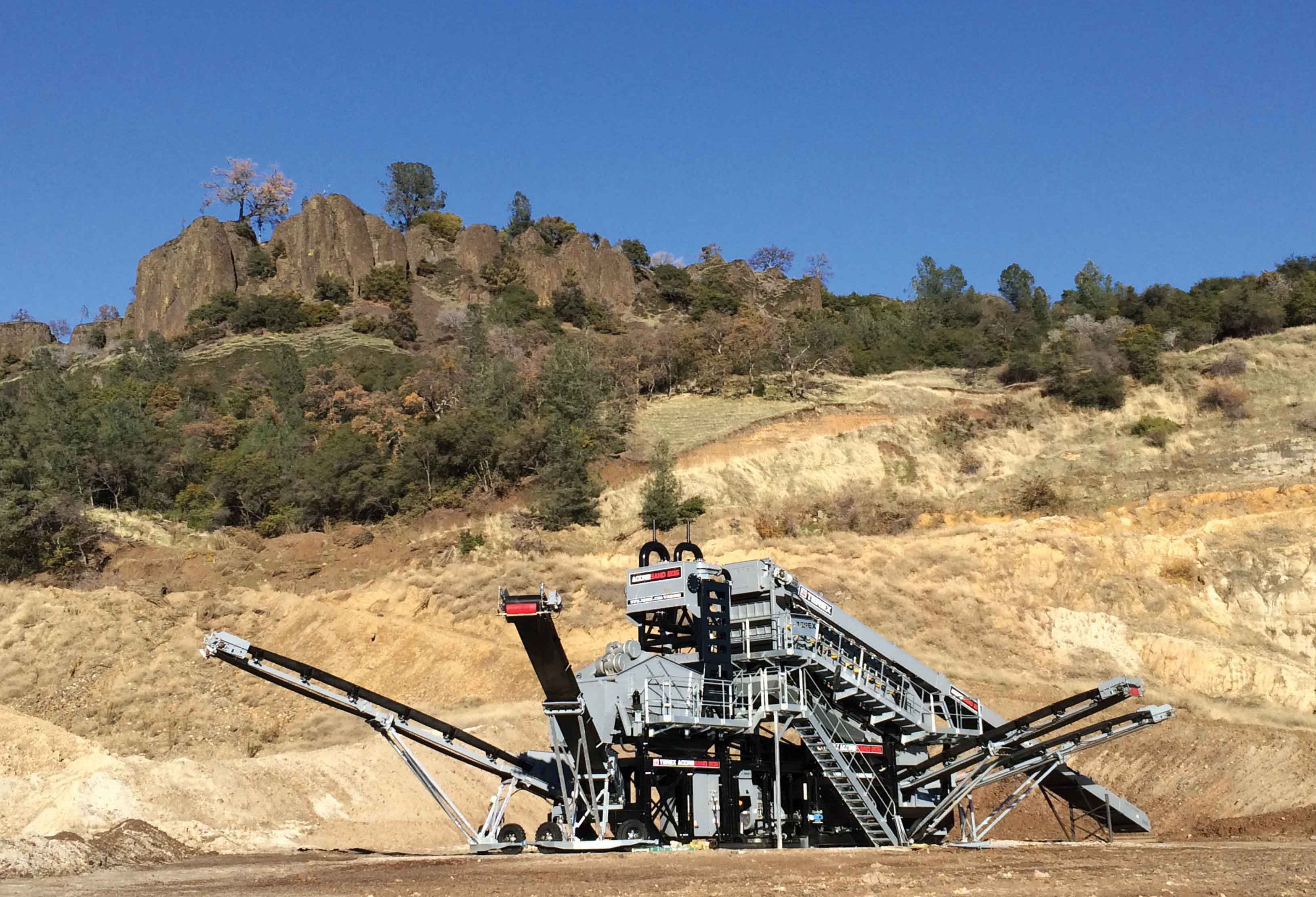
RSSA major aggregates company has installed a new wash plant for its multi-disciplined operations in Scotland.
The plant, supplied and installed by authorised distributor Blue Machinery Scotland, is capable of processing in excess of 200tonnes/hour of quarried sand and gravel feed material, and is producing a range of aggregates and concrete sand at the quarry, which also produces sand and gravel, decorative aggregates and ready-mixed concrete.
The Aggresand 165 is of modular design and construction, and it can be containerised for ease of transport, being fully pre-wired and pre-plumbed.
At Capo Quarry, quarried aggregates are fed into the plant’s 9m³ feed hopper, which features a remote-control tipping grid. Material is then fed onto an inclined conveyor which delivers it to the first processing stage of the Aggresand 165, a 4.8m x 1.5m triple-deck rinsing screen box. Equipped with individually controlled spray bars on each deck, the two-bearing screens are fitted with polyurethane modular screen media on all three decks, which wash and separate the material, leaving three sizes of high-quality aggregates: 100-24mm, 24-12mm and 12-6mm.
The remaining 6mm-0 is pumped to a cyclone system which retains all material above 75 microns and produces two grades of sand. Any residual material is moved to a lagoon to be filtered, with the resulting clean water recirculated into the system, improving water recycling and reducing waste in the process.
The TWS Aggresand 165 plant is said to be fulfilling a need for increased volumes of sand following Breedon’s recent success in winning concrete sand supplies to the AWPR highway contract, Aberdeen.
“We are very pleased with the large tonnage produced by this versatile wash plant, and the modular nature of the Aggresand is a real benefit, giving us the capability of relocating the plant throughout our various sites to accommodate the production demands of current contracts. Another excellent feature is the accessibility to all parts of the plant, meaning that maintenance is straightforward. This plant’s excellent performance is proving to be a major contribution to our requirement for increased volumes of high-quality endproducts,” says Bob Hare, company production manager for Breedon Aggregates.
TWS also recently introduced 4Site, its new project management service to aid customers and distributors with the installation of TWS equipment, providing three tailored packages to choose from, Silver, Gold or Platinum. “The introduction of this new project management service is a very positive approach by TWS which can only help strengthen the brand’s position in the global marketplace,” says Austin Carey, managing director, Blue Machinery (Scotland).
“We are delighted as a distributor to be able to offer such a comprehensive management service providing a turnkey solution to our customers.”
4Site is led by Garry Stewart, project manager TWS, who says: “We believe that for rapid response, qualified and effective support is crucial in meeting end-users’ needs, letting distributors deliver on their promises as well as developing long-term customer relationships, which is exactly what 4Site will offer.”
Sean Loughran, director of TWS says that response to the introduction of 4Site from TWS’ global distributor network has been incredible and distributors are excited about offering the service to their customers.
In 2009, with another local site running out of mineable reserves, Dexter Sand and Gravel’s area manager Mike Martin, and mining engineer Scott Jinks, started looking for a new site, and broke ground at the Dexter site in the US in February 2012.
Today, the site is a flourishing operation, producing concrete and masonry sand at the rate of more than 180tonnes/hr.
“This site is a great sand deposit with a small amount of gravel that is easily separated,” says Martin.
“The challenge with this deposit is that it contains trace amounts of lignite.”
Lignite is a material similar to soft coal, and it causes problems with concrete sand because it is lighter than the sand and essentially pops out as the concrete sets, causing voids in the finished concrete.
Concerned with the quality issues caused by lignite, Martin and Jinks decided to work with
A McLanahan Lites-Out system, also known as a Flat Bottom Classifier, was settled on to remove the lignite. The system uses a pulse-type discharge to induce a jigging action that helps dilate the bed and frees the coarser organics such as lignite through the fluidised bed.
McLanahan says the gravitybased process does not require chemicals, or something like Magnetite, to help the separation.
And that the same technology can be used for soil remediation or to separate construction debris.
“The Lites-Out Flat Bottom Classifier has a small footprint on the location because it is flatbottomed along with lower head height, which decreased our pumping horsepower needed,” says Martin.
“The machine features a diverter box that allows Dexter to make concrete and masonry sand at the same time, saving time, energy and money.”
The Lites-Out System removes +50 mesh lignite from a -4 mesh feed to achieve the published specifications for lignite-free sand. McLanahan has also installed a warning system to ensure lignite does not enter into the concrete sand.
“The system helps us gradation-wise with the concrete sand but also removes any trace amounts of lignite. This makes a high-quality concrete sand which is saleable for transportation projects and general construction projects,” says Martin.
“The success of this plant, from greenfield to construction, was due to the success of us and McLanahan coming together as a team. We worked together to overcome any issues and get the job done,” says Jinks.
Dar es Salaam, Tanzania-based Estim Construction, one of the largest civil and building companies in East Africa, now owns
“Estim Construction builds high-rise buildings, so ensuring highest quality, strength and consistency in our concrete production is crucial,” says Darpan Pindolia, director of Estim Construction.
“This new CDE Global installation, which we understand is the most advanced plant of its kind in East Africa, has enabled us to optimise production and maximise our return on investment through consistency in feed rate.”
CDE says that testimony to the growing awareness in the quarrying industry of the multiple benefits of sand washing, the partnership between CDE Global and Estim Construction in Dar es Salaam was “a labour of love and an exciting breakthrough in the African market.”
From humble beginnings 25 years ago in the form of a small truck, Estim Construction has grown to become one of the largest and most respected companies in Eastern and Southern Africa, with the Dar es Salaam headquarters, and sister offices in Zambia and Mozambique.
CDE says that communication of initial needs with CDE Global was made easy as its South Africa-based business development manager was always available to talk without time zone constraints or for a visit to the customer’s site.
In-depth conversations followed, based on observations made during site visits, and effective communications with all relevant sections of the company led to the identification of specific requirements and to a sand-washing solution to be developed, focusing on Estim Construction’s priority of two different sands and maximum recycling of processed water.
“A CDE Combo X70, an integrated sand washing and water recycling system, which uses 90% less water than traditional sand washing systems, was approved by Estim Construction as its solution of choice. Bespoke additions or modifications were applied to meet their circumstances and requirements,” says Nicolan Govender, CDE Global regional manager for Africa.
“To ensure that Estim Construction had complete ownership of its operation, a CDE engineer trained an Estim Construction operator to oversee the installation and take actions based on the changing characteristics of the feed material.
“The plant is fed 50tonnes per hour to produce 4tonnes per hour of final quality washed sand. Waste and water from the EvoWash report to the AquaCycle high-rate thickener so that up 90% of the water is recycled and reused. The concentrated fines are flushed out, resulting in minimal water replenishing the water tanks.
“We could not be happier with the choice we made. Working with CDE Global, and especially their Business Manager and engineers, has been a crucial factor in achieving the best final product,” added Pindiola.
“Thanks to our CDE Combo X70 we can now complete orders for various grades of concrete required for rafts, columns and slabs to produce paving blocks and other items in the knowledge that we will always meet our clients’ deadlines and produce consistent quality and output throughout the washing process.” RSS