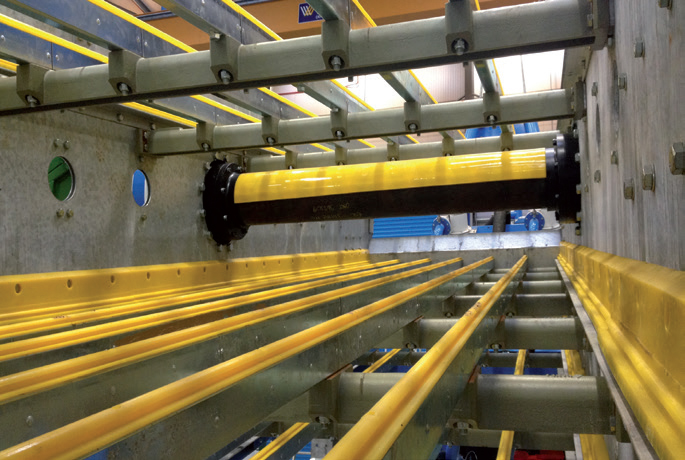
Greater efficiency is a key feature of the latest washing solutions to have come out of Europe and the US. Guy Woodford reports.
The company’s sand and gravel reserves were running low at its Stannochy Quarry site in Brechin, northeast Scotland, prompting a recent move to a new site at Struan Quarry, in the nearby village of Edzell. The firm also needed a new wash plant as their current system was old and becoming inefficient. The company chose an AggreSand 165 wash plant to help produce their premium sand and gravel products as it addressed a high silt problem and was capable of producing three aggregates and two sands that customers required.
Trading for more than 70 years, The Geddes Group is a family firm originating from an agricultural base, where they still own and operate farms as Geddes Farms. The Group also offers a full range of earthworks, tipping, recycling and muck away facilities, quarry aggregates, asphalt and ready-mix concrete products. Headquartered in Arbroath, northeast Scotland, The Geddes Group also has depots, quarries and plants throughout east and central Scotland.
The Geddes family were the first customers to see the world’s first AggreSand in operation, following the official launch event, and again at the
It was following these site visits and several consultations with TWS and their Scottish distributor,
Frank Geddes, Geddes Group’s managing director, Neill Geddes, the Group’s plant director, and Graham Geddes, the Group’s director, said: “I immediately saw the benefits of the plant and it was evident it was the solution for Geddes. The access and serviceability features off the machines, along with the rollout centrifugal pumps and roll out chute work, were especially valuable features.”
TWS distributor in Scotland, Blue Group, Scotland, and TWS applications and engineer teams worked closely with the Geddes Group, initially to identify their specific requirements in terms of desired products and specification. This entailed several sites visits, feed material analysis, plant drawings and design modifications to suit their specific spec. Samples of the feed material were sent for further testing at TWS headquarters in Dungannon, Northern Ireland. A full civils and plant layout drawing was provided, outlining the water and electrical; input/output points.
The high sand to stone ratio suggested that the high capacity plant would be the most suited solutions for their specific needs. The service and support from TWS, along with their distributor, is typical of what customers can expect when purchasing a TWS product. TWS offer their expertise and highly skilled team of engineers to assist and guide the customer from the initial conception to final installation. The plant was installed and fully commissioned at the Geddes site in November 2014, becoming the first AggreSasnd to grace the Scottish shores, with a further one since installed at another site in Inverness.
Neill Geddes added: “The plant has been producing effectively since it was installed. The HMI Control system was a feature that struck me. The ability and ease of obtaining live data in terms of water pressures, flows, cyclone feed pressures as well as motor amp reading is also very impressive.”
At Stannochy Quarry, the feed material, natural sand and gravel, is pre-screened and fed from a loading shovel onto a H9 hopper. The top deck is fitted out with 24mm² polyurethane modules and 12mm on the middle deck. The bottom deck is split 1/3rd 3mm and 2/3rd 5mm to produce two grades of sand, concrete and building.
From time to time, the concrete sand fraction at the Geddes Group’s new pit site can be what is referred to as ‘hungry’, but by utilising the novel AggreSand cyclone underflow blending system the company is able to transfer a percentage of fines from the building sand to the concrete sand, thus ensuring specification is maintained.
In addition, for the Geddes Group the AggreSand 165 plant produces three clean aggregates (10mm, 20mm and 40mm) for use as draining, landscaping and concrete stone.
An additional feature of the new ProGrade screens is the patent pending CDE U-Span cross members. The new cross member design is modular across the ProGrade range and also includes zero welds. As well as offering enhanced geometric consistency, the new design facilitates increased space between screen decks, allowing for quick and easy access to replace screen media.
Kevin Vallelly, CDE Global’s product development manager, said that as well as the introduction of the company’s patented technology on a number of screens and dewatering screens, it will also be incorporated on the new EvoWash 100 range of sand washing plants and across the M2500, M3500 and M4500 portable washing plants and the R2500 primary screening unit.
The new ProGrade screen design system is now available on the ProGrade P2-75 (2 deck 5m x 1.5m screen), P3-75 (3 deck 5m x 1.5m screen) and P2-108 (2 deck 6m x 1.8m screen). The new design will also soon be offered on the ProGrade P3-108 (3 deck 6mx1.8m screen).
The new Hydro-Clean washing unit from
Taking a maximum feed material size of up to 150mm into its vertical drum, the Hydro- Clean employs high-pressure nozzles, rotating at 90rpm, to spray up to 90% recycled water on the material with pressures up to 2,900psi. The washing unit removes silt and clay particles as small as 63 microns from mineral mixtures and, with its short retention times, can process up to 400tonnes/hour, depending on model size and application. Due to its compact size and weight, overall operating and structural costs are considerably lower than with traditional washing systems—which also require more equipment and a greater footprint.
The Hydro-Clean is said to consume little water and power. Water consumption ranges from 27 to 211gpm, depending on application and model size. Ideal for use in clay-heavy material deposits, dirty material is fed via hopper to a vertical washing drum, where highpressure nozzles mounted at the top rotate and spray the material with water. The water streams spread and wash the material at pressures of up to 2,900psi, effectively interacting with the material to break up agglomerates and clean the particles of stubborn material. The turbulence in the drum creates additional scrubbing and abrasive forces that enhance the cleaning process as the material travels down the drum cylinder. High-pressure streams of water are injected into areas of the rock (holes, cracks, etc.) that are difficult to reach with traditional cleaning methods like log washers or screws – creating a cleaner product that generates higher selling value.
During the cleaning process, the washed material works its way down the drum and exits onto a discharge conveyor that leads to a standard wash screen, removing any remaining dirt or clay still on the stone as it fractionates the material.
The resulting dirty water flows through polyurethane screen mesh installed in the sides of the washing drum. It is collected by a waste water pipe, which sends the water to a treatment system for additional fine screening.