’ container. The panel is programmed for automated start up and shut down sequences and was fully wired and programmed before leaving the factory.
“The plant is effectively addressing Readymix’s problems. It is achieving excellent results by being much more efficient while generating outstanding commercial output and dealing with the demands of the construction market,” says Fergal McPhillips, sales manager TWS, following a recent trip to the Trinidad site.
Readymix (W.I.) is a member of the TCL Group, a leading producer and marketer of cement and ready-mix products in the Caribbean, where it is now the single largest producer of pre-mixed concrete in Trinidad and Tobago.