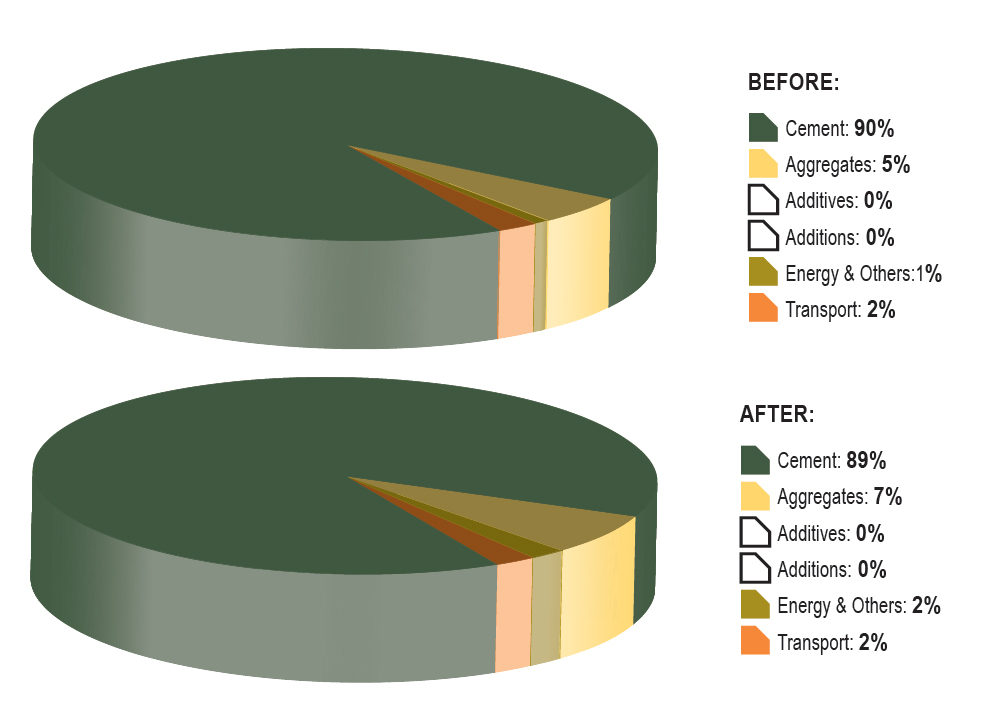
All major companies in the quarrying industry have drawn up plans to reduce emissions and save money. Patrick Smith reports
The subject of embodied carbon and ways of reducing it is of growing interest in today’s construction industry.
There are many ways of tackling the issue and the aggregates industry, like many others, has come up with detailed plans to cut greenhouse gases.
Among incentives are carbon credits, which are similar to certificates that represent a reduction of greenhouse gases in the atmosphere. Projects that prevent the generation of greenhouse gases or remove greenhouse gases from the atmosphere earn these credits. They in turn can then be sold to other businesses and individuals to offset the emissions they generate.
It has been estimated that one carbon credit is the equivalent to a saving of one tonne of carbon dioxide (CO2), and carbon credit projects to help reduce or emit carbon emissions include renewable energy, fuel switching and energy efficiency, something all the major quarries have initiated. It has been estimated this market is now worth over US$176 billion (€143/25 billion) and is growing.
At
“At the end [of the 2007-12 programme] we had achieved our key commitment of reducing net CO2 emissions per tonne of cement produced by 20%,” says Lafarge’s chairman and CEO Bruno Lafont.
India’s Geneva cement pact
Indian cement majors, including
The pact was signed in Geneva, Switzerland, with member companies of the World Business Council (WBC) for Sustainable Development’s
“This will be the first roadmap to focus on one specific industrial sector in a single country,” says the WBC.
The India roadmap is being developed by the WBCSD’s CSI and the International Energy Agency (IEA). The IEA will be bringing in expertise in data analysis and modelling, and roadmap development.
The technical consultancy will be provided by the Confederation of Indian Industry and the National Council for Cement and Building Materials.
Under the pact, a Low Carbon Technology Roadmap for the Indian cement industry will be launched towards the end of this year, and will provide a possible transition path for the cement industry to reduce its direct emissions by 18% by 2050.
“While public policy responses are critical in addressing climate change, the private sector also plays a leading role in providing innovative business solutions. We view the roadmap project as an initiative to share best practices in sustainability,” says Ramesh Ramanathan, manager, (manufacturing, agri business and services),
As a global producer of cement, aggregates, such as crushed stone, sand and gravel, and ready-mix concrete, Holcim says it recognises the need to improve sustainable construction through innovative processes, thereby reducing CO2 emissions and energy consumption.
The programme outlines 34 new ambitions to be achieved by 2020 with nine major ambitions, which include reducing by 33% Lafarge’s CO2 emissions per tonne of cement compared to 1990 levels; using 50% of non-fossil fuels in its cement plants (including 30% biomass) and having 20% (15 million tonnes/year) of its concrete containing reused and recycled materials.
Air emission targets per tonne of clinker (compared to 2010 levels) include 50% reduction in dust emissions with no kilns emitting more than 50mg/Nm³; 25% reduction in NOx emissions and a 30% reduction in SO2.
To mark its century,
“There is enormous potential in this area, and I am convinced that future generations will be able to construct buildings in a much more environmentally conscious way thanks to innovative methods and processes. We hope that this new professorship will be heavily involved in finding and disseminating solutions for optimised resource usage that can be implemented quickly,” says Bernard Fontana, CEO of Holcim.
Meanwhile,
Cemex says the calculator maps out the embodied carbon step-by-step through the supply chain from the manufacture of the raw materials to the delivery of the end product on site, with bespoke reports quickly generated for customers. It has been used on some 40 projects from single loads to large complex contracts, and Cemex says that on a power station contract it was possible to cut over 25tonnes of CO2 using the tool.
The tool has data on the embodied CO2 of the raw materials and all Cemex plants and quarries including gas, water, fuel and electricity. The carbon emissions from transporting the material, whether by road, rail or water, are also an important factor that is included in the calculation.
Having calculated the embodied carbon in a certain type of concrete, the tool can also substitute alternative mixes, for example using CEM II instead of CEMI, Portland Cement and alternative modes of transport, for example, or using rail for part of the journey instead of road to reduce the total CO2 emissions.
“The carbon agenda is increasingly in the minds of clients, contractors and legislators. The new Carbon Footprint Calculator can offer our customers a more detailed solution of how to cut carbon but still use a high specification material,” says Andy Spencer, Cemex UK sustainability director.
The company says the calculator provides customers with a complete ‘cradle-to-gate’ carbon quotation, meaning the footprint includes CO2 emitted from extracting, processing, manufacturing and transporting the product and the materials used to make it.
According to Tarmac it will help customers to manage the carbon footprints of their projects and provide supply chain partners with complete transparency about the embodied carbon of the products they use.
“Reducing and managing the carbon footprint of our products and operations is a key focus for Tarmac, and we are committed to supporting our customers in doing the same. Providing a transparent and comprehensive carbon calculation helps our clients to cut carbon and deliver more sustainable projects,” says Dr Martyn Kenny, director of sustainability at Tarmac.
“It is important to consider the carbon footprint across the whole life of a project, and the construction materials used make up a part of this. Our new calculator provides comprehensive carbon data across a complete product range and a nationwide network of sites.
“There is a rapidly increasing demand for more information on carbon and increased levels of environmental reporting, so it is vital that we can provide accurate information on the carbon footprint of materials in the supply chain. Our Carbon Footprint Calculator provides this level of transparency, so customers can deliver on their goals and gain a competitive advantage.”
The calculator is part of Tarmac’s long-term sustainability programme. Recent work has included the roll-out of energy and carbon roadmaps and energy-saving assessment tools at all sites, a major waste-derived fuels programme and the introduction of SMART metering technology at each site.
The company also claims it was the first in the quarrying and aggregates industry to trial hydrogen powered-vehicles as part of a research project to compare their viability and performance against petrol and electric vehicles.
Working with energy and storage clean fuel company ITM, Tarmac has been carrying out Hydrogen On Site Trials (HOST) using the company’s transportable hydrogen refuelling station (HFuel) at a UK site.
Lime without the grime
Researchers at George Washington University have invented a solar-powered process that makes lime from limestone without emitting any carbon dioxide.
The process has been demonstrated in a proof-of-concept device at the university in Washington DC, US, and has been presented in a paper, STEP Cement: Solar Thermal?Electrochemical Production of CaO Without CO2 Emission.
The researchers estimate that the process could cost less than the conventional one, and claim it could eliminate a major global source of carbon dioxide emissions.
Lime is used to make cement, purify iron, treat soil, and produce products including glass, paper and sugar. It is claimed that cement production alone emits 5-6% of total man-made greenhouse gases, and most of that comes from producing lime.
Rather than simply heating up limestone until it releases carbon dioxide (as in the conventional method) the process uses a combination of heat and electrolysis, which produces lime, oxygen and either carbon or carbon monoxide, depending on the temperatures used.
The researchers built a device that includes three Fresnel lenses for concentrating sunlight. (Fresnel is a type of lens originally developed by French physicist Augustin-Jean Fresnel for lighthouses). Two of those heat a mixture of lithium carbonate and limestone (calcium carbonate). The third focuses light on a high-efficiency solar cell, which provides the electricity needed to electrolyse the carbonate mixture.
High temperatures reduce the amount of electricity needed and cause the lime to precipitate out of the mixture, making it easy to separate.The researchers say the device works only when it is sunny, and intermittent operation is not ideal for an industrial process. However, they propose using molten salt to store heat, a system used in some solar thermal power plants. That would allow the process to run day and night.
Carbon Trust award for Lafarge
Lafarge has achieved recertification of the
First certified in 2010, Lafarge was able to show further positive steps on cutting carbon in the two years since.
Energy-saving measures have included using ducting to redirect heat generated from compressors to warm up workshops; installing timers on office heaters; installing individual switches on lighting; implementing ‘soft starts’ on crushers and conveyors; establishing more vigorous maintenance and repair programmes to optimise efficiency of equipment, and, at Dowlow Quarry (County Derbyshire, England), replacing the bi-monthly grass-cutting routine with sheep grazing.
“Only a third of companies regain the Standard so we are absolutely delighted to be among those top organisations making a real commitment to cutting carbon emissions and acting on climate change,” says Helen Atkins, CRC and energy performance adviser.