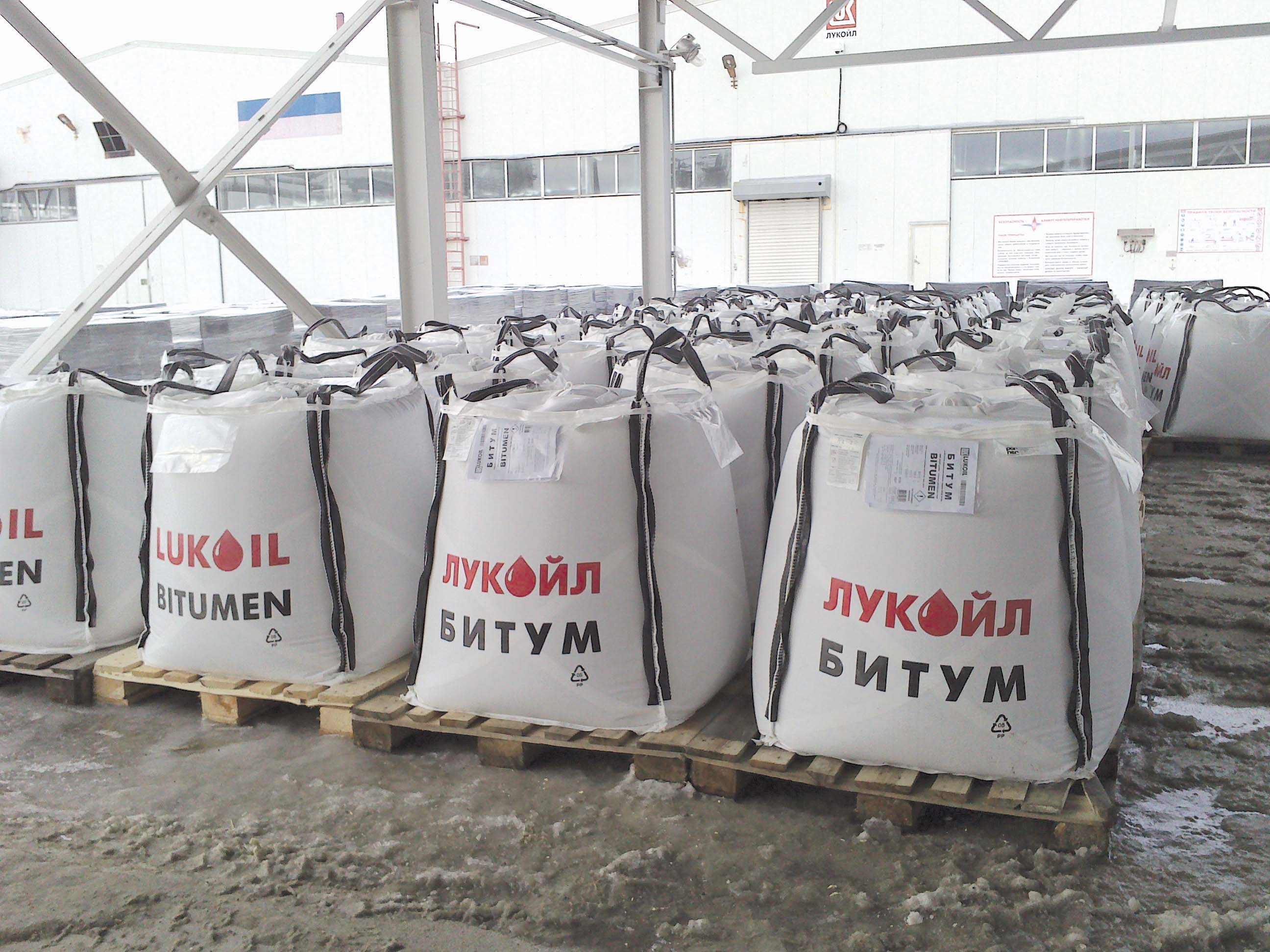
Bitumen is one of the most widely used products in the world, with an estimated 85% being used annually as the binder in asphalt for roads and other paved areas such as airports, writes Patrick Smith.
Indeed, world demand for asphalt is projected to rise 3.6%/year through to 2017 from a weak 2012 base to 121 million tonnes or 734 million barrels, according to a new World Asphalt study from The
The Asia/Pacific region has overtaken North America as the largest regional market for asphalt, driven primarily by strong growth in China and India, although demand for asphalt in the United States will rebound from the sharp declines in the 2007-2012 period while recovery in asphalt demand in Western Europe will be driven by increased spending on road works after years of very low spending on infrastructure improvements, although countries such as Turkey are also looking to improve infrastructure. With 23,000km of roads now, it has plans to grow that by 61% to 37,000km by 2023.
Today, roads are constructed with various types of modified bitumen, and global oil companies have been leading the way in polymer modified bitumen (PMB) research.
Warm mix asphalt, which is produced at low temperatures, is now among the many forms, which includes synthetic products alongside asphalt concrete, hot rolled asphalt, porous asphalt, stone mastic asphalts and thin surfacings. Such products have been developed to save money when building or maintaining roads or airports.
The International Air Transportation Association (IATA) reported that air passenger traffic surpassed 3.1 billion airline passengers, and is expecting more in 2014. With more flights and larger, more sophisticated aircraft such as the Airbus A380, airport runways at major international hubs need to withstand an enormous amount of weight, friction and heat from these larger aircraft. The Airbus A380, for example, weighs almost 400tonnes, the equivalent of approximately 400 family cars.
So when Dubai International Airport, the world’s second busiest international airport, required its two runways to be upgraded and resurfaced in May 2014,
Shell’s bitumen solutions have been used in airports since 1968, backed with Shell Bitumen’s technical expertise, and supply base spread out across the globe.
“Our state-of-the-art bitumen solutions and expertise in the airport sector has been a market leader for over four decades. Our dedicated Shell Bitumen Solution Centres work with our customers to develop solutions that suit their needs; not only in airports, but also in other infrastructure projects,” says Nick Chong, vice president of Shell Bitumen.
The Shell products used for the Dubai project included Shell Cariphalte DB, a special PMB grade, which the company previously developed for use in earlier projects at Dubai Airport in 2007.
It is a specialised runway pavement binder that provides the pavement with structural integrity in the face of very high flight operations (take-off and touch-down) especially with heavier airplanes and complex gear configurations.
Also used was Shell Cariphalte PG 76 Fuelsafe, a special type of PMB that preserves the pavement integrity in instances of fuel spillages that otherwise can lead to disintegration of the pavement layer.
These technologies were developed to provide airport operators with solutions that will require less maintenance as runway lockdowns for pavement maintenance are expensive and challenging.
Meanwhile, attendees at the recent Argus Europe Bitumen Conference in Rome, Italy, heard how the global bitumen market is changing, with the products now travelling further, a trend that is likely to increase in the future. This means new ways of transporting it over long distances are emerging.
“There is going to be a change in the marketing, logistics and consumption of bitumen,” says Albert Troxler, Poerner’s head of international sales.
Poerner has invested several years in developing bitumen bags, along with an associated cooling and packing system, which can hold 1tonne of bitumen. The bags can be transported using standard trucks and ships, and stored indefinitely before being melted: liquid bitumen has to be heated during transportation and can travel limited distances.
Poerner has already supplied its bagging system to refineries in Iran, Bosnia, Bahrain, and Russia, although Russian oil giant
Future areas of interest and research for the two organisations include rheology, the development of low temperature applications and understanding how binders from recycled asphalt behave, perhaps when recycled several times.