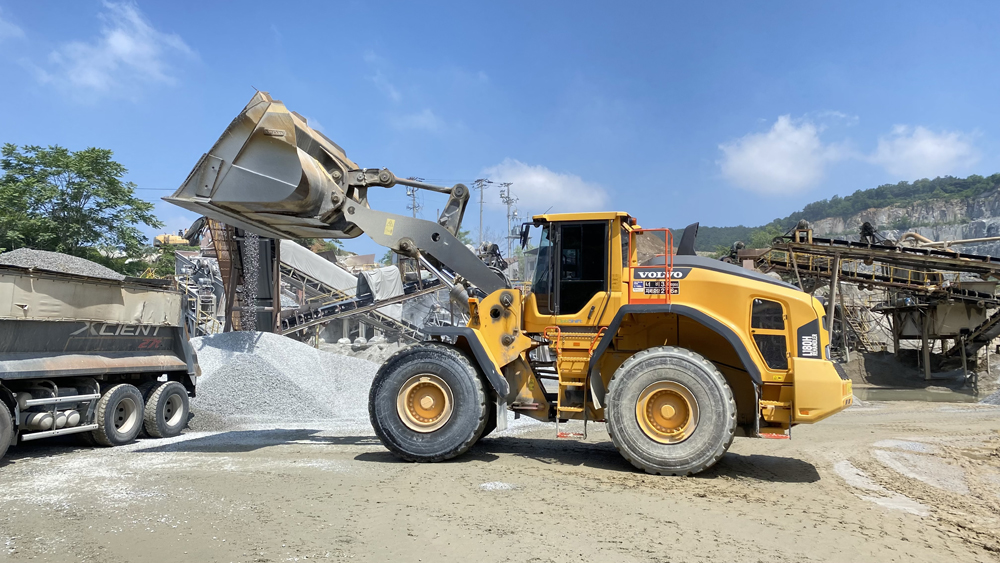
A fleet of wheeled loaders and excavators is helping a Korean aggregates producer cut down on its fuel consumption while keeping pace with the ever-growing aggregates demand. The fleet of Volvo CE equipment – which includes a new EC550E crawler excavator in addition to articulated haulers – has been deployed by Daeil Development, which operates three quarries in Iksan, North Jeolla Province.
Iksan’s location in the fertile plains between the Geumgang and Mangyeonggang rivers has long made it a centre of agricultural and religious significance. Now the city of 300,000 people is undergoing rapid transformation into a national transport, industrial and cultural hub.

Large-scale construction and infrastructure projects are being implemented one after the other, especially around the Saemangum National Industrial Complex, which at 409km2 is the world’s largest reclamation site. Demand for aggregates and building materials is booming and has seen Daeil Development grow along with the city.
Established in 1983, Daeil Development’s three quarries generate up to a million cubic metres of aggregate per year. To meet these production targets, the company requires high uptime from its equipment – a combination of durable design, simple maintenance requirements and reliable aftermarket support. Fuel-efficiency as well as the safety and comfort of operators are also important considerations.
In addition to various large crushers and conveyors, the company employs a fleet of 16 Volvo machines, comprising 11 excavators of various sizes, three L180H wheeled loaders and two A25D articulated haulers. Its most recent acquisition was a Volvo EC550E excavator.
“The impact of introducing a Volvo EC480E excavator and L180H wheeled loaders to our site has been even better than expected and we now achieve much higher fuel efficiency than with the equipment we had before,” said Pyeong-sik Kim, CEO of Daeil Development. “I am also very pleased with the productivity and cost-effectiveness of our Volvo machines.”
He added that, due to the EC550E excavator’s ability to handle several tasks at once, the company expects its cycle times to reduce and its productivity to increase significantly.
Volvo CE says the EC550E excavator’s new IMVT hydraulic control system is perfectly matched to the low-RPM engine, which makes it possible to perform the work of a 60-tonne super excavator with low fuel consumption. Meanwhile, the low centre of gravity and HD counterweight maintain stability on tough terrain. The CDC (comfort driving control) enables the operator to control machine movements with a simple joystick, and a FOG (falling object guard) for protecting the front and top of the cab from falling objects is installed as standard to enhance convenience and stability during operation.
The EC550E is also equipped with Volvo CareTrack telematics to enable real-time machine management at Daeil Development sites. This connectivity supports Daeil Development to leverage data insights for high efficiency, productivity and stable work patterns among its fleet.
In the Czech Republic, a new Doosan DX350LC-7 Stage V-compliant excavator has added increased power and fuel efficiency for working with heavy blocks of granite at the Ruprechtice quarry.
The quarry is one of several northern Bohemia quarries owned and operated by Ligranit, using state-of-the-art equipment like the DX350LC-7 in tough conditions. The new excavator was supplied by Garnea, Doosan’s authorised Czech dealer.
Dating back to 1910, Ruprechtice quarry was owned for many years by the famous stonemason, Josef Lange, and by the Liebig family. It subsequently became the property of the state until 1992, when it was acquired by private company, Ligranit. The quarry specialises in the extraction and sale of much sought-after Czech granites, that architects both at home and abroad regularly specify in their designs and for use by sculptors.
“Over the last 10 years, quarrying has changed in terms of processing granite blocks. Previously, everything was done by hand. Today, it is mainly carried out with the latest machinery and technology,” says Radek Svoboda, production manager at Ligranit.
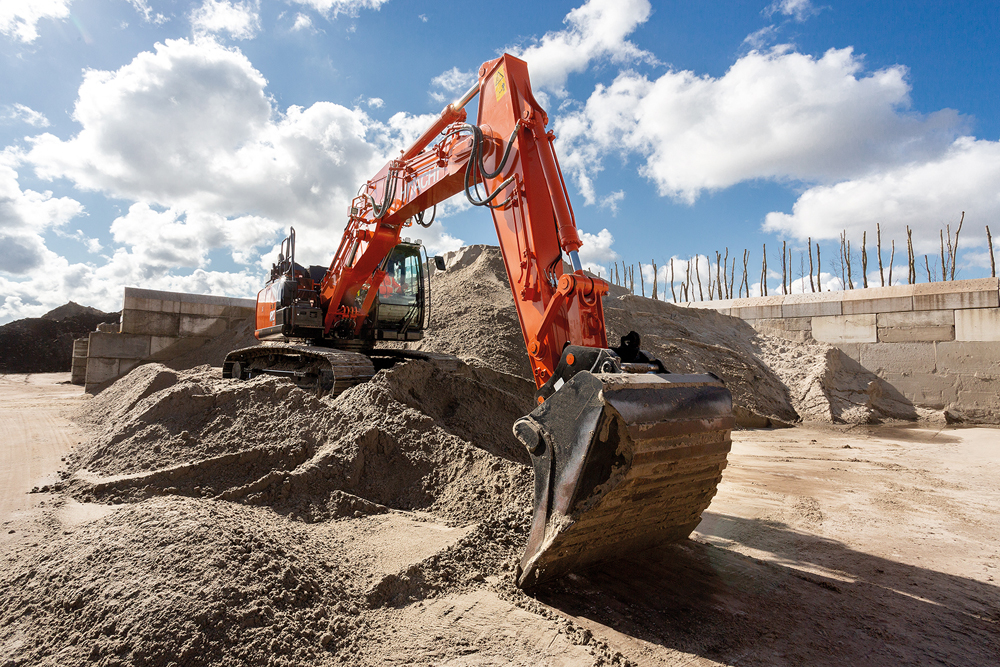
According to Ligranit, the processing of granite blocks requires machines that are both powerful and efficient. It is precisely these requirements that have been met by the new Doosan DX350LC-7 excavator from Garnea. The key selection parameters included an emphasis on exceptional performance, low fuel consumption, operator comfort and, last but not least, environmental friendliness.
“We purchased the new Doosan machine for its power and low fuel consumption. Of course, the length of the warranties and the service from Garnea are also important factors,” explains Svoboda.
As well as exceeding the parameters set by Ligranit, another aspect supporting the purchase of the DX350LC-7 was the excellent service record of a smaller Doosan DX140LC-5 excavator owned by Ligranit. The Stage V compliance of the new DX350LC-7 also met the environmental standards required by Ligranit. But the most important factor was the excellent relationship with Garnea. “We negotiated with the management of Garnea and everything that was promised with the new DX350LC-7 has turned out exactly as they said,” adds Svoboda.
Excavators in the Ruprechtice quarry are brought into play after blasting work has finished, whereby small controlled amounts of explosive are carefully placed to obtain the necessary amount of stone. After blasting, stone blocks weighing from 100kg -to 3 tonnes are selected. The larger pieces of stone are reduced in size using the excavator equipped with a hydraulic breaker. Care is taken to ensure that the material obtained is of the highest quality.
Using an excavator, the blocks are moved and further divided using a splitter. For more precise work, splitting is done manually. Where the potential for material quality is best, entire blocks are transported out of the quarry and worked on with a saw. “These blocks weigh between 5 and 15 tonnes, so the power of the machine is therefore a big plus for us,” adds Svoboda.
Hyundai Construction Equipment (HCE) has launched a new line of A-Series wheeled excavators featuring EU Stage V diesel engines.
The four machines, with operating weights of 14-23 tonnes, feature low-emission Cummins B4.5 and B6.7 S diesel engines with a combined after-treatment system and no requirement for exhaust gas recirculation (EGR). HCE says the excavators offer customers increased productivity with lower emissions.
The machines also feature load-sensing hydraulic systems with load-independent flow sharing for increased controllability.
The revised line-up starts with the HW140A, weighing in at 14,900kg with a monoboom and 15,860kg with a two-piece main boom. This machine shares much of its undercarriage and upper structure with the HW160A, with weights of 17,580kg/18,390kg. A compact radius HW170ACR is offered exclusively with a two-piece boom, at 18,810kg and the range is completed with the HW210A, at 22,270/23,665kg.
The HW140A, HW160A and HW170ACR are powered by a 4.5-litre Cummins B4.5 diesel engine, replacing the larger 6.7-litre engine in the previous generation of machines.
The new compact engine uses a wastegate turbocharger and has a Flex-Module two-can exhaust system, comprising a diesel oxidation catalyst (DOC), diesel particulate filter (DPF) and selective catalytic reduction (SCR).
HCE says there is no requirement for exhaust gas recirculation (EGR), reducing service cost for customers, while the smaller engine is more fuel efficient than its predecessor. Despite the reduction in engine capacity, the new machines benefit from an increased output, with the HW140A, HW160A and HW170ACR now all delivering 129kW (173hp), up from 117kW (156hp) on the previous generation HW140.
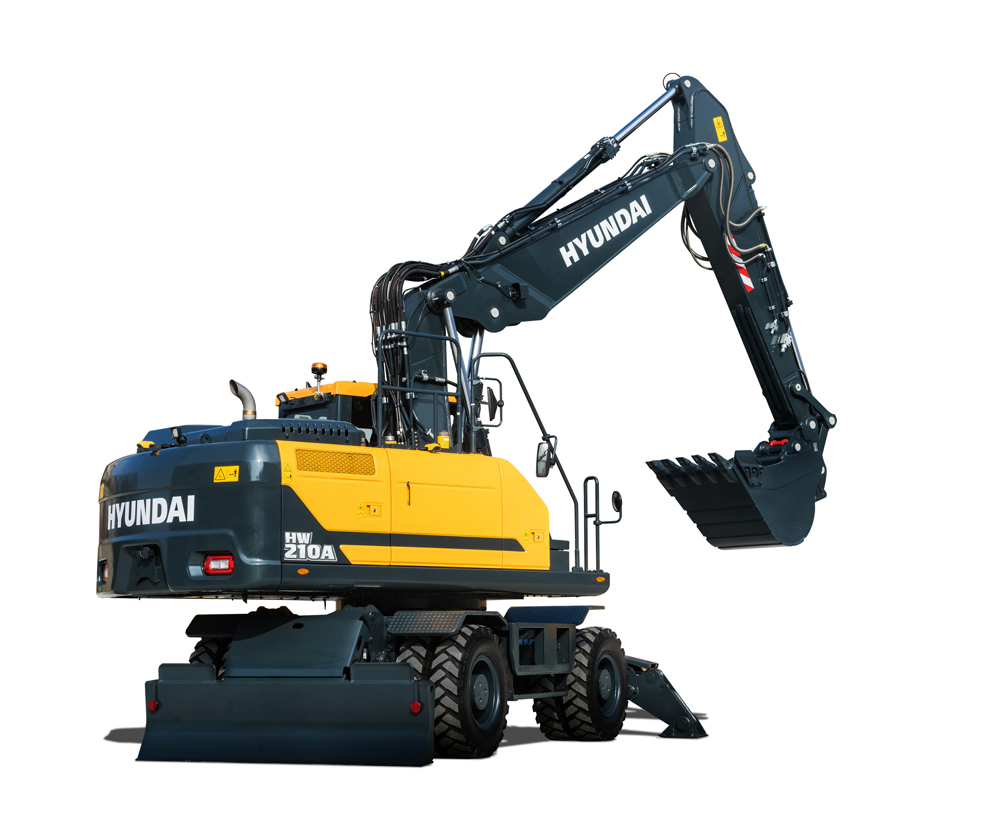
The HW140A and HW160A excavators’ swing centre and lower frame has been moved forwards by 100mm to boost machine stability. In addition, the right-hand side of the upper structure comes forward 150mm, to provide additional space for the fuel tank. The left-hand side moves forward by 230mm to improve visibility from the cab and to make additional space for the engine bay. The rear swing radius on the standard counterweight HW140A and HW160A also moves forwards by 200mm, to cut the rear overhang and makes the machines more manoeuvrable on confined sites, while increasing lifting capacity.
Peter Sebold, product specialist at HCEE, commented on the new excavator range: “The revised boom geometry, in combination with LUDV load-sensing hydraulics, provides Hyundai’s new wheeled excavators with outstanding performance in multi-function operation, smooth controllability and the necessary stability for maximum productivity.”
Japanese manufacturer Kobelco has extended its line-up in the 50-tonne class with the introduction of two new models.
The all-new SK500LC-11 and larger SK530LC-11 benefit from increased speed and performance, improved reliability and maintenance, state-of-the-art ergonomics and design and are Stage V compliant. Weighing in at over 50 tonnes, the SK500LC-11’s engine performance is top of the 50-tonne segment, thanks to the new turbocharged, Stage V-compliant 13-litre Hino engine.
Kobelco says that, for the customer, these improvements in performance mean the SK500LC-11’s cycle time has been shortened by 5.1% (compared to H-mode on the SK500LC-10), fuel consumption has improved by 5.4% (compared to S-mode on the SK500LC-10) and productivity has increased by 6.2% (compared to Eco-mode on the SK500LC-10). The SK500LC-11 is best suited to general construction applications, while the SK530LC-11 is ideal for general construction and quarrying.
“As you’d expect from heavy excavators operating in such harsh environments, lifting capability and stability is of particular importance,” Kobelco states. “The SK500LC-11 has a higher operating weight (50.4 tonnes) when compared with the previous SK500LC-10, leading to increased stability.”
Both the SK500LC-11 and SK530LC-11 benefit from high hydraulic pressure (Heavy Lift) for greater lifting power at close radius, allowing for smooth and steady operation while moving heavy objects. The machines are also said to have excellent lifting performance when compared with competitor machinery, particularly at a working radius of up to 9m over the side. For comparison, the SK530LC-11 has an operating weight of 53 tonnes and benefits from an adjustable undercarriage. Its track gauge can extend to 2,890mm, promoting top-of-the-market stability and superior lifting performance, while when retracted, the overall width of the crawler is just 2,990mm (vs 3,350mm on the SK500LC-11). This decreased width enables better transportability, particularly in mountainous regions where the roads may be narrow.
Both the SK500LC-11 and SK530LC-11 models are available with standard boom and three-arm variations, or as a Mass Excavation model with a short boom and short arm.
Commenting on the launch of the new SK500LC-11 and SK530LC-11 machines, Kobelco product manager Peter Stuijt said: “Years of research, coupled with feedback from our customers, has resulted in the development of a new breed of heavy machines that excel in performance comfort and operability. “First impressions of the SK500LC-11 from our dealer, Comet Loc, in southern France are extremely positive, with operators reporting that the new machine is very fast, accurate and easy to drive.
“They also report that the stability is very good when loading rocks, and the high level of comfort in the new cab is appreciated. We look forward to getting more feedback during demonstrations of the new model at the 2021 Dig Tour in France.”
Hidromek is launching the new HMK 500 LCHD crawler excavator, which has the highest tonnage in its H4 Series. The Turkish manufacturer says it offers superior durability owing to the revisions made in the undercarriage, the strengthening of its heavy-duty structure and its developed technology. The HMK 500 LCHD is designed to provide strong and smooth performance in the most difficult working conditions with its robust and balanced structure.
The 3.2m³ bucket capacity, 6.3m standard boom length, 52-tonne standard machine operating weight and the technological equipment in the HMK 500 LCHD are designed to increase performance and productivity.
Improvements to the HMK 500 LCHD have been made in arm and boom structure, undercarriage, and attachment groups by using more durable materials. Hidromek says these changes offer uninterrupted operation in the fields with the most severe operating conditions such as mining, marble and large construction sites.
The electronic system of H4 Series excavators is designed to protect the engine and hydraulic components to provide fuel saving and superior performance.

In the new series, an automatic stop system through configurable idling and stopping times provides fuel saving by stopping the engine after the machine is on idle.
Hitachi Construction Equipment Europe says owners can maximise uptime with its new Zaxis-7 range of medium excavators. The new ZX160-7 and ZX180-7 Stage V-compliant models are said to offer an enhanced operator experience, with their efficiency and versatility providing operators with opportunities to increase profits and reduce costs.
The manufacturer says that up to 7% less fuel consumption is achieved over previous models thanks to Hitachi’s HIOS IV hydraulic system and improvements made to the travel device.
Operators can also control fuel efficiency and reduce costs by using the new ECO gauge, which is clearly visible on the multifunctional colour LCD 8” monitor. In addition, Hitachi says owners can boost profits by working on a wider range of projects thanks to the excellent versatility of Zaxis-7 excavators.
Both models are available with mono- or two-piece boom. The ZX180-7 is available with a long undercarriage for optimal stability and narrow for easy transportation. The reduced swing radius of the ZX180-7 also makes it suitable for working in confined spaces, while different attachments are quickly changed using the enhanced attachment support system on the monitor.
CASE Construction Equipment dealer Warwick Ward has sold and delivered a modified new 721G wheeled loader to Blackpole Recycling based in Worcestershire, England.
At the customer’s request, Warwick Ward modified the 721G model so that it is designed for purpose with comfort-ride solid tyres that further protect the machine from punctures, as well as extra belly guards, a waste ejector ram guard and a screen guard outside of the cab. The machine is also fitted with a Venturi kit that will protect it when working in dusty environments.
The new G-Series wheeled loaders come with a brand new payload system designed for reliability, time savings and resulting productivity improvements. The system is integrated directly into the loader’s primary display and provides bucket-weight, pass counts, accumulated/running weight, job tracking data and more, for high-volume loading and production environments.