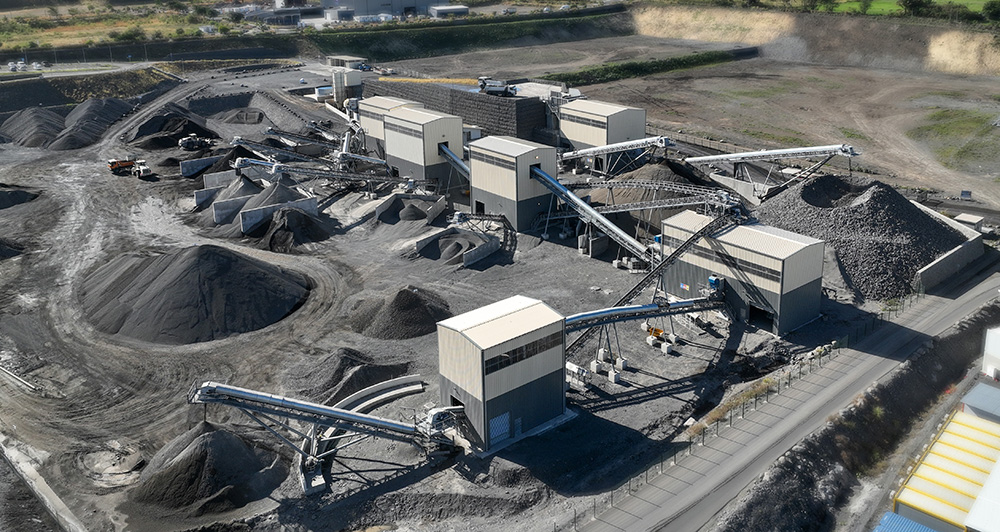
The tailor-made Metso Outotec plant for SCPR’s Pierrefonds site is comprehensive, along with being highly productive and efficient. It consists of a Nordberg C130 jaw crusher, a PF561 pan feeder, Nordberg GP100S and HP200 cone crushers, a Barmac B7150SE impact crusher, an MB352 Rockbreaker, a CVB 103P inclined screen, ES203 and ES403 horizontal screens, conveyors and auxiliary equipment. The plant configuration can produce up to 376 tonnes of product per hour.
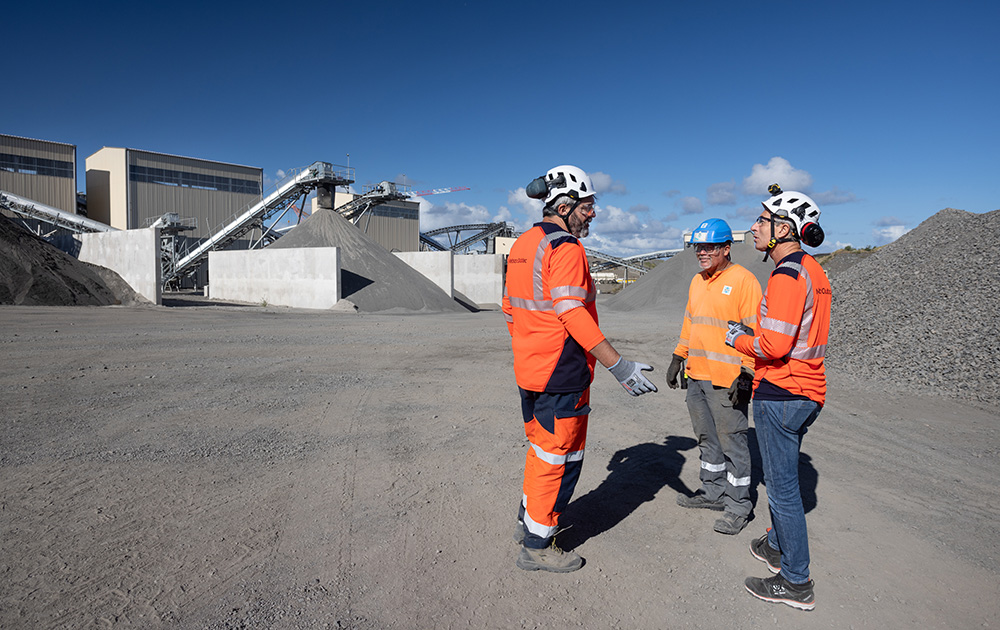
SCPR, a Colas Group company, signed the installation contract with Metso Outotec in December 2019, with engineering beginning in January 2020. Primary foundations were set in April 2020, with secondary and tertiary foundations completed the following month. Mechanical erection began in July 2020, completing in February 2021. Plant commissioning and start-up began in January 2021, with the set-up fully operational since May 2022.
“The site is a completely new one. Before, there were only mango trees on it,” explains Thierry Le Cloître, SCPR’s head of materials services. “Our previous site was around five to six kilometres away. It included a Metso crusher and some Metso screens, but the crusher was over 30 years old. We were keen to invest in a new site. We are extracting the alluvial material for the new site from the same place near a river where we sourced the material for the old site.”
Le Cloître says SCPR’s old materials-processing site processed just over 300,000 tonnes of material per year, with the objective for the new state-of-the-art Metso Outotec plant-equipped Pierrefonds site three times that level.
“We don’t have any more capacity at our other processing site in the west of the island, so we are crushing all the additional material for customers in the south [Pierrefonds]. We have a large customer base in La Réunion, including those working in road construction and concrete production and companies and individuals involved in smaller building projects.
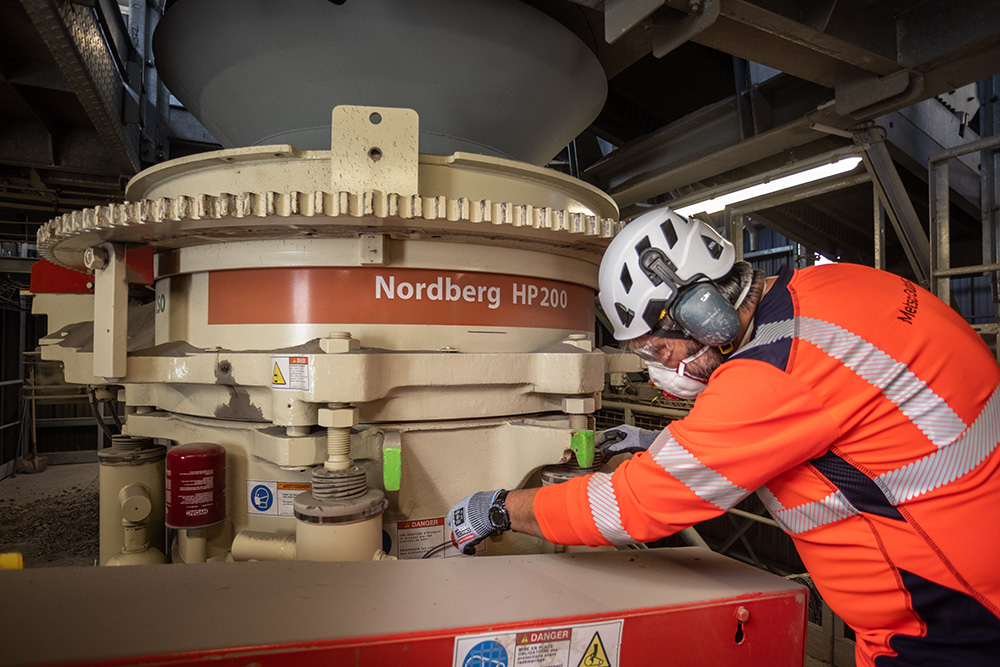
“Our new Metso Outotec plant has two production chains: one for sand and gravel crushing, screening and washing for concrete customers; the other for big rocks over 80mm which are crushed and screened for asphalt plant and other customers.”
With a population of just over 873,000 and covering an area of 2,511km², La Réunion is located around 950km east of the island of Madagascar and 175km southwest of the island of Mauritius. Le Cloître says this makes exporting SCPR’s products too expensive.
Commenting on SCPR’s working relationship with Metso Outotec before closing the deal on the new plant installation, Le Cloître says: “We knew what type of installation we wanted. We have four crushing plants across the island and know exactly what material we have to crush and how to crush it. What we needed to work with Metso Outotec closely on was the exact detail of each production chain that enabled us to match our [treble] production objective and be able to measure exactly what we produce. We also wanted to be very selective about what we produce, so we produce only what we needed, with no waste.”
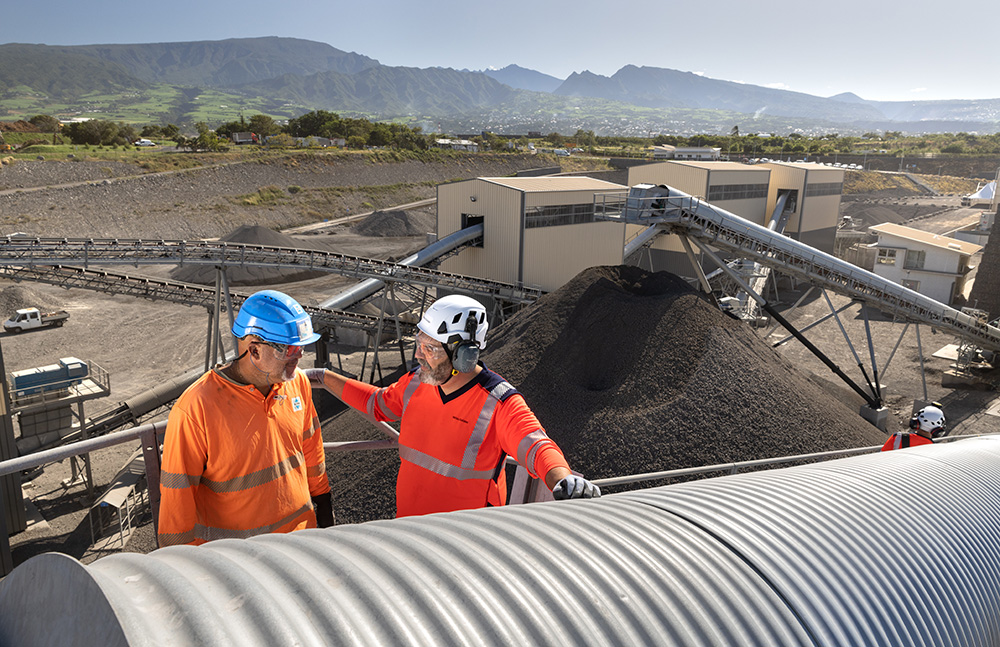
Le Cloître says SCPR put the new Metso Outotec site set-up through a rigorous two-week testing period before it went fully operational to check whether the new installation was likely to meet SCPR’s ambitious long-term production target of 900,000 tonnes of material processed a year. “It met our production targets for those two weeks, but it was a very challenging time, as it was during the COVID-19 pandemic.
“We started operating the plant fully last year over one shift of seven hours per day, five days per week. In September 2022, we pushed that up to ten hours per day. In December, we went up again to 14 hours of operation across two seven-hour shifts. We aim to run the plant 21 hours a day over three seven-hour shifts by the end of March or early April 2023. That five-day running time will take us to 900,000 tonnes a year.
“You expect to need to adjust things when you open a new site and run a new crushing plant of this size, but in less than a month, we had the final product quality we wanted.”
Touching on the servicing and maintenance needs of SCPR’s new Metso Outotec plant, Le Cloître says the skill and experience of the company’s engineering team and its familiarity with Metso Outotec plants and replacement parts mean that production issues that arise can generally be resolved in-house. “Metso Outotec engineers make visits to the island twice a year to see us and other customers to check crushers and other installed plants. They also came in December last year, just two days after we highlighted a particular issue [with the new set-up].”
“We had a lot of discussion with the customer before we settled on the final plant solution,” explains Marc Fourneret, senior project manager for Metso Outotec’s aggregates business area. “The biggest challenge was supplying the right solution that fitted the budget of the customer.”
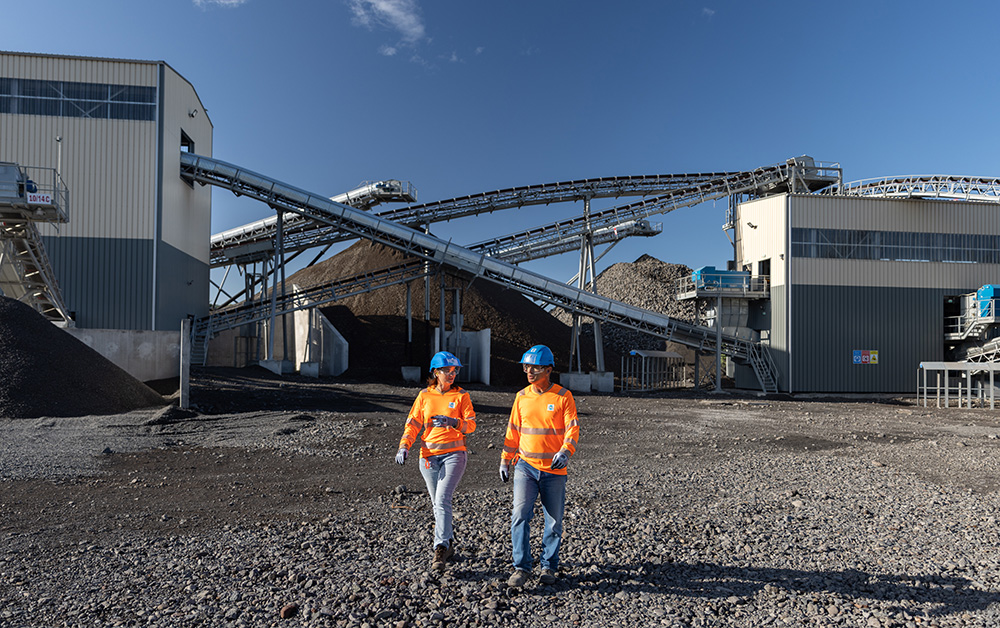
“Automation is the key to managing this plant, to enable the customer to be selective in the product they are producing,” says Françis Lacôte, process and application expert at Metso Outotec. “If you want to produce more or less of a certain product, you can do that with automation, with all the [Colas] software-generated information coming to a single [customer] point. There is more variation in the material content fed into this plant than was planned.
“The plant we supplied can react quickly to any changes in the feed material,” continues Lacôte. “You get a full overview of the plant, and if you are a specialist, it is really easy to investigate and find any trouble spots.”
Speaking about challenges that arose during the plant installation for SCPR, Fourneret says: “The first challenge was COVID-19. Just two months after we started the engineering process, we were in the pandemic. After that, there was the challenge of transporting all the required equipment to the island. That took time. Now the plant is running, I think it’s performing even better than what was specified in our contract with the customer.
“We have a very good relationship with SCPR and Colas and have just signed a contract with Colas for another big plant in French Guiana [an overseas department of France on the northeast coast of South America].”
Fourneret and Lacôte were speaking to Aggregates Business in January 2023, with Lacôte highlighting that Metso Outotec engineers were due to visit SCPR’s Pierrefonds site in mid-February. “The company’s production is changing to reflect the changing market. So, we need to adapt [the plant] and ensure even greater flexibility.”