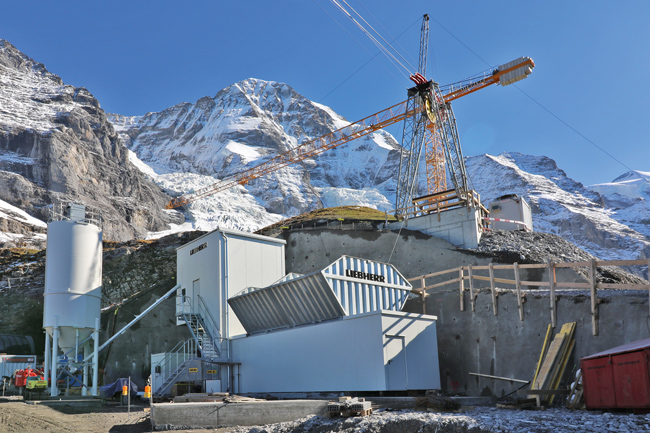
Manufacturer helps contractors to tackle logistical and on-site challenges of concrete supply for major Alps cable car scheme. Liam McLoughlin reports.
A
German-based equipment manufacturer Liebherr says the project was a challenge both in terms of logistics and on-site operation.
The Grindelwald-Männlichen Gondola Cableway company and Jungfraubahn railway company are planning to build the V-cableway that will open up both the Eiger Glacier and the Männlichen (Bernese Alps). From a joint terminal in Grindelwald-Grund, a tri-cable aerial cableway will lead to the Eiger Glacier and a ten-seater aerial gondola cableway to Männlichen. In addition, the new Rothenegg station will give the V-cableway a direct connection to public transport.
The project managers at ARGE V-Bahn Oberland were looking for a mixing plant with special properties that could be transported by cable car. They opted for the Compactmix 1.0 A-R/ RIM-M due to its compact design, system performance and pre-assembled, transport-optimised modules.
Since the aerial cableway was not ready for operation by the specified assembly date, the plant components were transported to the construction site by a 2-axle truck and dump truck. The plant itself was then built on the Eiger Glacier at an altitude of 2,340metres. For optimum mixing results, the plant is equipped with a ring-pan mixer with agitator system.
For concrete production at low temperatures, the plant is fitted with a winterproof housing. The aggregates and cement are also delivered to the plant by aerial cableway and fed directly from the cable car into the series silo. The clients as well as the contractors are Jungfraubahn AG and Männlichenbahn in Grindelwald.
At the forthcoming
The company says that another outstanding product to feature at bauma will be its new Powerbloc drive unit for the pump system. All hydraulic switching and metering elements are fully integrated, which eliminates the need for many hydraulic lines and other parts.
Liebherr says that its concrete technology operation, one of eleven divisions within the Liebherr Group, saw growth during 2018.
Construction waste such as concrete washout is under scrutiny from environment agencies around the world, largely due to its heavy metal content, notably chrome.
Concrete washout is the process of cleaning construction site equipment, such as the chutes of ready-mixed concrete trucks and hoppers of concrete pump trucks, to remove the remaining concrete before it hardens.
With the rate of construction unlikely to slow down, the Watson-Marlow Fluid Technology Group (WMFTG) predicts there will be no let-up in the quantity of concrete washout produced. The UK peristaltic pumps manufacturer says there needs to be an increased awareness of technology that can help concrete plants and construction firms meet growing demand, without suffering legal, financial or environmental consequences associated with waste disposal.
It adds that among such technologies are WMFTG’s latest Qdos chemical metering pumps and Bredel hose pumps, which are designed for tough applications such as construction sites, aggregate and concrete production plants.
Water contacting freshly exposed or poured concrete takes on an alkaline pH (circa 13) due to chemical reactions between the water and free lime particles within the cement. At a typical concrete plant, up to 12,000m3 of water is consumed every year, which means that the washing down of machinery, equipment and transportation vehicles becomes problematic.
WMFTG says the issue is equally prominent at construction sites, where there are many common sources of alkaline waters, including: washing chutes and drums used with fresh concrete; cutting or coring concrete structures; hydro-demolition processes; surface water run-off from recently lime-stabilised sites; stockpiled or spread-crushed demolition materials; placement of fresh concrete beneath groundwater (such as piled foundations).
While most are familiar with the dangers of acids, highly alkaline substances such as concrete wash water can be just as corrosive, and if left untreated can cause concrete burns, damage to vegetation and the surrounding ecosystem.
So, how does the industry go about resolving the high pH of wash water? WMFTG says that to adjust high pH wash water in line with consent levels, a process of neutralisation using controlled amounts of reagent is required. Typical reagents include mineral acid (either sulphuric or hydrochloric acid), citric acid, carbon dioxide (CO2) and self-buffering solutions.
The company adds that its peristaltic pumps are increasingly favoured for concrete washout applications, due to their extremely low maintenance requirements, and safe, non-contacting pumping method. Without mechanical seals or valves to leak or corrode, Qdos and Bredel pumps completely contain the pumped fluid, preventing operator contact with chemicals or spillage of untreated sludge.
Turkey-based ELKON has been chosen by a Hungarian contractor to supply its ELKOMIX-135 Quick Master compact concrete batching plant for a major road construction scheme. The EU-funded project, in an area close to the Austrian border, involves the construction of the second phase of the M85 motorway.
The M85 motorway is part of the European E65 road, which begins in Malmö, Sweden, and ends in Chaniá on the Greek island of Crete.
The ELKON plant will provide high-quality and non-stop concrete for the 21.8 km portion of the 88 km long motorway between the cities of Felsirákos-Sopron and Sopran-Nagylózs.
The plant is equipped with winter covering that enables the production of concrete even in heavy winter conditions down to -30°C. The concrete batching plant is closed with completely insulated panels and features an aggregate heating system with steam generator and aggregate heating pipes, along with automated cover over the aggregate bunker.
ELKON says the new project plays an important role in Hungary’s access to central Europe, and will reduce traffic congestion, shorten journey duration and help alleviate the burden of road transport in the region.
ELKON has been providing plant to the Hungarian contractor since 2015, having supplied a previous concrete batching plant for work on the bypass section of the EU-funded 8 highway (M8) project.
The two batching plants supplied have largely the same configuration, being equipped with 4500/3000 l. ELKON Twinshaft Mixers that have 120m³/h concrete production capacity. Their compact design is designed for easy installation and transportation. The 6x20m³ aggregate bins in both concrete mixing plants allow the storage of six different aggregates to be used in the special concrete mixture required by the project.
Northern Irish building materials provider Cubis Systems (a division of building materials company Cubis Industries) has co-developed a bespoke static concrete batch plant with Rapid International.
Until 2019, Cubis’ prior concrete production system involved the use of a volumetric truck mixer. This production method made the process of achieving desired outputs and tensile strength of the final product more difficult to control and time-consuming.
With a desire to continue targeting key global markets, Cubis required a new system which offered a greater degree of consistency, flexibility and increased outputs to keep pace with growth
The plant at the Cubis site in County Armagh integrates a Rapid RP500 1 door Planetary mixer, positioned on a specifically designed platform, granting easy access for maintenance.
The Rapid Planetary concrete mixer features outputs of 0.5m3 per batch, a pneumatically operated discharge door with heavy-duty mechanisms, extra thick chill-cast wall and floor tiles and a 22kW 3-phase motor.
The mixer is intended for precast applications, making it a suitable choice for Cubis. The mixer’s star mixing action is designed to create high turbulence, resulting in a consistent and homogenous mix. The mixer’s motor and gearbox are positioned on top of the mixer allowing easy access for cleaning and maintenance.
Cubis also opted for an optional Rapid Jetwash to enable fast and powerful mixer cleaning. The Rapid Jetwash is a fully galvanised, self-contained, high-pressure mixer washout system. Each wash cycle takes four minutes and the 2,000psi unit can power up to four mixers simultaneously.