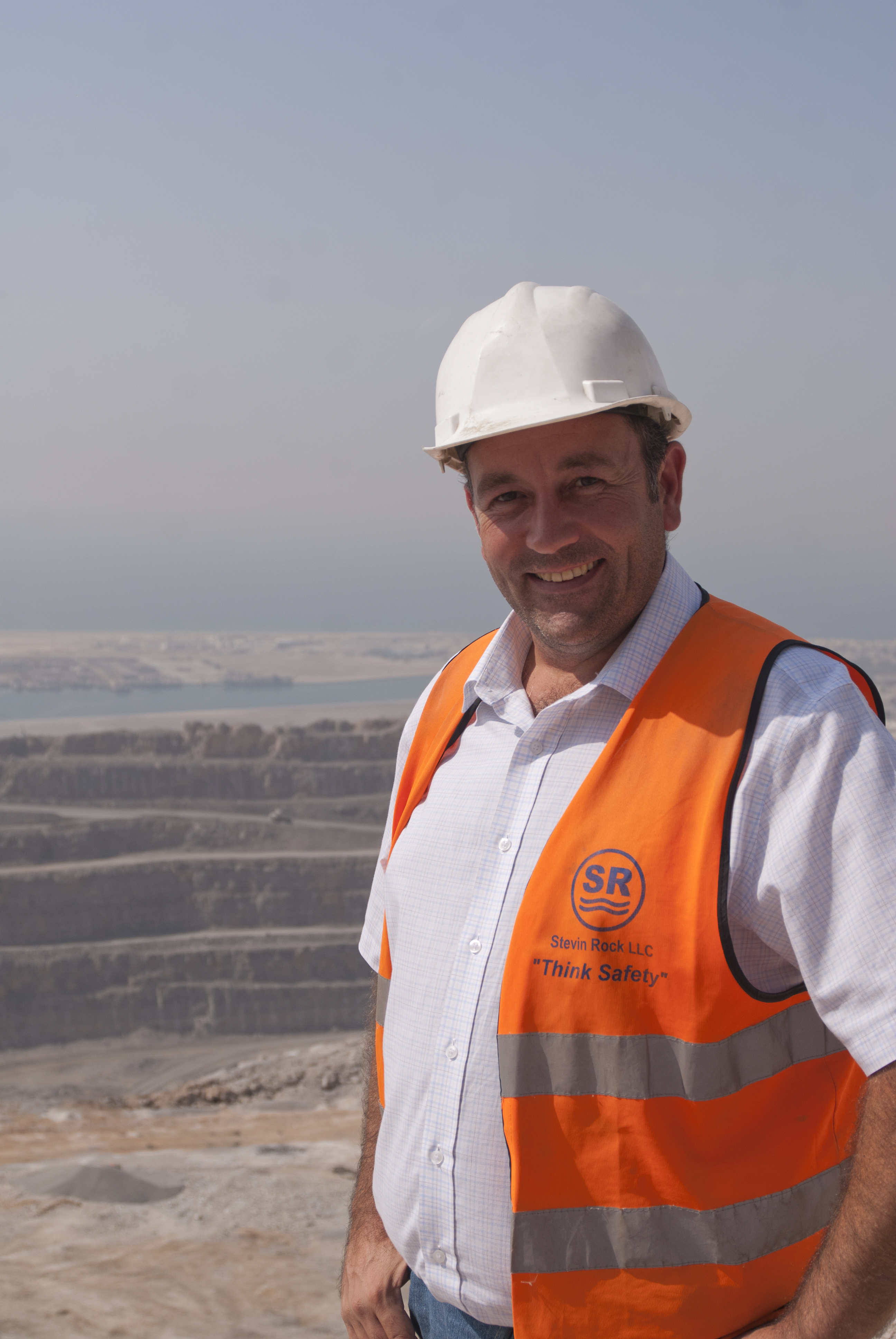
The Middle East’s largest aggregates producer, Stevin Rock, is demonstrating that improved safety management and updated equipment can result in massive productivity gains. Stevin Rock is no stranger to big numbers: the company produces more than 60 million tonnes a year from its quarry No. 2 in the Emirate of Ras Al Khaimah. Formed in 1975, Stevin is the largest producer of high-grade limestone, Gabbro rock, concrete and asphalt aggregates in the region, acquiring the adjoining Ras Al Khaimah Rock Company (RAK) in 2007 as part of its ongoing growth strategy. Dan Gilkes reports from the company’s Quarry No. 2, in Ras Al Khaimah.
Government-owned,
With around 250 pieces of mobile plant working in Quarry 2, Stevin Rock has a well-established operation, built up over many years. However when technical and operations manager Simon Turner took control of the site in the middle of 2012, he decided that the company needed to make some big changes, to both increase production and to improve health and safety within the quarry.
Fortunately those two concerns are not mutually incompatible, in fact quite the opposite is true, as not only has health and safety improved, but the company has seen a 15% rise in efficiency and an even more impressive 30% rise in productivity, with almost no additional machinery or personnel.
That’s not to say that there hasn’t been new equipment on site, in the last year Stevin Rock has invested AED 170 million (US$46m) in upgraded mobile plant. That includes the arrival of 10
The company also purchased six
Keeping tight control over such a large fleet, and achieving reliable, productive utilisation, has been key to the increase in overall productivity on site. However creating the correct organisation within the quarry has been equally vital, with Turner appointing a number of highly experienced European quarry experts to his management team.
“I restructured the management of the site with more expat supervision,” he says. “Last July I was having to spend up to seven hours a day in the quarry, now that is around one hour each day.
“But it is a continuous course of improvement. We’ve seen some big wins in terms of productivity, now the smaller things need to be assessed. This site is primarily about logistics, it’s a load and haul site. We have put the plan in place, now we need to prove it.”
In total the quarry is around 1.5km wide, from one side to the other, reaching 800m into the mountains behind. The lowest working benches are around 40m above sea level, but the 15m high benches rise to an incredible 450m above sea level as the quarry moves back into the mountain.
At any one time Stevin can have up to 20 active digging benches, with around 30km of working face in use. The company utilises computeraided design, the latest geophysical drilling and testing technology, laser pro¬ ling and has an experienced survey and blast design team. Blasting is carried out six days a week, with around 120,000 tonnes of material being blasted each day.
As mentioned, Quarry 2 relies primarily on load and haul, and Stevin has a fleet of more than 110 rigid dump trucks running at any one time, serving 9-10 prime movers at the various faces. Those digging machines can be both wheeled loaders and crawler excavators, depending on the bench shape and the material.
“We have had narrow bench issues before but we are getting past that now and making the site more suitable for wheeled loaders,” says Turner. “However we do need a mix of both wheeled loaders and excavators to operate efficiently.”
The eet of trucks feeds a range of production areas, using four Hewitt Robbins primary screens, a Lokomo K160 primary jaw crusher and two
With up to 21 production lines in operation there are a host of screens in use to size product, with numerous conveyors being used to transport the material to the base of the hill. In addition the smaller rigid trucks carry larger blocks of stone to a rehandling site at the base of the quarry.
From there material is loaded using the HD325s onto sea-going barges in the harbour. The barges have an average capacity of 10,000 tonnes, though can carry as much as 25,000 tonnes of limestone for export. Stevin can load up to 800 tonnes per hour into the barges with as many as seven berths in use at any one time.
To give an idea of the scale of the operation, a 50tonne Caterpillar 988H is used to stockpile the stone on the barges once it has been tipped by the trucks.
As part of Turner’s reorganisation of the site, Stevin is about to move two of its main primary crushers from their current position 60m above sea level, right up to a new site at 185m high. The company will then install a further 3km of conveyors to move material down the site to secondary crushers, rather than running it down in dump trucks.
“We have a plan to spend AED30m (US$8.1m) this year on conveyors,” says Turner.
RIGID DUMP TRUCKS
38 x Terex TR100
20 x Terex 3311/33100
12 x Caterpillar 777G
16 x Caterpillar 769D
20 x Caterpillar 769C
4 x Caterpillar 772G
30 x Komatsu HD325
CRAWLER EXCAVATORS
4 x Komatsu PC800
6 x Komatsu PC400
6 x Caterpillar 390
2 x Caterpillar 385
6 x Caterpillar 345C
WHEELED LOADERS
2 x Caterpillar 992K
6 x Caterpillar 992C
2 x Caterpillar 990
36 x Caterpillar 988H
4 x Caterpillar 980H
2 x Caterpillar 980G
2 x Komatsu WA600
MAINTENANCE
Dozers/graders
4 x Caterpillar D9R
2 x Caterpillar 14M
CRUSHING/SCREENING
4 x Hewitt Robbins primary screens
2 x Lokomo K160
2 x Metso C160
Various Metso C140 and C125
Kleemann SNH20 and 1630
DRILL RIGS
9 x Sandvik DX700Unusually for such a large operation, Stevin Rock runs a zero waste site, with literally everything that is excavated being used in the construction supply chain. With a scalpings ratio of just 17%, which is sent to cement production in five cement sites near the harbour, most of the limestone is sold for marine use. The core material is a 1-1,000kg limestone product that is used for island construction. In addition larger sections of stone are removed and sold in 0.5-6 tonne blocks as marine armour. In 2012 9.75m/t of this armour was used to protect islands in the oil fields of Abu Dhabi and Stevin produced more than 350,000tonnes of armour in January of this year alone.
Before the global economic crisis hit in 2008, the quarry at Ras Al Khaimah had been producing around 62m/t of material. By the end of 2012 the combination of Stevin and RAK was once again exceeding that production level. The site now has a production capacity of up to 10,000tonnes/hour and is currently producing up to 85,000tonnes per day of saleable material.
To further increase production within the quarry the management team has been analysing every aspect of the operation.
“We’ve done a lot of time cycle analysis to see where the holdups were. We’re also looking at excessive truck idling and correct positioning for maximum efficiency. We look at everything from an efficiency point of view now,” says Turner.
Nowhere is that focus on ef¬ficiency clearer than in the running of the mobile plant fleet. “We operate with a target of over 85% utilisation, which we are achieving on the working fleet,” says Turner.
“We do most of the maintenance ourselves, within manufacturers’ recommendations. We use a government lab for in-house oil monitoring and we change engines at planned intervals.
“Currently our plan is to change one HD325 engine per month with Komatsu and we plan to change one engine a month with Caterpillar too. The Caterpillar machines that we have just purchased have been taken on the basis of a guaranteed 90% availability, so Caterpillar has put its own people on site full time.
We have Komatsu engineers here too and we would very much like to have Terex people on site as well. It’s under discussion at the moment.
“One of the biggest challenges with the new equipment is electronics, which is why we have gone down the Product Link route with the new Caterpillar machines,” says Turner.
“Having the new trucks has certainly helped in our understanding of maintenance of the new systems too.” With so much new equipment on site, Stevin is also calling upon manufacturers to assist with its ongoing operator training policy. The majority of the firm’s operators come from India and live in a camp on the site. Relative inexperience and a language barrier can be concerns when starting out in the quarry.
“We are trying to improve our operator competency through proper training and dealer support,” says Turner.
This has been particularly important with the increasing reliance on retarders in new trucks, rather than operators wearing out service brakes on the downhill haul. Perhaps contrary to the general idea of increased production, Turner and his team are having to slow some of the drivers down, even turning to fines as a way of controlling top speeds within the quarry.
“We’re also taking tyre management very seriously as it is a massive cost of ownership issue,” he says.
It is easy to see why this is vital, in a country where daytime temperatures can reach up to 50degrees C in the summer months. Even hydraulic hoses have to be speci¬fied to withstand such tough operating conditions.
He is taking training and health and safety matters further though, initiating regular Safety Days within the quarry where all operatives will undergo training to ensure that safety standards are constantly being improved. There is still plenty of work to be done within Quarry 2, but Turner is happy with the progress that has been made.
Certainly Stevin Rock’s owners must be delighted by the improvements in efficiency, productivity and output. The good news is, that this is just the start.