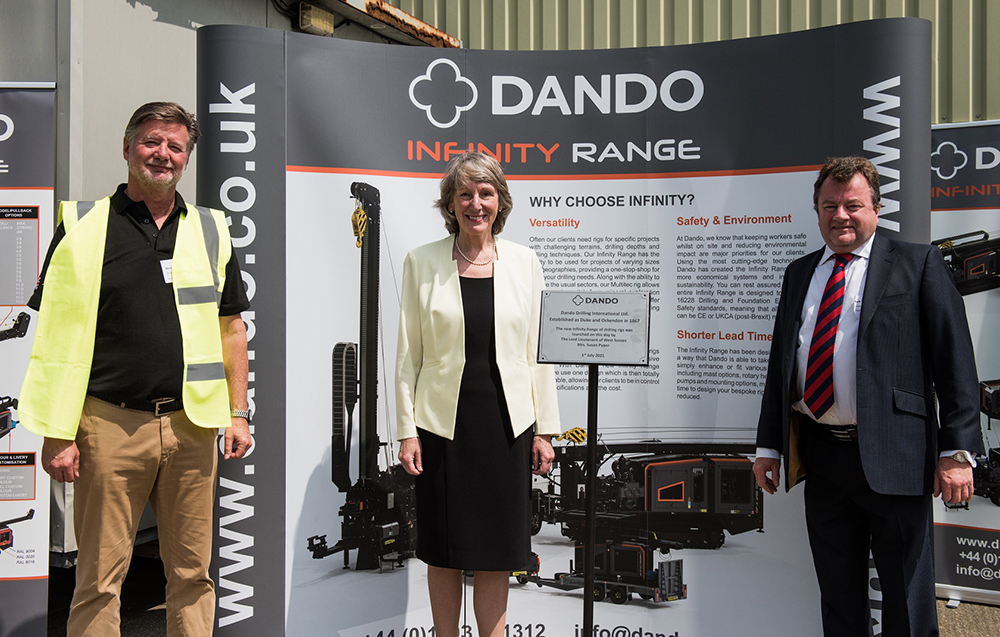
UK-based Dando Drilling International has launched its new Infinity range of drilling rigs.
The range offers high-quality drilling rigs for the mineral exploration, water well and geotechnical drilling sectors. Infinity products use a modular rig design which allows Dando to create bespoke rigs for its clients. The new rigs allow multiple variations, including the mounting, engine size, and various auxiliary equipment options.
Along with the ability to service the key sectors, Dando says its Infinity range offers a new series of Multitec rigs which allows customers to service different drilling sectors through the simple change of hydraulic components.
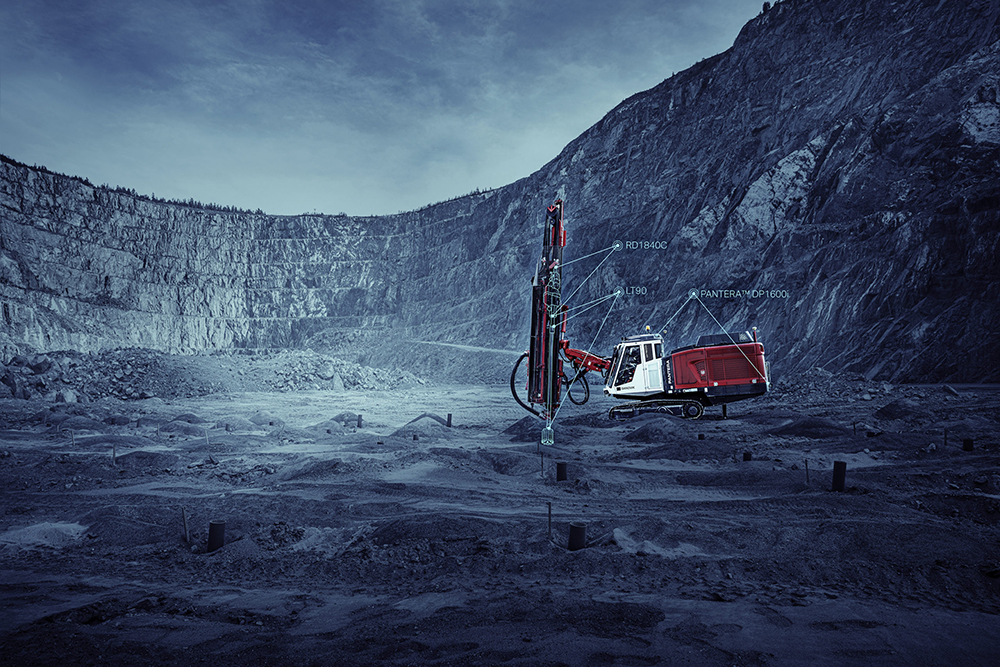
Dando’s Infinity drilling rigs were designed with three main principles in mind; versatility, shorter lead times and cost efficiency, while improving safety and reducing environmental impact.
Contractors and companies often need rigs for specific projects with challenging terrains, drilling depths and drilling techniques. Dando’s Infinity range is said to be well suited for projects of varying sizes and geographies, providing a one-stop-shop for any drilling needs. The range also includes new Sonic rigs and various rod-handling options, further providing customers with the ability to meet their demanding requirements.
The Infinity range is designed to allow Dando to take one rig and enhance or fit various components, including mast options, rotary heads, engines, pumps and mounting options. The company also offers product personalisation through paint customisation. The range also incorporates the latest engine designs and offers Stage V engines options for all machines.
Mark Jones, managing director of Dando Drilling International, said: “I am delighted to introduce Infinity range, created by our brilliant team of designers and engineers. The industry-leading design was created with our customers in mind, offering versatility, cost efficiency and shorter lead times. With almost infinite permutations, Dando’s Infinity range offers truly bespoke rigs.”
Sandvik Mining and Rock Solutions showcased the components of its latest Top Hammer XL system at the MINExpo International 2021 held in Las Vegas from September 13-15.
The company says the top hammer drilling innovation, designed for surface mining and large-scale quarry customers, offers a faster, more fuel-efficient and more cost-effective way to drill holes 140 to 178mm (5 ½ to 7 inches) in diameter. The components of the system – a new Pantera DP1600i drill rig, new RD1840C rock drill and new LT90 rock tools – are all optimised to work together seamlessly for exceptional drilling results.
Sandvik says that the system offers the benefits of top hammer drilling technology as a viable alternative to down-the-hole (DTH) drilling, on a much larger scale than before.
The Top Hammer XL drilling system expands the hole-size range of top hammer drilling to up to 178mm (7 inches) and provides a faster and more fuel-efficient drilling method. It is part of Sandvik’s commitment to use engineering and innovation to make the shift that will drive safer and more sustainable business. In addition to excellent drilling results, Sandvik says it offers an effective solution to reduce fuel consumption and, ultimately, CO2 emissions. The manufacturer adds that this more fuel-efficient yet productive drilling method can help its customers grow their business in a more sustainable way.
The Top Hammer XL system originates from the Sandvik facilities in Sandviken, Sweden, and Tampere, Finland, where all the components have been designed and manufactured. The components are designed to work seamlessly together and provide smooth operation and a highly productive system with optimum drilling results.
“A key asset of the Top Hammer XL drilling system is that all three main components – the drill rig, rock drill and rock tools – have been reviewed, redesigned and mutually optimised,” says Jukka Siltanen, product line manager, rock drills at Sandvik Mining and Rock Solutions.
The company says the efficiency of the new Top Hammer XL drilling system stems from the three components. The proven carrier offers a solid base for the extremely powerful rock drill that generates an optimum pulse for the effective tooling system, which in turn transfers the high-energy shock wave with minimum losses to the rock.
Sandvik says the Top Hammer XL system has been thoroughly tested and proven in several controlled field tests by drilling more than 100,000m in challenging rock conditions. The test results in the given conditions show a 50% reduction in fuel consumption, 25% reduction in total drilling costs and 15% increase in productivity compared with the DTH drilling method.
Pantera DP1600i is the newest member of the Pantera DPi series family of intelligent top hammer drill rigs, characterised by high penetration rates and advanced automation options for data-based fleet management and drilling performance optimisation. Designed for large-hole-size drilling, Sandvik says the Pantera DP1600i, with its practical intelligence and support for higher-level automation solutions, is ideally suited for production drilling in large quarries or open-pit mines.
The new Pantera DP1600i is based on the proven Pantera DPi series platform, with upgraded key components to meet the needs of the Top Hammer XL system. Together with the powerful RD1840C rock drill and robust LT90 rock tools, Sandvik says the end result is extreme capacity for a larger hole size, without increasing the actual physical drill-rig footprint. Pantera DP1600i can be customised with a variety of options to meet special requirements.
The Pantera DP1600i drill rig is available with Tier 3 and Stage 5 engine emission versions.
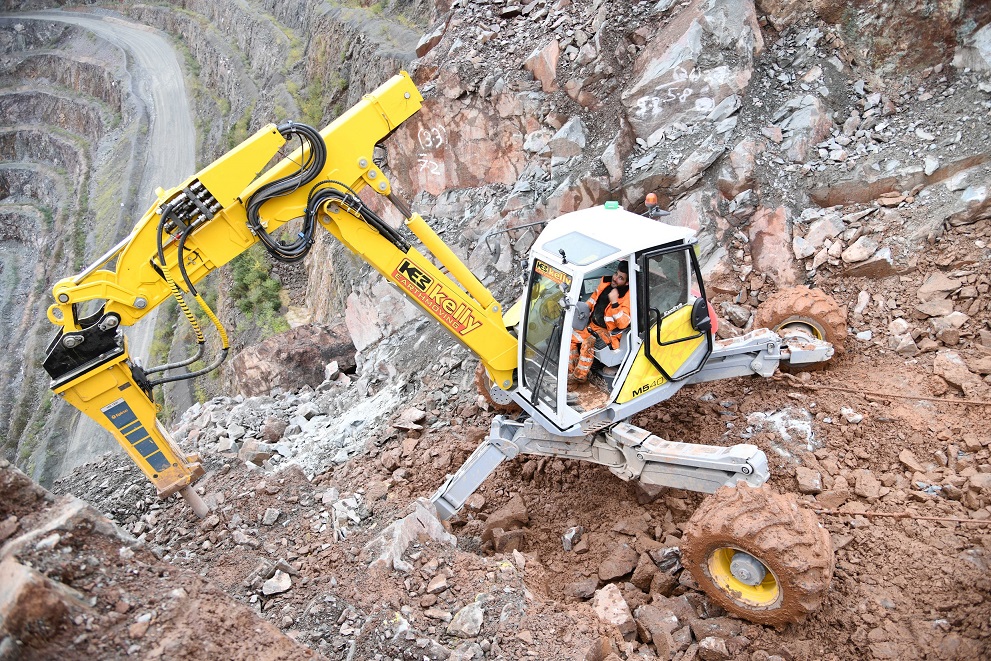
The new RD1840C rock drill is designed for large-hole drilling with high 49 kW (66 hp) drilling power. Sandvik says its robust design and well-balanced long piston percussion package are made especially for demanding circumstances. The new layout of pressure accumulators maximises efficiency and minimises hose vibrations. The state-of-the-art manufacturing process ensures the required high-quality of the rock drill components. The long piston technology generates high-impact energy with optimum pulse form, optimising performance in large-hole drilling without compromising the rock tools’ service life. The geometry and physical dimensions of the new RD1840C rock drill have been optimised for the entire Top Hammer XL drilling system.
As an additional option, RD1840C will be available with the Sandvik RockPulse tool stress-monitoring system later in 2021. The system offers the drill operator real-time measurement data on three key drilling parameters: drill bit response, tools load and feed level. The system measures the stress waves and guides the operator to find the right drilling parameters for the best rock contact and performance.
The LT90 rock tools are developed to match the other components in the Top Hammer XL system. The tools – consisting of a shank adapter, MF tube rods and drill bits - offer the best possible drilling dynamics and rock-breaking efficiency.
“Our patented and optimised LT90 rock tools design increases productivity, improves hole straightness and provides great coupling characteristics and a long service life,” says Fredrik Björk, product manager top hammer surface tools at Sandvik Mining and Rock Solutions. “All in all, this new shoulder-driven system with a double-pass thread gives our customers a much better drilling experience.”
The LT90 shank adapter, using high-quality steel, is designed for optimal energy transfer from the rock drill piston into the drill string and is developed in close collaboration between Sandvik’s experts on both rock tools and rock drills to ensure ideal performance.
With the new MF tube rods, developed to convey high-energy shock waves with minimal energy loss in the threads, Sandvik says its Top Hammer XL customers will get a higher rate of penetration, straighter holes and increased service life for the whole drill string.
The optimised thread design minimises stress levels from bending, and excellent coupling characteristics are seen in the double-pass thread of this tool system. Premium steel grades and heat-treatment processes further improve its durability. Sandvik adds that its patented retrac design forms the base for the LT90 drill bits, with a strong gauge row, excellent flushing, high rock-breaking capabilities and reduced hole deviation. The drill bits are available from 140 to 178mm (5 ½ to 7 inches) and can be delivered with standard carbide grades as well as PowerCarbide, depending on the rock formation.
US-based rotary drill bit manufacturer Terelion is expanding into the down-the-hole market. In addition to the existing rotary bits range, Terelion now offers the Warrior product line of DTH hammers and bits in sizes from 4 to 8 inches.
Traditionally, DTH is used for drilling up to 10-inch production blastholes in quarries and surface mines. Sandvik-owned Terelion says that being able to drill fast with minimum hole deviation in hard and fissured rock has earned DTH its popularity. It is also used for drilling pre-split and buffer holes in large surface-mining operations where production drilling is done by rotary.
“This makes our new Warrior DTH range a perfect complement for our customers, who mostly use our rotary tools in their production drilling,” says Rahul Obla, DTH product line director at Terelion.
Terelion says that introducing the Warrior DTH product line with a full range covering 4-, 5-, 6-, 7- and 8-inch hammers is a natural step for its new growth strategy.
“Our rotary drilling customers appreciate our premium product offering and committed way of doing business,” Obla says. “Now they can get their DTH tools in the same way from us as well. And of course, we address any operations using DTH also for production drilling, that seek an agile and committed tools supplier.”
Kelly Earthmoving has used an Epiroc MB 1200 hammer as part of the enabling works for the installation of a cable-suspended conveyor that will span nearly 1km at a UK quarrying customer in the Midlands.
Irish-headquartered Kelly Earthmoving says that installing the system at the quarry has required some serious advanced enabling and civil engineering solutions.
Kelly Earthmoving has a UK base in Preston and undertakes a variety of specialist work across the country. Whilst having ‘Earthmoving’ in its name, the company, headed up by Gerry Kelly, offers a more specialised service to its long-standing clients. “We can move earth, but that’s a little boring to us,” says Gary Kelly. “We move earth from places others can’t or won’t get to.”
In addition to moving awkward earth, Kelly Earthmoving also incorporates complex ground engineering into the package. The company provides bank stabilisation, piling and de-vegetation work, in addition to specialist equipment.
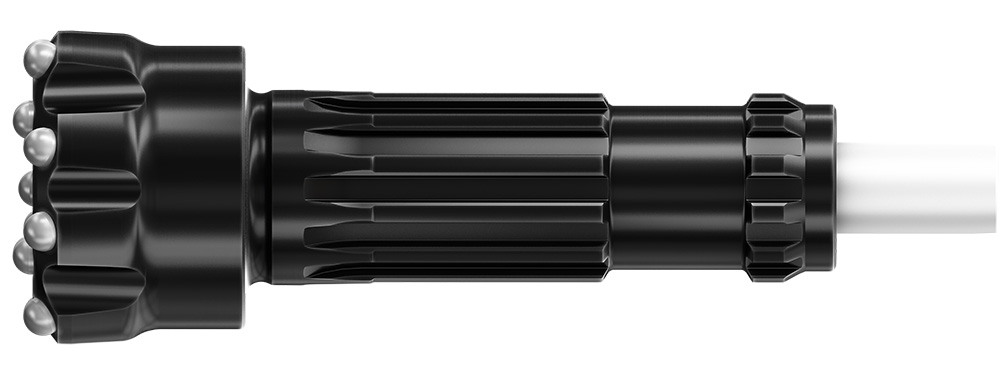
“We already undertake rock breaking and cutting for our existing clients,” Kelly explains. “But this project has seen us extracting and breaking far more rock than we have ever done on a single job. It’s been a tough but enjoyable project to be involved in but also one that has been hard on the equipment.”
The project has seen the Kelly team on site for 12 months, working on two separate sites. The terminal anchor point for the suspended conveyor system has been excavated and construction of a large concrete foundation is underway. This left the small, experienced team working almost at the top of the quarry and adjacent to an existing haul road.
The team has already created a working platform to allow the civil contractor to construct a piled wall which released the area required to construct the suspended conveyor’s deflection tower. Once completed, the Kelly team were back on site to create a 33 degree ‘slot’ through the upper quarry benches to accommodate the conveyor’s cable catenary profile.
From the upper platform, Kelly formed a slope down through the mudstone and rock to where a second working platform was broken out and levelled. At this point the team encountered the very hard rock that the quarry is famous for.
“We had a number of options for the removal of the rock head,” says Kelly. “We looked at sawing sections out, but the rock was littered with enough fractures that allowed us the quicker option of using hydraulic breakers instead.”
Whilst some of the exposed rock was easy to remove, the company found that the material below wasn’t and ended up breaking a number of hammers and countless chisels in the process.
“It was getting beyond a joke. Every couple of days we were breaking a chisel or sometimes more,” Kelly explains. “Our usual hammers were struggling with the hard rock so we decided to look at investing in something more reliable and productive to complete the job. Coyle Equipment Services has been supporting us on this project from their new, purpose-built depot in West Bromwich, so on the advice of William Coyle we used an Epiroc MB 1200 hammer as a replacement for one of our existing tools.”
He said his company has been very impressed with the Epiroc breaker’s reliability and performance in driving a path through the rock. Kelly says the 12-tonne, 157hp Menzi Muck walking excavator wields the Epiroc MB 1200 hammer with ease despite it being designed for the larger 15-26t carrier range.
“The Menzi is just a massive powerpack,” Kelly says. “It will push out over 200 litres per minute with the Powerline pump, far more than the Epiroc breaker requires.”
Lift capacity even at its full 6m-reach is over 4 tonnes which Kelly says makes the Menzi an ideal hydraulic attachment carrier. Carrying a hefty 120mm-diameter chisel, the MB 1200 delivers between 340 and 680 blows per minute which according to Kelly is more than capable of taking apart the rock they are now encountering.
Fitted with Epiroc’s AutoControl system, the hammer is able to detect pressure on the chisel. It also detects when the chisel breaks through the material to protect it from blank firing and causing potential damage to the percussion chamber.
“We’ve been very impressed with the hammer,” Kelly comments. “It’s more compact than the ones we have in the fleet, yet the performance is far better than anything we have used before. We’ve not had to change the chisel at all as the Epiroc original seems to be made of stern stuff.”
Despite having to deal with the pandemic and bad weather, Kelly says his company’s team has delivered an impressive result for the quarry’s project team. “The men and machines have performed very well on the project,” he adds. “We don’t take on ordinary jobs, we always like a challenge!”