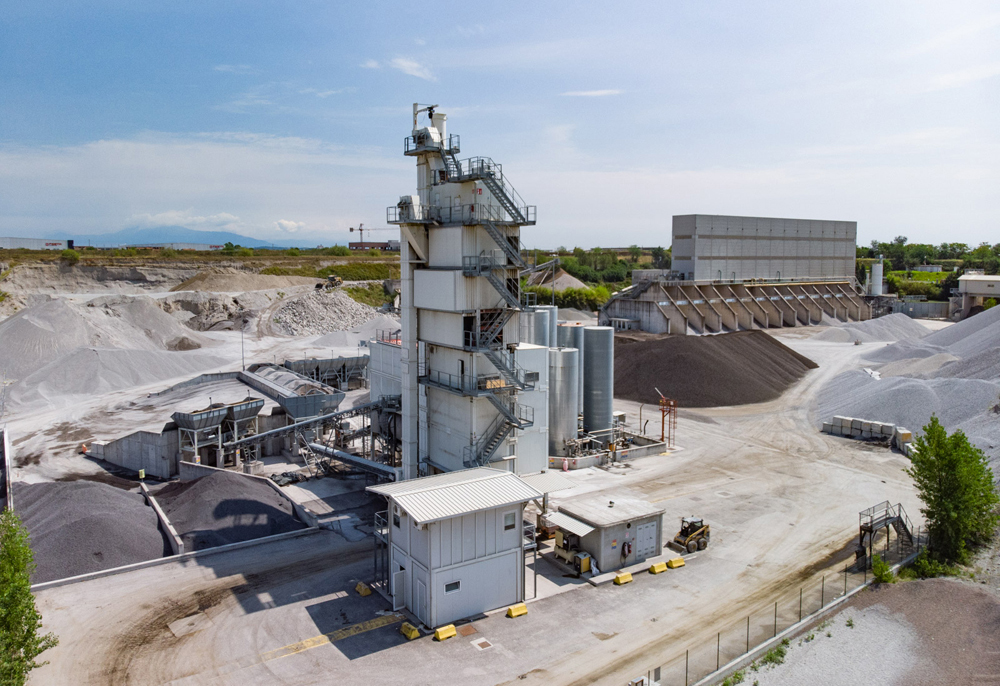
Vezzola, a family-owned and -operated company, was formed in Desenzano del Garda (Lake Garda) at the end of the 1950s and is still headquartered there. The company began extracting and supplying sand and gravel to local construction companies, subsequently expanding its offering with cement and bituminous conglomerates and earthmoving works. The company operates a vertically integrated business model capable of serving ever-changing and growing customer requirements, including using waste construction material to help make a bituminous and cementitious conglomerate. The company headquarters is just one hour away from Milan and Venice, benefitting from the region’s extensive and efficient infrastructure system. The central location provides a strategic hub that can serve the complex and diverse northern Italian infrastructure requirements.
Customer-focused supply chain
Vezzola’s production cycle starts with the excavation of material at its quarries or from other quarries, or procured from suppliers, depending on customers’ specific requirements. The company operates three large quarries and sand pits located at Montichiari, Lonato and Manerba, taking advantage of the large mineral deposits in the immediate vicinity, employing 90 people who are purpose-trained at Vezzola’s training facility. Annual production is 1,200,000 tonnes of natural and recycled aggregate in the region, 400,000 tonnes of asphalt and 250,000m³ of concrete.
Fourteen classes of aggregates are produced at the most modern plant in Montichiari. The facility also makes diverse and non-standard concrete and asphalt mixes that are first tested at the company laboratory and then sampled by specialised external laboratories. One such project involves using excavated tunnel material to remove impurities for use as aggregates for producing concrete and asphalt. If not used as construction aggregate, the quarried material is processed at cement, concrete and asphalt plant operations located at Montichiari, Lonato and Manerba.
Adding to its supply of materials, since the 1990s the company has embraced the circular economy (and adopted Italian and EU environmental legislation and specifications), producing an increasing quantity of material recycled from construction works. These are processed at Vezzola’s plants located at Montichiari and Lonato, with the material coming from both its construction works and third parties. All Vezzola production plants operate according to a ‘Factory Production Control’ (FPC) in compliance with the Italian Central Technical Service of the Higher Council of Public Works procedures.
In effect, this all means that Vezzola provides, through its multifaceted operations and locations, various services that can cover the entire production chain, from the extraction and processing of natural aggregate to research and development for using recycled materials. Materials are used for producing cement and bituminous conglomerates for use on road and civil construction projects, including airports, viaducts, roads and tunnels.
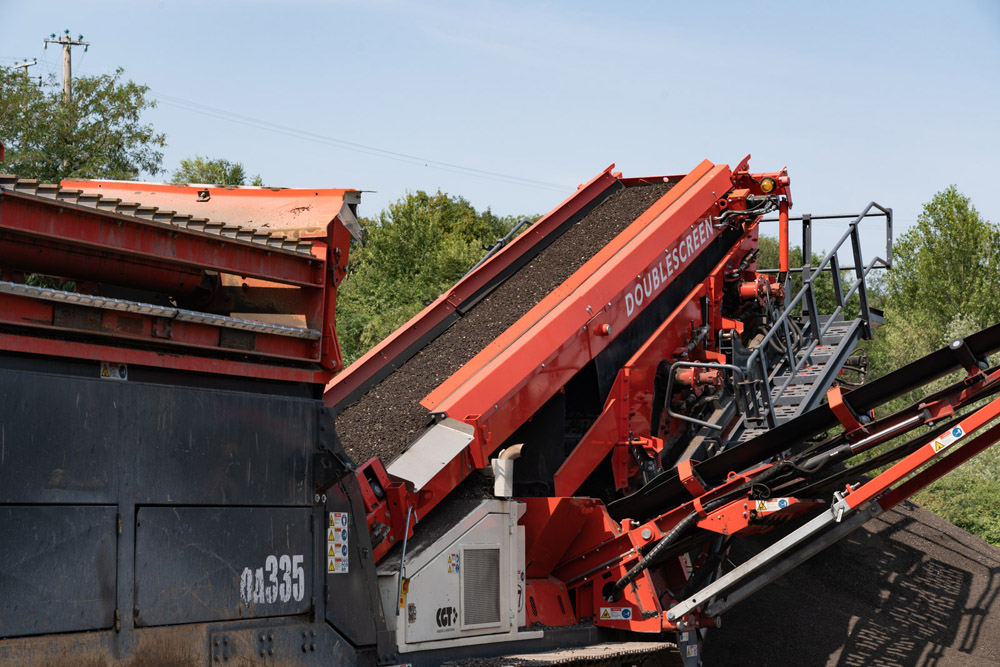
Flexibility is key
With quarries and plants to operate and diverse customer requirements to satisfy, Vezzola has developed a plant solution that maximises its operations’ efficiency. Thus, all recent plant investment has been for highly mobile solutions. One such operation in Montichiari (Brescia) is a new high-performance quarry designed to produce large quantities of high-quality, sized aggregate whilst emphasising environment and safety. Although the plant is of a considerable size, it has a minimal impact on the surrounding environment as it is wholly contained in the extractive basin. The contour area and escarpment of the basin have been planted and restored, while noise and dust are contained through sophisticated control, suction and humidification systems. The quarry produces sized aggregates, round concrete materials and crushed products for bituminous conglomerates, which are stored and separated into 13 different classes.
The preparation of specific material is undertaken using an automated loading system, managed by PLC (programmable logic controller), which ensures maximum precision and reliability in preparing the mixes and, therefore, the finished product. In addition to the plant’s standard production, Vezzola is also able to provide customised concrete and asphalt mixtures on request, automatically managing up to five hundred different mixtures. The plant can operate up to 400 tonnes per hour, with equipment from Vezzola’s versatile and mobile fleet used if and when required.
New ways of thinking
Vezzola believes that a successful company must be a partner to its customers and form a close relationship with its suppliers. This has proved to be essential as all its operations rely on various crushing, screening, loading, hauling and excavation equipment from one company. “One of Vezzola’s most important operational partners is CGT, a Caterpillar and Sandvik dealer. Caterpillar earthmoving machinery is used to carry out infrastructure works and undertake loading and uploading operations at the company’s operations.
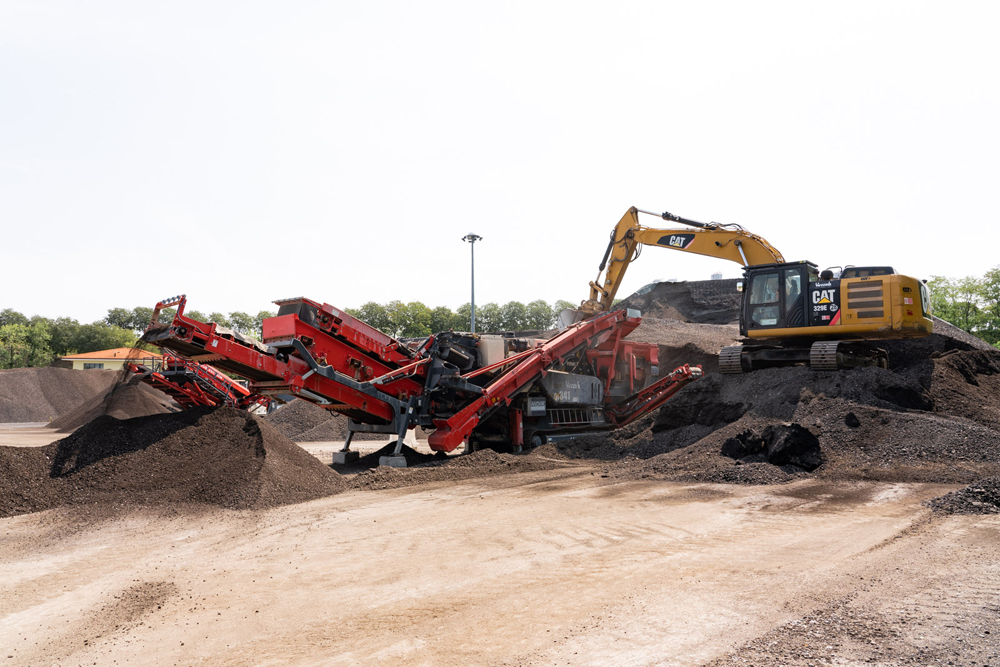
A broad and transparent dialogue has been cultivated over the decades of partnerships between the companies, which are essential for correctly planning the turnover of machinery and always maintaining high efficiency of the machinery,” says Diego Brunello, Vezzola’s production manager.
“In recent years, also thanks to the important stimulus programme of the Italian government for the development of automation systems called ‘Industry 4.0’, the interconnection between earthmoving machinery and the company’s headquarters has increased significantly. These investments have increased onsite machine use safety, scheduled maintenance interventions, the control of the machines’ efficiency, and materials handling data usage. Clients increasingly request the latter to improve the quality of the infrastructural works carried out.
“In partnership with Sandvik, it was decided to renovate part of the mobile systems as the flexibility that the systems could offer was fundamental. The business unit focused on producing building materials processes, not only limestone material but also recycled material. Decades of research and development have led the company (Vezzola) to produce on a large scale these materials from demolition works, milling of road pavements and recovery of steel waste. Large quantities of significantly different products are processed within the waste treatment platforms of Lonato del Garda and Montichiari,” added Brunello. He continued: “It was, therefore, necessary to find extremely flexible mobile systems, which could be easily transported from one plant to another and whose layout could quickly change from one to the other avoiding high costs of maintenance. A change of mentality was made, passing from fixed plants that process the various products to mobile plants transported to the various plants and process the materials directly. This change of mentality leads to lower CO2 consumption since the materials are not moved from one plant to another, but it is the plant that moves.”
Reliability, performance and the environment
Sandvik mobile screen and crusher are used to process very different inert materials. “Sandvik is the most reliable partner that best embodies these three characteristics. Sandvik is close to the customer thanks to a widespread sales network entrusted to CGT (in Italy). This advantage is irreplaceable as the answers are fast and certain. Reliability as the service is impeccable; maintenance is fast and accurate. Finally, the research that has been done on reduced emissions have made it possible to have machinery with a low environmental impact. In the last two years, the focus on innovation has shifted from product innovation to environmental innovation. We believe that the reliability of a company is also measured in the knowledge accumulated after years of research and development and which will become a new income in subsequent years. The search for the right partner is a very important, indispensable effort, especially in a world where uncertainty reigns supreme. The resilience of companies is today more than ever the minimum requirement to maintain one’s leadership,” explained Brunello.
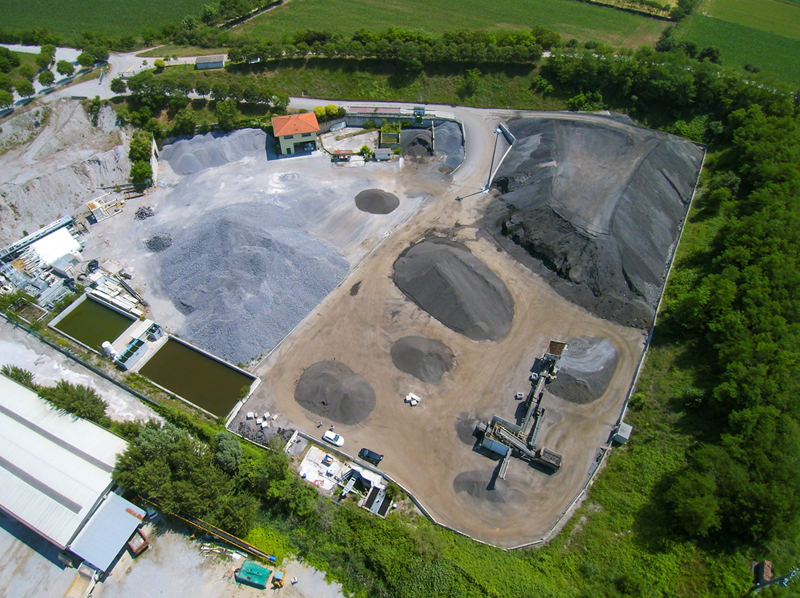
Maximised plant efficiency
To ensure that its quarries, cement-concrete and asphalt plants operate efficiently (as well as its construction operations), many Caterpillar earthmoving vehicles and trucks are used, including some of Cat’s latest ‘Next Gen’ developments. Alongside these, the Sandvik equipment consists of a QA335 Doublescreen and a QI341 impact crusher with hanging screen. Vezzola uses them both for recycling (demolition and asphalt) and at its quarries, depending on current requirements. “Vezzola chose Sandvik because its trademark technologies, ‘Doublescreen’ and ‘Prisec’, make the difference. A Doublescreen enables the screener to produce 30% more than another model of the same class. Thanks to Prisec, the impact crusher could work as primary or secondary, having the same production and quality. That gives Vezzola the opportunity to use the machines in different applications,” stated Brunello.
Vezzola purchased its first Sandvik equipment in 2017 and is a CGT customer of long standing. The company acquired its first Cat machine in the 1960s, now owning and operating 10 Cat hydraulic excavators, nine Cat wheeled loaders, two Cat dozers, one Cat motor grader and three Cat skid-steer loaders. Other equipment is hired in from CGT as needed.