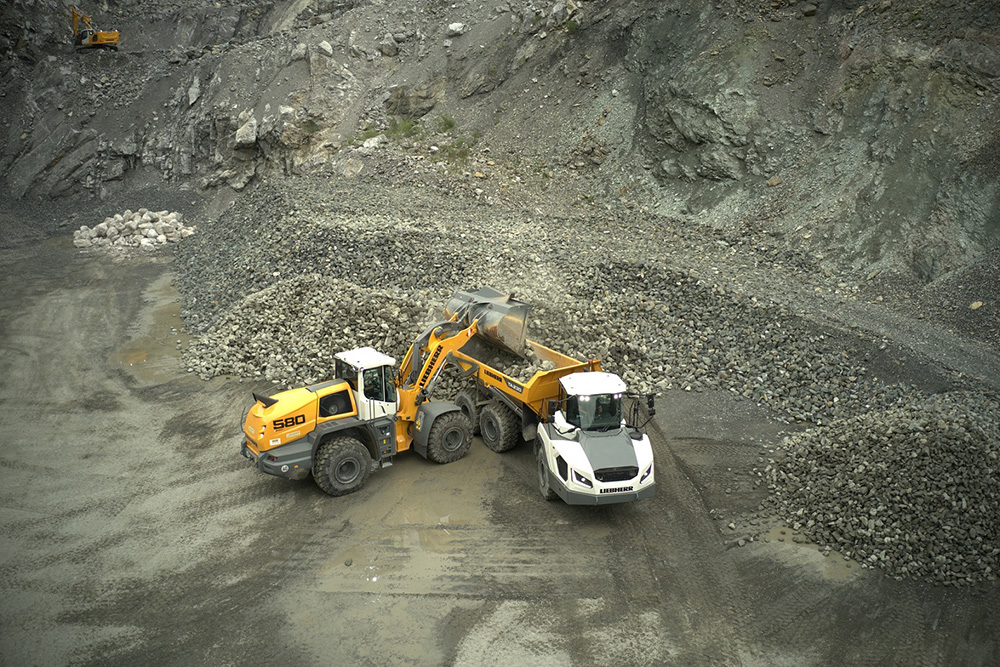
To use an industry-related metaphor, the mineral product stockpile was in good shape at the start of 2022. However, there was much concern over whether a perfect storm of external factors would harm the smooth flow of material off the conveyor belt.
In Britain, demand for mineral products, such as aggregates, concrete, asphalt and mortar, recorded double-digit growth during 2021, a sharp recovery from the COVID-19-pandemic-induced slowdown a year earlier.
A comprehensive industry survey by the Mineral Products Association (MPA) showed that volumes of primary aggregates increased by 15.7% on an annual basis in 2021, 14.1% for ready-mixed concrete, 12.5% for asphalt and 24.4% for mortar.
These materials are the essential elements of the construction supply chain, forming the foundations and structures of building projects and infrastructure schemes, with MPA members supplying 90% of total market demand in Great Britain. Compared to the previous quarter, sales volumes of aggregates and ready-mixed concrete grew by 3.8% and 5.9%, respectively, in Q4 2021. Asphalt and mortar sales recorded small quarterly declines, but total demand in volume remains elevated. Survey results also showed that construction demand remained strong in the final quarter of the year, despite unprecedented supply bottlenecks impacting progress on construction sites, cost increases and higher uncertainty due to Omicron.
Overall, the recovery in mineral products demand last year was faster than expected and imbalanced. For instance, aggregates and asphalt sales in 2021 exceeded pre-pandemic levels in 2019, but ready-mixed concrete and mortar sales remain weaker. Asphalt and aggregates demand was supported by an acceleration in infrastructure work, including roads and major infrastructure projects such as High Speed 2 (HS2). Asphalt sales have maintained a historically high activity level for the past 18 months, with producers working hard to meet pent-up demand from delayed road projects due to the pandemic. That’s in addition to the demand stemming from the Government’s Road Investment Strategy 2 and an increase in demand from local authorities for repair and maintenance work.
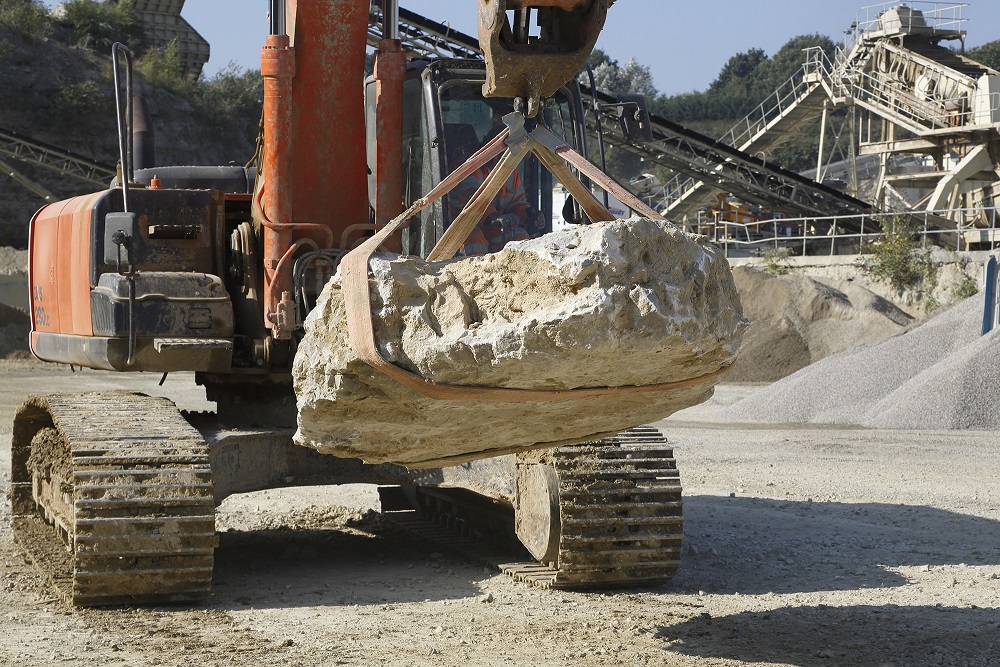
After a healthy first quarter of 2022 for UK producers of mineral products, the MPA believes the outlook for the rest of this year will be influenced by rising costs, lower growth prospects and international uncertainties.
MPA figures show that markets for essential materials like aggregates, concrete, asphalt and mortar continued where they left off at the end of 2021, with sales volumes increasing on a quarterly basis in Q1 2022. This reflects firm construction demand at the start of 2022 despite the bad weather that hit parts of Great Britain during February, and some easing in reported supply chain constraints, including for HGV drivers - albeit at a cost.
The latest MPA industry survey shows that asphalt sales volumes in Great Britain rose by 1% compared to the previous quarter, sand & gravel by 2.1%, ready-mixed concrete by 3.2% and mortar by 5.5%. Only crushed rock volumes saw a marginal decline on a quarterly basis (-0.4%) but remain at an elevated historical level.
After hitting their highest peak since 2008 last year, asphalt volumes continue to be supported by pent-up demand from delayed road projects due to the pandemic, in addition to demand stemming from National Highway’s Road Investment Strategy (RIS2) and an increase in demand from local authorities’ repair and maintenance work. The bulk of the logistical and haulage issues reported by asphalt producers last year appear to have eased, but the cost of labour, energy and raw materials including bitumen, are all escalating. The big concern is the impact this may have on planned National Highways schemes and already stretched-out local authorities’ repair and maintenance budgets.
Ready-mixed concrete sales were hit hard during the onset of the pandemic, and in the year ending March 2022 were still 6% below the pre-pandemic (2019) levels. Both London and the Southeast, which make up just over 30% of the total share of volumes across Great Britain, have endured a sustained period of weakness which can be traced back to comparatively slow recovery in commercial construction projects, particularly for new office towers and retail space. Overall demand is nonetheless supported by major infrastructure projects, including HS2 and Hinckley Point C, as well as a healthy pipeline of industrial warehouse projects.
Simultaneously, a pickup in new housing starts since last summer is also fuelling increases in mortar demand. On a quarterly basis, mortar sales reversed the two back-to-back quarterly declines in the second half of 2021, with a 5.5% increase in 2022 Q1. Sales volumes returned to their highest level since 2019 Q3. However, while the current year has begun strongly, the uncertainties facing housebuilding have increased amid rising costs of materials and labour. The wider macroeconomic conditions are also being closely watched, particularly as the increasing cost of living has sparked a decline in confidence among UK households and nudged the Bank of England to increase interest rates four times in less than five months, pushing up mortgage costs.
In the aggregates market, crushed rock sales remain comfortably above the pre-pandemic level, benefitting from demand from highways schemes and the manufacture of asphalt, and as fill materials on major infrastructure projects. Sand & gravel sales have been more muted, albeit this is linked to weaknesses in some areas of ready-mixed concrete demand.
The bulk of the momentum in mineral products demand recorded at the start of the year should carry over into Q2, but thereafter, Aurelie Delannoy, MPA director of economic affairs, warns that steep cost increases and broadening risks facing the UK economy could make for a more challenging environment over the second half of the year and into next year.
“Current construction activity levels and mineral products demand remain high. The short-term pipeline is also robust. However, with material cost inflation running at 25% on an annual basis in April, the supply environment is a challenge. There are concerns over the impact of passing these costs onto customers and the commercial viability of future projects.”
“We expect that large infrastructure projects will continue to drive further growth in demand, but this cannot be at the expense of the ‘bread and butter’ activity level fuelled by the private sector, particularly consumer-facing private new housing, private housing repair and maintenance and commercial retail sectors. Construction forecasters have already reduced their growth expectations for this year and there are signs that the pressures are continuing to pile up. This means that mineral products companies are facing a tough combination of rising costs, dwindling growth prospects and international uncertainties.
“Confidence to invest in future capacity to deliver on Government’s increased infrastructure and housing ambitions relies on better delivery of planned projects than has been evident in recent years. Meanwhile, two energy-intensive mineral products industries - cement and lime – have been excluded from Government’s compensation scheme for climate change costs on the basis of technicalities. Clearly, a more consistent and strategic approach to Government’s objectives and policy delivery is still lacking.”
The Construction Equipment Association (CEA) said UK Chancellor of the Exchequer Rishi Sunak’s Spring Budget Statement to parliament on 23 March 2022 was a “missed opportunity" to help manufacturing.
Suneeta Johal, CEO of the CEA, said that the measures set out by the Chancellor had ignored industry pleas for a delay to red diesel and biofuels rebate reform.
“This mini-budget was an opportunity for Rishi Sunak to take significant action to help businesses to minimise the impact of rising inflation, which is at a 30-year high and continues to rise," she added. "This Spring Fiscal Statement comes at a critical time for manufacturing in the UK – and as expected it did not deliver and was very much an exercise of smoke and mirrors.
"Petrol and diesel prices have soared in recent weeks hitting an all-time high – whilst the announcement of a fuel-duty freeze and the temporary cut of 5p per litre is welcome, in reality, it will do very little in the way of easing the burden on the construction sector, where despite extensive lobbying, Government has ignored pleas for a delay of the reform of the red diesel and biofuels rebate.”
Johal added that spiralling energy costs are crippling the construction equipment sector and the situation has worsened due to the Russian war on Ukraine. She said that the lack of support for businesses is "deeply disappointing".
"The VAT cut on energy-saving devices, such as solar panels, has marginal benefits," said Johal.
She added that investment in alternative sources of power was overlooked and is an opportunity missed.
"It was immediate help our sector needed - and once again Government failed to deliver," she commented.
The MPA also welcomed the 5p-a-litre reduction in fuel duty announced by Chancellor Sunak, but, like the CEA, said it was disappointed not to see a change of mind on the red diesel rebate, with fuel costs skyrocketing at a time of high inflation.
CEO Nigel Jackson said: "Taken in the round the statement does little to ease the worsening cost burden on industry, particularly energy and carbon costs, nor does it boost demand and give the confidence to invest in the short term or more strategically for the longer term."
The MPA, whose members produce 400 million tonnes of materials for UK building and manufacturing each year, had written to the Chancellor earlier in March to request a delay in the removal of the red diesel rebate, as well as calling for urgent action on soaring energy costs and transparency on delivery of the Government's infrastructure plans.
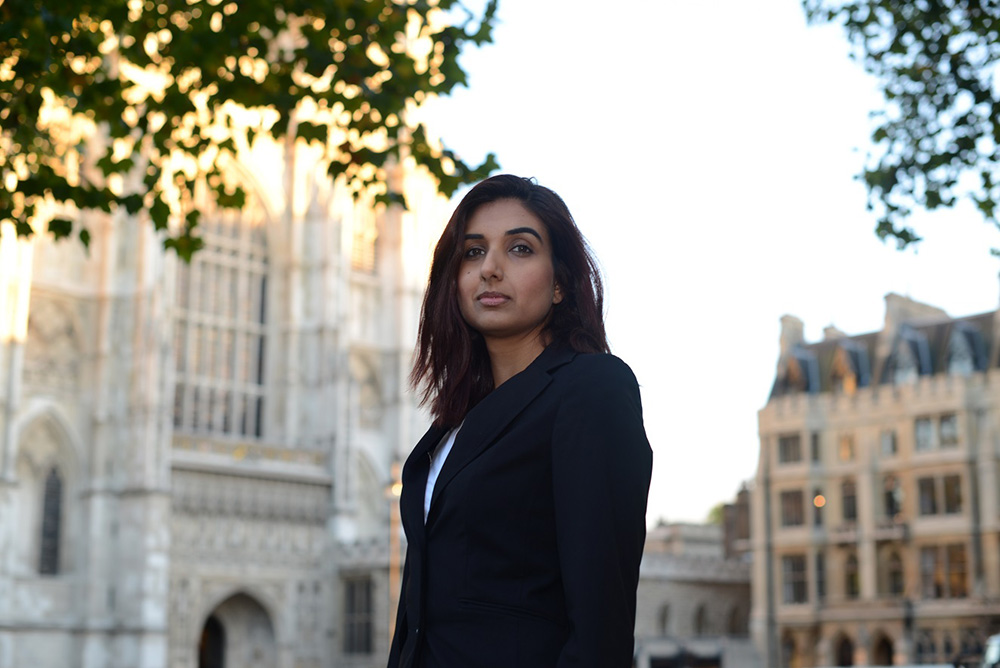
UK construction market output was valued at £286.99 (US$350.4bn) in 2020 and was forecast to record growth of more than 10% in 2021, according to analysis by GlobalData, a leading business market intelligence consultancy.
The UK construction industry is projected to register an annual average growth of more than 3% between 2022-2025, says Global Data, adding: “The industry’s output over the forecast period will be supported by investments in the transport, renewable energy, housing, automotive and manufacturing sectors.”
GlobalData expects Britain’s construction sector to return to pre-pandemic levels in 2022. However, the same source states that project delivery will continue to be hampered by high materials prices and shortages.
“The industry’s output over the long term will be supported by a strong pipeline of construction projects,” continues GlobalData. “In September 2021, the UK government published its National Infrastructure and Construction Pipeline, which outlines £611.4bn (€720.6bn) investment in infrastructure projects over the next 10 years. The largest share of the investment plan has been earmarked for the transport sector, which includes flagship projects such as HS2 and the Lower Thames Crossing road tunnel. The energy and utilities sector will receive £56.1 billion (€66.1bn) between 2021 and 2025, the second-largest share of the investment package and includes major projects such as the Hinkley Point C nuclear power plant.”
Irish building materials giant CRH says its UK & Ireland Q1 2022 sales were well ahead of the same period of 2021, reflecting good underlying demand and milder winter conditions. A group statement released on 20 April 2022 said: “In the UK, price increases were implemented across all products with volume improvements also positively impacting sales. Our businesses in Ireland had a positive start to the year with volume increases in all key products against a prior year comparative impacted by COVID-19 restrictions.”
CRH’s good Q1 in UK & Ireland follows on from chief executive Albert Manifold hailing the "outstanding commitment and resilience" of the group’s workforce after CRH posted a 12% year-on-year global sales rise in 2021.
GlobalData, states that the construction market in Ireland was valued at £24.6 billion (€28.9bn) in 2021. The market is projected to grow by the same source at an annual average growth rate [AAGR] of more than 4% during the period 2023-2026. The Ireland construction market growth in 2022 will, says GlobalData, be supported by investments in healthcare and housing initiatives under the 2022 Budget, which was announced in October 2021. GlobalData says the implementation of projects under the Nation Development Plan (NDP) 2021-2030 will also provide support, but there are downside risks in the form of supply chain disruptions and high prices for construction materials and energy.
Gerry Farrell, CEO of the Irish Concrete Federation, says that after a strong 2021 and first quarter of 2022, headwinds like those facing the UK mineral products industry may be experienced in Ireland.
“In general, there is a lot of concern at the potential impact of inflation and supply chain disruption on manufacturing and building costs. All our quarry and concrete manufacturing members up to now [mid-May 2022] are still relatively busy but there are some signs that the unprecedented increases in the price of building materials could lead to a slowing down of activity later this year and into next year.
“The Irish government is still predicting 5% economic growth this year, but inflation is a big factor, and it’s predicted to rise to 6.5% for 2022. There is a good pipeline of government public work to 2030, but the Construction Industry Federation has highlighted that materials and other cost inflation is pushing up the cost of building, which hits builders hard as they’re tied into fixed-price projects. Recently Government has indicated that they will look at introducing some kind of price valuation clause in public contracts to allow works to continue.
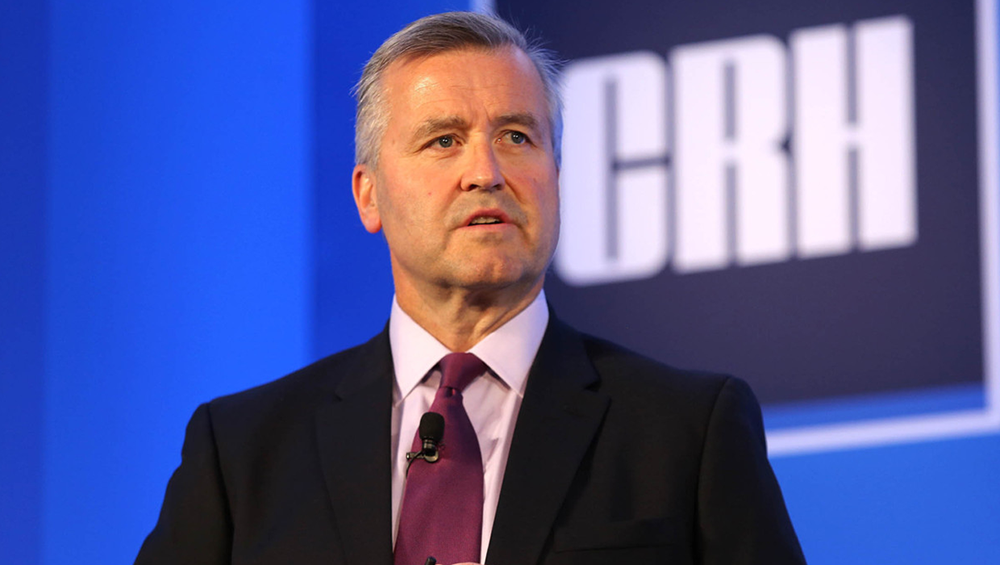
“Rising energy costs is another massive concern for our members, both directly and indirectly. Obviously, the key raw material of concrete is cement, which is highly energy-intensive to manufacture, making it particularly vulnerable to the massive increases in electricity costs in recent times. There has also been a major increase in the cost of fuel, thereby adding to transport and delivery costs and the cost of carbon credits arising from the EU Emissions Trading Scheme is starting to bite.”
On a more positive note, Farrell says that the Irish construction and building materials industries are buoyed by the Irish government’s Housing for All policy, which quantifies the need for the construction of an average of 33,000 houses per year until 2030. In 2021 there were only 21,500 houses completed so there is an urgent need for a major increase in new house construction from current levels. The question is, will this happen given rising building costs?
Farrell says the Irish building materials industry has not changed much in its large and small to medium-sized (SME) makeup in recent years. “The biggest new player here is Breedon, after its purchase of the Lagan Group.”
Speaking about the Irish Concrete Federation’s new projects, Farrell says: “We are setting up a sustainability resource within the federation as there is an ever-increasing need to communicate better that our members’ activities are absolutely essential for society and our materials are sustainable. We are also launching a policy document on the future availability of authorised aggregates reserves. Our members are concerned about the lack of authorised aggregates reserves in certain parts of Ireland, and we have identified reform of the quarry planning system as crucial in protecting the future supply of locally available and sustainable aggregates. Other areas we want to do more on is upskilling our employees through effective training and developing initiatives to attract new people into our industry.”