Many crushing plant operators across North India are back in action, having scaled back their output during India’s first wave of the COVID-19 pandemic. Renewed large-scale roadbuilding and railway infrastructure work overseen by the Ministry of Road Transport and Highways (MoRTH) is fuelling operators’ investment in increased production capacity and high-tech plant capability.
Speaking at a recent webinar attended by Aggregates Business International, Nitin Gadkari, India’s Minister for Road Transport & Highways and the Minister of Micro, Small, and Medium Enterprises (MSMEs), said: “India has managed to achieve three world records recently. Firstly, we could manage to achieve a record by constructing 37km of road per day during 2020-21. Secondly, construction of a 2.5km four-lane concrete road was achieved in a matter of 24 hours. Our ministry also achieved a record by constructing a 26 km one-lane road in 24 hours flat.
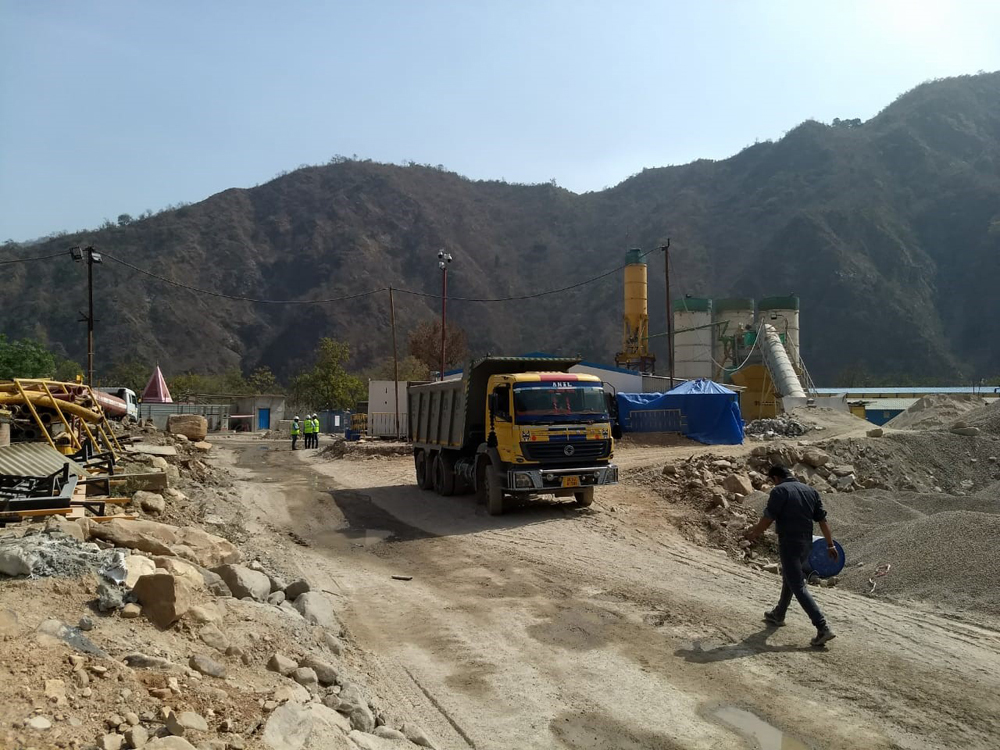
“The Ministry has constructed 13,327km of National Highways up to March 2021 as compared to 10,237km in March 2020. The award figure is 10,965km during this period as compared to 8,948km in the previous year. We will look to retain this momentum.”
MoRTH has planned to construct about 60,000kms of national highway in the next five years – with many linked projects in Northern India states. GHV India has been awarded the contract to build the Sohna-Vadodara section of the 1350km Delhi-Mumbai Expressway. Meanwhile, PNC Infratech has been awarded the contract to build four-lane roads on the Hapur Road section of the Delhi-Meerut Expressway. Work on the project must be completed in two years. Another major road project in North India is the 600km Delhi-Amritsar-Katra Expressway. KCC Buildcon and CDS Infra Projects have emerged as bidders for construction of the first three packages of the project.
Indian Railways is laying the 125km Rishikesh-Karnaprayag railway line 825 metres above sea level in the North India state of Uttarakhand. The build includes 12 stations, 17 tunnels and 35 bridges. The project of national importance, also known as Chardham, will connect North India’s four major centres of pilgrimage: Gangotri, Yamunotri, Kedarnath, and Badrinath.
Buoyed by the ongoing and upcoming big ticket projects’ huge aggregates requirements, North India’s biggest quarry and crushing plant owner, LSC Infratech, has been one of the heaviest investors in new crushing technologies. The company is commissioning a new state-of-the-art crushing, screening, and silica sand washing plant in the Karauli district of Rajasthan. It will be LSC Infratech’s eleventh major facility in North India. The new mega-production unit includes a stationary jaw and cone crushing plant from Indian crushing and screening equipment manufacturing major Propel Industries, and a silica sand washing plant from Germany-based Hazemag allimineral, and Australian firm Mineral Technologies. The plant line-up will be producing 14-22-44mm aggregates, 0-5mm manufactured sand, and varied graded silica sand.
Shiv Kumar Agarwal, chairman & managing director, LSC Infratech, said: “The mineral processing facility will have maximum levels of integration between the crushing and silica sand washing systems. The aim was also to have large-scale, reduced cost of production through maximum availability of the systems. Due to this, based on our past experiences, we went for Propel’s QM250, 250tph cone crusher, having very low cost of production. The very high grade of manganese steel inside the concave mantle of the crusher ensures there is much less wear and tear. Furthermore, Propel’s AVJ 912, 900mmx1200mm jaw crusher can accommodate large boulder sizes. Besides Propel’s 2060 200tph, three-deck vibrating screens will be able to work with good levels of flexibility. On top is Propel’s superior product support services.”
One of the major signs of on-site plant integration is a network of radial stacker conveyors. Throughput from the crushing plant is directly transported by the conveyors to the site’s washing systems, doing away with the need for rigid dump trucks during this stage of the production process. However, LSC’s five newly acquired Tata India-made 38-ton rigid dump trucks will be used to transport raw materials four kilometres to the new high-performing crushing plant, and to transport final crushed aggregate products to customer sites.
Agarwal said: “One of the major considerations of setting up this facility has been to cater for large-scale aggregates demand from road, general infrastructure and, importantly, ongoing railway projects in North India. The sand manufacturing unit has been set up to meet rising demand of silica sand from glass manufacturers like Saint Gobain, Asahi Glass and others.” LSC’s new Karauli district mine is feeding the new crushing plant with very good quality soft rock, metamorphic rocks, and silica dioxide SI02, required for making silica sand.
He continued: “We have carried out extensive research on the kind of silica sand beneficiation plant, we should go for our new facility to have less cost of production. The prime consideration to go for Hazemag allmineral sand washing plant was due to its unique ‘up-current classifier technology’ featuring higher levels of water pressure than competition plant offerings. This up-current classifier technology comes with an ability to cut the right size of silica sand through up-current water stream, thus eliminating traditional sieve-based separations.”
To have higher productivity while reducing operating costs, LSC has acquired two new three-ton Tata Hitachi hydrostatic wheeled loaders. The company has also bought 26-ton LiuGong excavators. The excavators will be used at the mines for loading the raw materials into the rigid dump trucks.
Agarwal said: “Higher fuel efficiency was one of the considerations in going for the LiuGong excavators. However, the other most important reason to go for 26-ton units was to have balanced productivity as required in the present COVID-19 scenario, with its fluctuating demand for aggregates.
“A 26-ton excavator can be both rationally used during peak and non-peak times. Through this usage we will be able to hedge our loan instalments comfortably. This is without shelling out a higher amount, as would have been required for a higher tonnage class equipment, even when it was less in use.”
Crushing plant owners in India have been generally preferring to have 20-ton class excavators. In some cases, they have been going for long-track excavators to work on larger stockpiles.
S.S & Co is another major North India-based quarrying company with a pan-India presence working on increasing its production capacity. The firm is setting up one new three-stage jaw-cone plant and another two-stage jaw-cone plant in Mouganj, located between Allahabad [officially known as Prayagraj] and Varanasi in Uttar Pradesh state. The new Metso plants are scheduled to begin production from next month and will mainly cater to upcoming state road and railway infrastructure projects.
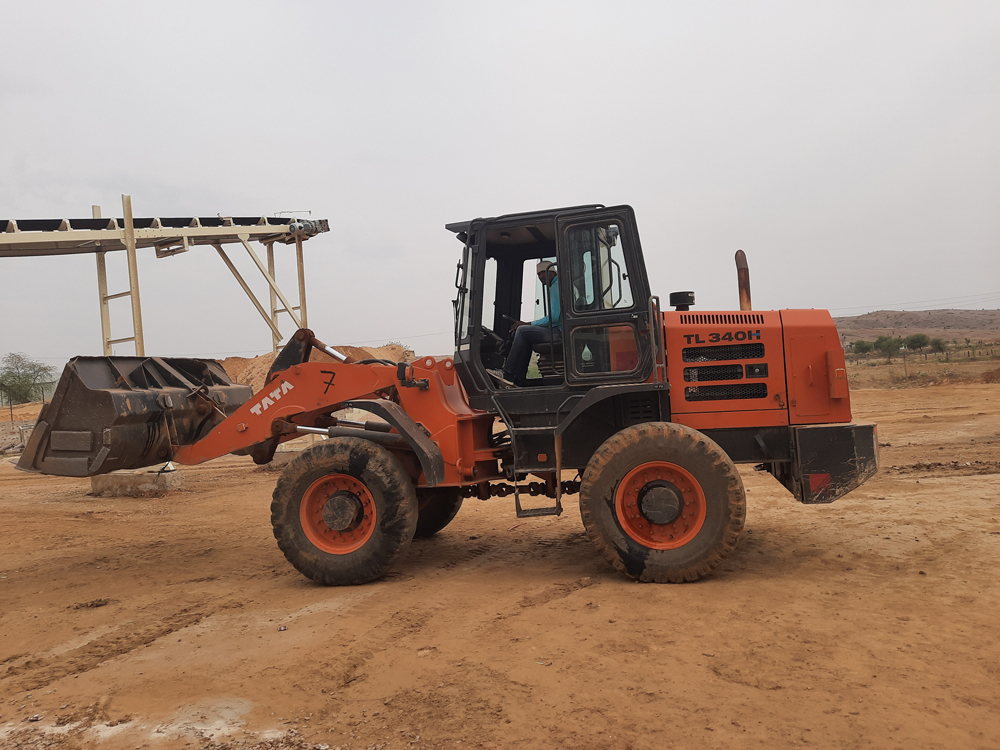
Manjeet Chawla, director of S.S & Co, said: “We will be selling the aggregates from the new facility to road contractors working on big stretches, so productivity requirements will be quite high. For this reason, we have gone for Metso plants. We have relied on Metso plants since we have been in business. This is due to the very high levels of reliability and superior product support.” For the Mouganj facility, S.S & Co will be buying six excavators, likely 22-38-ton class models from Kobelco. The company already has a mammoth fleet of 150 20-30 and 48-ton class Kobelco excavators.
S.S & Co operates 15 quarries in Bharatpur, Rajasthan. The quarries, leased from the Rajasthan government, all use Metso plants. Having recently set up two new two-stage jaw-cone plants within its Bharatpur quarry portfolio, S.S & Co is in the process of installing a further two-stage jaw-cone plant. The new Metso crushing plants are likely to be commissioned after the 2021 monsoon season.
Chawla said: “The plants will be producing up to 40mm aggregates which will be sold to road contractors with projects in Rajasthan and Uttarakhand in North India, and Delhi and its capital region.” S.S & Co will also be setting up an additional four two-stage plants in the East Indian state of Odisha later this year.
Chawla added: “Rocks from Haryana and Rajasthan are typically quartz with high levels of abrasive character. These require jaw and cone units with superior levels of metallurgy, with minimum wear and tear, for which we believe, Metso is the ideal choice.”
Rocks originating from Uttarakhand and other parts of North India, like the bordering areas of Jammu and Kashmir, Pathankot, Uttarakhand and bordering states of Uttar Pradesh are river boulders.
S.S & Co uses Atlas Copco and Epiroc rock drills during its aggregates production. The company also uses one two-stage Sandvik jaw-cone plant in Bhiwani, Haryana. S.S & Co also has crushing plants in the Central India state of Madhya Pradesh. The firm also employs a limestone mining contractor for cement plant customers.
Operating a different business model is Abhishek Malakumar, director of Malakumar Engineering. The company owns its own mine in the Charki Dadri region of Haryana and at Satna in Madhya Pradesh. It has one Terex three-stage jaw-cone-screen plant at Charki Dadri producing close to 90,000 tons of aggregates per month.
Malakumar said: “We crush 10% of the output from our mines and sell it to various contractors and end users. Remaining big boulder chunks obtained through drilling, deep-hole blasting and, finally, excavation are sold to various end users. We have refrained from setting up crushing plants. This is due to very high levels of competition in the business, due to large-scale concentration of crushing plants in the region.” There are close to 300 big and small crushing units in Charki Dadri, running plants between 100-300tph capacities.
“Since we only sell boulders to crushing plant owners, for enhancing productivity in our mines, we have been making sizeable investments for higher capacity excavators and advanced rigid dump trucks.” The company has 50 EC-350 35-ton Volvo excavators and 13 35-ton Kobelco 380 excavators.”
Malakumar said that he and his team’s experience of working with Volvo units has been great due to the machines’ strong break-out forces. “The excavators have strong undercarriage, enabling it to work on very rough and undulated terrain. Through Caretrack, we have been able to get good services from Volvo,” he explained.
Malakumar Engineering recently bought 20 Bharat Benz 8x4 rigid dump trucks with rock bodies. The company also has a fleet of 50 6x4 Man rigid dump trucks.
Demand for higher capacity rigid dump trucks has increased among crushing plant owners and road and rail project contractors working on aggregates-thirsty long road construction stretches. The other demand driver has been a requirement to travel over longer distances to deliver the final crushed aggregates to customers.
Pranav Shroff, deputy general manager of marketing at Construck Tata Motors, said: “28-ton 6x4 and 35-ton 8x4 units continue to remain the major demand segment of the rigid dump trucks from quarry owners in North India and other parts of India. However, we have been recently witnessing demand shifting to higher capacities [48-ton 10x2 and 10x4 RDTs] from major crushing clusters in North India. This is notably from operators in Kabrai, Jhansi and Kotputhli in Uttar Pradesh.” Tata Motors has recently launched the BS-VI emissions-compliant 10x4 Signa 48.25 TK rigid dump truck.

Arun Raizada, senior vice president of Himgiri Automobiles, the Ashok Leyland trucks dealer for Delhi and National Capital Region and parts of Uttar Pradesh, said: “There has been a spurt in uptake for Ashok Leyland’s newly launched Avtr range of long-haul 10x4 five-axle rigid dump trucks. This is due to its higher productivity and faster cycle times, delivered by 250hp fuel-efficient Ashok Leyland engines. We have been selling a fair number of these heavier units to crusher plant owners and contractors involved in road projects. However, with the onset of the second wave of COVID-19, there has been some decline in business enquiries and off-take of the vehicles.”
While quarry owners in North India have been making big capital investment to acquire newer technologies for higher productivity, purchases create higher expectations around product services.
Manoj Kotru, director of Alpha Teknisk, dealer for Volvo and SDLG products in Haryana, Uttarakhand, Uttar Pradesh, Delhi and the National Capital Region, said: “Business has been growing. Demand is up for advanced solutions. Notwithstanding, customers are insisting on big discounts and for extended warranties on excavator booms, tracks, and other vital components. There is now also bigger scale demand for free parts availability. These are new challenges. Nonetheless, in most cases we work closely with customers and try to work out product support packages which are commercially conducive to both parties.”