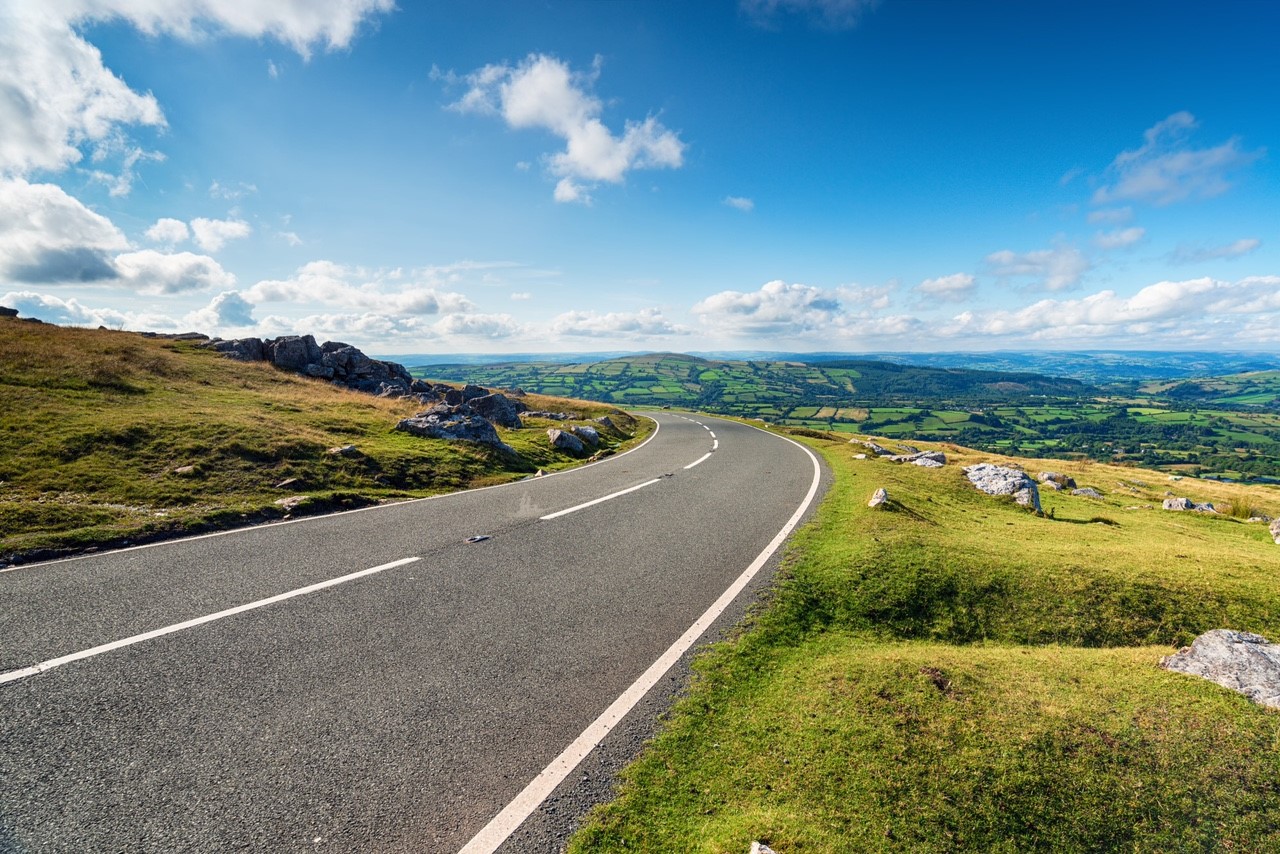
The UK-based building materials provider says that, as well as boasting a wealth of benefits from carbon savings, reduced build costs and enhanced life-expectancy, warm mix asphalt offers the same high quality and performance when compared to its hot mix equivalent.
Mixing at temperatures 20°- 40°C lower than hot mix asphalt (HMA) allows for a significant reduction in CO2 emissions by using less fossil fuels and resources during the manufacturing process. In addition, Aggregate Industries says nuisance fuming, odour and steam at the project site are minimal, enabling enhanced and safer working conditions at both the plant and site.
WMA also reaches trafficking temperatures quicker than conventional hot asphalt, enabling earlier reopening of carriageways to the travelling public, resulting in less traffic disruption and potential to reduce build costs. This will increase a contractor’s productivity by enabling more material to be laid within a working window, reducing the overall construction timeframe and subsequent delays to motorists.
Lower asphalt production temperatures greatly reduce binder ageing and in combination with the highly compactable nature of the asphalt, pavement life expectancy is significantly enhanced.
Surfacing contractor, Premier Road Surfacing, has already made the switch to Aggregate Industries' warm-mix asphalt. Matt Pursglove said: “Warm mix asphalt is a great product that has many benefits over the standard asphalt mixes. The benefit of using warm mix is that you can multi-layer within the same day if the site conditions allow, thus reducing the time required on site and lowering our carbon footprint. All our road planning produced goes back to Aggregate Industries’ mixing plants or quarries to be recycled back into the warm mix base and binder courses laid on our projects.”
Commenting on the transition to WMA, Vicky Smith, managing director of asphalt at Aggregate Industries, commented: "We recently made the switch from hot mix to warm mix asphalt across our range of asphalt products, which our customers have been piloting for a number of months.
“This is an important next step on our carbon reduction journey, and a vital move for the sector. Road networks will continue to be an integral part of society and it is how we produce the raw materials and construct them that must change to incorporate pioneering and advanced technologies, without compromising on performance and quality. We must find ways for roads to last longer and perform better.”
Smith added that if all production in the UK switched to WMAs, it would save around 61,000 tonnes of CO2 a year, the equivalent of cutting around 480 million kilometres (300 million miles) of car journeys. Up to £70m a year could also be saved through increased shift outputs. .
“Decarbonising construction materials and activities lies at the heart of Aggregate Industries as we strive to pave the way for a greener future. That’s why we have changed our way of working to use WMA as standard, which offers efficiency, sustainability and health and safety benefits without compromising on performance.”
Aggregate Industries says that lower temperatures for mixing also means that warm mix asphalt is easier to transport over long distances, saving time and money. When conventional asphalt is transported over long distances the logistical range is often restricted by asphalt temperature loss. Warm mix asphalt offers potentially longer haulage times to transport the product further without compromising workability.