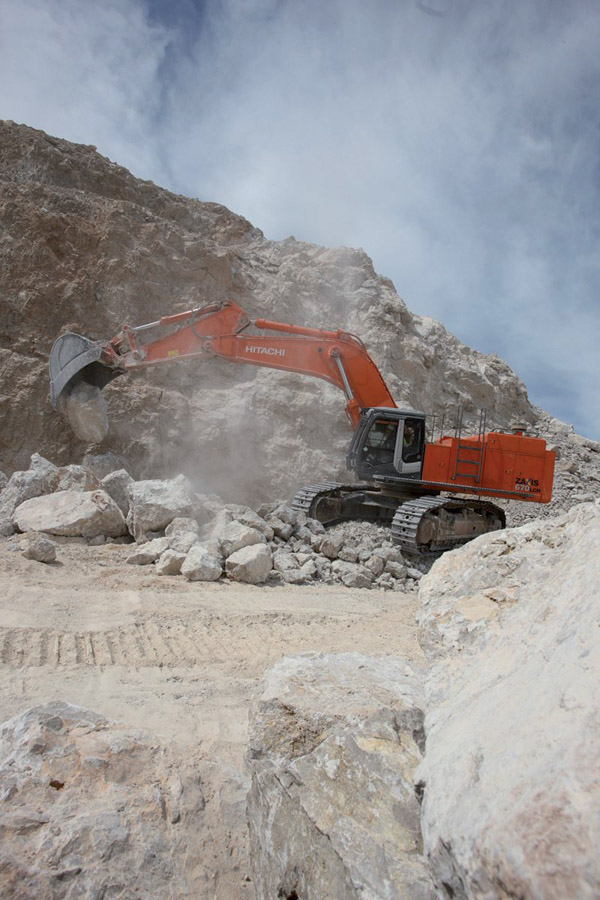
Focus on cost per tonne of production has led to growing numbers of quarry operators to investing in larger excavators. Claire Symes reports
Excavators used in quarries today are not only often bigger than those used a decade ago but are also much more advanced in terms of both technology and efficiency. And according to many excavator specialists in Europe's largest equipment manufacturers, this is a trend we are likely to see continue as operators seek to reduce costs and improve productivity.
"There is a growing trend within the quarrying market to buy machines that can comfortably meet production volumes in a bid to minimise down time and maximise residual values," said
In response to this demand manufacturers are now upping their range topping machines and, although excavators weighing in at 120tonnes are not unknown in quarries, most manufacturers are working to have 85tonne machines in their ranges. "The product that changed the market was the introduction of
Meeting the need
While the average size of excavator being used in quarries is rising, the machines still need to be matched to other equipment in the hauling and crushing system. But according to Douglas, the industry has also seen increasing demand for larger size support equipment such as trucks, crushing and screening plants.
"Quarries can decide to use an 80tonne class machine and operate a certain number of trucks or they can opt for a larger 120tonne machine and run fewer but larger trucks," said
"The trend towards larger machines has been clearest in quarries going for a complete overhaul. By choosing larger machines they can operate one excavator rather than two, which reduces costs and manpower needs. Two of the main drivers towards this have been the higher cost of fuel and rising labour costs.
"Nonetheless it is a fine line between having the excavator standing idle for long periods or having trucks waiting for loading - it all has to be matched to the on site crushing capabilities. There are situations where it is better to have more, smaller machines as there is less risk of breakdowns. This also applies to sites with a variable deposit where blending is carried out."
Powering up
One of the next significant changes to the excavator market will come in 2011 with the introduction of the next stage of engine emission laws. Some current engines almost reach the new standards now and may be able to comply with increased injection pressures, but some engines will have to look to post treatment solutions to meet the lower emissions levels.
"Engine emissions compliance will consume huge engineering resources for all OEM's over the next 6 years - up to and beyond Tier 4 stage II," said Douglas. "Of course, it is very difficult to pass on the development and installed costs to the customer, therefore we as OEM's must find creative solutions to meet the legislation and minimise the cost impacts.
"The drive for more and more efficiency and low carbon footprint requirements will see the development of alternative power, such as hybrid engines. Already the major manufacturers have started launching hybrid machines - these installations will improve in efficiency, cost and availability and will be seen more and more in the future."
Safety
Safety during operation has been significantly improved in recent years and Douglas points to the changes in cab design by way of example, "Cabs are typically being designed now for EOPS compliance and HAVS compliance as standard now to offer better levels of protection to the operator," he said.
Sinclair added, "If operated properly the features on a modern excavator make it very safe and the onus is moving away from the manufacturer and onto site. Correct operator training is essential." Walkways and access systems are already standard in some European markets, particularly, the UK and introduction of the Machinery Directive next year is likely to raise standards and result in more widespread adoption. "The Machinery Directive changes coming in December 2009 will raise the bar in terms of safety, for sure.
I am still concerned that whilst we strive to comply with these requirements, the system is not being policed properly, and is still too open to interpretation," said Douglas.
Sinclair said, "The consolidation within the industry is also helping safety systems to become more common than current legislation," said Sinclair. "But is likely to be another five to 10 years before we see sophisticated changes across the market."
Added intelligence
Like many items of construction equipment, new excavators now commonly feature satellite monitoring technology. "Transfer of machine data via satellite which is accessible via a webpage allows machine owners and dealers to monitor a range of performance statistics," said Edwards. "Details like engine performance, idle time, hydraulic performance, start and stop times and faults. The data means that maintenance can be scheduled based on actual performance and it is also possible to arrange just in time delivery for parts.
"There are further advancements in satellite monitoring to come, which will improve use on site. Data being gathered from such systems will help to further extend service intervals in the future much the same as has happened in the automotive industry - cars now indicate when a service is due rather than being based on hours/miles but that can only come through experience based on existing data.
"This will have real benefits for the quarrying sector. One of the key factors in the service interval is the final drive oil which is usually changed every 2000hours. But the amount of travel will depend on the actual application - an excavator working on a pipeline construction may spend up to 20% of its time travelling, where as a quarry machine may only spend 5% of its operating time travelling. To cover all applications the standard service interval has to be set at the higher level, so the quarry machine's servicing is inefficient but setting the interval by performance data would greatly reduce unnecessary downtime."
Further development
While excavators used in quarries are likely to benefit from performance based servicing, the way machines are used means that quarry operators may not gain as significantly from other developments. "There is a lot of standing time in quarries and generally a fixed output. As a result it is unlikely that quarries will benefit much from any further advances in machine technology," said Sinclair. "If machines become any quicker then even skilled operators will struggle to get the best use out of them." Future developments may not help to advance productivity, but they may help to reduce unexpected downtime and improve maintenance planning well as minimise running costs.