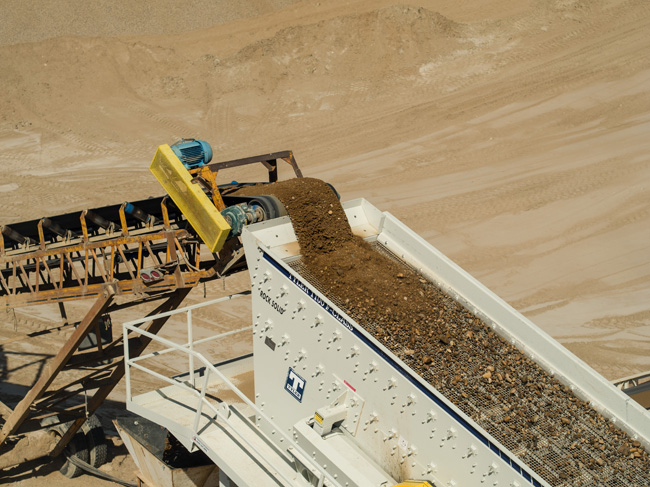
Speaking on the subject, Steve Fair, Tyler Engineered Media manager of the Haver & Boecker Niagara Canada Facility, said: “When it comes to screen media, spending a little extra time on preventative maintenance can have a noticeably positive effect on profits. Getting longer life from side-tensioned screen media sections means less frequent downtime replacing the media, as well as lower annual screen media expenses.
These four steps during routine maintenance will help catch inconsistencies that might lead to bigger, more expensive problems.
1. Check the tension rails. Look for wear, corrosion or cracks and eye the rails for straightness, which is necessary for even tension.
2. Examine all nuts and bolts and replace any that are worn, stripped or corroded.
3. Inspect the machine for balance and excessive vibration, which can lead to screen media failure or unintended machine wear. An easy way to do this is with a vibration analysis system, which measures and reports on the health of a vibrating screen.
4. When it comes time to remove and replace screen media, take a little extra time to pull off the bar rail or crown liners and inspect the steel bar rails for wear or warping. A good policy is to set a schedule for replacing the bar rail liners during each screen media change-out. Consistent maintenance will lengthen screen media life.
“While these maintenance tips will help lengthen screen media’s lifespan, it’s always a good idea to start with high-quality, long-lasting screen media. Some polyurethane hooked screen media, for example, lasts seven to nine times longer than woven wire cloth, while some that combine an engineered composite with woven wire cloth last four to seven times longer than woven wire.”
Fair adds that with the potential for fewer breakdowns and more productivity, doing routine maintenance and researching new, long-lasting screen media options is a worthwhile—and profitable—use of time.