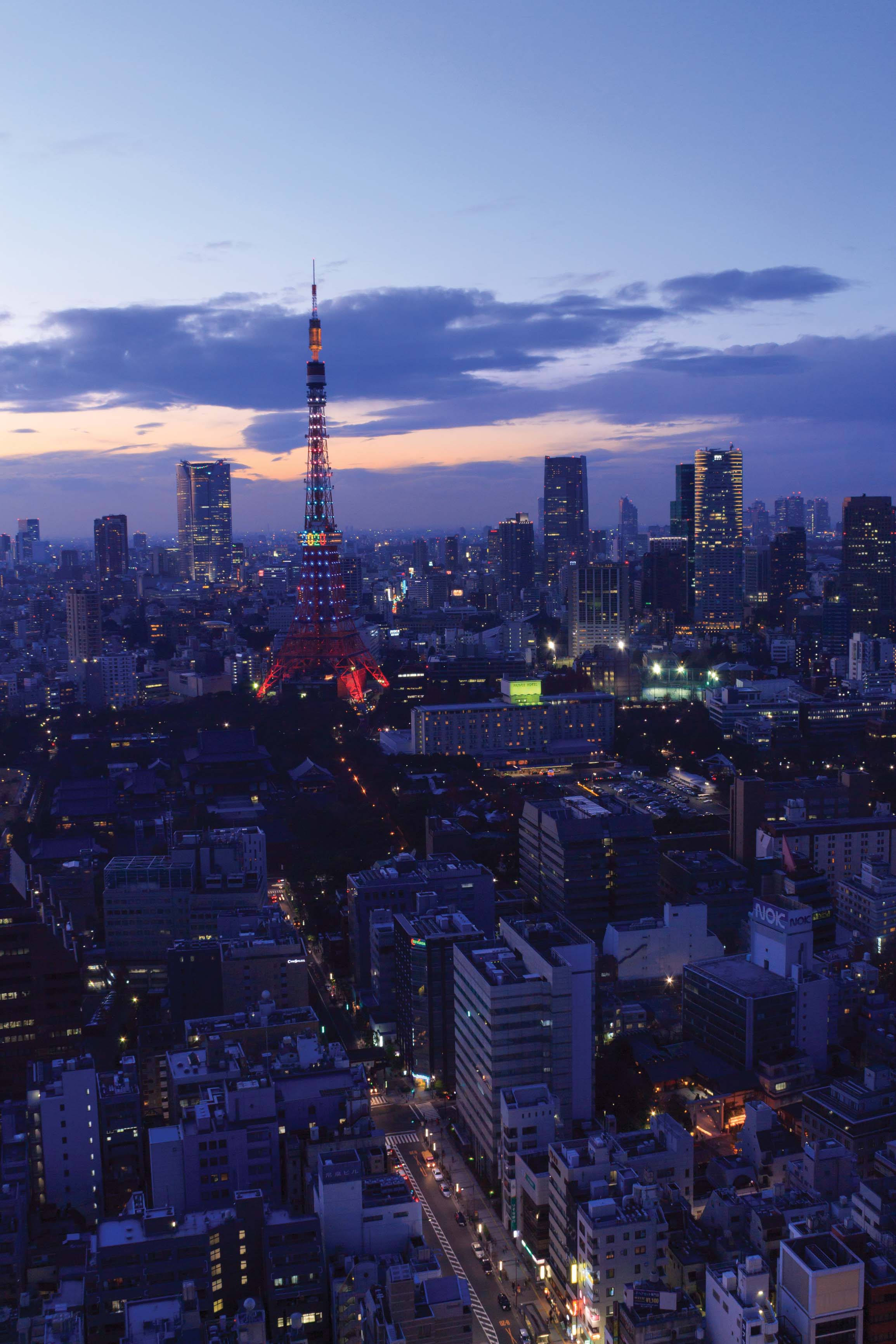
Japan’s ruling government has ploughed huge sums into upgrading Japan’s infrastructure, creating huge opportunities for aggregates producers and construction equipment manufacturers. But, as Guy Woodford asks, will such investment lead to long-term success for those involved in the Asian nation’s construction and aggregates sectors?
After coming into power in December 2012, Japanese Prime Minister Shinzo Abe aimed to spend 10 trillion yen (US$107 billion) on infrastructure over the following 15 months in a bid to revive his country’s flagging economy.
To put the investment figure, around half of which is said by critics to be funded by government debt, in perspective, a
More recently, in May 2015, Abe also unveiled a plan to expand Japan’s financing for infrastructure projects in Asia by 30%, with highly respected business news outlets such as The Wall Street Journal saying how this signalled Tokyo’s intent to counter China’s push to spearhead a new regional investment bank.
The Wall Street Journal said that the increase in Japanese funding would see the nation contribute around $110 billion in the next five years to fund major infrastructure investments across Asia. Various options will be used, including expanding the Asian Development Bank’s lending capacity and yen loans from the Japanese government.
Latest Japan Construction Equipment Manufacturers Association (Japan CEMA) figures indicate that Abe’s initial 15-month domestic infrastructure spending bonanza to April 2014 may have had some impact on domestic construction equipment sales for the year – up 8.8% compared to 2013. The Japan CEMA also notes that North America, Europe, and Asia, excluding China, have also been encouraging export destinations for Japanese OEMs, with year-on-year sales growth of 9.8% in 2014.
However, as Japan’s population is ageing and shrinking, suggesting less need for new infrastructure and a smaller working population paying taxes into government coffers, many critics, including leading economists, have been left bemused by Abe’s hugely ambitious domestic and Asia-wide infrastructure spending programmes.
On the other hand, others back the Japanese government’s spending, stressing the need to deliver, among other things, a successful 2020 Tokyo Olympics.
The world’s 61st largest country, Japan boasts around 1.2 million kilometres of roads, giving it the world’s fifth-largest network. One of the current major Japanese highway network expansion projects is the $32billion construction of a second Tomei-Meishin Expressway, connecting Tokyo and Kobe via Nagoya. Japan is also reported to have 680,000 bridges, almost 10,000 tunnels, 250 bullet trains and 98 airports.
Some critics have talked of the country’s new infrastructure ‘white elephants’, citing, for example, the airport in Ibaraki, 85km north of Tokyo, which opened in 2010 at a cost of about $225 million as a hub for low-cost carriers. Now it is said to handle just six flights a day.
With further research indicating a declining number of motorists on Japanese roads, did the huge spending on infrastructure in Prime Minister Abe’s first 15 months in government supply, as the Japan CEMA figures indicate, only a short-term boost to construction equipment and aggregates demand, or will it help secure long-term growth?
Yoshida says that new infrastructure projects will lead to a 30% rise in the number of Japanese tunnelling jumbo job sites in 2015-2016, compared to the past three to five years. Yoshida continues: “This means that there will be a shortage of machines to undertake the drilling. In addition, most of the existing jumbos are so old that they cannot endure the work required at long tunnelling sites such as the Maglev high speed railway projects. For those projects, the contractors prefer to use brand-new machines due to durability, reliability, and efficiency. This means that there are many opportunities for us to supply our equipment as Sandvik’s reputation for tunnelling jumbos is very good.”
Sandvik Construction also believes there will be a big increase in demand for specialist demolition and reconstruction equipment linked to work connected to the 2020 Tokyo Olympics.
“One factor that has enabled Sandvik to gain significant competitive advantage is that we have been quick to embrace new environmental challenges, such as reduced engine emissions. Many local competitors have not been so environmentally focused and will not be able to take advantage of improved market conditions until they fit the Tier4 Final engines,” adds Yoshida.
The earthquake and tsunami caused significant sinking of the ground level in several coastal areas in the northern part of Honshu island. Before new construction works can begin, the level has to be raised by several meters with aggregates.
Of Japanese demand for aggregates and quarry-based equipment, Suhen Agarwal, Metso vice president crushing & screening equipment sales & distribution, Oceania, said: “In Japan, the construction industry value is approximately US$250 billion. The cement production is approximately 60 million tonnes. Hence, it entails a large demand for aggregate and quarry based equipment. The total aggregate production in Japan is approximately 400 million tonnes and the construction machinery demand is around $11 billion.”
Agarwal says nearly 350 pieces of crushing & screening equipment (mobile and stationary combined) were sold in Japan in 2014, and similar demand is expected in 2015. “The market mainly is dominated by local manufacturers, yet there is enough potential for global company’s such as Metso to get a decent market share due to their high technology and better performance equipment,” says Agarwal. “Currently, Metso has a fair market share in the addressable market portion, mainly in mobile machines and we have increased our share consistently in last few years.”
Agarwal believes the upgrading of existing old local machines and the need to invest in plant for upcoming infrastructure projects gives the Finnish giant growth opportunities. “With our state-of-the-art mobile machines, we have already established a niche place in Japanese market. Down time and cost per tonne are critical factors for customers in Japan and where customers are more open to adapting and investing in the superior technology from Europe.”
Meanwhile,
“Hydraulic excavators are used [in Japan] not only for loading but also for a diversity of other purposes, and often for intensive high-load work in the country’s quarrying industry. As a result, the risk of breakdown is high, particularly for the structure.
“Therefore, many users want hydraulic excavators to have specifications that raise their durability, including specially reinforced booms, arms and buckets, and undercarriages with reinforced guards. Although improvements in power and speed are important, many users regard reduction in running costs as an important matter.
“The hydraulic excavators used in most quarries in Japan do not need to be so big, but what they do need to have is reasonable power and durability, which is why the companies choose excavators in the 35 and 45 tonne classes.”
Although not currently involved in large scale Japanese infrastructure projects, the Hitachi CMJ spokesperson said that it may become involved in works linked to the Tokyo 2020 Olympics.
Japan’s cutting-edge cement industry may also benefit from increased infrastructure spending linked to Tokyo 2020 and other key national infrastructure projects.
According to the Japan Cement Association, as of April 2014, the cement industry’s production scale spanned 30 plants owned by 17 companies, supporting clinker production capacity of 55 million tonnes.
Cement plants are located all around Japan. There are particular high concentrations, however, in the Kyushu region (6 plants) and Yamaguchi Prefecture (4 plants), both areas known for their rich limestone resources, and the Kanto district - the nation’s largest cement consumption market (6 plants). Currently, there are large-scale plants with annual clinker production capacity of over 6 million tonnes. Furthermore, clinker production capacity per plant is around 1.8 million tonnes.
The Japan Cement Association says Japanese cement plants continue to advance mechanisation and computerisation, with the average number of full-time workers at each plant now slightly over 100 people.