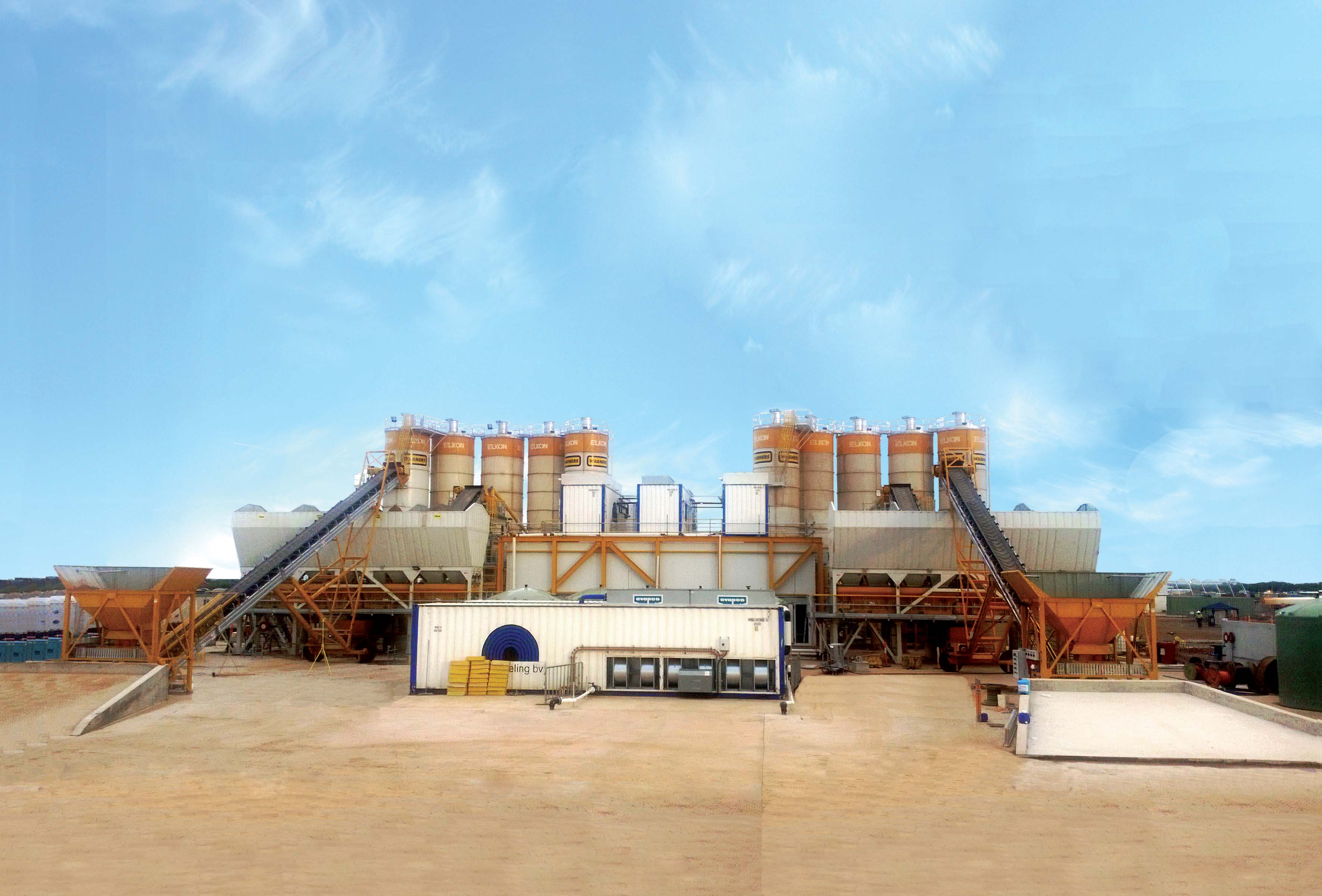
The formula for making concrete: water, cement and aggregates, seems simple, but concrete manufacture is a complex process. Developing various mixes for concrete requires advanced scientific skills, with the quality of the cement and aggregates and the dosage and proportions just some of the variables that influence the properties of concrete.
Likewise, the equipment for producing concrete has become more sophisticated over the years with precision measurement of the ingredients now standard on most machines.
For example, the Euromix 500 SM WEA Compact made by
Using a truck trailer with integrated water and power supply, the system is said to be ideally suited for off-road operations where infrastructure, such as building wind energy plants, railway lines, tunnels or bridges, is required.
In these fields of operations, the greatest challenges to concrete technology and quality assurance have to be met,” says SBM.
“Our singularly powerful Euromix 500 SM WEA Compact is an efficient solution for all manufacturers of mobile high-quality concrete,” says
All processes are recorded electronically and documented by data transfer meaning that, for example, demanding repair and restoration works can be carried out economically.
A German client is using a Euromix 500 SM WEA Compact at a wind park project in Northern Germany to pour foundations for wind energy plants.
To be able to counteract the forces appearing there and to assure both function and safety of the plant, the annular gap between concrete foundation and tower of the wind plant is poured with UHPC.
For this purpose, a superior fibre-reinforced concrete has to be produced in the open air in the shortest time possible.
The location-independent Euromix 500 SM WEA Compact concrete mixing plant with its integrated concrete pump presses the special concrete directly into the annular gap.
The mobile mixing plant can independently supply four of these sites/day with materials supply carried out by a separate supply vehicle to ensure direct transfer of the concrete additives on the building site.
SBM Mineral Processing, part of the MFL Group, which is a full-service supplier for stationary and mobile concrete mixing plants, as well as mineral processing and conveying plants for the raw material and recycling industry, says its plants are suitable for year-round operation and, importantly, can be used in extreme weather conditions.
Turkish company Elkon has exported and successfully put into operation two units of its Elkomix-135 stationary concrete batching plant at the Ichthys LNG Project, one of the world’s biggest liquefied natural gas (LNG) projects with US$34 billion (€25 billion )being invested in the scheme in Darwin, Australia.
In February 2012, the JKC Consortium (Japan Gas, KBR and Chiyoda Corporation) was awarded the contract for engineering, procurement and construction works of this giant project with a $15 billion (€11 billion) budget. The plant will be operated by Inpex of Japan and Total of France.
Elkon says it has a wide range of stationary type concrete batching plants with production capacities from 14m³/hour to 175m³/hour with one mixer.
“In addition to this, the capacity can be 200m³/hour, 270m³/hour, 300m³/hour and 350m³/hour in Stationary Type Concrete Batching Plants with double mixers on the same chassis,” says the company.
Such plants are mostly preferred for high capacity concrete production requirements, for special projects and for the projects which will take a long time in the same location.
“Elkon locates the stationary type concrete batching plants in limited areas to maximise benefits to the customer and makes special designs on customer requests.”
The plants have fully automatic computerised control systems and there is the possibility of different types of concrete production with different type of mixers with components from companies including
Prior to buying the Elkon equipment, personnel from the JKC consortium and Wagners Company (its partners on concrete production) visited Elkon’s factories along with other European concrete batching plant manufacturers.
“Elkon has successfully completed the requirements of this special project which was conforming to the Australian standards in a short time,” says Elkon.
“All welding processes are examined by non-destructive inspection methods (radiographic, ultrasonic, magnetic and penetrant) and reported in a detailed manner. Elkon specially redesigned the concrete plants against the cyclones in the Darwin region.”
The plants were put into operation by Elkon’s engineers in July, 2013, and each plant is equipped with 4,500/3,000litre Elkon Twinshaft mixers which has the production capacity of 120-135m³/hour of vibrated concrete (concrete that has been vibrated either internally or externally after it has been placed in order to produce a denser mass).
Each concrete batching plant is also equipped with five units of 150tonne bolted-type cement silos which also conform to the Australian standards.
“The whole plant was specially designed to be placed on zero ground level, so additional concrete foundations were not required. Aggregate feeding into the aggregate in-line silo is made by means of a special radial-type aggregate prefeeding system in the concrete batching plants,” says the company.
“An aggregate weighing system is used in these plants which can reduce aggregate weighing time.”
One of the world’s biggest construction companies,
The Austrian company selected an Elkomix-60 Quick Master Compact concrete batching plant to produce concrete for a hydroelectric power station project in Permeti.
The plant type, added to the production range of Elkon in 2009, is said to offer easy and quick installation, minimum foundation costs, compact installation area and less transportation costs.
Following this, Strabag also bought four more Elkon concrete batching plants (two Elkomix-60 Quick Master wet-type plant and two Elkomix-60 Quick Master dry-type plant) for construction work at the Alto Maipo Hydro Tunnel Project in Chile.
The Elkomix-60 Quick Master is equipped with 1,500/1,000litre Elkon twinshaft mixer and has the capacity to produce 55m³/hour of vibrated concrete.
Meanwhile, CEI Enterprises (an
The plant line will include nine new designs of concrete plants that will include both traditional batch plants and innovative new plant technologies.
Included in the new innovative technologies will be the conventional concrete, roller compacted concrete (RCC), and cement treated base (CTB) plant designs that had previously been produced by Astec, also an Astec Industries company.
As a result of this technology transfer, Astec is exiting the concrete production plant business to focus on a new renewable energy product line. This will move all concrete plant production equipment to CEI.
“The CEI concrete plants will feature innovative, leading-edge technology that will bring new solutions to concrete contractors working to build heavy civil, airport, highway and hydrodam projects,” says the company.
“These solutions will provide contractors with higher quality concrete at lower costs to produce it.”
Another achievement has been scored by Simem with the installation of an MMX 5000 super mobile concrete batching plant in Naples, Italy.
The project is sited in the Levante Darsena and will produce the expansion of the dock where container traffic is forecast to double in less than four years.
MMX stands for Mobile Mixing eXcellence, and represents in Roman numerals the year 2010, the year the plant was launched worldwide.
Two patents for industrial property referring to the moving mechanism of the mixer and chassis hood-scales were acquired by Simem in 2009, and thanks to these plants can ensure an hourly output capacity of 130m³ of high quality concrete, says Simem.