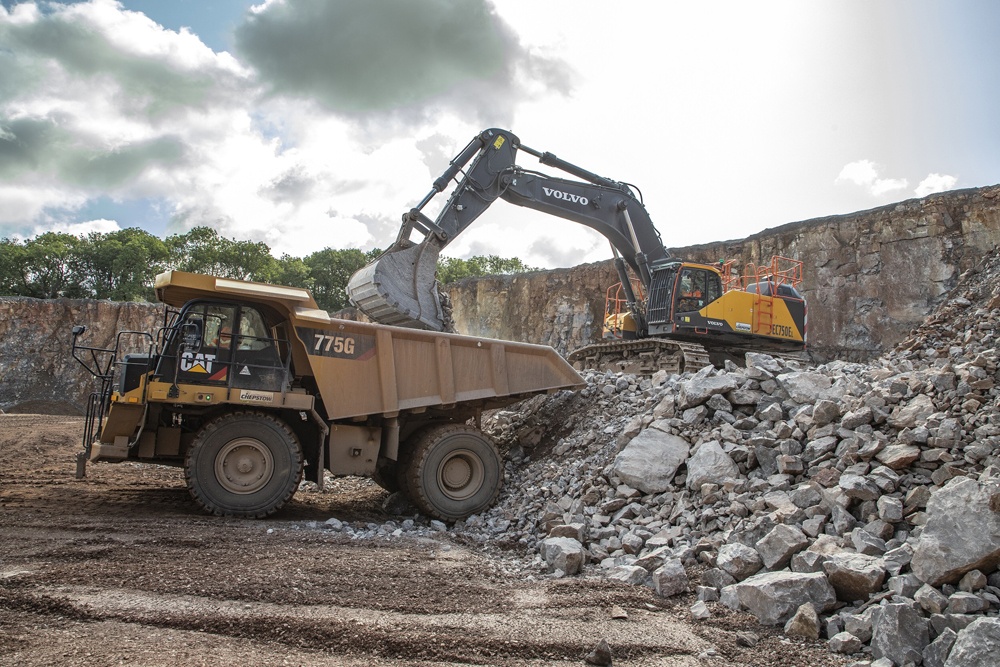
2020 will be remembered as the year that Covid-19 turned the world upside down. The unprecedented nature of the pandemic has undoubtedly disrupted businesses across the globe, including our sector.
With no recognised standard or ‘one size fits all’ approach to how businesses can efficiently adapt to comply with a Covid-19 world safely, we’re all working hard to navigate our way through it.
Of course, the quarrying and aggregates sector has experienced its specific challenges. Many businesses operating in this space can link their success to the construction industry. And with construction sites temporarily shutting down due to changing government guidelines, staffing issues and a decline in workload, there’s an obvious connection to the downturn our sector is facing.
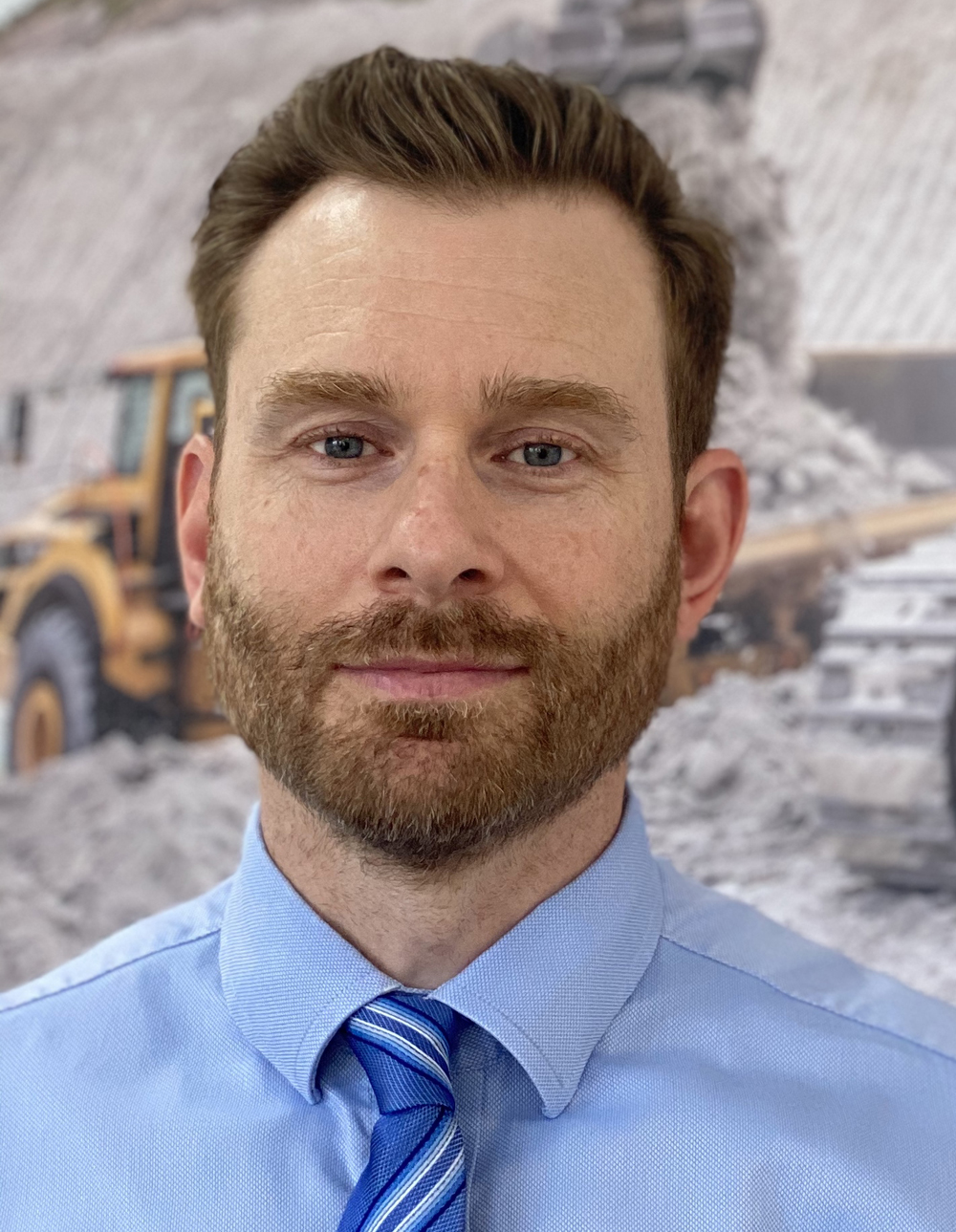
Thankfully, construction and quarrying has always been a cyclical business, and there tend to be seasonal trends throughout the year, every year. While it’s inevitable that the last few months may result in a much lower trough than normal, HS2 and other stimulus packages that are due to kick-off in the near future could potentially reverse the industry’s declining output to pre-Covid levels.
Indeed, for CPI, some sites have barely skipped a beat over the last few months, depending on the locality or whether they were considered core or essential. In particular, our work in power stations and steelworks has continued as normal, albeit with more protocols in place.
In our case, years of heavy investment into health and safety measures has helped us to adapt more quickly than other businesses to the crisis – and our core ethos of striving a zero-risk environment for our employees and stakeholders has helped us to remain buoyant throughout this challenging time. If anything, the pandemic is a prime example of why health and safety should always be high on the agenda for decision-makers in quarrying and aggregates – or for any company in any sector – so that we can protect ourselves from the unexpected.
In the last few years alone, CPI has introduced washable seat covers into its vehicles, implemented the regular wiping down of cabs, and we’ve also safeguarded our employees by introducing HEPA filters, which are commonly found on airplanes, into our fleet as standard. These have been found to provide extra air filtration for our operators, protecting them from dust, and recently, Covid-19.
We’re also one of the only companies in the UK and Europe to introduce haul assist technology across multiple sites. The live truck GPS positioning, granular data for each day allows us to understand who’s taking breaks with other and conforming to site protocols along with ensuring drivers are using the same vehicles each day etc. This software essentially acts as our own track and trace software, enabling us to have improved safety for all our employees at such a critical and concerning time.
Clearly, senior management teams need to ask themselves some searching questions to continue to safely operate sites at this time. Sometimes, this means rewriting the rule book. In our case, we’ve introduced new safety measures including adopting new cleaning protocols, implementing staggered shifts, maintaining operator separation and opening welfare units on-site. We’re also seriously considering the weather, and how we’ll conduct daily briefings at a social distance once we enter the winter months.
Ironically, our mantra “we all stand together to stay safe together” has been fast undermined by Covid-19. Historically, we’d actively encourage our operators to take breaks away from machines, encouraging them to socialise more with one another and not spend days in isolation. We also invested a great deal of time and resources to build teams that work closely with each other and all move towards the same objectives – ensuring that our employees feel comfortable in reporting issues and working together for near misses. However, given that we’re operating in an environment where we need to follow isolation protocols, that now seems like a double-edged sword.
It’s one of many examples where the overwhelming influence of Covid-19 in the workplace has the potential to let other areas within businesses slip and regress – and there’s a risk of overall safety taking a step backwards as companies try to navigate their way through this time.
As a business, we’ve therefore decided not to specifically focus on ‘making things safer’, but instead to ‘change the face of safety’.
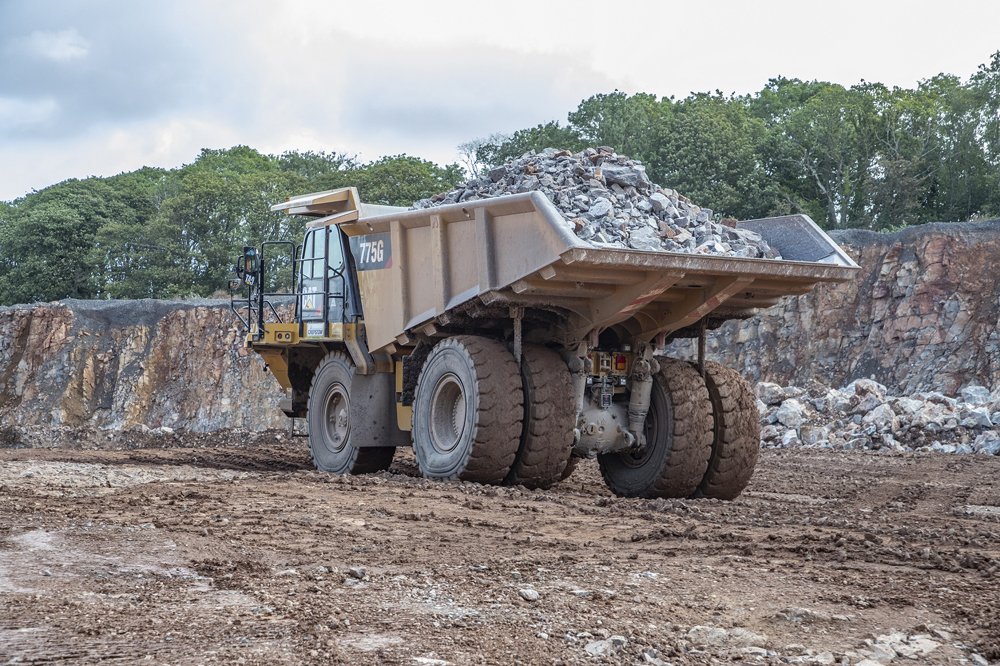
But what does this mean? Put simply, for any business to succeed within the current climate and highly competitive environment, they must maintain focus on their key drivers and simply incorporate Covid-19 protocols into day-to-day operations. Those focussing purely on implementing Covid-19 measures and rectifying issues that these measures cause will not only begin to lose sight of other health and safety risks – such as dust, vehicle/pedestrian collisions and driver fatigue - but also revenue, profit, and other areas which safeguard the future of the company. Of course, it’s a challenge to adopt this approach towards Covid-19, but it also presents an opportunity to magnify focus on running a successful business in what is set to be a very tough couple of years.
To ensure that a ‘business as usual’ approach to the crisis is sustainable, all of our Covid-19 measures are simple to remember and easy to enforce. We’ve made a conscious effort to cut through the noise, and now hand washing, operator isolation and even quarantine are as commonplace across the business as hi-vis jackets, steel toe caps and risk assessments. Undoubtedly, these measures will eventually become the norm for our sector, and businesses which can adapt to them the quickest can maintain their focus on the actual task at hand.
One particular topic of conversation that continues to circle above those working in the sector is that of personal protective equipment (PPE). It’s a conversation that has intensified during the pandemic, and has also hit the headlines due to shortages across the NHS. There’s no doubt that businesses should have PPE in place for employees where appropriate. However, PPE is the lowest form of control, and if used alone won’t solve the issue. There are varying ways to reduce the risk of spreading the virus. For instance, encouraging remote working or isolation, restricting interaction between employees, providing additional welfare services and enforcing on-site social distancing. PPE should work in tandem with these kinds of initiatives and underpins the other necessary measures that we’re putting in place.
Of course, we know that complacency around safety can happen, so to really cement best practice in the workplace during these challenge times, we’ve launched a behavioural safety programme. This further intertwines the mind-set and approach for both safe working methods and Covid-19. It pushes us to create interdependency within our workforce through cultural and behavioural changes, ensuring that everyone is looking out for one another.
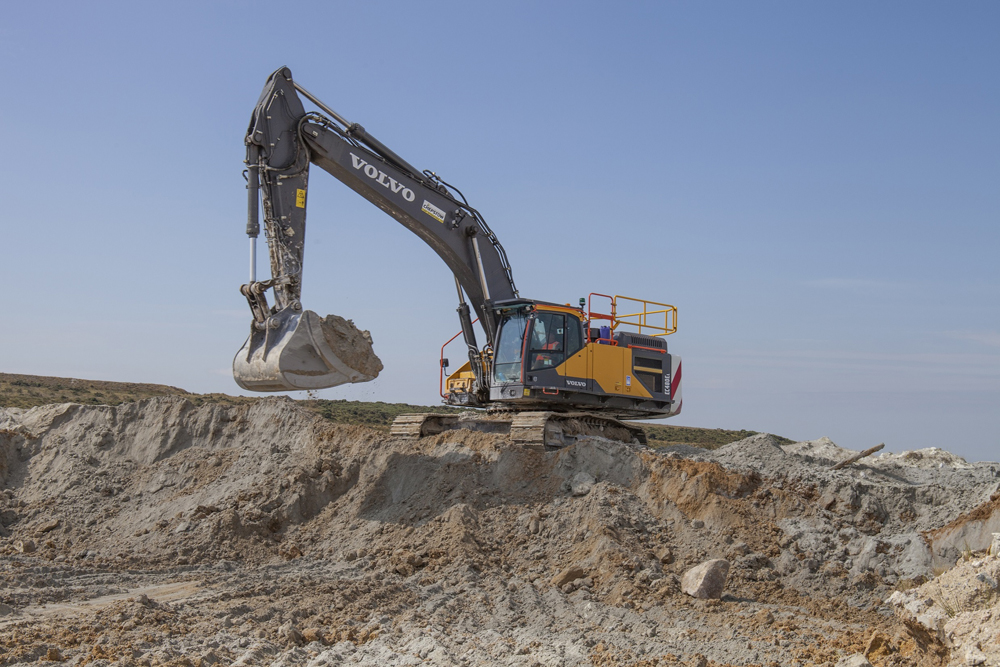
The future of the quarrying and aggregates sector may currently appear pretty uncertain, but companies can take steps to mitigate the situation. Businesses must find a way to quickly incorporate Covid-19, government guidelines and the series of new protocols into their day-to-day operations. As a sector, we can’t fight the pandemic, but we can learn to live and work alongside it. If businesses can find a way to do both of these things successfully, it could very well be the difference between navigating a way through the pandemic, and not being engulfed by it.
About Chepstow Plant International
Chepstow Plant International is a privately-owned mineral and aggregates contractor, with over 50 years’ experience within the mineral products sector, resulting in unparalleled knowledge of quarrying, earthworks, material handling, managed fleet solutions and used plant equipment. Chepstow Plant International prides itself on being able to provide sustainable and practical solutions for resource extraction, whilst maintaining health and safety to the highest standards. The company’s award-winning initiatives in health and safety ensure that it is continuously at the forefront of the company’s approach as it strives to construct a “zero-risk” environment.