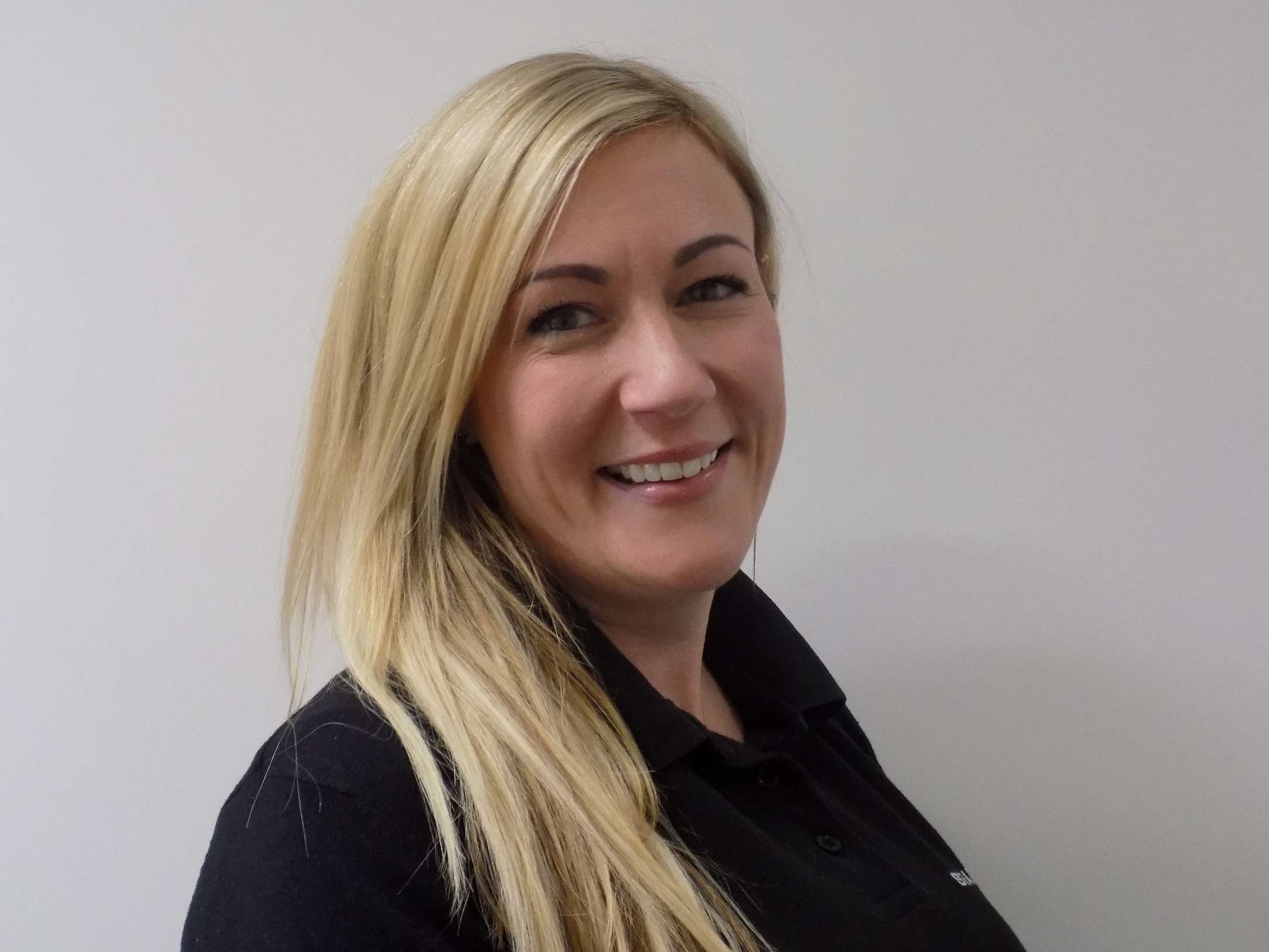
In the aggregates industry there’s been a lot of talk given to sustainability and carbon reduction over the years, but it’s more often than not been a welcome added benefit coming from reducing costs rather than the goal itself. But times are changing. With COP26 making headline news across the world, climate change is being taken seriously. In line with the UK’s landmark Net Zero Strategy, from April 2022 new legislation requires Britain’s largest businesses to disclose climate-related financial information. The aim is to get businesses to consider the risks and opportunities they face as a result of climate change and encourage them to set out their emission reduction plans and sustainability credentials. But companies of all sizes and across all sectors are now examining their own strategies to achieve net zero by the earliest date possible.
For many aggregates-based businesses this will require significant changes in the coming years, from energy sources and usage, through to production processes and equipment, and beyond. Yet not everything needs to be a giant leap to get where we need to be.
If anyone has ever shown even a passing interest in cycling, they may have heard the phrase ‘marginal gains’.
Developed by performance director of British Cycling from 2003, Dave Brailsford came up with the theory that small yet significant improvements can lead to substantial results. Up until that point, the team had just one gold medal to show in its 76-year history. Under Dave’s guiding hand and adoption of the ‘marginal gains’ theory, the British Olympic cycling team won seven out of 10 gold track cycling medals at the 2008 Olympics.
The rest, as they say, is history.
The marginal gains idea is not only applicable to sport but has made an impression in industry. At Brammer Buck & Hickman, we have been looking at how marginal gains can be applied across our customers’ businesses to improve productivity and reduce costs.
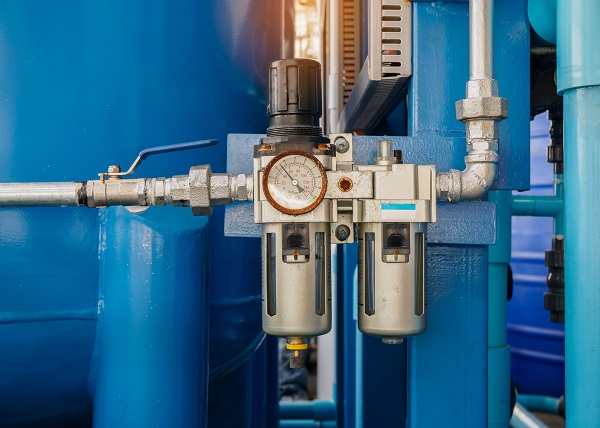
We have applied this same theory to issues of sustainability, and one area where it has had the most impact is in compressed air usage.
Compressed air is used extensively throughout aggregate processes, from controlling valves and actuators in asphalt plants through to cleaning silos in concrete production sites. But generating compressed air is energy intensive and, as a result, expensive.
Up to 73% of the total cost of ownership of compressed air installations can be attributed to the cost of energy consumed by the compressor and ancillary equipment over a ten-year period. What’s more, 30% of compressed air is wasted or misused. Is it possible to reduce this energy usage without negatively affecting a machine’s performance and without significant expenditure? The answer is a resounding yes!
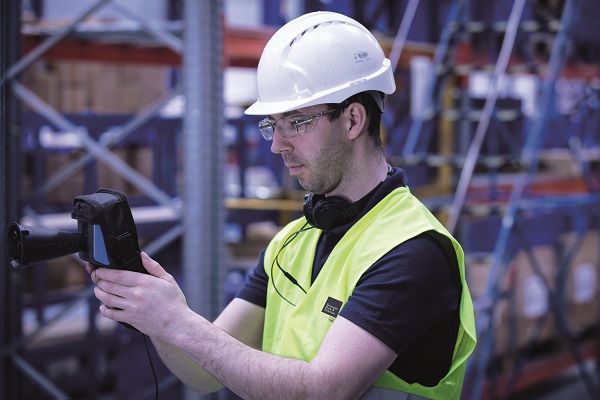
Here are our top five tips for reducing energy consumption in the aggregates industry when it comes to compressed air:
Tip 1: Choose the correct components
Switching to high flow couplings could increase the productivity of air tools by some 50% and reduce energy consumption by up to 30%. In more than half of all applications, the pneumatic drive is too large for the intended purpose. Simply downsizing the cylinder or using single-acting cylinders are often all that is required of a pneumatic system and can help reduce air consumption.
Also, look at the connectors you are using. Every tube run, fitting and filter causes a pressure drop. Every 1 bar pressure drop means an increase of 7% to the cost of compressed air generation. A 90⁰ elbow can be the equivalent of a 1.6-metre pipe length.
Check to see if you can change elbows to straight connectors and Tee’s to Y pieces.
Tip 2: Hose and tubing sizes
Opting for a tubing size with a smaller diameter for valves and cylinders can reduce air consumption while choosing a larger diameter hose for air tools can save money. Using tubing with low drag co-efficiency can increase air flow and reduce pressure drops to optimise compressed air systems to achieve yearly savings of around £15,000.
Tip 3: Reduce the pressure
Incorporating pressure regulators at point of use can very quickly pay dividends. Reducing the pressure by just 1 bar can see up to a 10% reduction in energy usage. Installing a regulator means the pressure may be reduced without having a negative effect on the operation of the machinery. As well as wasting compressed air, operating at too high a pressure can increase wear on the components leading to burnout and the associated maintenance and replacement costs.
Tip 4: Switch off and save
Pneumatic equipment left idling can consume between 20-70% of its full load power. Apply responsible usage principles to pneumatic components such as: installing manual shut off valves and switching off when machinery is not in use; implementing time-operated solenoid valves, which allow the operation of pneumatic components only if a subsequent piece of equipment is in use; or installing sensor-operated interlocks which detect the need for compressed air equipment to operate can isolate or apply air as appropriate.
Tip 5: Stop leaks
In a pneumatic system, leakages can account for between 5-10% of the air supplied, although some systems record a loss of 40-50% of the air input. Dust is a fact of life on aggregates sites and has a direct impact on compressed air systems as it gets into the system, causing excess seal wear and premature failure, not just in the valve but on every component, all the way round the pneumatic circuit connected to the valve. By fitting a £2 Silencer in the exhaust of every valve open to the atmosphere, you can protect against dirt ingress and increase mean time between failure.
Also, use a tube cutter to ensure a good seal, rather than scissors, box cutters and the likes.
Consider installing a flow meter, which is the most effective way of reducing leaks and energy consumption, by monitoring leaks as part of a facility-wide maintenance programme. You might also want to consider investing in a Compressed Air Leak Audit to fully identify leaks so you can take remedial action.
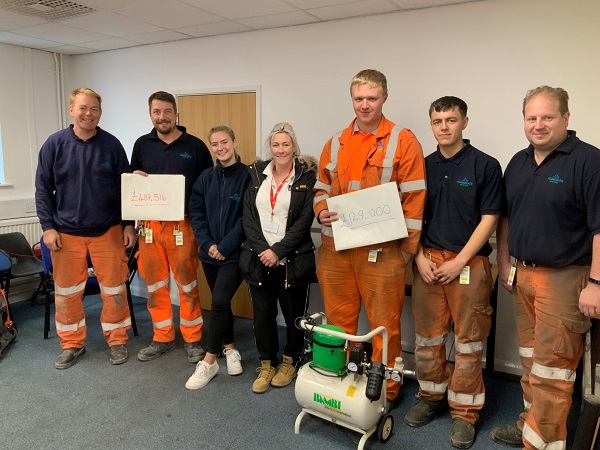
These small adjustments are easy to make without the need for any costly equipment or intervention from third parties. In fact, they can be done by some of the most junior employees, including Apprentices, ensuring everyone can participate in the move to more sustainable processes.
We regularly run workshops on compressed air under the name of ‘REHAB’, which stands for:
- Reduce Energy
- Education
- Health & Safety
- Autonomous Maintenance
- Best Practise
These workshops are designed to empower customers to make changes for themselves, and the response is always one of astonishment when we can prove together, with hands-on training, how these minor adjustments can generate significant results.
With climate change an inescapable fact and companies moving sustainability up the agenda, everyone has a part to play, and even small changes can have a big impact when made universally.
REHAB training workshops are available exclusively from Brammer Buck & Hickman. For more information, contact your local branch or download the REHAB brochure from https://uk.rubix.com/catalogue-library?src=catalogues