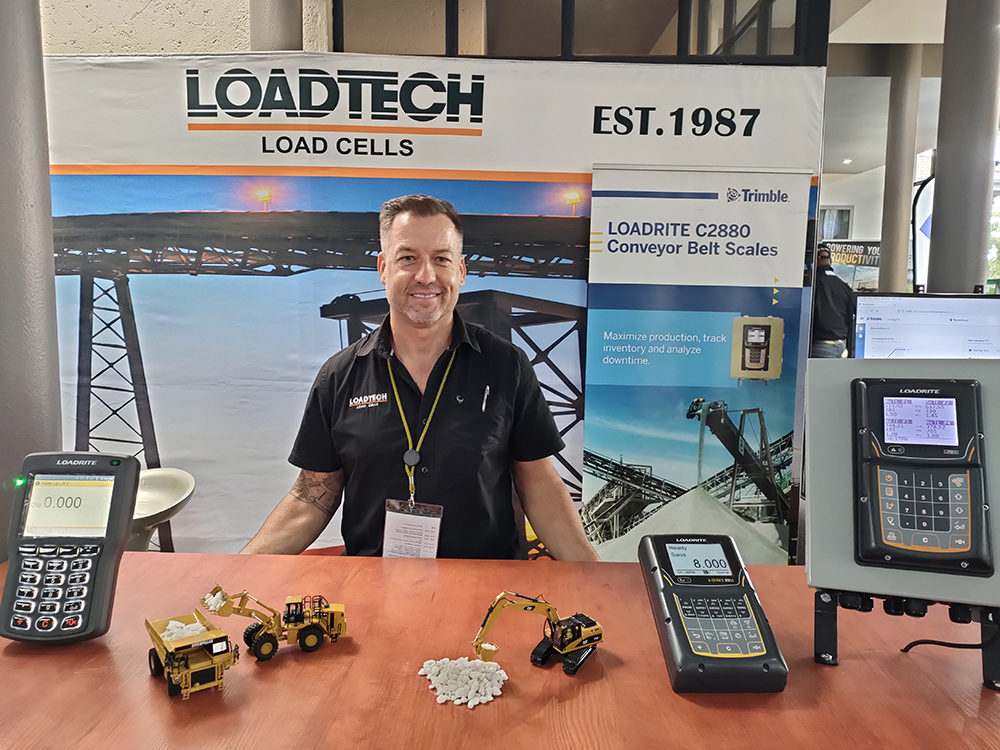
In an environment where emphasis is fixed firmly on productivity at lower cost of operation, quarry managers are finding value in fleet-wide payload management systems that give them the ‘pulse’ of their loadout processes and the entire operation at large.
Modern load-weighing systems, says Webster, provide a networked, holistic view of operations, enabling quarry managers and operators to respond proactively with each load. Increased productivity goes beyond faster, more accurate loading; it now directly impacts the bottom line in each phase and across the entire operation.
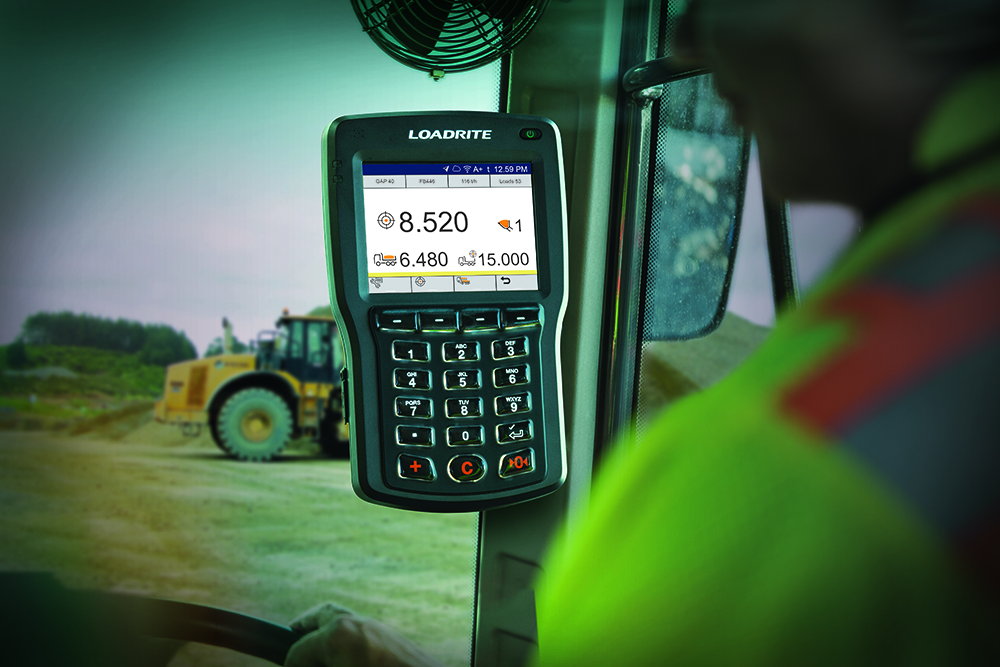
Based on this understanding, aggregates producers are increasingly investing in these technologies to enable them to make informed decisions. Consequently, Loadtech has in recent years observed increased uptake of its Loadrite weighing systems in Africa. The company’s growth in the past three years, says Webster, is a clear indication that the market is fast maturing.
“We have recorded a substantial 15% business growth in the past three years,” confirms Webster. “COVID-19 has taken some of the competitors out of business and this has contributed to about 5% of our growth in the past two years. The remaining 10% is purely new business driven by the increased uptake of these solutions in the local market.”
Webster says new load-weighing systems, such as the Loadrite L3180 Smartscale provide much more than accurate payload weight. They add value with features that improve site safety, track stockpile inventory, empower operators with performance feedback, integrate with truck scales, and more.
Launched locally some three years ago, the Loadrite L3180 Smartscale is Loadtech’s best-selling solution in sub-Saharan Africa at the moment, with several big quarrying groups among the early adopters, says Webster.
“We sold about 90 units in the first year and about 200 the second year. There is an apparent mindset shift in the industry. Quarry owners are now aware that they can actively reduce their total cost of ownership by using load-weighing systems’ monitoring and alert features to set benchmarks and measure productivity,” he says.
By tracking the amount of material moved per hour to measure productivity and set benchmarks using load-weighing systems, operators can identify underperforming machines and make appropriate adjustments to ensure all assets on site are working at their optimum efficiency.
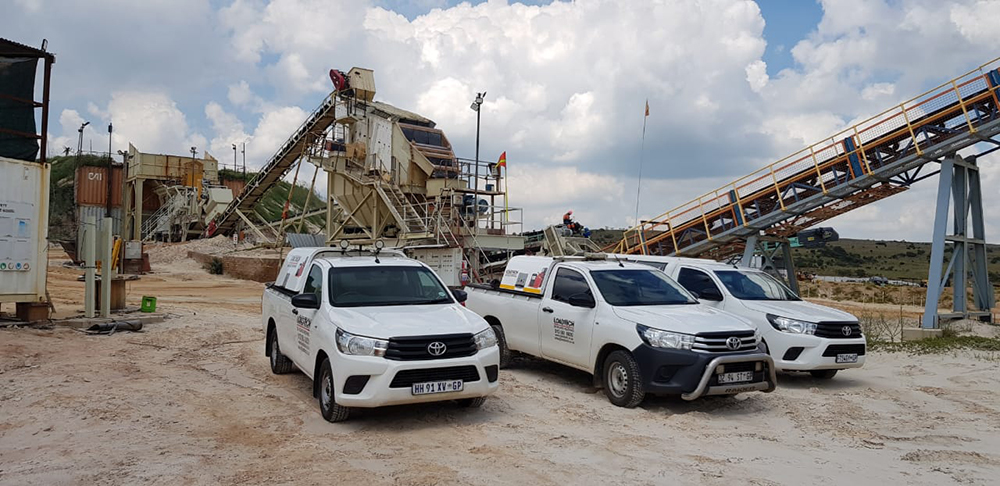
An on-board weighing system such as the Loadrite L3180 SmartScale can be used to calculate the weight of material in an excavator’s or loader’s bucket, relay this information to the operator and record the weight for later use. Being able to track the amount of material moved per hour can then be used internally as part of an overall business analysis to measure productivity and set benchmarks.
“Once you know your benchmark productivity rates, it’s also easy to identify equipment that is underperforming, which sets off a trigger for an investigation into the underlying causes. These causes can vary widely, from operator error to equipment failure.”
Once productivity benchmarks are set, fleet managers can customise their systems to capture a wide range of other data such as cycle times, which can then be used to identify process bottlenecks and inefficiencies. By resolving these issues, quarry managers can improve productivity and reduce operating costs.
“This Loadrite system can also measure the cycle times between each loading event, which can show how efficiently material is being moved. Shorter cycle times generally point to a more efficient and therefore more profitable operation,” says Webster.
The system also actively helps reduce fuel usage. By using an accurate on-board weighing system, operators can ensure trucks are filled correctly the first time, with no productivity lost due to underloading or overloading.
“By loading trucks correctly from the outset, unnecessary truck movement is reduced as there is no need to turn around for either a refill or a removal of material once the trucks get to the weighbridge,” he says.
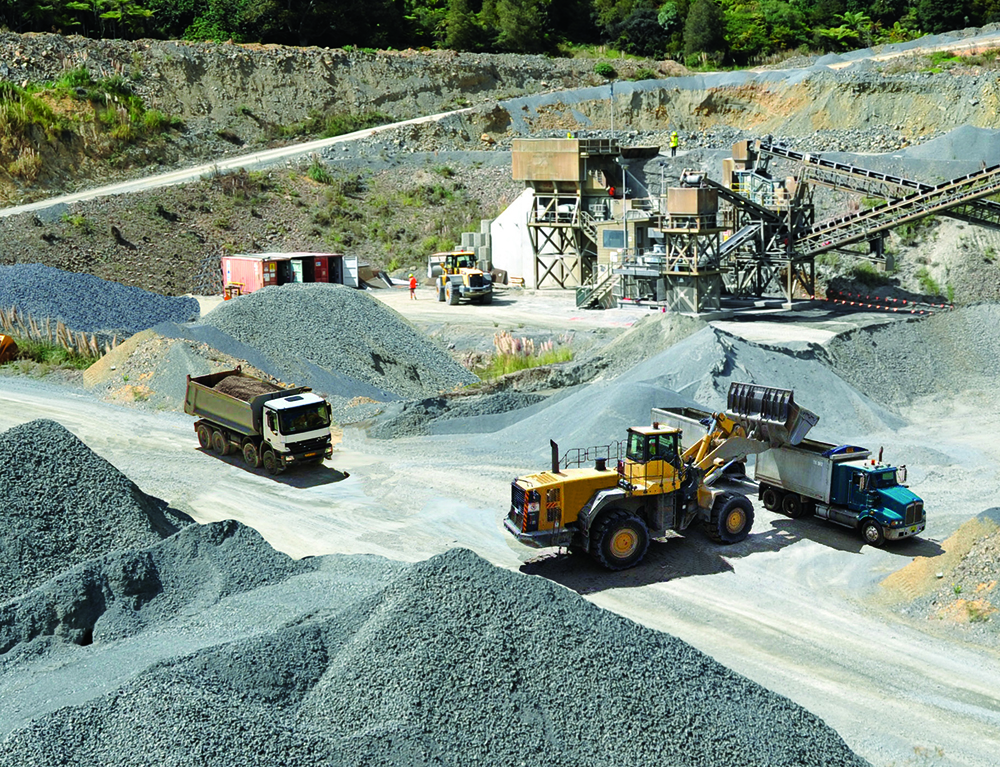
A major talking point on the Loadrite L3180 is the use of angle sensors instead of traditional rotary triggers. This maximises weighing accuracy, even in tough conditions. For example, the solution is able to adjust for rough terrain, technique and movement so new and skilled operators can load with greater accuracy, precision and speed.
The Loadrite L3180 SmartScale uses weighing intelligence and solid-state sensors for more accurate, precise and faster loading. It also connects machines and devices for the collection and syncing of data via the built-in WiFi to the InsightHQ reporting portal. When using Trimble’s cloud-based InsightHQ quarry-reporting portal, personnel can gain access to site production and operator key performance indicators (KPIs) on desktop or mobile devices.
“The L3180 now offers in-cab KPIs, including tonne/hour, tonnes and truck count to enable operators to monitor performance and achieve daily targets,” explains Webster. “Data is presented in dashboard or graphical formats, including a new loadout-performance heatmap, powered by built-in GPS. The system caches data locally and then syncs it with InsightHQ.”
Amid this growing uptake of load- weighing systems in the sub-Saharan Africa market, Loadtech has just launched the Loadrite 360 payload management system in this part of the world. The company is currently trialling the first units at one of the leading aggregates providers’ quarries in South Africa.
The Loadrite 360 – a loadout-automation and -reporting system for quarry loadout activities – consists of a wheeled loader onboard scale, an automated communications connection and a performance-reporting tool. Jobs are entered in the office and selected in the loader, reducing data entry, eliminating mistakes and improving customer satisfaction.
The technology is designed to transform the way in which quarries have always conducted their loadout processes. Traditionally, operations have relied on weighbridges alone. These are known to be prone to product errors and weight challenges.
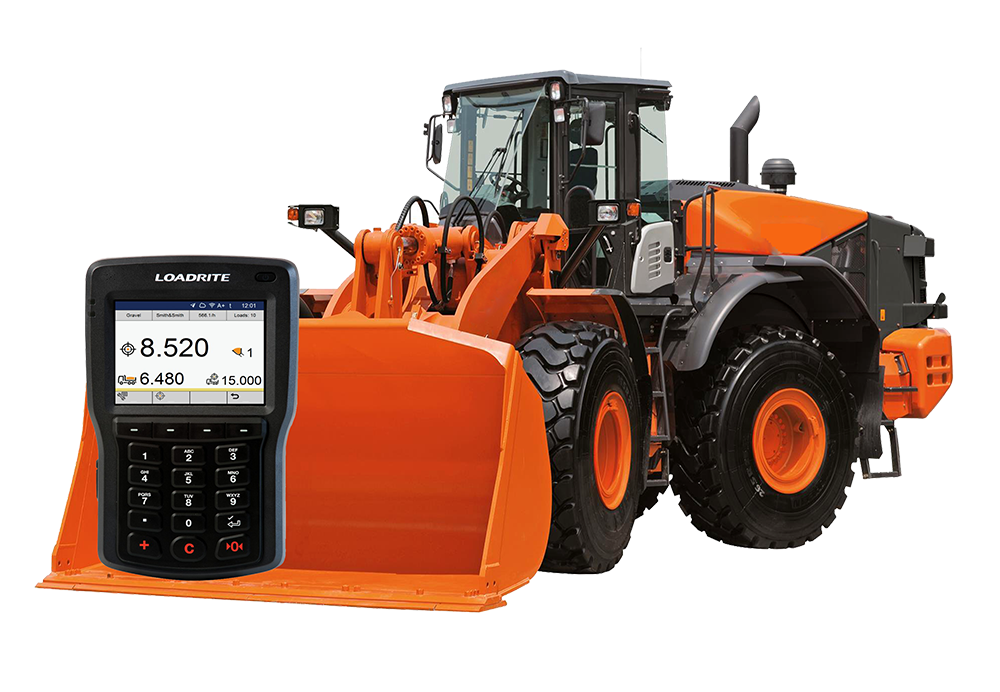
With the Loadrite 360, aggregates producers can turn their workflows around – literally. Instead of having a weighbridge at the exit, it could be moved to the entrance area, where information about the truck – including the registration, tonnage and product required – is captured and relayed to the loader. As soon as the truck drives in, the loader operator already knows the quantity and type of material to be loaded. This reduces loading, waiting and idle times.
“The Loadrite 360 can holistically improve loadout operation through performance metric tracking, job data automation and real-time 360° job visibility. It connects the loader and the weighbridge so as to provide data-sharing of loadout jobs, resulting in greater efficiency, improved visibility and higher product sales,” says Webster.
The two-way automated communication shows jobs requested at the weighbridge as a job list on the scale inside the loader cab and completed loadout data is fed directly into the weighbridge ticketing system. This reduces double-entry work and data-entry errors for both the operator and the weighbridge attendant. Accurate on-screen job data reduces error-prone verbal communications and allows more time for loading.
With the InsightHQ reporting option, managers can monitor site production and performance anywhere, at any time, on any mobile device or web browser. InsightHQ also allows centralisation of data from excavator and belt scales.
“Although the Loadrite 360 is primarily a tool to improve the accuracy and speed of loadout operations, it can also reveal hidden improvement opportunities. The system enables users to drill into production data to see individual trucks, loaders or even bucket-by-bucket data and identify opportunities to improve,” concludes Webster.