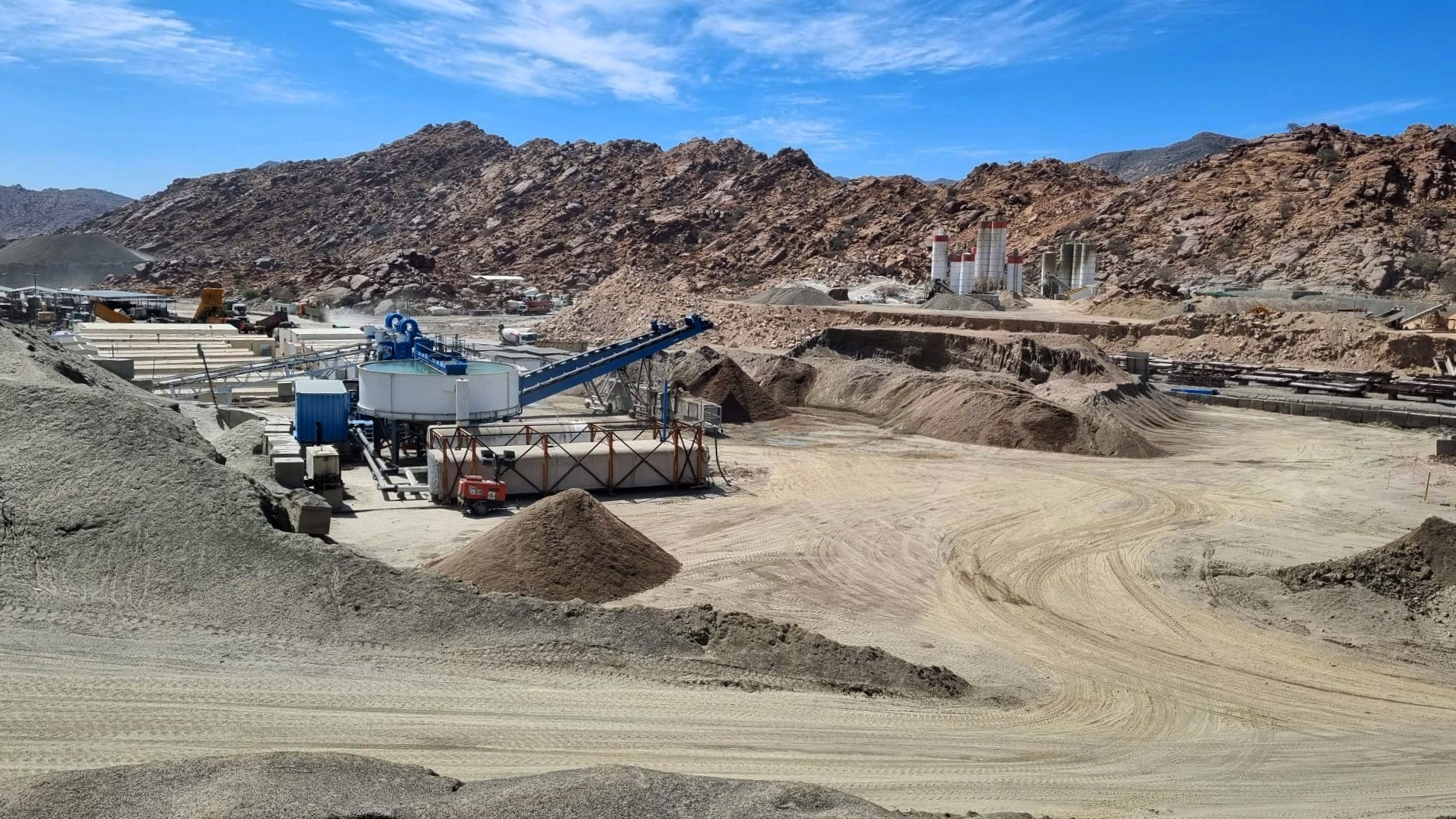
Madinat Al Wurood, also known as the City of Roses, is a new suburb in the north of the Taif governorate. Under the supervision of the Ministry of Housing, the project, part of Saudi Arabia’s Vision 2030, will see the development of over nine million square metres of land, including 112km of road networks and 5,400 residential villas in its first phase alone.
JCC, a key supplier in the realisation of the ambitious project, produces and supplies readymix concrete of varying strengths to large-scale public works and infrastructure projects throughout the Kingdom of Saudi Arabia.
To date, JCC has supplied over 425,000m3 of poured concrete to the project to construct over 1,500 prefabricated residential units.
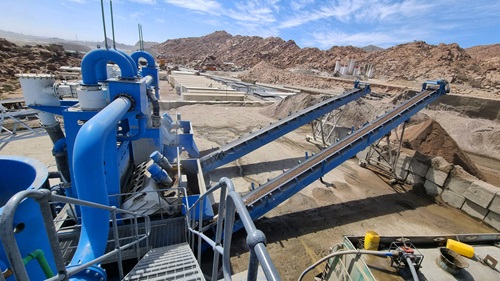
With a view to further improving the efficiency of its operation, the compressive strength of its concrete, and to reduce the environmental footprint associated with concrete production, JCC partnered with CDE to design and engineer a wash plant to efficiently process and enhance the sand equivalent (SE) value of its crusher fines.
CDE’s regional manager for the Middle East & Africa, Mr Ruchin Garg, said: “The use of unwashed crusher fines in concrete production can impact upon the end use of the final concrete product, rendering it unsuitable for higher value construction applications. It can also increase the requirement for cement in the concrete mix in order to achieve the desired compressive strength, a costly process both commercially and environmentally.”
JCC’s Taif area manager, Mr Abdelmajeed Al Kurdi, said: “Concrete is, by its very nature, a highly taxing industry on the environment. From cement manufacturing to water consumption, the process leaves a considerable environmental footprint, which we’re committed to addressing.”
CDE’s significant presence in Saudi Arabia was a major factor in the decision to partner with the washing experts, Mr Al Kurdi added.
“Washing materials is an entirely new direction for our company, and so we sought more than technology, more than a supplier. We sought a partner, and given CDE’s presence and solid reputation in the local market, we trusted the quality of its equipment and the expertise of its team.”
JCC visited Al-Tawi, another of CDE’s customers in Saudi Arabia, operating its washing technology as part of its readymix concrete production.
“Attending the reference site was a key moment in the process. Observing the technology in operation reinforced our belief that CDE was the partner of choice to help us achieve our aims with this project,” Mr Al Kurdi added.
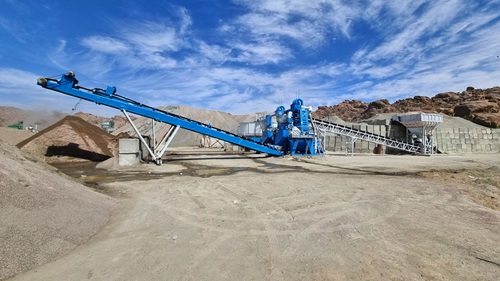
Laboratory tests conducted by CDE revealed the SE value of the crusher fines feed material used in JCC’s concrete mix to be around 50%.
“The SE value indicates the proportion of dust and clay-like material in the feedstock,” Mr Garg said.
“The lower the value, the more of that material is present. Equally, if we increase the value, then the final concrete product is stronger and requires less cement to bind.”
Using CDE-manufactured sand in the concrete mix design lowers the production of CO2 by optimising the concrete mix with less cement required to obtain the same compressive strengths.
With a view to increasing the SE value of JCC’s feed material, CDE proposed a wash plant set-up comprising two of its patented EvoWash sand classification and dewatering plants coupled with its AquaCycle thickener for water management.
A compact, modular sand washing system, CDE’s EvoWash washes and deslimes the crusher fines by ensuring low moisture product with the help of its high-frequency dewatering screen. The hydrocyclone technology provides unrivalled control of silt cut points and eliminates the loss of quality fines.
Working in tandem, CDE’s AquaCycle offers an alternative to water extraction from natural sources and the costly process of pumping water to the plant, especially in arid regions where water resources are not readily available. It significantly reduces water consumption by ensuring up to 90% of process water is recycled for immediate recirculation around the plant.
Processing up to 300 tonnes per hour (tph) of material, the CDE solution is producing 200tph of 0-5mm sand with a final SE value of 88%, up from around 50% prior to commissioning and significantly exceeding acceptance criteria of 70%.
“Our solution has delivered a significant improvement in the SE value of JCC’s material and optimised its concrete to reduce the volume of cement required in the readymix, resulting in significant savings in cement consumption,” Mr Garg said.
Mr Al Kurdi added: “As well as driving down cement consumption and boosting the SE value of our material to produce a higher quality end product, the solution designed and engineered by CDE has also delivered significant efficiency gains in terms of water management on-site.
“Already, the integration of our first CDE wash plant into the operation has transformed our business and given us a competitive advantage in the local market. We can exceed expectations, which will position us well for future success as we tender for high-value projects of major public interest.”