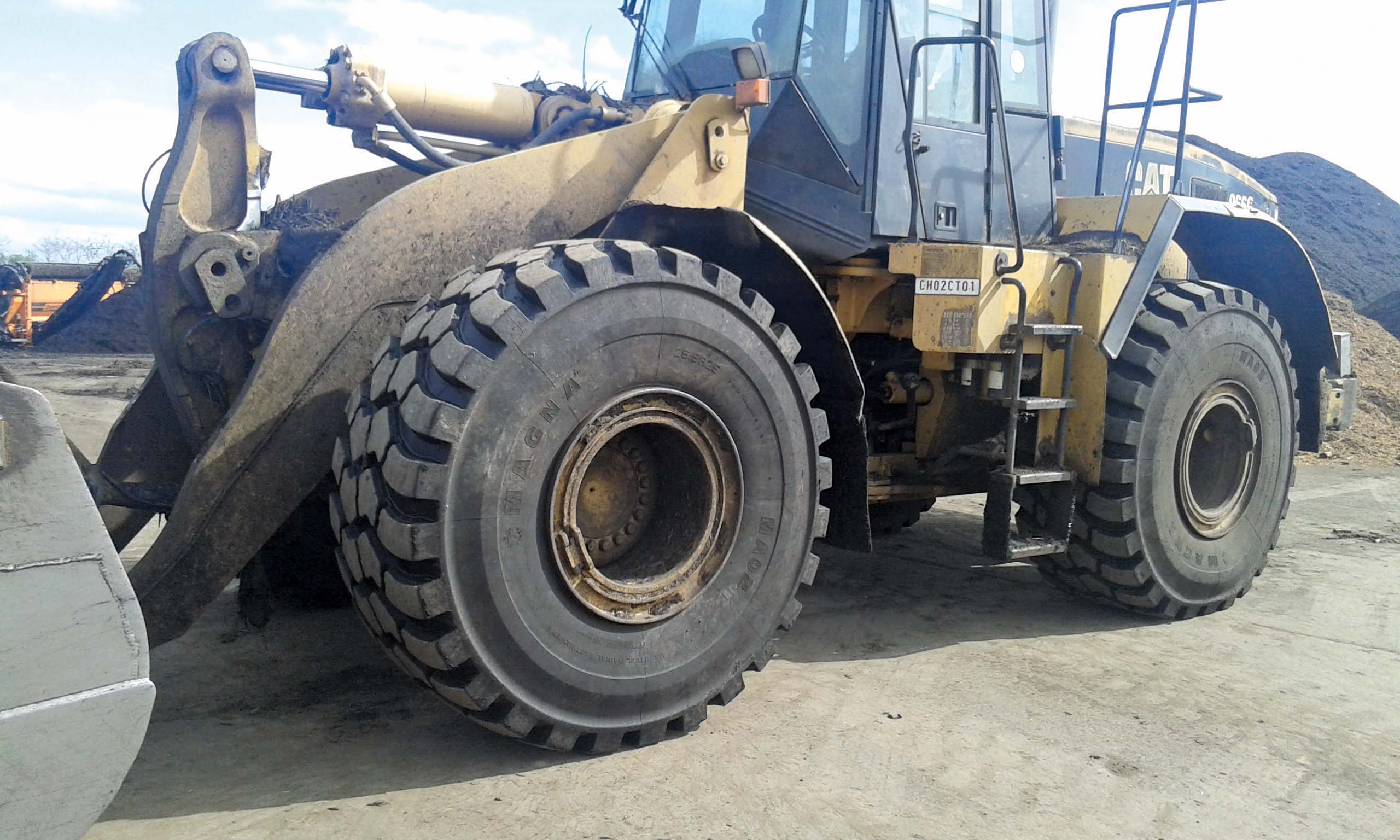
Despite economic slowdowns, demand remains high for companies that can demonstrate competitiveness in quality, price and delivery. This maxim applies as much to the rough and tough industries such as minerals, aggregates, fossil fuels, demolition, recycling and forestry as it does to the service sector.
Where load and haul is a central component of an operation, optimising plant availability is the key to success and this success depends on skilled staff and a rigorous maintenance schedule with particular attention to the tyres.
A good plant manager will make certain that both staff and machines are well protected. Without a full set of sound tyres, as without a skilled operator, a loader or a truck is just an expensive lump of metal.
No two sites are the same, so it is essential to invest in tyres that promise optimum serviceability. And when the cost of a tyre is in the thousands this makes sense.
Big name manufacturers, including
The considerations that apply to automotive tyres are amplified many times when it comes to selecting Earthmover Tyres as each condition or combination of conditions must be matched by the appropriate construction and tread.
For example, a few questions that have to be answered: Is the site wet, clayey or icy? Is the running surface abrasive powder, shingle or flin? How long and steep are the haul roads? What weights/ tonnages are being shifted and is the work in extreme temperatures?
“Then there is tyre wear and tear, and while manufacturers do their best to make their tyres abrasion-resistant, the very flexibility that makes a tyre what it is, is precisely what makes it vulnerable to sidewall piercing,” says German company
“If a tyre wall is damaged quick action may save the day, but however good the repair the tyre will have lost some of its original integrity. While tyre dealers prefer to sell tyres, their technical support will accept that there are instances where TPCs are essential.
“Nowadays, the consideration is no longer whether or not to fit tyre chains, as to whose brand and which type.”
There are around ten tyre chain manufacturers worldwide, and following a series of acquisitions and consolidations, Europe boasts few tyre chain manufacturers, including Erlau and Austrian company
However, before fitting TPCs, the correct tyres are selected from companies such as Magna which says that its Magna MA02 E3+/L3+ for wheeled loaders and articulated dump trucks (ADTs) offers excellent performance, with the MA02 being its flagship product.
“This E3+/L3+ rated tyre, available in tyre sizes 23.5R25, 26.5R25 and 29.5R25, is designed and constructed with the latest Magna radial tyre technology, and the MA02 is OEM approved for
“Magna MA02 is already in use in more than 100 countries around the world, to the full satisfaction of end users. Recently, Magna Tyres received a performance report from one of the largest softwood sawmills in Latvia, where the 23.5R25 MA02 is currently running over 5,700 machine hours on a
“End users from all over the world choose Magna MA02 for various applications. Recently, Magna Tyres received very positive feedback from a steel company in South Korea, where a
The company, which currently has ten sales offices worldwide, is headquartered in Waalwijk, the Netherlands, where it has decades of experience in manufacturing and trading premium quality rubber compounds.
“From this experience, Magna Tyres Group started developing high quality tyres for mining, construction, port handling and industrial purposes, especially designed for challenging applications. Recently, the company included truck tyres for on/off road use in its programme and is further developing a new and special OTR winter tread pattern for various applications.”
With continuing expansion of its sales and distribution network, Magna plans to invest in a new 24,000m² warehouse at Waalwijk to fulfil the increasing needs of European partners in Germany, France and the Netherlands and to provide the best service and availability for OEMs including Terex, Liebherr and
Meanwhile,
“This top-of-the-range tyre is an evolution of its predecessor and is based on the Earthmax SR 40 technology. It has been introduced to the market to offer the end user even more power and performance. The new tread features reinforced connecting elements for major lug stiffness resulting in more stability,” says BKT.
“The geometrical lug pattern has been designed to enhance the traction capacity, an essential feature for articulated dumpers operating on toughest terrains under demanding conditions.
“The all-steel Earthmax SR 41 is available in the sizes 29.5R25 and 26.5R25, and these have extra deep tread (classified E4 or 50% more compared to standard) which turns into a longer tyre life cycle ensuring a large number of working hours. Besides, the new model has been developed with a major space between the lugs to significantly reduce the risk of stones or other foreign matters getting stuck in the tyre.”
Goodyear has developed the RL-4D tyre range in response to customer demand for a harsh floor tyre in underground mining. A hybrid mix of the GP4-D and the company’s RL5K tyre, the RL-4D is suitable for ADTs and wheeled loaders. Initially the tyre has been launched in an 875/65R29 size, but the company could develop additional sizes if there is demand.
It has also upgraded its RM-4A+ rigid truck tyre, with the introduction of the RM4B+. The tyre has been developed to combat heat build-up in long- haul road applications. This prevents premature wear and results in lower lifetime running costs for the mine or quarry.
Trelleborg Wheel Systems is also planning the global roll-out of its Brawler range of large OTR solid tyres to complement its existing range of premium tyres for materials handling applications.
“Brawler is particularly suited to the waste and recycling industries. Many customers in these industries are making the switch from either pneumatics or foam-filled pneumatics to solid tyres on large applications. Sites often operate 24/7 and require tyres that last longer, need little maintenance and deliver the best total cost of ownership over their whole life,” says Roberto Zampieri, construction business development manager Europe for Trelleborg Wheel Systems, Industrial Tyres.
“The Brawler Solidflex range was developed to maximise user comfort without compromising life or performance. It uses a patented eliptical hole pattern in the side wall, allowing for much greater deflection over broken terrain; vital for applications where drivers are working on rough ground.”
And it is in such conditions that TPCs are put into use, with Erlau saying: “No matter how well made and maintained, tyres can suffer from unacceptably heavy abrasion to the extent that you can almost see the tyres shrink as, day after day, the tread (and your investment) turns into dust. Quartz, silica, dolomite, basalt, iron ore and diamondiferous deposits are just some of the causes of tyre abrasion.
“In these instances, a quality abrasion resistant chain is ideal for creating a barrier between your tyres and the ground. The density of the mesh required will depend on the exact nature of the work site.”
The company offers a wide selection of solutions to suit the conditions such as its open ring link chain Garant series where the tyre tread cannot provide sufficient displacement to ensure adequate grip; its Terraplus with studded links for extra bite where additional grip is required; the lightweight, energy-saving X19 Fels Toro, a chain that resists abrasion so effectively that Erlau claims a 30% longer service life.
While commercial confidentiality makes it hard to get hold of reliable figures, Erlau says an independent study from a European quarry, although a little dated, illustrates the benefits of TPCs.
A Caterpillar 988B loader running on 36/65-33 DTs in a German limestone quarry was getting through a set of tyres every 1,200 hours at a cost to the company of US$7,615 per set ($31.35/hour).
The quarry invested $56,200 in a set of Erlau Fels Royal X16 TPCs extending tyre life to 12,000 hours and reducing tyre costs to $3.13 per hour.
“Factoring in a conservative chain life of 10,000 hours ($5.62 per hour), the total hourly cost dropped to $8.75, a saving of $22.60 (72%). Productivity also showed significant improvements. Load-out went up by 16% from 550tonnes/hour to 630tonnes/hour and downtime dropped from 160 hours/year for tyre repairs to 36 hours/year for chain servicing. Loader availability shot up 124 hours, up 78%,” says Erlau.
“Following installation of the TPCs, the 988B’s annual output grew from 1,012,000 tonnes to 1,253,032 tonnes, an increase of just under 24%.”
Indeed, Pewag has also produced figures, which it says shows the cost benefits of fitting TPCs. The company, which some years ago launched its strongest TPC, the Tycoon, has in the last few years focused heavily on safety and user friendliness.
“Pewag invented a new system for the repair of connecting pieces, which are the main source of working accidents related to tyre protection chain handling. The task for the Pewag R&D team was clear: invent a new system for repair and connecting pieces, which offers similar or longer lifetime and which is connected with maximised safety and user friendliness.”
After two years of intense tests in the UK and South Africa the company finally unveiled its new connecting repair ring and pin lock NT (no tool), and last year started to launch the new spare parts line step by step.
“The hammering of the pin for both parts is completely saved and for the handling of the connecting repair ring only a special key is needed. For the pin lock there is no tool needed as the pin is just pressed in by hand and keeps the position by a sophisticated spring device. For demounting of the parts only an Allen key for the connecting repair ring is needed and a screwdriver for the pin lock,” says Pewag, which sells 2,200 TPCs globally each year.
Some cost-efficiency figures released by the company are based on tyres costing €15,000 each. It says that without chains, a Caterpillar 992 D with a tyre dimension of 45/65-45 working at a gold mine in Peru would have a tyre life of 3,500 hours, meaning a cost per hour of €4.29. With chains (chain costs are included in the calculation) the tyre life would be 12,000 hours and would equate to a total cost per hour of €2.54 with a return on investment at just over 5,100 hours. Over 12,000 hours, the cost without chains is €51,428.57 while with chains it is €30,500, a saving per chain life of €20,928.57.
The company has also carried out a test to demonstrate increased productivity using TPCs with partner
“The idea about testing Pewag TPC at a limestone quarry came up to prove to the management of the quarry division of Strabag, Mineral, that TPC not only drastically reduces tyre costs but also increases the productivity,” says Pewag.
“The final result of the test was that TPC decreased the wear of the tyre, provided more grip, increased the comfort for the operators and also increased the productivity for loading the dump trucks by 12.27%. Mineral also mentioned that diesel consumption rose by 10.39% (about 2.3litres/hour) and the investment costs for the TPC.
“For the operators TPC enabled them to increase the number of loading cycles, stabilise the machine and let them forget about sharp, big rocks which can cut tyres.”
Cemex UK to adopt ContiPressureCheck TPMS
With a fleet of over 300 trucks often operating in arduous quarry and site conditions that make tyres more prone to punctures and damage,
Daily driver checks and workshop inspections are part of the company’s tyre management regime, but even with such a rigorous process in place in-service failures were often difficult to detect before a small problem became a large one.
Working closely with Continental, Cemex fitted six trial units of the ContiPressureCheck tyre pressure monitoring system (TPMS) on a variety of vehicles.
The direct measurement system, mounted inside each tyre and monitored on a screen inside the truck’s cab, has integrated sensors, a data processor and communication system that immediately detects any changes in air pressure or temperature and sends this data to the in-cab display enabling the driver to take immediate action to deal with the problem.
Positive results came early in the trials, with ContiPressureCheck picking up a leaking valve on a drive axle when the system was installed on the truck and a puncture on a tank trailer being detected before any structural failure occurred.
“These two events alone proved that automatic tyre pressure monitoring is the way to go with its potential to improve safety, cost and downtime,” says Carl Milton, Cemex regional logistics manager.
Cemex and Continental are also utilising the ContiPressureCheck system to study the length of time over which normal pressure degradation takes place in tyres. Continental believes this information could be extremely beneficial to fleets as it would enable pressure maintenance schedules to be optimised and could lead to potential savings in service costs.
The company reports good feedback from drivers, and it is already planning a phased introduction across its entire fleet with priority going to those areas of its operations identified as having high call-outs, downtime and puncture issues.