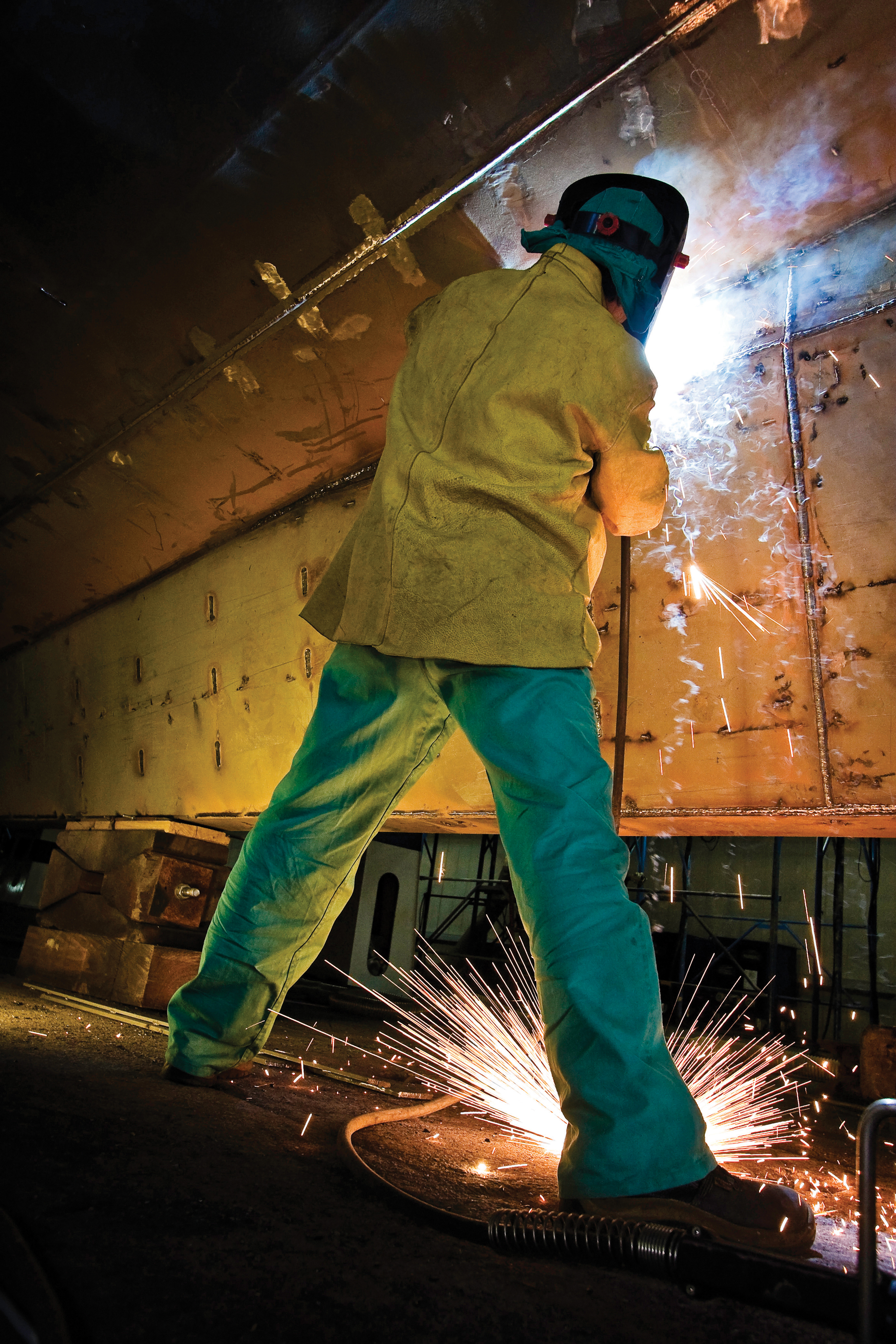
A new campaign seeks to raise awareness about the importance of carrying out maintenance in a timely and safe manner to reduce the number of people injured or killed
Statistics show that maintenance can be a dangerous task, with about 10% to 15% of all fatal accidents at work occurring while it is being carried out.
The
Between 15% and 20% of all work-related accidents happen during maintenance and the campaign stresses that maintenance affects every workplace in every industry and that it concerns people at every level.
It is not only individual maintenance workers who are the target group, says EU-OSHA director Jukka Takala. Operational managers and those responsible for planning should look at how to do maintenance in a smarter way to avoid problems before they even appear.
The Healthy Workplaces Campaign 2010-2011 launches on 28 April to begin more than a year of activities running in 35 countries including the 27 EU member states. The new campaign has two main messages: that timely maintenance is essential for workplace health and safety and that maintenance in itself can be a risky task.
Maintenance is easy to neglect and overlook but there is much at stake if it is not carried out properly. There are of course legal requirements on organisations. But it also makes business sense.
"Getting maintenance wrong is extremely costly: good safety management is good for business," said Takala. "Our aim is to encourage organisations to see maintenance as a process that needs to be managed systematically, rather than as a simple, one-off task."
EU-OSHA identifies a whole range of hazards faced by maintenance workers, from the physical such as noise, falls or being crushed to the chemical and biological, including contact with hazardous substances. There are also psychosocial hazards including time pressure.
There will be many events focused around the October 2010 and October 2011 European Weeks for Safety and Health at Work in addition to other activities throughout the campaign period. Ways of getting involved include organising workshops, poster competitions, quizzes, open days and media activities.
The campaign website includes advice and tips on running events as well as materials for download. There will also be good practice awards, recognising companies or organisations that have made outstanding and innovative contributions to promote an integrated management approach to safe maintenance.
The five basic rules to safe maintenance are intended to give a structured method that organisations in all industry sectors can follow.
"Make sure you know the maintenance issues and plan them at the time when you are planning the whole process," advises Takala. This includes aspects such as thinking ahead to ensure safe access.
Maintenance workers themselves should be directly involved in the initial risk assessment, which should consider potential hazards and the roles and responsibilities of everyone involved as well as the tools, equipment and any training required. Next step is to make the working environment safe, for instance by locking off the power supply to the equipment. The workers must be supplied with whatever personal protective equipment they may need and the maintenance work must be carried out as planned.
"If you have to do maintenance unexpectedly then you are under tremendous pressure to do it quickly because of the need to get the production going again," said Takala. "If you need to do something quickly you tend to bypass some of the more complicated procedures."
The process ends with checking that the maintenance has been completed properly and that the workplace has been left safe. Completing a report provides a record of what has been done and gives scope for commenting on any difficulties or recommendations so that it can be done even better next time around.