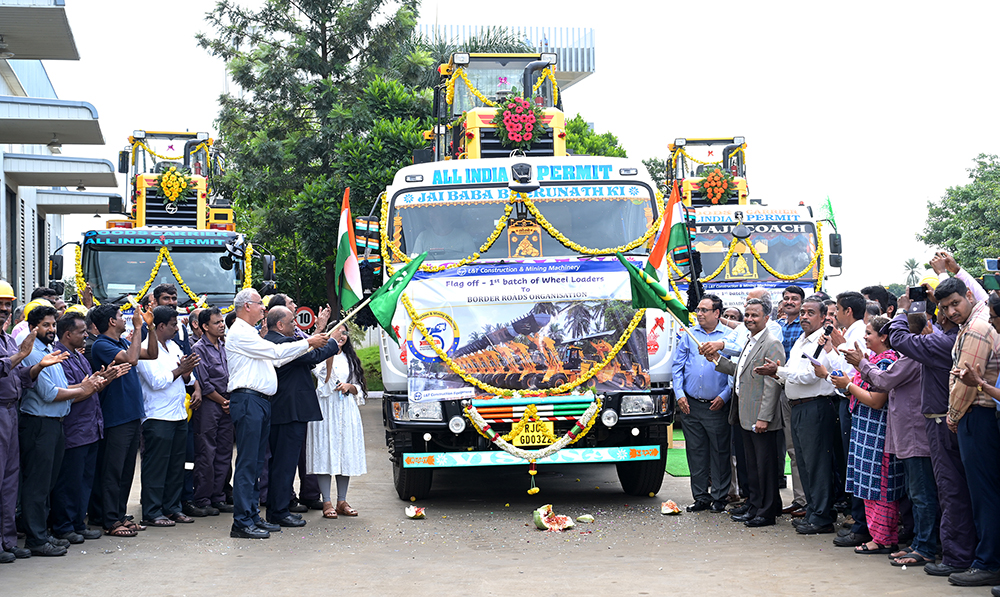
Demand for aggregates continues to remain strong, led by the ongoing large-scale expansion of India’s road construction sector. It is also buoyant due to the major ongoing extension of India’s railway network, with the laying of new lines, and the doubling and tripling of existing lines, requiring vast volumes of aggregates ballast.
One important rail capacity expansion project led by Indian Railways is the doubling of the line between Bondamunda in Odisha and Ranchi in Jharkhand state in Eastern India. This includes the laying of 158.5 kilometres of new track. Another major works is the laying of a third line, stretching 155.5 kilometres between Narayangarh in Madhya Pradesh, Central India and Bhadrak in Odisha to allow increased movement of freight trains with higher parcel loads.
Despite the health of the Indian transport infrastructure development sector, paradoxically, demand for vital off-highway equipment used in quarry-crushing-supporting activities and road and rail construction works including backhoe loaders, wheeled loaders, rigid dump trucks (RDT’s), and compactors has been suppressed for much of this year. Commercial quarry owners, main contractors, subcontractors and renting agencies have been putting into abeyance acquisition of new equipment for some time, partly due to the higher initial cost of equipment featuring engines conforming to new CEV-IV emission norms. Rising diesel fuel costs have also reduced equipment purchases, as have increased product support and services costs accompanying newer-range off-highway machines.
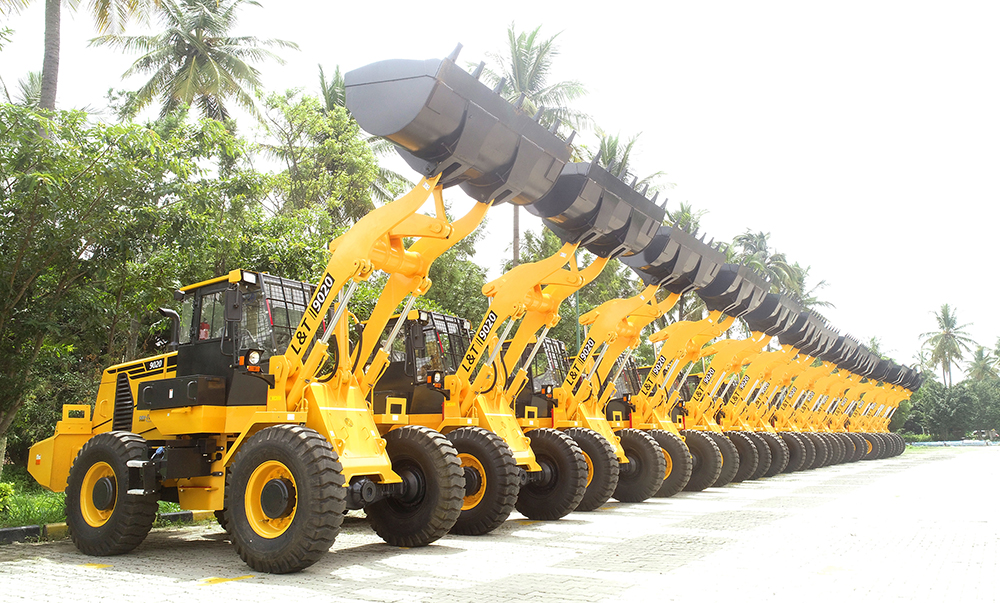
Research by Aggregates Business International has found that while big Indian transport works contractors with large order books have been acquiring some new equipment, the pace of acquisition has been slower in 2022 compared to 2021. Big road contractors like Dilip Buildcon, G.R. Infra, H.G. Infra, APCO, Gawar Construction, Patel Infra, Monte Carlo, Ashoka Buildcon, and KCC have been acquiring 10-20 excavators this year. However, there has been greater purchasing activity by medium and smaller-sized road contractors like Mundan Construction, Saran Construction, and Ravi Infra who have been purchasing many excavators. The bulk of the demand has been for the 20-ton class machines, with the market size hovering around 20,000+ units this year. The Indian excavator market overall is projected to reach 25,000 units a year by the close of the final year on 31 March 2023.
While wheeled loader demand has been lower in 2022, manufacturers remain optimistic about sales growth potential given the backdrop of firm demand fundamentals. Some of this stems from a focus on urban mass rapid transport infrastructure that will necessitate larger volumes of aggregates, sand, cement and ready-mix concrete plants and the machines that enable it. “Demand will continue to be there for three-ton class loaders. However, we see demand for five-ton class machines catching up,” says B.K.R Prasad, head of marketing & product development, Tata Hitachi Construction Machinery Company.
Wheeled loader manufacturers are unanimous, though, that it will be some time for unit demand to become fully ignited. Dimitrov Krishnan, managing director, Volvo CE India, said: “Subcontractors and hiring segments continue to be in wait-and-watch mode as hiring rates continue to remain soft. Noticeably, significant price increases arising from the transition to CEV-IV-compliant wheeled equipment and a steep rise in steel prices continue to have its impact on keeping purchase decisions at abeyance.”
Interestingly, wheeled loaders are being used in a more diverse range of quarrying applications, as Subhash Sharma, regional manager, key accounts at Volvo CE India, explains: “Quarry owners that have been traditionally using excavators for hopper feeding, handling stockpiles and loading crushed aggregates into rigid dump trucks are now migrating to wheeled loaders to do those jobs. Three-ton class loaders are now also being acquired by small-size quarry owners.
“There is also a rising use of wheeled loaders for handling manufactured sand as a sizeable number of quarry owners are setting up multiple trains for higher aggregates production. They are also setting up manufactured sand plants to attain higher levels of optimisation and profitability in their operations.”
An interesting evolving trend is using eight to 10-ton and 13-14-ton class excavators fitted with multiple attachments in bigger transport contract works requiring higher productivity. The excavators are replacing backhoe loaders that had been doing most of this work.
Due to higher initial new machine acquisition costs, customers have been preferring to extend the use of their existing equipment fleets, while also looking to minimise operating costs. However, big and middle-level road construction sector customers and commercial quarry owners are showing rising interest in machines featuring advanced technologies through which they can lower their operating costs.
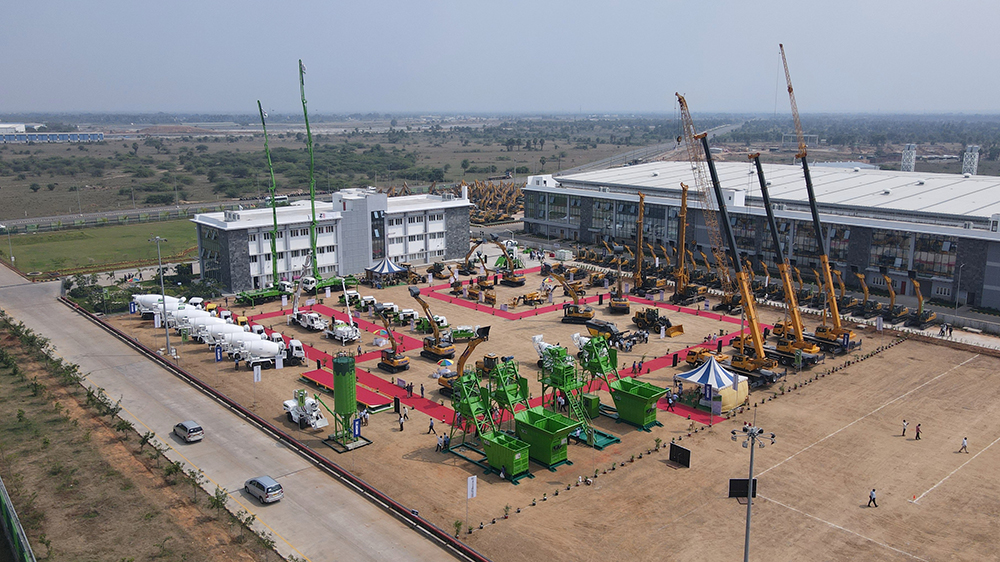
Saurabh Agarwal, director of LSC Infratech, one of the biggest quarry owners in Northern India, says “We have found the Tata Hitachi, TL 340 H prime, 3.4-ton wheeled loaders extremely beneficial, enabling us to curtail our operating costs. We have deployed the loaders at our main Haldwani operations in Uttarakhand and in our new facility at Bharatpur in Rajasthan to handle aggregates and silica sand. Inculcation of advanced hydrostatic technology in the wheeled loaders has eliminated the use of conventional transmission. It handles the same payload while maintaining the lowest deadweight of the machine. This technology also increases efficiency by minimising mechanical losses, making it the most fuel-efficient wheeled loader in its class.”
Ram Kripal Singh, director of North India-based R.K. Singh Constructions, says his company owns more than 100 Volvo FM 460 rigid dump trucks (RDTs) and 60 Scania RDTs. The firm has also recently placed orders for new Volvo FMX 550 RDTs. “The Volvo 460 rigid dump trucks have proven highly useful to us for transporting overburden materials from 50-to-70-metre-deep opencast mines at Northern Coal Fields of Coal India Limited at Dudhichua Mines Singrauli in Central India. The 22 cubic metre-bodied trucks are being used 18-20 hours daily for covering distances of between 6-10 kilometres in dumping overburden materials. Despite their very higher usage, we have found that the per cubic metre of load hauled is more with lower/per unit diesel consumption. This has enabled us to derive right levels on return of investments. Further, there is very minimal truck breakdown due to very high levels of proactive onsite parts and maintenance support. This is making our operations profitable.”
Rajesh Singh Gurjar, managing director at RGS Infratech, the dealer for Terex equipment, Chicago Pnuematic compressors, and Dynapac road construction machines in Rajasthan, says that new and existing quarry owners and road contractors have been preferring to acquire hybrid, track-mounted crushing and screening equipment due to its lower maintenance costs. He has sold three Terex Finlay Hybrid plants since October 2021.
He continues: “Quarry owners operating across all important crushing clusters in Rajasthan are also seeking newer levels of services and readily available parts support. This is because utilisation levels of plants have been going up, crushing high abrasive rocks to cater for the aggregates demand of ongoing, large-scale road construction projects going on across North India. To have higher availability of plants, crusher owners are now looking for companies who are able to provide annual maintenance contracts for a stretch of two to three years. Over this time, the OEM [original equipment manufacturer] will completely maintain and operate the plants giving the required agreed throughput.”
To attain higher throughput, operators in important crushing clusters in Rajasthan involving Kotputli, Sikar, Bharatpur, Rupbas, Bikaner, and Nangal Pahadi (prominent for meeting the aggregates demand for Delhi’s National Capital Region) are preferring 300-350tph stationary plants, rather than their traditional 250tph plant choice. Track-mounted plants offering a 200-250 tph throughput are also proving popular. The Rajasthan crushing clusters are also home to strong demand for 450-500 CFM (cubic feet per minute) pneumatic compressors for operating jack drill and track-mounted drills to drill into rock boulders to enable blasting and breaking.
Furthermore, demand for wheeled loader block handlers is expected to increase in Rajasthan from new crushing clusters including Diggi Malpura and Chitamba Mines. Demand for block handlers has been stable from existing clusters like Jaipur, Jalore, Barmer and Dev Garh in Rajasthan. Granite mine owners have been showing interest in wheeled loader block handlers due to their higher utility in pushing marble blocks compared to excavators.
To cater for the demand for higher productivity and reduced owning and operating costs, Indian equipment manufacturers have been introducing new solutions and improving the capabilities of existing machines.
Vivek Hajela, vice president & head, CEB, L&T Construction & Mining Machinery (L&T), says: “Considering the requirements of the large crushing and screening plants, we have made suitable changes in the arm, linkage and bucket designs of the L&T 9020 wheeled loader – CEV-IV. These changes enable better material retention during carrying and effective loading onto carriers. In addition, rollout forces have been increased to allow for faster loading. The horizontal reach has been improved to enable levelling of the heaped material inside Hyva body RDTs. The engine power of our L&T 9020 model has been enhanced to 140hp from 133hp to ensure extra power availability. All these changes have improved productivity by 20-25%.”
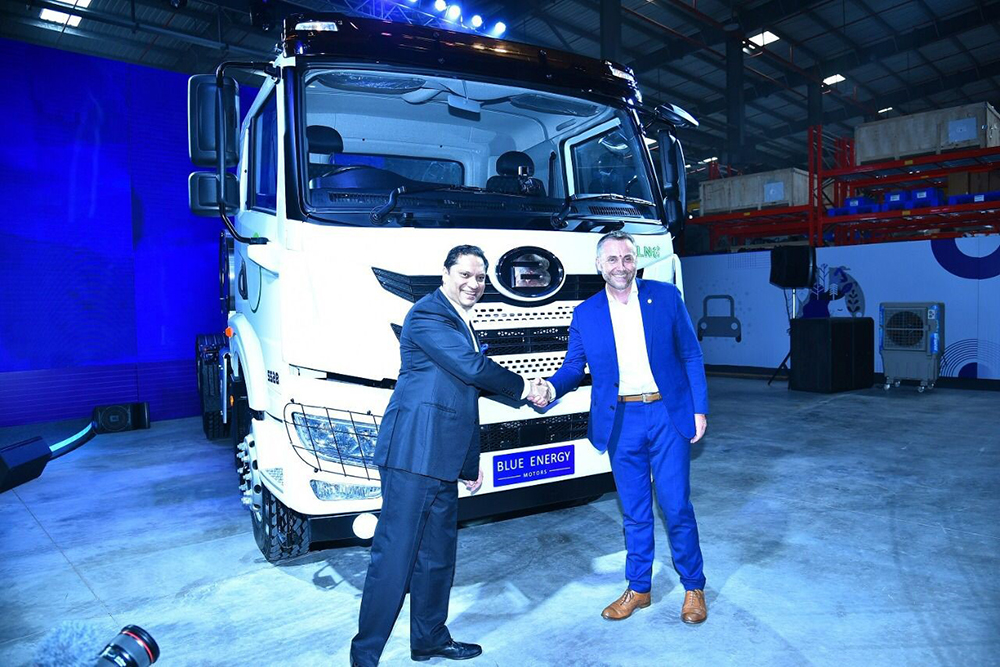
Hajela says L&T recently dispatched the first batch of 25 special variants of L&T 9020 wheeled loaders suitable for operation in harsh terrains, high altitudes and extreme weather conditions for use by the Border Roads Organisation of India (BRO), which is engaged in serving strategic national requirements.
“These sturdy machines are fitted with cold starting kits, enabling them to operate in sub-zero temperatures of up to minus 20 degrees,” he explains. “BRO will deploy them to strengthen road infrastructure in Northeast, North and Northwest India. LTCEL bagged the prestigious contract for supplying seventy L&T 9020 wheeled loaders, its single largest order, against stiff competition from domestic and multinational companies.”
To counter rising fuel and material costs to keep overall project costs down, the Indian Government has been insisting that construction equipment manufacturers develop more efficient technology solutions.
Addressing a recent gathering of representatives from top equipment manufacturers such as JCB India, Volvo CE, L&T, that was also attended by Aggregates Business International, Nitin Gadkari, India’s Union Minister of Road Transport & Highways, Government of India, said: “There is a huge scope for bringing innovative construction technologies. This will not only increase the pace of road construction, but also enable contractors to make more profits. Some of the key breakthroughs have been the newer soil stabilisation technologies in the construction of bridges and tunnels.”
Emphasising the need to use alternative fuels, he continued: “The scope of construction is immense in India given the large government roadmap. Despite adequate funding, the cost of construction needs to be minimised to make projects financially viable. This can be achieved by introducing innovative technologies, including alternative fuels. Use of alternative fuels like biofuel, methanol, and other bio-products will negate the impact of the spiralling crude oil prices.”
Gadkari suggested that stakeholders in the construction industry should focus strongly on research and development and gave the example of the initiative taken in the Northeast India construction market where diesel and methanol were mixed in a 50:50 ratio. To make alternative fuels available on a larger scale, the government is experimenting with ethanol to derive higher calorific value at par with diesel and is also working on developing bio CNG sourced from the Indian Oil refinery plant at Panipat, Haryana, North India.
“OEMs should consider developing machines in which their petrol engines can be converted to flex engines that can use biofuel, methanol, and other bio-products. This will not only check pollution in a big way but will also reduce the cost of operations and thereby minimise the overall cost of the projects,” said Gadkari.
Taking onboard the Indian government’s directive, OEMs have been developing machines running on alternate fuel hybrid technologies. This was seen in some of the machines showcased at the recent Excon exhibition in Bangalore, India’s mega construction equipment event featuring a large array of prominent manufacturers including JCB, Cummins, L&T, BKT, CDE Asia, Volvo Trucks, Tata Hitachi and Komatsu.
Blue Energy Motors recently launched India’s first liquified natural gas (LNG)-fuelled green truck at its newly inaugurated plant in Chakan, Pune, Western India, in the presence of Anirudh Bhuwalka, CEO of Blue Energy Motors; Gerrit Marx, CEO of Iveco Group; and Sylvain Blaise, president of Iveco Group’s Powertrain Business Unit.
Speaking at the event, Bhuwalka said: “With a keen focus on developing LNG as an alternate fuel, Blue Energy Motors’ heavy-duty and long-haul trucks powered by LNG are set to pioneer the green trucking revolution in India. The market entry of the LNG-fuelled trucks is starting with the introduction of the 5528 4x2 truck as the first model. Blue Energy Motors’ trucks are created and tested to meet the rigorous duty cycles of the Indian transportation sector. Through the FPT Industrial cutting-edge technology in the field of natural gas, these trucks provide best-in-class TCO with unparalleled riding comfort and safety for drivers throughout lengthy hauls.”
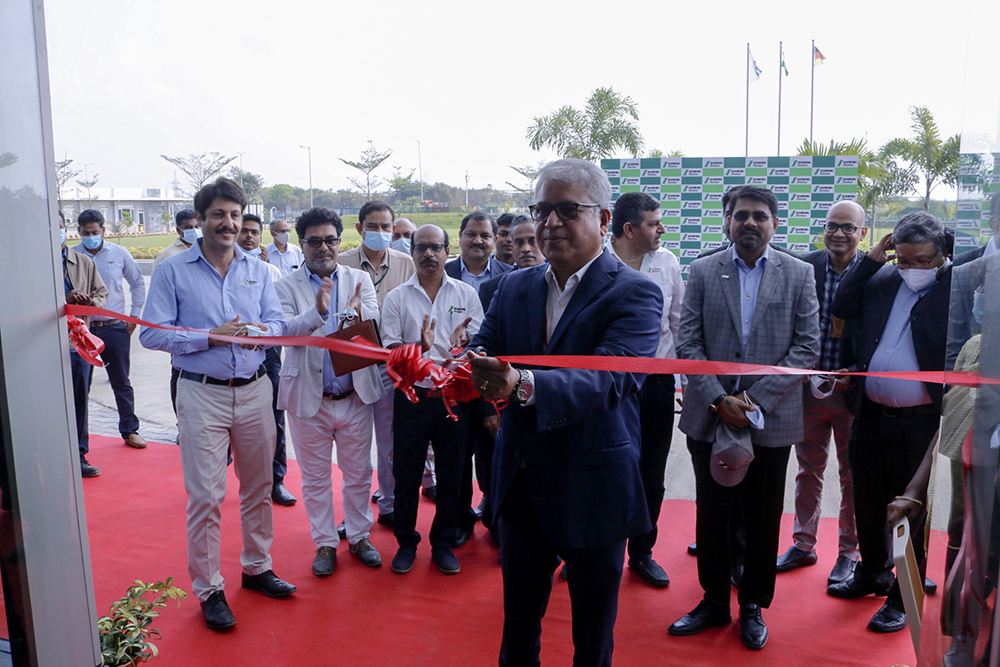
Iveco Group’s Blaise said: “India is one of the largest vehicle markets in the world and our cutting-edge technology and natural gas engines are key enablers of the ecological transformation and generating value for the transport operators.”
Bhuwalka added: “The Blue Energy Motors’ 5528 truck uses an FPT Industrial multipoint stoichio metric combustion engine to ensure best-in-class fuel consumption and lower noise than diesel engines. With 280hp power and 1000Nm torque, it is one of the most powerful natural gas trucks on the Indian market and is compatible with CNG, LNG, and bio methane. The 5528 4x2 truck has the industry’s first 1000-lt fuel tank which provides the range of up to 1400 km in a single fill. Given this long range, issues pertaining to range anxiety are well taken care of and with the upcoming LNG dispensing network, sufficient coverage across key routes in India will be available without need of frequent refilling.”
Blue Energy has installed capacity to produce 10,000 trucks per year, which can be augmented further as demand picks up. With Indian market demand prospects continuing to remain firm in the medium and long term, off-highway equipment manufacturers are going in for capacity expansion by opening new facilities. The facilities will also cater for healthy export as well as domestic unit demand.
Schwing Stetter (India) has recently commissioned a new global manufacturing hub in Cheyyar, Tamil Nadu, to cater for national and export customers. There will be a focus on localisation at the new site to lower initial costs.
V.G. Sakthikumar, the company’s managing director, says: “The new facility will be promoting XCMG products, helping Schwing Stetter (India) to expand and strengthen its business presence in India. The XCMG products score high on technology and services and deliver a high level of performance with low operating costs.
“We will use our state-of-the-art production and testing technologies to further align the new solutions to meet customer expectations in segments like road and metro railway construction, the latter catering for upcoming Indian high-speed rail projects.
“We have appointed close to 28 dealers and have put together an expert sales team for both pre- and post-machine sales of models produced at the new facility, notably mobile and crawler cranes, piling rigs and motor graders.”
Sakthikumar says sales of XCMG 20-ton excavators have been “highly encouraging” since their launch a few years ago, with XCMG excavators achieving the largest single brand sales in India in 2021, “even when the segment was depressed”.
He adds: “Based on customer requirements in both the track and stationary crushing segment, we will be introducing required solutions. Currently, we have a strong presence in niche demolition waste recycling with our Rubble Master plants. We plan to position ourselves more strongly with solutions that will enable commercial quarry owners to optimise their crushing plants and be more profitable. Our key initiative will be to provide solutions for producing manufactured sand. We will support the mineral processing plants with our wide range of high-performing wheeled loaders, as we did successfully for ready-mixed concrete plants.”
Indian off-highway machine companies are also working hard to create products and services closely attuned to customers’ needs.
According to R.B. Patel, managing director of Electro Magnetic Industries, a Gujarat-based manufacturer of vibratory screens, circular vibratory screens, vibratory conveyors, vibrating grizzly feeder, vibratory motors, demand for quality components is also growing due to crushing and screening OEMs offering ever-higher product standards to deliver higher plant availability alongside greater production volumes.
“We are working proactively with customers in our production of mobile, stationary and tracked plants. Our work is supported by our integrated manufacturing facility involving our own foundry, fabrication and performance test facilities.” Electro Magnetic Industries’ (EMI) clients include Sandvik, Metso and prominent Indian crushing and screening manufacturers like Puzzolana Machinery Fabricators, and Marshman.
An interesting novel EMI product is dump body vibrators for rigid dump trucks. The 12-volt DC vibrator mounted on the tipper trucks will discharge sticky wet and frozen materials quickly and safely. Patel said: “With the solution, tipper truck operators do not need to bang tailgates, jam brakes or pop clutches. The vibrators give a quicker and cleaner dump every time, reducing the risk of vehicle damage. The vibrators will also facilitate discharge of compacted materials at lower dumping angles to avoid possible vehicle tip-over.”
Another Gujarati company, Dynemix India, has launched concrete reclaimer solutions for aggregates and concrete slurry reuse and concrete bucket attachments.
Jignesh Patel, Dynemix India’s managing partner, says: “The concrete reclaimer is meant for the ready-mixed concrete industry, where there is rising requirements of contractors for higher levels of plant optimisation. It arrests the concrete from spillage while being transferred from transit mixers.”
With Indian national and state governments continuing their commitment to develop India’s infrastructure for the long term, building materials and building materials production machinery demand is expected to gain further momentum in Q4 2022 into Q1 2023. Several major infrastructure projects are approaching completion with large new projects set to begin before India’s next general election in spring 2024. However, some industry analysts anticipate that product and machinery demand could dip in 2025. AB