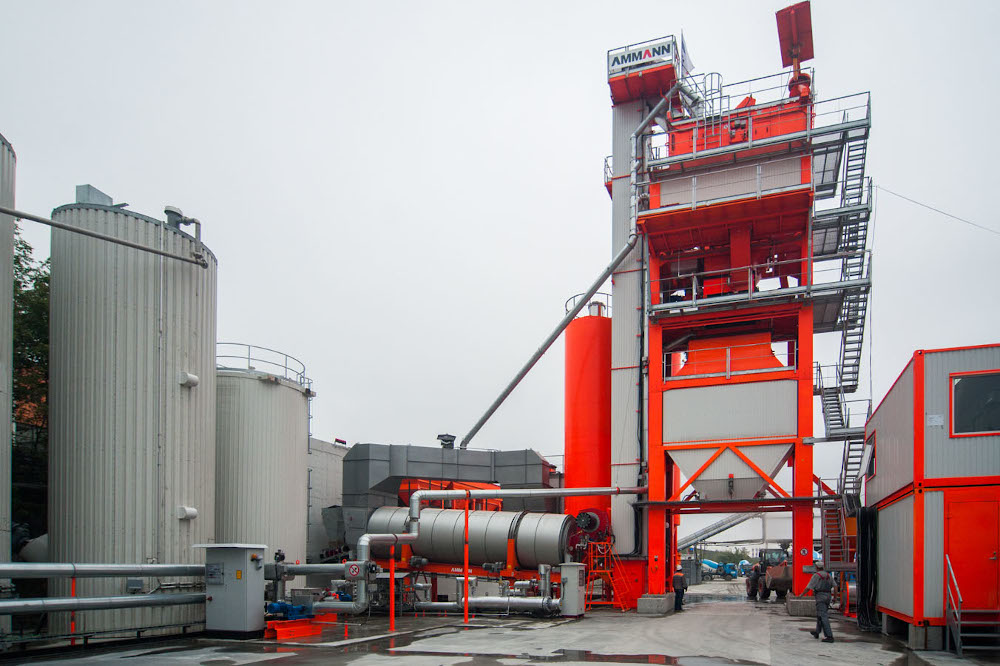
Tiger Mix, based in Vladivostok in south-eastern Russia, has been a concrete producer since 2016. It recently began asphalt production with the purchase of the Ammann ABA UniBatch.
Tiger Mix chose the Ammann plant in part because of its ability to utilise multiple fuel types, enabling the company to take advantage of the lowest-cost options as prices fluctuate. The flexibility ultimately will help Tiger Mix appeal to new customers and retain current ones by minimising mix prices.
Tiger Mix is also benefitting from Ammann’s environmentally friendly systems that lessen noise and dust levels. A green plant such as the ABA UniBatch can be located in residential areas and city centres, thereby reducing the customers’ hauling distances. Shortened routes can lower customer costs significantly in terms of fuel consumption, the number of haul trucks required – and the number of drivers, too.
The plant can also be fitted with components that can employ high levels of recycled asphalt (RAP). Tiger Mix sees a need for the increased use of RAP in the future, so the company was sure to acquire a plant that could easily add those capabilities.
The Ammann plant began operation in September. It was a quick turnaround from deciding to enter the asphalt market to producing the first batch of mix.
“The idea to expand production and acquire an asphalt-mixing plant first came up less than a year ago,” said Ilya Nemaltsyn, the general director of Tiger Mix. “The construction of the plant was relatively short – about eight months from the moment of the idea to the choice of a supplier and then finally to the commissioning.”
Nemaltsyn confirmed that fuel flexibility was a key factor in the purchasing process. “What’s unique about this plant is that it can operate on three types of fuel: natural gas, oil and diesel,” he said.
Having these options provides more than price protection. Some fuels are better at creating certain types of mixes, he said. “These choices provide flexibility in the production of mixtures and also meet all environmental standards.”
The plant can incorporate varied aggregates and bitumens and meets international quality standards. It produces about 210 tonnes of mix per hour.
“All the innovations that are available are applied in this plant,” said Oleg Avakin, Ammann area manager for the Far East. “All Ammann equipment is distinguished by a high degree of design study, reliability, economy in terms of energy efficiency, and environmental friendliness.”