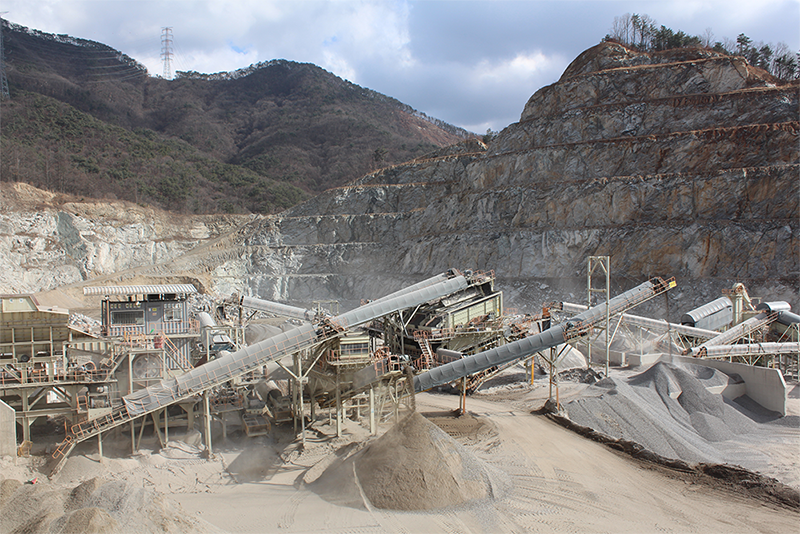
South Korean aggregates, sand and gravel demand is rocketing. While high demand is not unusual given that 81% of its population of 51 million live in urban areas, creating a constant need for new infrastructure, such is the current building boom over 390 million tonnes were consumed nationally in 2021, according to figures published by the South Korea Ministry of Land, Infrastructure and Transport (MOLIT). That is a comparable consumption level to France. Furthermore, South Korean aggregates, sand and gravel consumption is tipped by the same source to rise to over 420 million in 2022. This represents a lot of orders for the country's 500-plus quarries.
The election of Yoon Suk-yeol, a conservative former prosecutor, as South Korea's new president in March 2022 is unlikely to impact the firm infrastructure spending commitments made by former president Moon Jae-in. Yoon and his People Power Party triumphed over Lee Jae-myung and his Democratic Party following a bitter battle in a politically divided nation. Under the South Korean constitution, presidents are restricted to a single five-year term.
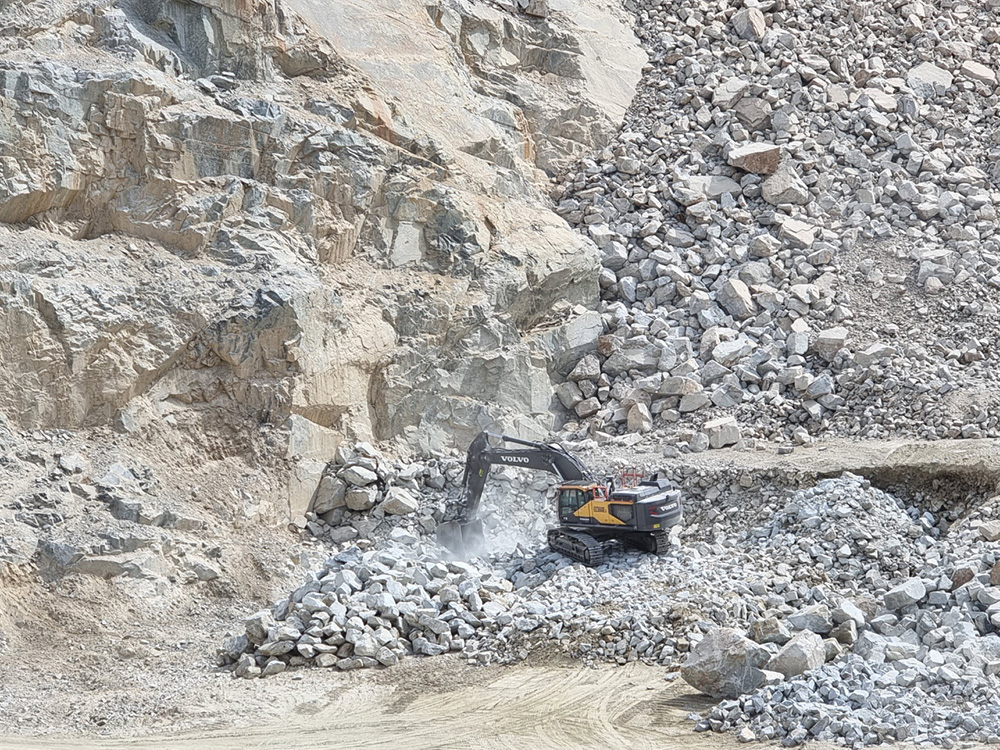
Washing plant giant CDE's PT CDE Southeast Asia business says the biggest aggregates, sand and gravel demand in South Korea is centred on the country's capital, Seoul, and Incheon, South Korea's third-largest city, in Gyeonggi province, in the north-west of the country (169.403 million tonnes in 2021)
Speaking about the key issues South Korean aggregates, sand and gravel producers face, a company spokesperson said: "Currently it seems to be very difficult to acquire permissions for new quarry or to extend permission period for existing quarry. This is due to restrictive environmental measures.
"We have heard complaints about decreased turnover due to the implementation of a government's 52-hour workweek policy. There are also challenges in finding personnel, and new legislation has been put in place regarding management and ownership accountability for severe accidents on sites."
Commenting on what kind of aggregate, sand and gravel washing plant South Korean quarrying customers are looking for, the spokesperson continued: "Because of high land prices, customers prefer compact facilities. Some are also looking at two-level washing plants solutions. All customers want high efficiency, low water content in their sand products and less water consumption."
Lee Yongjik, vice president of the Korea Aggregates Association (KAA), echoed CDE Asia's mostly upbeat appraisal of the South Korean aggregates market: "We're expecting aggregates demand to increase over the coming decade, as the [former Moon Jae-in] government announced a plan to provide 300,000 more houses in Seoul's satellite cities to stabilise real estate prices. The price of real estate has doubled in many parts of the country during the last couple of years, and it has become impossible for young people to purchase homes. Getting timely quarrying permits to meet increasing aggregates demand is a very important issue."
Lee said the government also committed to building a further 1.27 million homes in the metropolitan Seoul area through its New Town Development Plan. "It also secured land for another 830,000 homes, so we need to plan for the seamless supply of aggregates for those homes," he stressed.
Commenting on concerns over South Korea's aggregates extraction licensing rules, Lee continued: "The licence to extract aggregates is given by the Korea Forest Service. The main mission of the Korea Forest Service is to preserve the forest, not to ensure a timely supply of aggregates. There is not any institution that balances such conflict of interests. Thus, there is a problem with meeting demands for aggregates. About 40% of all aggregates supply comes from quarry extraction in the mountains.
"In order to make up for a decrease in other sources of primary aggregates, we need to increase quarry extraction, but getting a licence is very difficult. This can lead to unreliable aggregates supply. In 2017, 60% of the planned amount was met, whereas, in 2020, 94% of the planned amount was supplied. Taking an average over the past six years, 82% of the planned mountain aggregate amount was supplied."
Lee said that since 2021, incentive points are awarded in the Aggregates Extraction Competency Assessment to South Korean aggregates supply businesses operating 'environmentally friendly' facilities or equipment. Factors influencing an assessment score include deploying electric excavators, dust suppression systems, and operating closed stone crushing facilities.
"The Korea Aggregates Association and the aggregates industry are working hard to change laws so that local governments license businesses based on good production planning to ensure timely and quality supply of aggregates," explains Lee.
"We are also pushing to find a good governance solution where the currently mandated need for resident/local fishermen approval for marine aggregates dredging can be negotiated to lead to a win-win situation.”
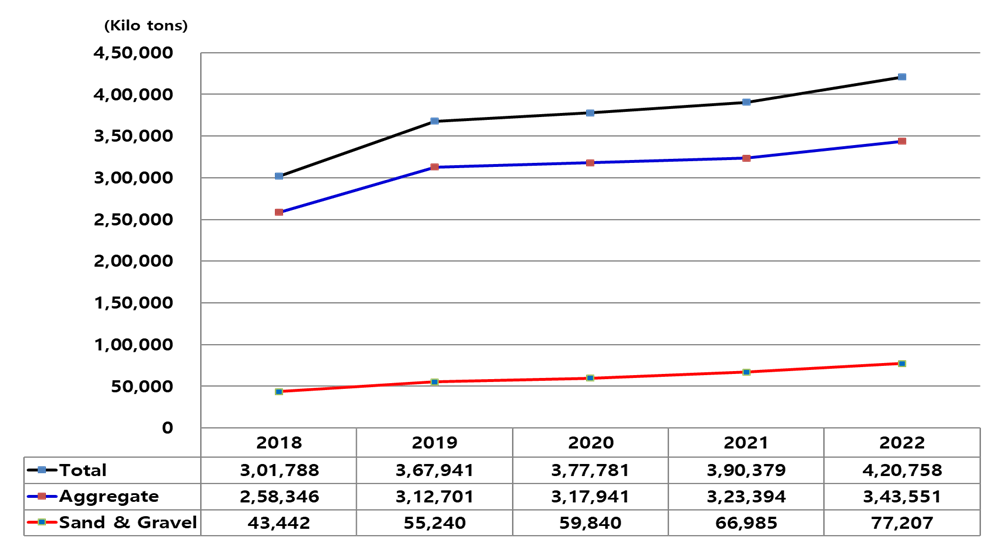
Lee said that the Korea Aggregates Association is also working to change the criteria of the Post-Environmental Impact Assessment (EIA) for closed quarries. "It is required for an aggregates supply business to conduct an EIA for three years after it has closed the quarry and has made restoration of the site. However, other development projects only go through an EIA at the closing of a site or project. It is unfair that quarries are subjected to a different interpretation of the regulations."
Kyounghun 'KH' Lee, key account manager at Volvo Construction Equipment's South Korean business, said South Korean quarrying customers tend to opt for larger rather than medium-sized wheeled loaders and crawler excavators. "This improves productivity and reduces labour costs considering the expansion, strengthening and implementation of the 52-hour workweek (five days a week) policy and the Serious Accidents Punishment Act.
"For example, whereas the Volvo EC300E excavator and L150H and L180H wheeled loaders were the most popular in the past, the most common models now are the Volvo EC380E and EC480E excavators and L220H and L260H wheeled loaders. Larger wheeled loaders with a bucket capacity of over 7m³ are generally preferred since these can load a 25-tonne tipper truck in three passes."
Lee said: major South Korean quarrying and aggregates customers are also greatly interested in Volvo Co-Pilot and Assist Services. "These customers are the most concerned about working efficiency and productivity. Load Assist with On-Board Weighing, for example, is becoming increasingly popular as it can calculate precise delivery amounts to eliminate conflicts between primary contractors and subcontractors due to inaccurate delivery amounts."
Asked about the growth potential for Volvo CE in South Korea's quarrying sector, Lee said: "We have strong opportunities to increase our sales of large excavators and wheeled loaders, which are highly preferred in quarries because of their superior operating performance, high productivity, high fuel efficiency, and strong durability. We also expect to increase our sales of articulated haulers, which work well in partnership with our larger excavators and wheeled loaders.
"We also have opportunities to support customers to decrease the carbon footprint of their operations. The recent strengthening of environmental regulations and volume restrictions for quarries have made aggregate supply unstable. Hence, aggregates producers are seriously concerned about environmental impact due to the growing possibility of a supply shortage of natural aggregates compared to demand."
Lee said that according to MOLIT, aggregates would be supplied this year based on the principle of regional self-supply. If there is a shortage, the transport of sea sand from South Korea's EEZ and neighbouring areas will be adjusted to stabilise the aggregates supply for each region. An EEZ (exclusive economic zone), as prescribed by the 1982 United Nations Convention on the Law of the Sea, is an area of the sea in which a sovereign state has special rights regarding the exploration and use of marine resources, including energy production from water and wind.
"Given quarrying conditions and the trend to decrease natural aggregate sources, MOLIT plans to use forestal aggregates and crushed aggregates as much as possible, and to promote the use of alternative aggregates, such as recycled aggregates," continued Lee. "In addition, MOLIT plans to invigorate the production of crushed sand within regions lacking their own sand production and to meet the shortage by importing coastal sand from the West Sea EEZ and the Ongjin and Taean areas."
Lee said that as well as a major increase in housebuilding in 2022, as outlined by MOLIT, being good for aggregate demand, The Bank of Korea's economic outlook report also offers much encouragement for aggregates demand as construction investment in 2022 is expected to increase 2.9% compared to 2021. Major transport infrastructure projects, such as Seoul's GTX (Great Train Express) super-fast subway, will, believes Lee, also support increased aggregates demand. The first route of GTX railway is due to open in 2024.
Hyundai CE invests in production
Hyundai Construction Equipment (HCE) is investing US$170mn in its Ulsan production plant in South Korea, increasing capacity by 50%. The move will support the business's growing presence in the booming global construction equipment market while providing a manufacturing base for a new generation of electric- and hydrogen-powered equipment.
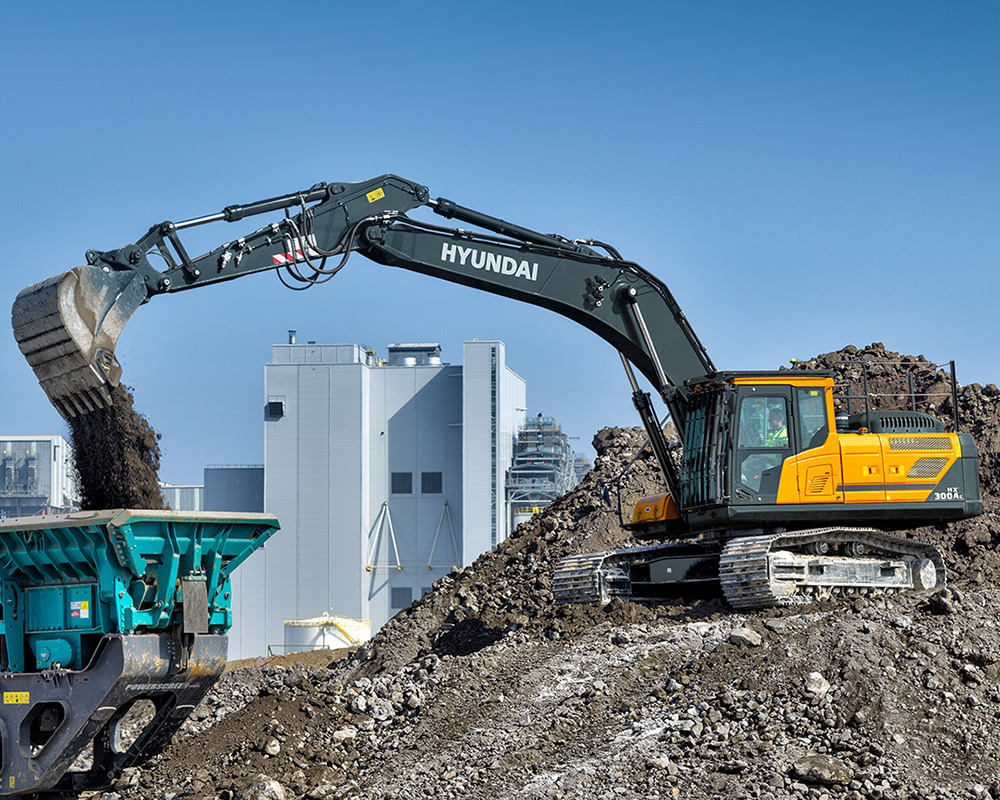
The investment, to be delivered over the next four years, will increase production at the giant plant by 4,800 units a year, bringing annual capacity to 15,000 excavators, wheeled loaders and other construction models.
HCE will merge the production and assembly functions currently in Factory 1 and Factory 2 into a single facility, simplifying processes and increasing savings by maximising efficiency. This will reduce the working hours involved in machine production and cut logistics costs throughout the supply chain. The move will also reflect HCE's environmental, social and governance factors, using eco-friendly sub-materials when conducting interior and exterior finish work.
The company is increasing its market share in every business region by responding to current market trends in the global construction equipment market and by looking ahead to the customer requirements of tomorrow's infrastructure and construction projects. The company is also planning to benefit from the recent US launch of the 'Build Back Better World (B3W) initiative for developing countries.
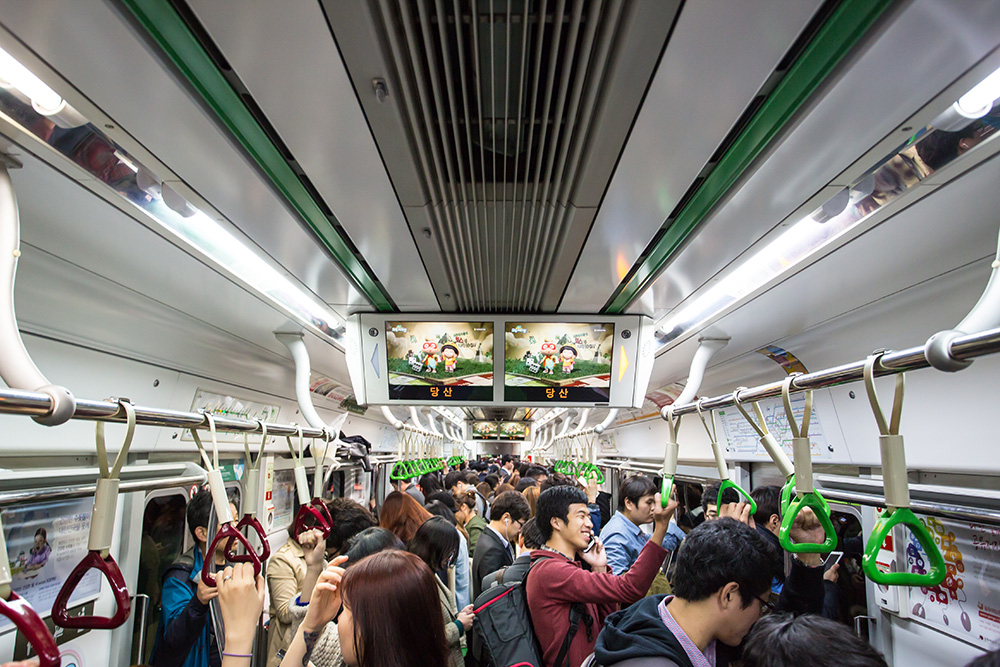
HCE announced in 2020 that it plans to bring to market a range of excavators powered by hydrogen fuel cells, produced in cooperation with Hyundai Motors, which has its largest automotive plant in Ulsan. The company has already unveiled a range of hydrogen-powered industrial forklifts that will launch in 2023. It continues to develop the low- and zero-carbon emissions equipment that the customer will demand in the future.
"Strengthening the competitiveness of the Ulsan factory is the first challenge that needs to be addressed to reach the global top five, the goal of the construction equipment division of the Hyundai Heavy Industries group," said CEO Choi Cheol-gon. "With this investment, we will further raise our brand competitiveness by producing and delivering construction equipment with increased efficiency."
In November 2020, HCE completed the construction of a technology innovation centre, investing $65mn. The new centre includes 16 laboratories, employing more than 100 researchers. It is involved in research and development projects focusing on eco-friendly technologies, high-efficiency and noise-reduction technologies and a virtual verification system. The site also performs quality research and verification of components and completed equipment.
Uni researchers develop storable cement-based energy material
Engineering researchers at three South Korean universities have developed cement-based composites with conductive fillers that generate and store electricity by contact electrification.
Smart cities that champion sustainable net-zero energy consumption are no longer a new-fangled concept. However, achieving this state seems plausible only in the distant future for the building sector.
Now, university researchers have developed a novel cement-based composite that can generate and store energy induced via contact between materials. This material could be used to build buildings that can harvest energy from human motion in their floors and wind and raindrops hitting them.
Everything around us is getting smarter, from devices to home appliances and eventually entire cities. The concept of a smart city, which involves energy-efficient ecosystems that can reduce carbon emissions, save energy, and provide better lives, is no longer a thing of the distant future. However, it's worth noting that since the building sector alone is single-handedly responsible for 40% of the entire modern world's power consumption, buildings need to be able to offset this energy consumption.
The solution to this problem may be closer than you might think. In a recent study published in Nano Energy, researchers from Incheon National University (INU), including Prof. Seung-Jung Lee, and researchers from Kyung Hee University and Korea University, addressed this issue by developing an all-new structural material that can make construction more eco-friendly.
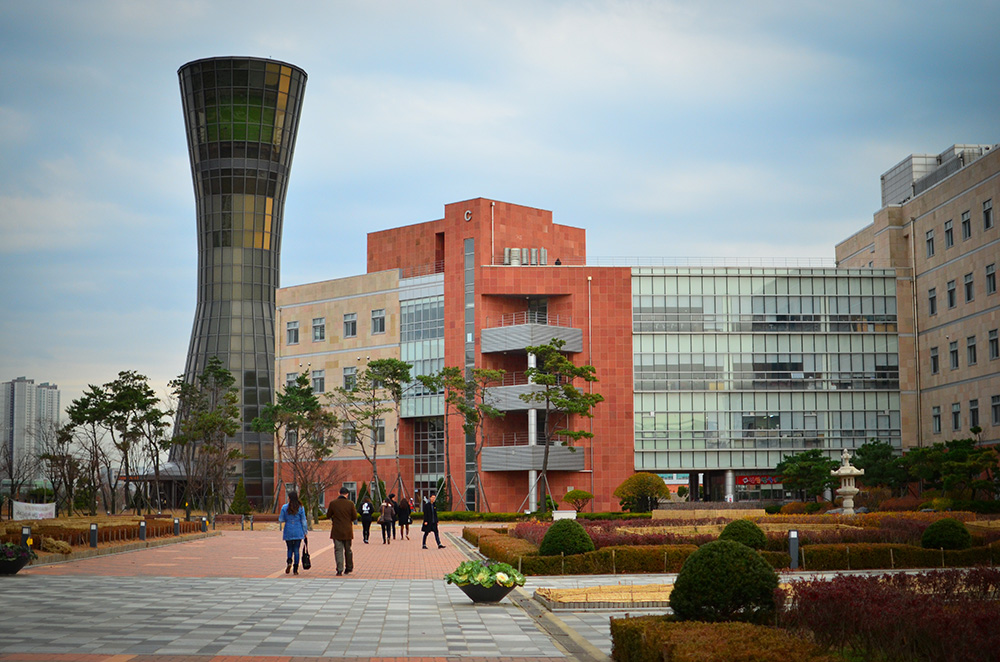
The team developed a cement-based conductive composite (CBC) with carbon fibres that can also act as a triboelectric nanogenerator (TENG)— a type of mechanical energy harvester. This paper was available online on 3 August 2021 and was published in Volume 89, Part A of the journal Nano Energy in November 2021.
"We wanted to develop a structural energy material that could be used to build net-zero energy structures (NZES) that use and produce their own electricity. Since cement is an indispensable construction material, we decided to use it with conductive fillers as the core conductive element for our CBC-TENG system," explains Lee. The concrete exteriors of buildings are often exposed to external mechanical energy sources such as ocean waves, movement of objects, wind on the walls, and raindrops on the roofs. Cement-based TENGs can harvest energy from these sources via contact electrification— a process where electricity is generated due to interactions between two materials.
The team designed a lab-scale NZES and a CBC-based capacitor using the developed material to test its energy harvesting and storage abilities. The results indicated that at a 1% volume of conductive carbon fibres in a cement mixture, the CBC mixture exhibits optimal electrical properties while retaining the superior mechanical properties of cement. The researchers' electrical measurements confirmed that CBC-TENG could be safely used as a building material as the current generated by it was much lower than the maximum allowable current for the human body.
Apart from energy storage and harvesting, the material could also be used to design self-sensing systems that monitor the structural health and predict the remaining service life of concrete structures without any external power. "Our ultimate goal was to develop materials that made the lives of people better and did not need any extra energy to save the planet. And we expect that the findings from this study can be used to expand the applicability of CBC as an all-in-one energy material for net-zero energy structures," concludes Lee.