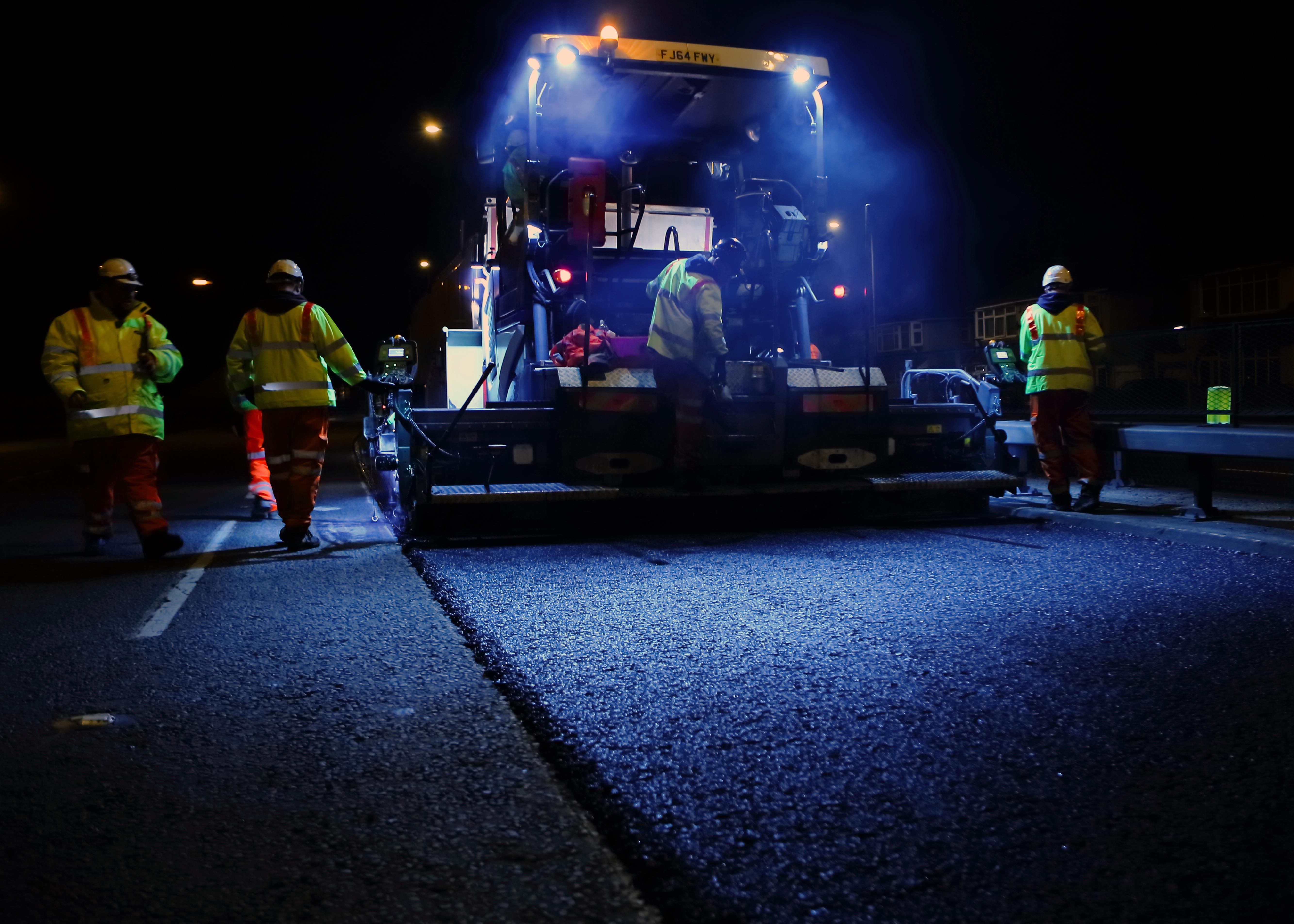
Aggregate Industries’ Contracting Division has unveiled a new state-of-the-art automated data gathering system, which is set to make the road surfacing process “infinitely safer”. Guy Woodford reports.
Introduced in line with the company’s zero-harm ethos, Aggregates Industries’ Contracting Division’s new system, known as Automated Inspection and Testing (AIT), will see all pavers, rollers and survey vehicles fitted with the latest technology, including GPS, infra-red sensors and a data recording unit – all of which will be used to automatically capture high quality data before, during and after the surfacing process.
The innovative initiative has been designed to minimise the risk to employees during pavement construction by replacing the need for a human technician to carry out the highly dangerous task of data capture. The investment by one of the UK’s leading building materials suppliers, which also offer a national road surfacing and contracting service, follows a number of serious incidents across the industry in recent years, including fatalities.
Neil Leake, national technical manager at
“By removing the need for technicians in data capture altogether, our AIT system is a new state-of-the-art approach that could potentially save lives - with extensive trials proving it has made the road surfacing process infinitely safer. At the same time, it will also go a long way in plugging the industry-wide skills shortage, as it means data capture operatives can now be redeployed to other contracting areas in urgent need of skilled staff.”
After consulting with leading materials and testing firm Mattest Southern, Aggregate Industries formulated the AIT system so that pavers and rollers can be linked together to manage the compaction process, by recording the rolling temperature and the number of passes.
Meanwhile, the final element of the AIT procedure is surface texture and rolling straight edge testing of the finished pavement, which, using laser scanners and video recording, can now be completed with improved accuracy and without the need for a human technician. The result is a complete record of the laying process with zero risk to employees.
Leake added: “The AIT system has proved to be an incredible success. Following extensive trials to determine the accuracy of the data gathered, we are now using it on a number of contracts and have seen marked improvements in safety across the board, whilst at the same time providing enhancing asset management data for our customers that also meets Building Information Management (BIM) compliance.”
Paddy Murphy, managing director of Contracting Services at Aggregate Industries, said: “Innovation and safety is at the heart of everything we do. Therefore, I’d like to thank all those involved in this project for their hard work and commitment in creating a system we hope will make a lasting contribution to improving safety standards across the industry.”
In other health and safety news, Hanson, a leading UK building materials supplier, has extended its vehicle fleet with the arrival of the first of 40 new low-entry cab ready-mixed concrete trucks, reflecting the firm’s ongoing commitment to road safety.
The Euro 6-engined trucks have a panoramic glass cab design and are fitted with 360° cameras. This, coupled with the lower driving position, significantly improves the driver’s visibility of cyclists and pedestrians, particularly on the near side.
The highly manoeuvrable front and rear-steer aided trucks are also fitted with a lightweight drum, improving efficiency and saving fuel by increasing the load size from 7.5 to 8m³.
The vehicles are initially being used in London, where they form part of Hanson’s services to the Thames Tideway Tunnel project, while also helping to meet Transport for London’s direct vision standards.
Matt Barlow, supply chain director at Hanson, said: “Safety is our number one priority and these new trucks fit the bill: they improve safety on construction sites, and help to protect vulnerable road users, which is vitally important in busy urban areas.”