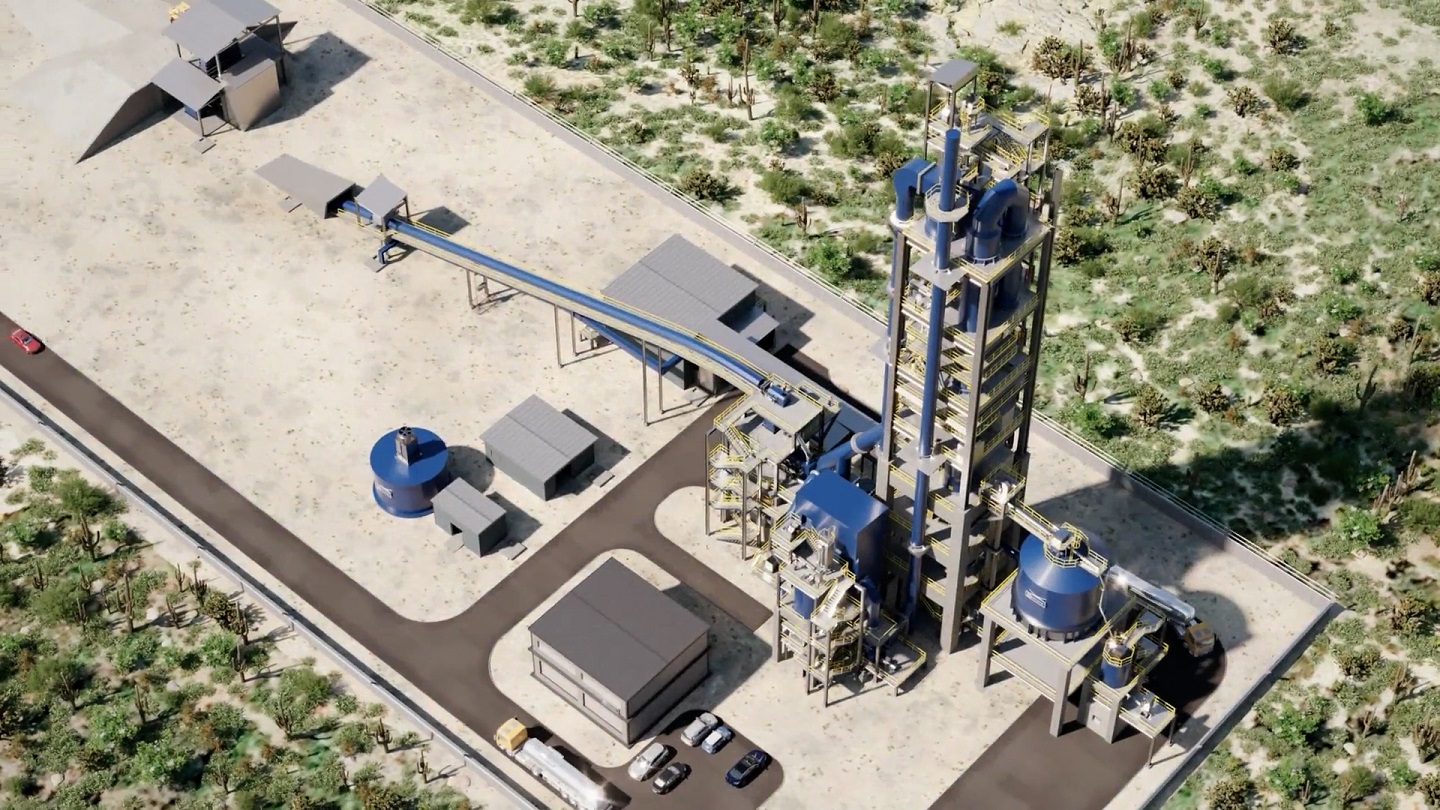
The technology will cut up to 20% of CO2 emissions compared to current practices on site. The order given to Denmark-based FLSmidth includes what is said to be the world’s largest gas suspension calciner system and a complete grinding station, adding another 120% grinding capacity.
FLSmidth adds that the order is set to provide significant reductions in carbon emissions to CBI Ghana’s cement production outside of Accra in southern Ghana. Together with the new grinding station, Swiss-owned CBI expects both financial and environmental return-on-investment from lower specific CO2 emissions, energy and fuel savings, and reduced costs from clinker imports.
“Ghana is the perfect location for using clay as an environmentally friendly alternative to clinker,” says Frédéric Albrecht, CEO at CBI Ghana. “West Africa is traditionally a clinker- and cement importing region due to the lack of suitable limestone reserves. Developing countries with their young populations and a growing need for infrastructure and housing represents the future in cement consumption. Calcined clay cements are the most sustainable alternative to traditional clinker-based cement. With the support from FLSmidth, we will be able to operate clay calcination in a large scale."
FLSmidth says that using calcined clay to minimise the need for traditional, carbon-intensive clinker is a key technology in eliminating the environmental footprint from cement production, which today accounts for 7-8% of the world’s CO2 emissions.
“In the light of the commitments made by the international community – most recently at COP 26, the CBI Ghana project is yet another example of how the cement industry is responding to the need for more environmentally friendly processes,” says Carsten Riisberg Lund, cement industry president at FLSmidth.
“Using clay as a supplement in the cement production is not new – it has been done for decades. But, with our new clay calciner system, we can produce a highly reactive clay that is able to substitute between 30-40% of the clinker in the final product, resulting in up to 40% CO2 reductions per ton of green cement compared to traditional OPC cement."