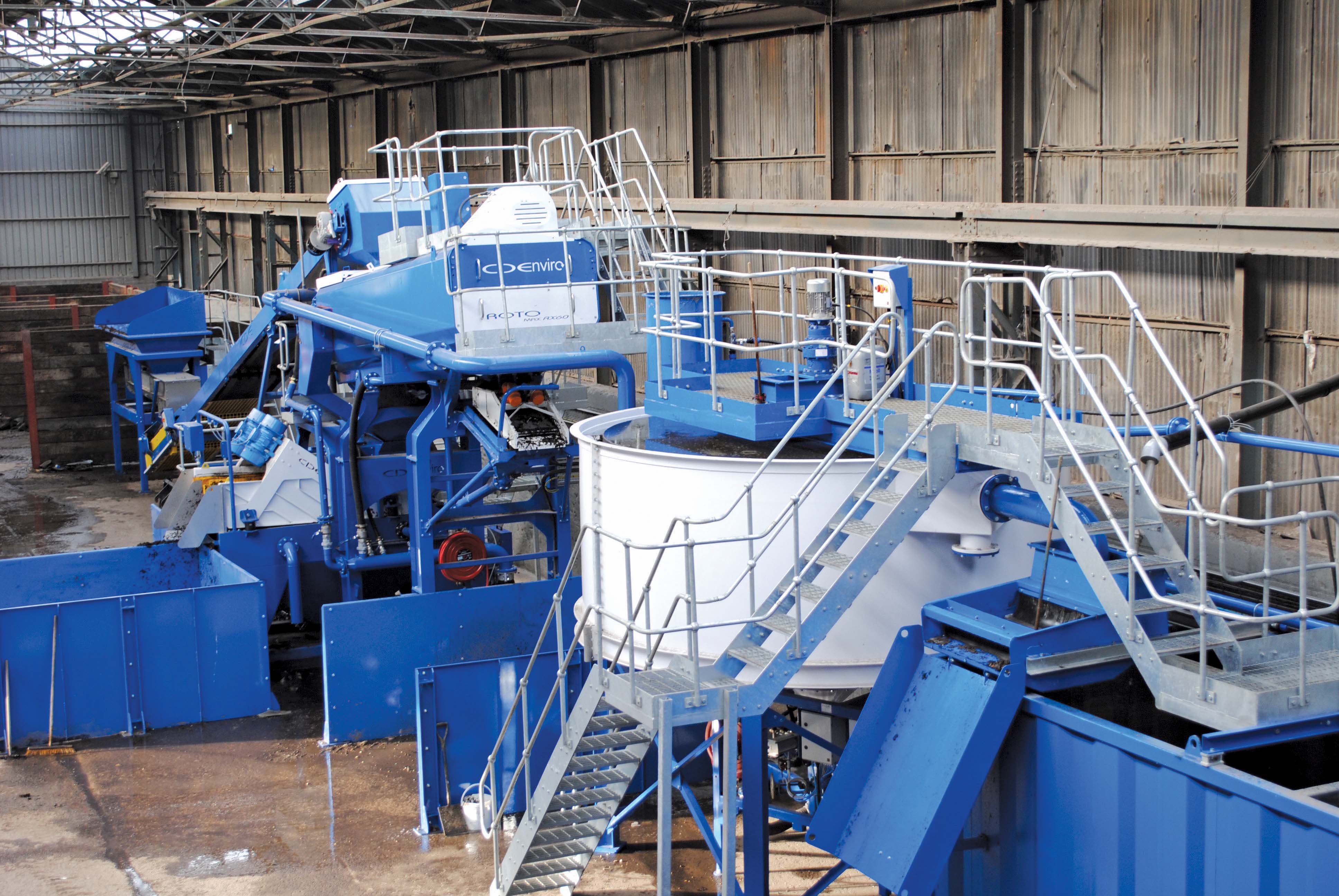
As the world’s ready supplies of natural materials diminish, the reuse or recycling of existing materials has taken on a new urgency.
No matter what the product, many countries have in place targets that they would like to achieve for the recycling of waste, with quarry products high on the list.
Indeed, the European Commission’s Waste Framework Directive (WFD) sets a target for 70% recycling of construction, demolition and excavation waste across Europe by 2020, and according to the latest figures available the amount of this material that was recycled was 61.8%.
While the straight presentation of this figure alone would indicate that progress is being made and the EU target is achievable, earlier this year Peter Craven, head of marketing at
In a comment he says that closer examination of the figures reveals that there is a huge difference between the top performers and those who as yet have not grasped the opportunity presented by CD&E waste recycling.
“Those member states that are on target have either hit the target already or will do so without much more effort.
On the flip side, those member states that will miss the target are so far behind schedule that it’s not achievable anyway,” says Craven.
“What is the purpose of any target? Surely it is to drive improvements, increase efficiency, encourage innovation? The 70% recycling target from the WFD does none of these things in its current form. By not addressing this issue now we will waste the next six years waiting to report on a target when we already know the answer.
“The UK, Germany, France, Benelux and the Alpine States will all hit the 70% target (some have reached it already) without having to change anything about how they approach the recycling of construction, demolition and excavation waste for the next six years.
“The Nordics, Iberia, Italy and the countries in Central and Eastern Europe will all miss the target, but will have made some investment in basic processing technologies for this material in an effort to demonstrate some degree of effort to reach the target.
“While the industry focuses its efforts on a meaningless 70% recycling target the volume of CD&E waste produced across Europe will rise to over 1.1 billion tonnes per year, a 26% increase on the current level.
“A recent report from Frost & Sullivan reported that “While 95% of this (CD&E) waste is reusable, recycling is just not being managed properly.” (The full comment can be found at www.cdeglobal.com).
In any event, few would argue that recycling is essential, and to this end CDEnviro has installed its first road sweepings recycling plant in the Southern Hemisphere at physical services company Citywide, Melbourne, Australia.
CDEnviro says the process of recycling road sweepings has been proven to divert waste from landfill while cleaning and recycling the washing water within the system. The turnkey road sweeping recycling solutions is said to provide the potential to recycle all incoming waste streams to realise the maximum reduction in waste to landfill.
Recycling road sweepings has become common in the UK in recent years because of the rising landfill costs and because of innovative technology, which has brought a commercially viable solution to the market place.
Indeed, since its installation in 2012,
Only recently the
The Stuttgart project saw the launch of the R2500 primary screening unit as the feed system for CD&E waste recycling plants. Its most significant development, says CDE Global, is the introduction of the new Infinity P2-75 bolted screen (a 5mx1.5m) aggregate screen which has been awarded a global patent as a result of the construction of the side walls of the screen.
In Denmark, the Christensen brothers from Tjæreborg opened a new recycling centre in Esbjerg to mainly recycle asphalt, concrete, bricks and other construction debris.
Seeking a new plant to help produce the most popular grain with a diameter of 0-32mm,
“I was personally completely convinced that this crusher would be perfect for their requirements,” says Klaus Meldgaard, sales manager.
On the first day 900tonnes of recycled material was realised and on the second day 1,200tonnes of final material 0/32mm was crushed.
The Rockster crushing plants can be supplemented with a screening system consisting of screen box and return belt, making crushing and screening possible on one mobile plant.
A company specialising in construction waste management and demolition has opened a new, state-of-the-art aggregate washing plant that will provide a local source of high-grade recycled aggregate products 12 months of the year.
R Collard’s new £2 million (US$3 million/€2.8 million) recycling facility in Eversley, County Hampshire, southern England, incorporates the latest technology to enhance the quality and efficiency of the recycling process.
Designed and installed by Duo in just six weeks, the plant contains the latest generation of washing systems supplied by
The plant is said to boast a number of innovative new features including cyclone technology that produces high-grade coarse sand product with 2% silt content; integrated sorting systems removing more non-mineral contaminants and enabling more wastes to be used as feedstock; it can operate all year round due to a new feeder system which can process cohesive material even when its moisture content changes, and it has fully adjustable components that enable bespoke products to be generated;
“The refinements to the technology involved will enable us to process more wastes than we collect from local sites and create a truly closed-loop recycling system for construction waste in the south of England,” says company founder and managing director Robert Collard.
Washing plants process construction and civil engineering wastes into a clean homogenous recycled product by removing contaminants and extracting silt and clay which bind the constituents together.
With its crushers, screens and stockpilers found working in many regions including New Zealand, Australia, Asia, across Europe and in the USA, Northern Ireland-based
County Kent based KKB Group specialises in providing practical solutions for the development of brownfield sites that increases the value and environmental performance of the regeneration process. Its offerings include surveying, land remediation, waste recycling, plant hire and aggregate production.
Paul Donnelly from RK6, says: “The DF410 tracked screener is the first screener Anaconda made and is today still the most popular.”
The DF410 offers three-way screening and stockpiling of a wide range of materials including demolition waste, crushed rock, sand and gravel, topsoil, compost, woodchip and coal. Features include a heavy-duty feeder complete with impact bed, heavy-duty belt, drop-down end plate for direct feed from crushers, and variable speed belt control. The screen can produce up to 250tonnes/hour depending on conditions.
US company
The company says that efficient separation of materials has historically been a difficult task for the recycling industry.
The state-of-the-art Eriez Magnetics Europe test centre allows customers to visit with bulk samples of material and see how accurately and efficiently the range of equipment on offer separates it, helping to determine which combination of machinery is the best fit for their waste processing needs.
The facility is equipped with Eriez’s full range of recycling products, including its complete line of eddy current separators, vibratory feeders and metal detection equipment.