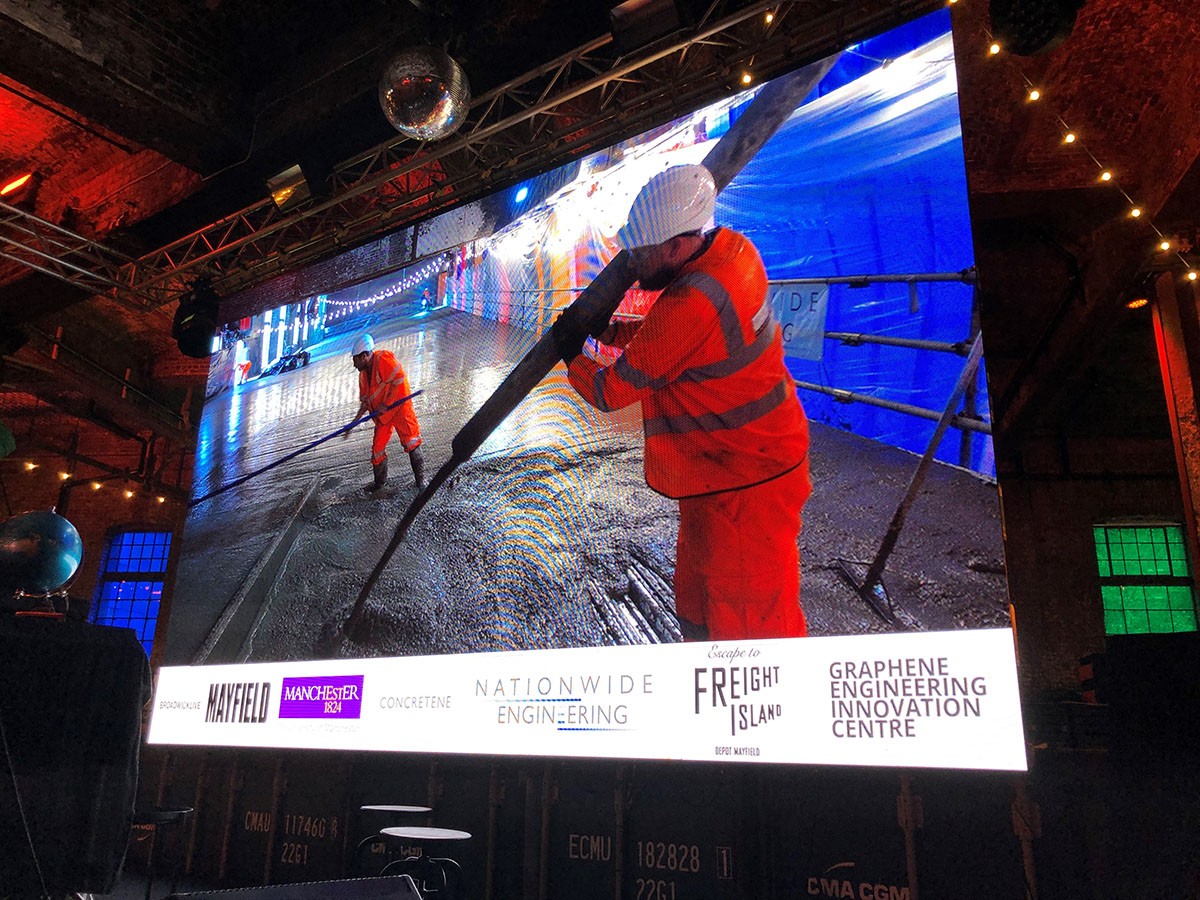
The new 'Concretene' product - developed by Nationwide Engineering and The University of Manchester in the UK - has been used for the first time (on October 12) in Manchester’s Mayfield regeneration scheme.
Concretene uses graphene – the 2D material discovered in Manchester – to significantly improve the mechanical performance of concrete, allowing for reductions in the amount of material used and the need for steel reinforcement. The creators claim this can reduce CO2 emissions by up to 30% and drive down costs, meaning Concretene is both greener and cheaper for developers.
The creators say that Concretene has great potential to address the construction industry’s need to lower emissions, by reducing the amount of concrete required in construction projects by as much as 30%. It also offers efficiency savings by slashing drying time. Pours of Concretene to date have achieved the equivalent of 28-day strength in just 12 hours.
At Mayfield, it has been used to create a new 54m x 14m mezzanine floor, which will become a roller disco at the Escape to Freight Island attraction in Mayfield’s vast site, a former railway depot.
The installation is the first ever commercial use of Concretene in a suspended slab and is said to mark an important step towards testing and developing it as a widely-used building material, allowing it to be used as a substitute for concrete on an industrial scale.
The Concretene pour is intended to help reinforce Mayfield’s return to prominence in the city amid a £1.5bn regeneration project.
The material has been developed by the University of Manchester’s Graphene Engineering Innovation Centre (GEIC) and Nationwide Engineering, a company co-founded by a former University of Manchester civil engineering graduate, Alex McDermott.
Nationwide Engineering co-founder Rob Hibberd commented: “This is a huge milestone for the team, as not only is this our first commercial, third-party use of Concretene, but also the first suspended slab as used in high-rise developments.
“As world leaders in graphene-enhanced concrete technology, the interest from the international building industry has been beyond expectations, as looming legislation is forcing significant carbon reductions throughout construction."
He added that his company's partnership with the University has fast-tracked the development of Concretene, going from lab to product in 18 months.
James Baker, CEO of Graphene@Manchester at the University, said: “This Manchester-based technology can also contribute to levelling up by positioning our region as a global R&D centre for sustainable materials for the construction industry – attracting investment, creating new businesses and offering high-wage jobs.”
Arlene van Bosch, development director, U+I, added: “Our ambition is for Mayfield to become an exemplar sustainable neighbourhood, where people and planet come first. Innovations such as the use of Concretene are central to realising our vision – we want to push the boundaries of design and construction to create the most environmentally-friendly place possible."
The pour of the suspended slab at Mayfield marks a significant step towards testing and developing Concretene as a widely-used building material, allowing it to be used as a substitute for concrete on an industrial scale. Graphene for the pour at Mayfield was provided by Versarien, a Tier 1 partner of the GEIC.
Production of cement for concrete is one of the leading causes of global CO2 emissions, producing around 8% of total global emissions.
Most commonly, graphene is a material extracted from graphite but it can be derived from many different products, including recycled plastics or biomass. The creators say this makes Concretene a game-changer in the race to lower the industry’s whole-life carbon footprint.
The use of graphene in concrete produces 6.3kg of CO2 per tonne of concrete – a 21.94kg reduction per tonne compared to traditional steel reinforcement. The total estimated reduction in CO2 emissions for this floor slab compared to a traditional concrete solution is 4,265kg.