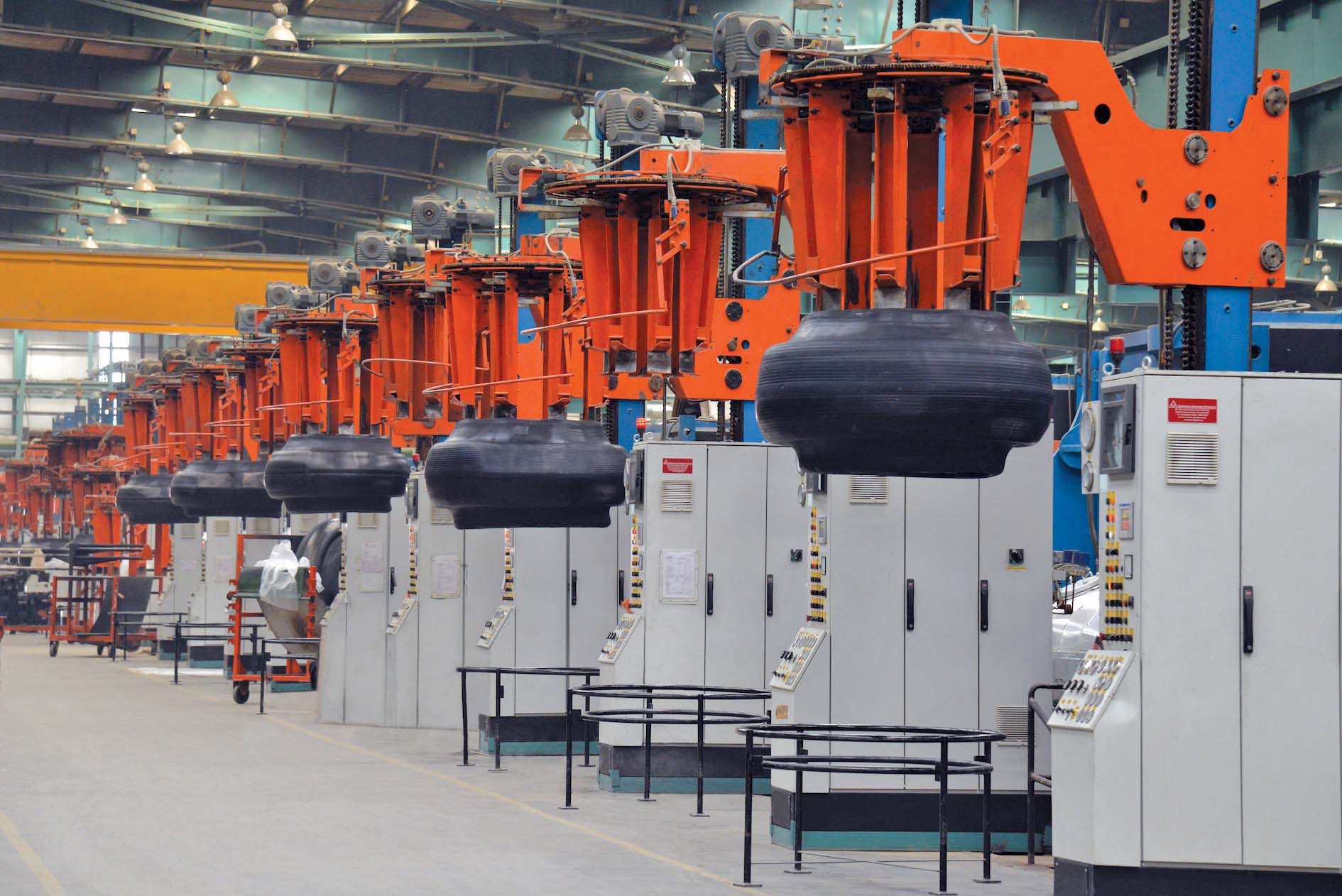
Uptake of OTR tyre stocks has slowed recently due to lower sales of medium and higher capacity rigid dump trucks, wheeled loaders and related equipment for loading and haulage. This has been caused by a slump in activities amid the Covid-19 pandemic in sectors such as coal mining, aggregates and cement production. This has affected the Indian and the wider global market, and BKT has a major presence in both.
While demand for newer tyres has been slowing down, customers are looking to extend the use of existing assets to cut operating costs. This trend is impacting all the major OTR manufacturers and BKT is looking to leverage its product offerings by adding value to product support services, while also exploring newer business areas.
Speaking to Aggregates Business International, Rajiv Poddar, joint managing director, Balkrishna Industries, said: “Demand is slow and competition is getting tougher in the Indian and global OTR markets. To drive business, we are working on multiple areas. This includes, widening our product portfolio. The key initiative is production of new ‘Ultra Large’ OTR tyres for rigid dump trucks. This will widen our product portfolio further.
"The second major strategy is towards keeping our operating costs low to pass on benefits to customers. In addition, we are exploring newer possibilities to improve product support, so the customers are able to derive optimum total lifecycle benefits from our tyres. BKT enjoys a strong brand recall in both the global and domestic markets. Our tyres are in great demand as they are of very superior composition, with an innovative tread design that helps lower the cost of operation per km with resultant lower fuel costs per hour.”
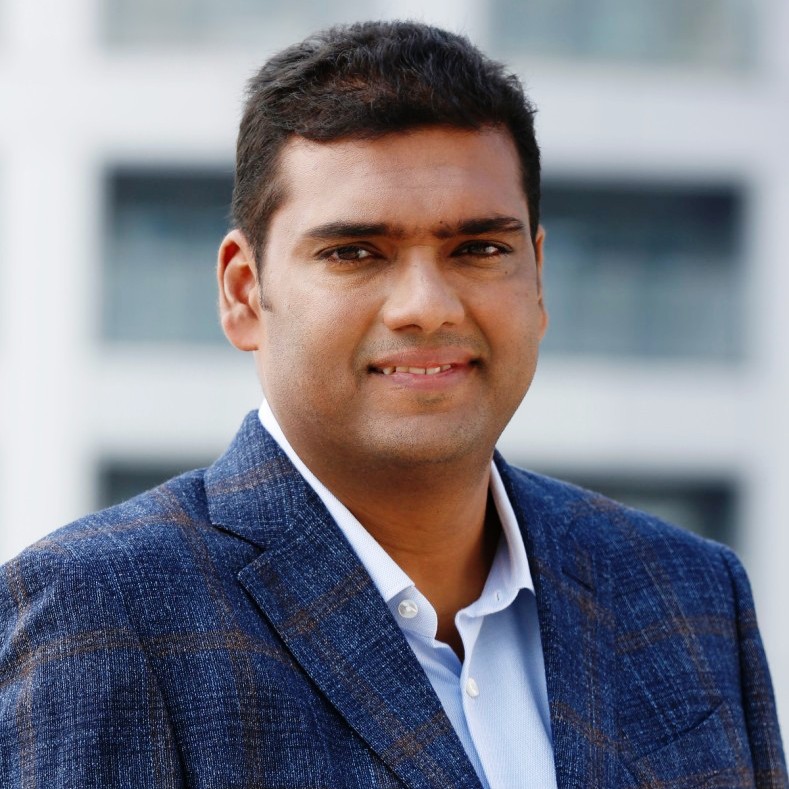
BKT says it is on course with its expansion plans and is all set to revamp its first plant at Aurangabad in Maharashtra, Western India. It is also modernising its Rajasthan production facility in Northern India and adding new products to the state of the art Bhuj plant at Gujarat in Western India.
The Bhuj plant has an advanced rubber testing facility for chemical, physical, and rapid control tests. The tests are conducted to examine the character of the rubber after mixing of the final compound. The Bhuj plant also possesses a test track which BKT says is the first of its kind in India. The track is used for endurance, performance and driving comfort of its tyres on different surfaces - ranging from uniform road conditions to rough terrains such as concrete, bitumen and farm tracks with pebbles. BKT has a production capacity of 140,000 tonnes per annum.
Poddar says: “The expansion plans are based on the long term, stable demand fundamentals from the Indian and global markets. We believe that the slowdown in demand is a temporary phase in India. The Indian economy has strong demand fundamentals in many sectors such as agriculture, mining and mineral processing which are performing well. These sectors will drive business.”
The Indian government has recently begun the exercise of allocating 50 coal blocks, holding close to 225 million tonnes of reserves, in various parts of the country. To further reduce the impact of the slowdown caused by the Covid-19 pandemic, India’s Union Ministry of Road Transport & Highways is looking to fast track road construction projects.
To widen the scope of its product offerings and sales, BKT says it is looking closely into business segments such as infrastructure construction equipment. Poddar added: “We are also looking at new segments like mobile cranes. We plan to develop advanced solutions through co-engineering alliances with international crane OEMs for both the Indian and export markets. Accordingly, we will adhere to their quality standards to deliver total lifecycle costs and will provide the necessary support services for the products.
Poddar concluded: “We have recently begun production of carbon black as one of the key raw materials for our internal use at Bhuj facility. Our backwards integration will further improve our product quality, while keeping costs down. To scale up business, we will continue to focus on the replacement and retail markets with our on-site, advanced, customised, product support initiatives.”