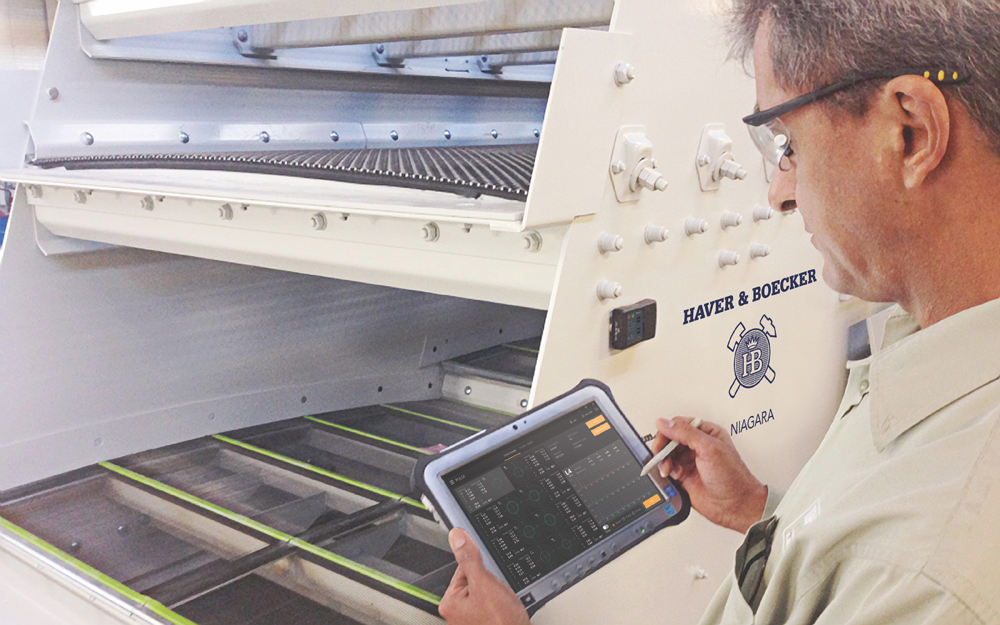
Wilm Schulz, H&B Niagara’s parts and service manager, said: “Our Pulse Vibration Analysis Service offers more than just technology. We want to help our customers by serving as an extension of their maintenance teams, bringing the knowledge of an OEM to help support their operation.”
Pulse Vibration Analysis Service uses the company’s industry-leading Pulse Vibration Analysis software to examine the health of a vibrating screen to ensure optimum screening performance and equipment reliability.
Pulse detects irregularities that could translate into diminished performance, decreased efficiency, increased operating costs and imminent breakdown. This gives producers advanced notice so that their operation can plan preventative maintenance programmes to avoid premature wear, downtime and additional expense.
The service programme includes a complete vibrating screen inspection by an H&B Niagara-certified service technician. Following the inspection, customers receive a Pulse Diagnostic Report, which provides an analysis of their vibrating screen and detailed recommendations to prevent downtime.
All Pulse Diagnostic Reports are stored in an online asset management system, giving customers access to a complete record of their vibrating screens’ service and performance histories. This information allows customers to maximise uptime and productivity, and as a result, increase profitability.