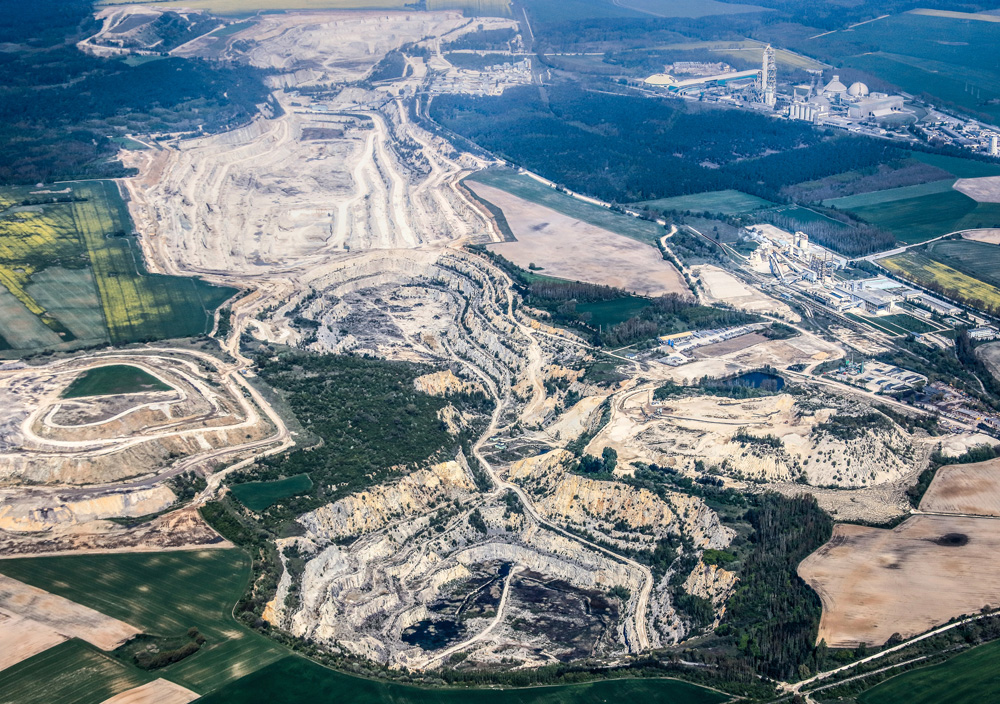
Stretching over nearly seven-and-a-half kilometres and with an annual limestone aggregates production rate of 7.5-8 million tonnes, plus more than 1.5 million tonnes/year of overburden processing, Kujawy is Poland’s largest quarry.
The Lafarge Poland-owned and -operated site near the small industrial city of Inowrocław in north-central Poland is the only limestone quarry in a region dominated by agricultural industry. Quarrying on the vast site dates back to the 1860s. Cement production began onsite in 1969, with Lafarge Poland acquiring Kujawy Quarry (Kujawy) in 1995. The quarry’s management is currently in regular discussions with local community leaders about extending its quarrying production at the north end of the site, which would enable them to tap into more of the quarry’s 1.2 billion tonnes of mineral reserves. Lafarge Poland’s current operating licence allows it to quarry at Kujawy until at least 2054.
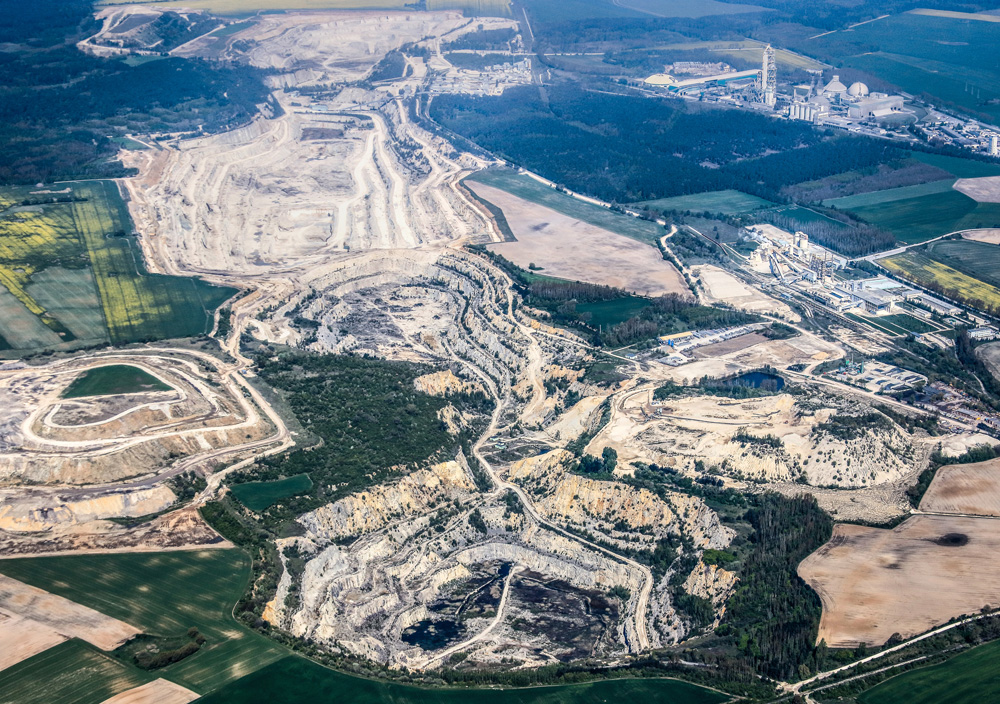
Kujawy’s limestone aggregates products are used in cement and road-based construction projects. They are also used to make soda lime, lime fillers and fertilisers, the latter for farming customers and a growing area of business. The site has four open pits – Wapienno East, Wapienno West, Bielawy West, Bielawy East, two overburden dumps – Wapienno and Bielawy – and four crushing and screening plant lines, operated from an ABB software-equipped control room. One plant line produces aggregates of various sizes for road construction and cement making, others produce road sub-base product, grit, and recycled aggregates material. Magic Mountain, the recycled aggregates plant line, is generally idle over two or three winter months. Quarry-face blasting takes place three times daily – with silo- and stockpile-loading work carried out seven days a week.
Major Polish infrastructure projects using Kujawy limestone aggregates products of various sizes include the S5 Expressway linking Ostróda, Grudziądz and Bydgoszcz in northern Poland with Poznań and Wrocław in the west of the country, and the 130km-long S1 Expressway currently under construction in western Poland.
Playing a key role in ensuring Kujawy’s huge annual production output is a comprehensive Caterpillar machine fleet consisting of two Cat 990 and two Cat 982 wheeled loaders, one Cat 988K wheeled loader, seven Cat 775G rigid dump trucks, an M 320 hydraulic breaker attachment for crawler excavators and a Cat Certified Rebuild 772 rigid dump truck, reconfigured as a giant dust suppression/water sprinkler truck for Kujawy’s site haul roads. Kujawy management is also in discussion with Cat about purchasing a 988K XE (hybrid/dual power) wheeled loader.
The large Kujawy fleet’s performance and health has been monitored for the past three years by a Cat Job Site Solutions (Cat JSS) program devised by Lukasz Kuczer, Caterpillar Fleet Manager Job Site Solutions – Europe, Asia & Middle East; Jaroslaw Wojtanowski, Quarry & Aggregate market manager at Cat Poland dealer Bergerat Monnoyeur (BMPL); and Sylwester Skora, HME fleet performance manager for Lafarge Aggregates (Poland). Key performance indicators (KPIs) covered by the Kujawy Cat JSS program, implemented via the use of Cat VisionLink web-based machine fleet monitoring technology, include individual machine productivity and efficiency measuring, looking at, among other things, machine production volumes, operator capability, machine idleness and fuel consumption. Fleet operation and maintenance planning and Cat SOS (scheduled oil sampling) are other important elements of the bespoke program.
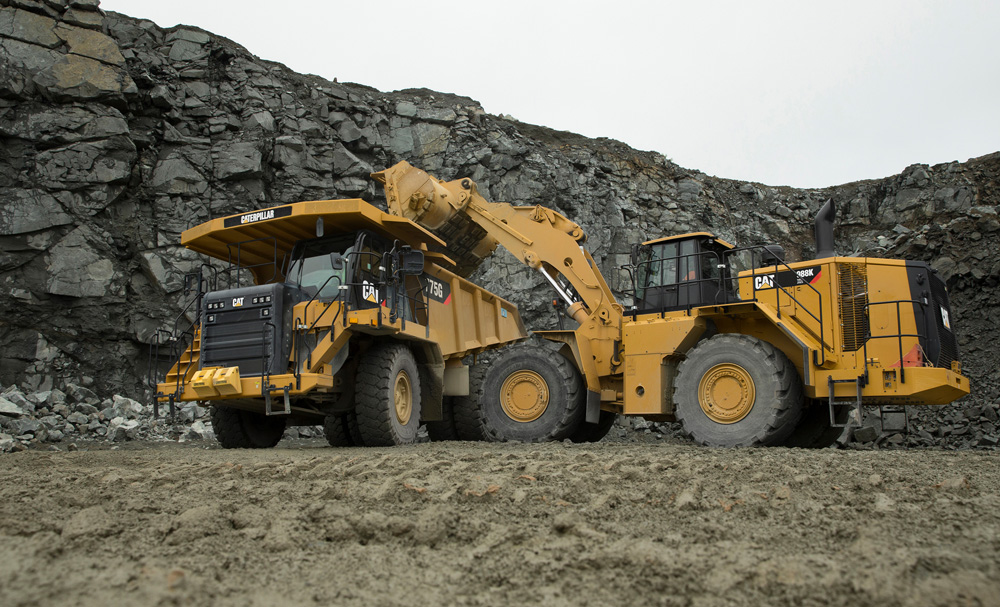
The Cat JSS program is also being followed at five other Lafarge Poland quarries, with a total of 25 Cat machines covered across the company’s six sites.
“Lafarge [Kujawy] needs to earn money from their machines and expects us to help keep their machines running,” stresses Kuczer. “Every month I am sending a Cat JSS fleet summary report to Sylwester and we arrange a call if there are things he wishes to discuss. I also every week have an internal call with BMPL’s [machine] service department where we discuss the fleet’s performance, partly via machine technical codes, and scheduled maintenance times during upcoming weeks.
“Then every quarter at a different Lafarge Poland quarry we have a meeting with Sylwester, other members of the Lafarge Poland management team and BMPL where we present the results of the different Lafarge Poland Cat JSS fleet management programs over the last quarter. We cover how did the machines perform and their utilisation, including fuel consumption. We also look at health and safety concerning operator driving events and how best to tackle them. Lafarge Poland, BMPL and Caterpillar treat health and safety as a high priority. At the end of every meeting we draw up an action plan. All this helps Lafarge Poland keep their machines running and optimise their utilisation. They are a very demanding customer, but we like that.”
“Caterpillar is supporting us with good management of our equipment,” says Sylwester Skora. “They also help us to work very closely with our equipment operators, with a Cat operator training day taking place at the quarry every year. We always see operator efficiency improvements after these days.
“Through Cat Job Site Solutions our equipment fleet is definitely achieving higher productivity and fuel consumption is less. We are also seeing less machine downtime due to our ability to be pro-active on maintenance.”
Skora says Kujawy has been purchasing Caterpillar equipment for many years, with the eldest loading model at the quarry around 15 years old.
“We like to have long-term relationships with our equipment suppliers. Caterpillar models compare well against similar premium equipment manufacturers on price, fuel consumption, maintenance cost and productivity. For example, we choose to run Cat 60-tonne class rigid dump trucks [775G] because of these qualities.”
Asked by Aggregates Business whether Kujawy’s Caterpillar equipment fleet could be improved in any way, Skora says that he is working with Wojtanowski of Bergerat Monnoyeur to address a concern expressed by some of Kujawy’s loading-machine operators who perceive the fitted four-point cabin seatbelts to be uncomfortable.
Kujawy director Hubert Włodarski heads up the quarry’s management team with the whole site operated by 127 Lafarge Poland staff, plus more than 100 contractor employees involved in onsite material loading and hauling.
“Luckily, there are no other sites around us producing limestone aggregates,” says Włodarski. “Since 2018, we have reopened quarrying activities in what were two non-active pits - Bielawy West and Bielawy East. The 8 million tonnes of aggregates we produced in 2018 was the quarry’s record production year. Last year we produced 7.6 million tonnes and we expect to produce a bit more than that in 2020.”