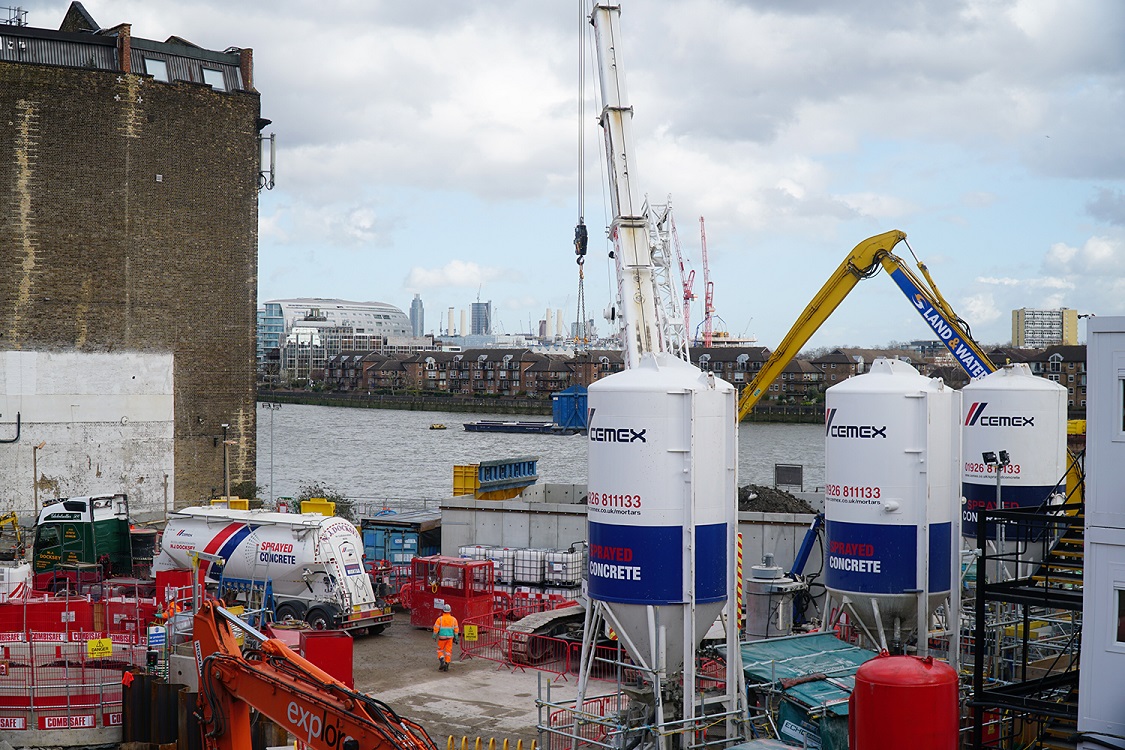
The tunnel will upgrade London's sewer system to cope with its growing population. Currently, London relies on a 150-year-old sewer system built for a population of less than half its current size. As a result, during periods of heavy rain, the existing infrastructure can become overwhelmed.
The new 25km tunnel will intercept, store and transfer sewage waste away from the River Thames.
Starting in Acton, west London, the Thames Tideway Tunnel will travel through the heart of London at depths of between 30 and 60 metres, using gravity to transfer waste eastwards and be processed and dealt with in a modern state of the art facility.
CEMEX's primary lining spray concrete is being used for the shafts and launch tunnels in the central part of the project – a 12.5km stretch of the tunnel moving under central London which is being constructed by a joint venture between Ferrovial Construction and Laing O'Rourke (FLO). The concrete is sprayed from bottom to top in one continuous operation until the shaft wall is complete. An extremely complicated mix is required, consisting of eight separate constituents which, when combined give ultra-high strength of +60n/mm2, consistency of 600mm flow and workability retention of two hours.
When sprayed, it has to adhere to the tunnel or shaft wall/ceiling and gain strength immediately to a very high strength gain requirement. The concrete also needs to be highly pumpable, in some cases with a pipeline length of up to 400m.
CEMEX manufactures the product at its dedicated Spray Concrete plant in Buxton, Derbyshire, from where it is transported into central London at rates that peak at around 3,000 tonnes per month. Supply is likely to continue for a few months, although this may be extended due to the coronavirus pandemic's impact.
Sergio Menendez, president of CEMEX Europe, Middle East, Africa & Asia, said: "The Tideway project is one of incredible scale which will solve serious capacity issues with London's sewer system and have considerable benefits for the area's wildlife and population, while also creating jobs, a rejuvenated river economy and new areas of public space.
"This is a serious piece of engineering, and we're proud to be working with world-class contractors to build this key infrastructure in the most sustainable and cost-effective way possible for one of the world's greatest cities.
Michael May, sales manager for CEMEX Mortars Europe, added: "Our sprayed concrete forms a key part of the central part of the tunnel and it was vital to get the complicated mix right. Fortunately, we have worked with FLO before, and so there was already an understanding of the works required and the performance required from the material to be supplied."
Borja Trashorras, project manager at FLO's Albert Embankment site, said: "CEMEX's primary lining spray concrete provided a good solution at Albert Embankment Foreshore for the construction of both connection tunnels and our 53m drop shaft through some challenging ground conditions. Having sprayed over 5,000 tonnes for this package of works meant we built a strong and reliable line of communication with CEMEX. Logistical planning was essential in the delivery of these works due to our central London location, which CEMEX was able to co-ordinate and support with ease."