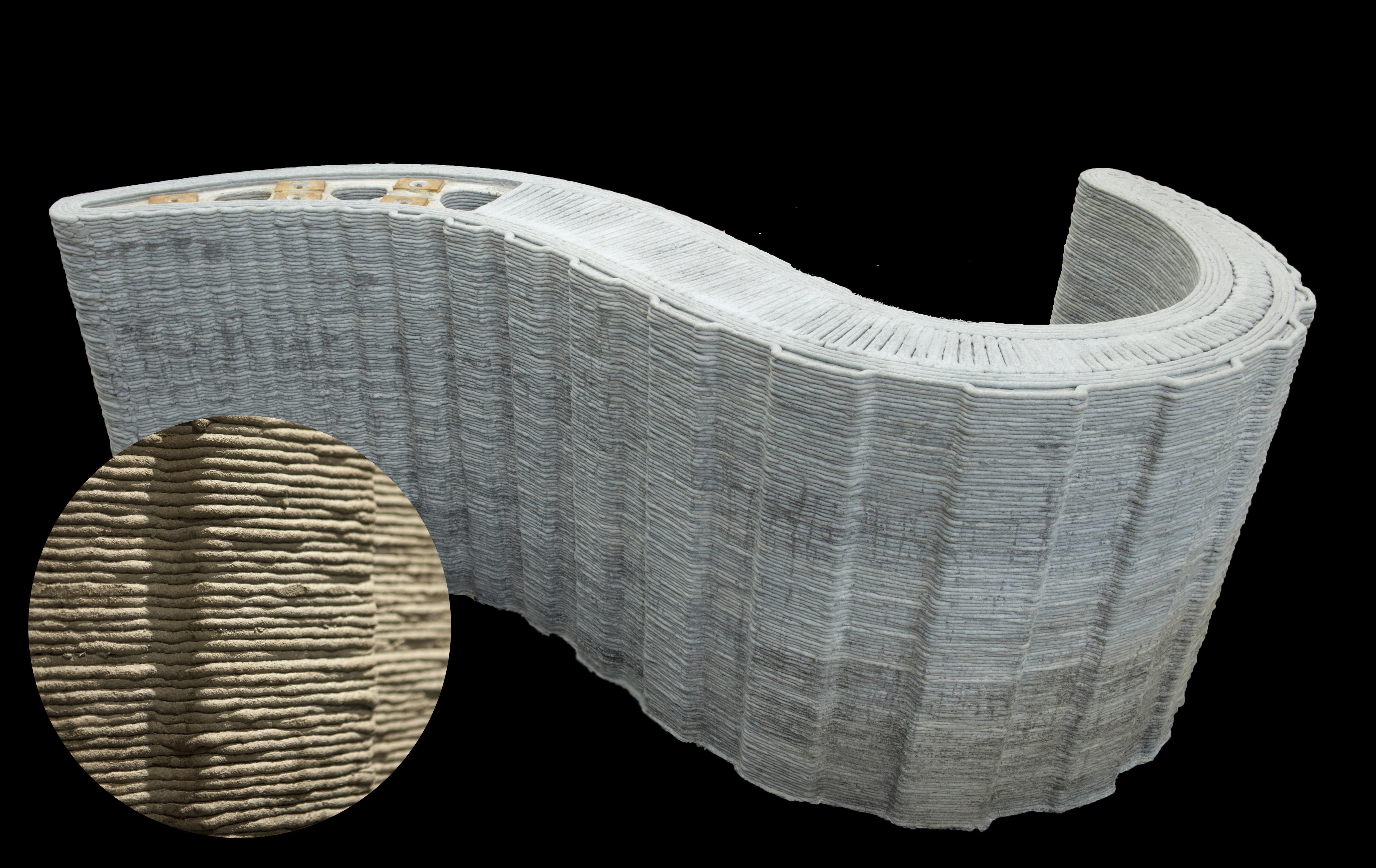
The versatility of concrete, the most widely used man-made material measured by tonnage, has been known for thousands of years writes Patrick Smith.
Ancient Romans made wide use of concrete, the incredibly flexible and adaptive blend of water, aggregates, sand and cement, and today it is still being developed.
For example, outside the more traditional uses, such as highways, bridges and buildings, global cement company
The aim of the agreement is to allow Skanska to use (under licence) 3D concrete printing technology developed through research at Loughborough University, applying it to real applications.
A team in the School of Civil and Building Engineering at Loughborough, led by Dr Richard Buswell and Professor Simon Austin, has worked on the development of 3D printing technology for the construction industry since 2007.
The project was started under the Engineering and Physical Sciences Research Council’s (EPSRC) Innovative Manufacturing and Construction Research Centre (IMCRC), and the team has developed 3D concrete printers fitted to a gantry and a robotic arm, which is now in its second-generation form.
The printer deposits a high–performance concrete precisely under computer control. It works by laying down successive layers of concrete until the entire object is created. The printer can make things which cannot be manufactured by conventional processes such as complex structural components, curved cladding panels and architectural features.
The aim of the initial 18-month development programme is to develop the world’s first commercial concrete printing robot.
Working with Skanska are a number of influential collaborators including Foster and Partners, Buchan Concrete, ABB and
The agreement puts Skanska in a good position to capitalise on an emerging technology with the potential to revolutionise the design and construction process.
“3D concrete printing, when combined with a type of mobile prefabrication centre has the potential to reduce the time needed to create complex elements of buildings from weeks to hours. We expect to achieve a level of quality and efficiency which has never been seen before in construction,” says Rob Francis, Skanska’s director of innovation and business improvement.
Dr Richard Buswell from the Building Energy Research Group at Loughborough University, says: “The modern construction industry is becoming more and more demanding in terms of design and construction. We have reached a point where new developments in construction manufacturing are required to meet the new challenges and our research has sought to respond to that challenge.
“We are pleased and excited by the opportunity to develop the world’s first commercial 3D concrete printing robot with Skanska and its consortium. We have been convinced of its viability in the lab, but it now needs industry to adapt the technology to service real applications in construction and architecture.”
With an investment of approximately US$2 million (€1.6 million), Cemex says that the start of sales and installation of the 100,000 ecological concrete cookstoves to improve the quality of life of approximately half a million people in Mexico and Guatemala by 2017 is an action it performs as part of the Global Alliance for Clean Cookstoves, an initiative that seeks to foster the adoption of clean cookstoves and fuels in 100 million households globally by 2020.
Meanwhile, Keyline has supplied a range of materials, including concrete products, for a new, safer design of roundabout which has been completed in Bedford, England, and is the first of its type in the UK.
The roundabout was previously one of the worst accident blackspots in the area, and the new turbo roundabout features plastic lane dividers which make drivers stay in their lane once they have entered the roundabout.
The council chose Manit Contractors for the project, and all of the concrete products used to construct the roundabout were supplied by Keyline, for whom Manit is one of its biggest customers.
The project features conservation kerbs, which are shot-blasted to provide the look of granite, to fit with the council’s increasing aesthetic preference for municipal schemes across Bedford.