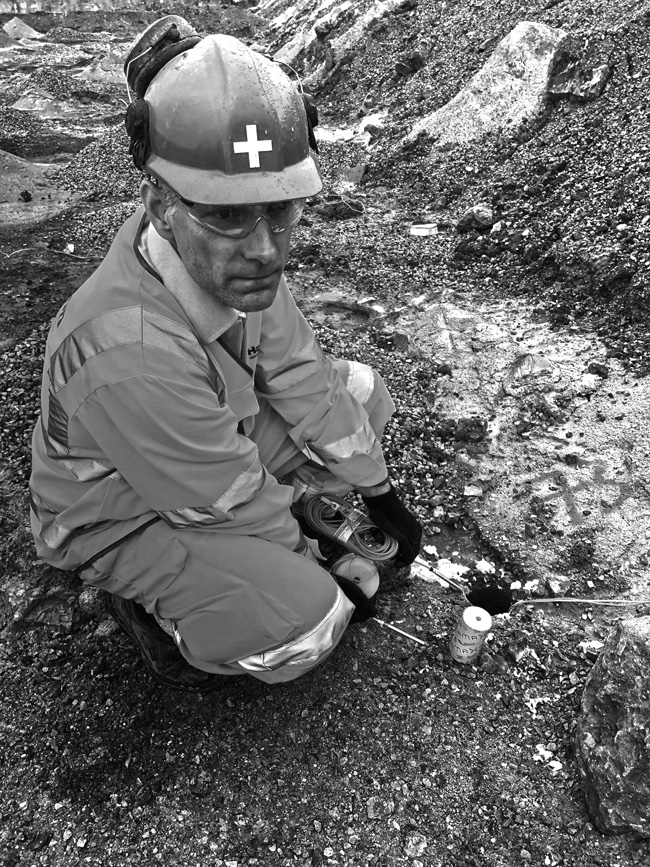
Robin Gillespie is the first person in the UK minerals extractives and quarrying industry to achieve a first-class honours degree on a course developed by the
You warm to Robin Gillespie when you meet him. As well as being full of energetic conversation and witty, self-deprecating one-liners, he is also passionate about all things ‘quarrying’. Currently
A part-time degree designed specifically for the mineral products industry to prepare its leaders and managers for the future, the BSc (Hons) Minerals Management is a blended learning course involving online modules, as well as field projects.
“I enrolled on the inaugural BSc degree course in 2014, combining it with my work as the manager of Hanson UK’s Shap quarry in Cumbria [north-west England]. I had to drop out after six months as I had no assistant manager at that time who could help with some of my workload. By 2016 I had a stable team in place and Phil Redmond [MD Hanson Aggregates UK] and Simon Day [Hanson Aggregates (North) UK] agreed to my request to restart the course. I can’t thank them enough for that. I’d also like to thank Hanson UK as a company and staff at the University of Derby for all their support during my studies.”
Gillespie, who is married and has two sons, is “very proud” to be the first student to achieve a first-class BSc (Hons) Minerals Management. “It took a great deal of hard work; many Saturdays and Sundays locked in my office at Shap quarry. In May 2016 my wife turned 50 and her birthday coincided with our 25th wedding anniversary. We had booked to go on holiday to Sorrento in Italy, but it clashed with a degree assignment I needed to finish. I was sat at this big marble table in our hotel and people were asking me what I was doing sat there with all these books and papers around me? My wife was very understanding and just told me to ‘get on with it!’ I certainly didn’t do many home improvements or much gardening for two years.
“During the honours degree course, I went down to the University of Derby three to four times a year for two years. We would work morning and night and do a lot of course research back in our hotel rooms. It was certainly not a jolly! Your head was crammed full of things. Most of the others doing the BSc course were aged around 23 and 24 and were doing it after finishing their foundation degrees. During our Derby meet-ups, I would joke that I was older than the lecturers! Most of the rest of our course was done via Blackboard Learn (virtual learning environment).”
Gillespie’s 63-page work-based project for his honours degree looking at the benefits of using electronic delay detonators (EDD) versus pyrotechnic detonators (Nonel) for quarry blasting earned him an 86% mark. As well as the project playing a key role in Gillespie becoming the first first-class honours student in Minerals Management, Hanson UK’s parent company, HeidelbergCement, has been so impressed with its documented potential efficiency and financial gains, that it is recommending that EDD use is preferred at each of its 30-plus Hanson UK quarries. They are also looking into the merits of greater EDD use at company quarry sites worldwide.
“It is great to hear that my research is reinvigorating discussion about HeidelbergCement’s global use of EDD for quarry blasting. The company’s Special Interest Group (SIG) is currently looking at how to implement EDD use at its quarries across the world. I did state in my final project report that HeidelbergCement should employ a blast optimisation specialist who could visit its biggest quarries globally and explain how EDD can be adopted and optimised.
“Blasting has been a fascination of mine for as long as I’ve worked in the quarrying industry. It is the most exciting part of the job, but it’s also got a lot of scope to go wrong. This makes it very important to have knowledge about how best to manage it.”
A lot of modern quarrying technology was first used in the global mining industry, with EDD blasting a prime example, given its initial adoption by South African and Australian mining operations in the early 2000s.
Gillespie says there is currently a 50-50 split in UK quarries’ use of EDD and Nonel for quarry blasting. This may be due to many British quarry owners and operators, and those in other parts of the world, remaining unconvinced by their cost to benefit ratio. Some may also have little knowledge of alternatives to traditional Nonel.
Gillespie’s quarry blasting project research was based on six trials he carried out at Shap quarry in 2016 and 2017. The quarry, where Gillespie worked as unit manager from October 2009 to January 2018, processes around 1.1 tonnes of limestone/year. As well as producing various -2mm to 100mm aggregate product for highways and construction sector customers, the quarry also produces industrial powers and lime kiln feed for the nearby Tata Steel works. Current planning permission for quarrying on the site runs until 2042.
“Without external factors such as extreme weather or unexpected and excessive plant, loader or hauler downtime, the savings I identified in my research through full adoption of EDD amount to £1.44 million [€1.61mn] per year. This is based on 30 million tonnes of rock blasted by HeidelbergCement’s Hanson UK quarry operations in 2016. However, I’ve worked in the UK quarrying industry for 33 years, and know external factors come up all the time. Even based on a 50% saving from full EDD adoption, that’s £720,000 [€806,000] a year.”
Gillespie has calculated that Shap’s full adoption of EDD for quarry blasting will save £41,800/year.
Of the key benefits of EDDs, Gillespie says: “EDDs improve site safety and offer better initial fragmentation of your blasted rock. This means the rock requires less drilling and excavator breaker and hammer attachment work. This also reduces attachment and excavator wear costs, along with excavator fuel cost. Aggregate material also arrives more quickly to your primary crusher, saving time and money. Reducing plant fleet fuel use also reduces your CO2 output. From a HeidelbergCement perspective, this ties in with the company’s commitment to sustainable quarrying.”
But what about any negatives associated with the use of EDD? “They are up to five times more expensive than pyrotechnic detonators. Critical communication links with EDDs can be disrupted by a stray current leakage or failed communications. They also have greater shock and pressure sensitivity.”
Born in Barnsley, South Yorkshire, Gillespie grew up in Penrith after his father took a job as curator of Lowther Wildlife Park. Although his current job requires a lot of domestic travel, he and his family still live in the town. “I’ve been in Penrith since I was two, but my uncle was the colliery manager at Barnsley’s main coal pit and then at Riccall mine, which was part of Selby coal field. The mine held the UK record for the fastest million tonnes of coal recovered in a year. It was by October one year in the late 1980s to early 1990s. Through my uncle, I’ve always had a strong interest in mining and minerals.”
One of the leading suppliers of heavy building products in the UK, Hanson UK, Gillespie’s employer, is developing talent to drive innovation and future business growth. Karen Wright, talent and development manager, said: “We provide a number of structured support programmes providing the training and necessary skills for those that aspire to be our future business leaders.
“Robin is a great example of what other science and engineering graduates could achieve on our graduate management trainee programme. These are in place to attract, develop and retain the talent that Hanson UK and the quarrying industry need for the future.”
Commenting on Gillespie gaining the first first-class honours degree from a University of Derby Centre for Mineral Products course, James Thorne, chief executive officer of the Institute of Quarrying (IQ), said: “Robin’s success marks a significant milestone in the continual progression of the mineral extractives programmes at the University of Derby.
“IQ’s partnership with the University of Derby is helping raise standards of professionalism throughout the industry, as more and more individuals and operators recognise the profound benefit of academic qualifications from higher apprenticeships through to honours degrees.”
Professor Judith Lamie, pro vice-chancellor, external affairs, at the University of Derby, added: “The University’s Centre for Mineral Products delivers industry-standard and globally recognised qualifications to the mineral products sector. We have a long-standing commitment to training and development in the mineral products industry and are extremely proud of our students who qualify in this field.”
Mark Osbaldeston, who heads up the Centre for Mineral Products at the University of Derby and worked closely with Gillespie during his studies, said: “I’m personally delighted for Robin that he received a well-deserved first-class honours degree. His application and enthusiasm for the course was exceptional.”