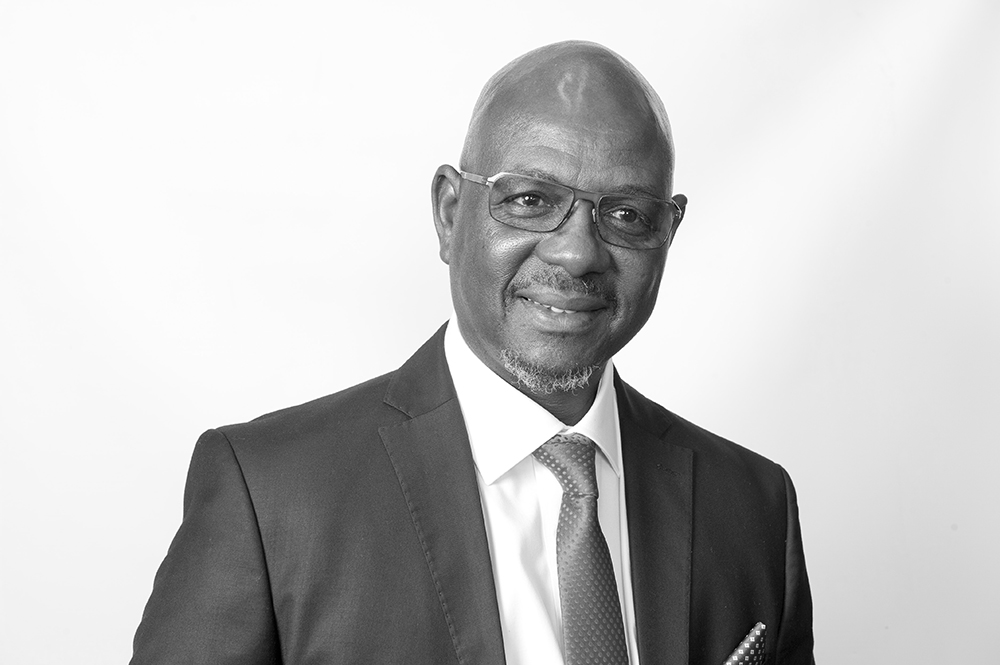
In building or civil construction, cement is the glue that binds the structure together. Yet, Njombo Lekula, MD of PPC RSA Cement, South Africa’s leading cement manufacturer, laments the influx of sub-standard products in the South African market, which are threatening the built environment and placing people’s lives at risk.
Lekula says usage of sub-standard cement has various implications that may negatively affect the sustainability of buildings and structures, thus leading to increased repair or maintenance costs, and in worst-case scenarios, resulting in injuries and fatalities due to structural failures or collapse.
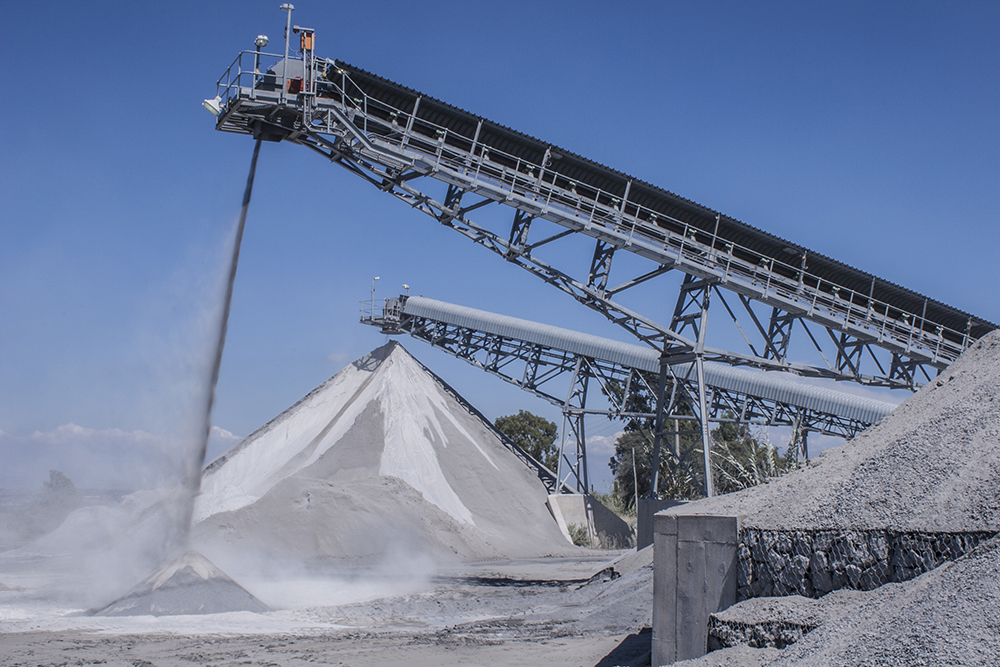
Speaking to Aggregates Business International, Lekula notes that there has been an influx of third-party cement blenders in the South African cement market in the past two years. He estimates that third-party cement blenders, also known as non-integrated cement producers, now account for more than 1.8 million tonnes of cement sales per year, in a market that is selling about 13.5 million tonnes of the country’s available capacity of 18-20 million tonnes per year.
During a normal market surveillance exercise whereby it tests competitor products for benchmarking purposes, PPC found that there was huge quality gap in some of the products in the market, which warranted further investigation. In an effort to protect the wider South African cement industry and the consumer at large, PPC appointed Beton-Lab, a South African National Accreditation System (SANAS)-accredited independent laboratory in September 2017 to prove intentional thwarting of standards by third-party blenders.
“When we realised the extent of non-conformance to standards, we decided to conduct quality checks on a continuous basis. Despite the fact that we have a very capable laboratory, which I consider to be one of the best in the African cement industry, we decided to engage the services of an independent laboratory to ensure transparency and non-bias in the results. We have been monitoring this for about 18 months and the results are shocking,” explains Lekula.
Beton-Lab’s study involved 274 samples of 14 products from 10 different companies. The report was recently released and the findings were shared with the National Regulator of Compulsory Specifications (NRCS) and the South African Bureau of Standards (SABS), largely showing continued non-performance of the cement tested.
Explaining the process and requirements, Lekula says the weights of the bags were checked and the EN strength-testing in accordance with SANS 50197 for two, seven and 28 days was performed. The SABS’ prescribed uncertainty of measurement allowance of 2.5% was applied when analysing the resultant data. The results showed the inability to produce a consistent quality product and thwarting of standards in most cases.
“Some of the products failed horrendously,” says Lekula “Firstly, the products failed on bag weight. In some instances, some of the bags were found to be weighing around 46kg, which is 4kg short of the required 50kg. That is unfair to the consumer. Secondly, we picked up products that did not meet the standard in terms of strength development.”
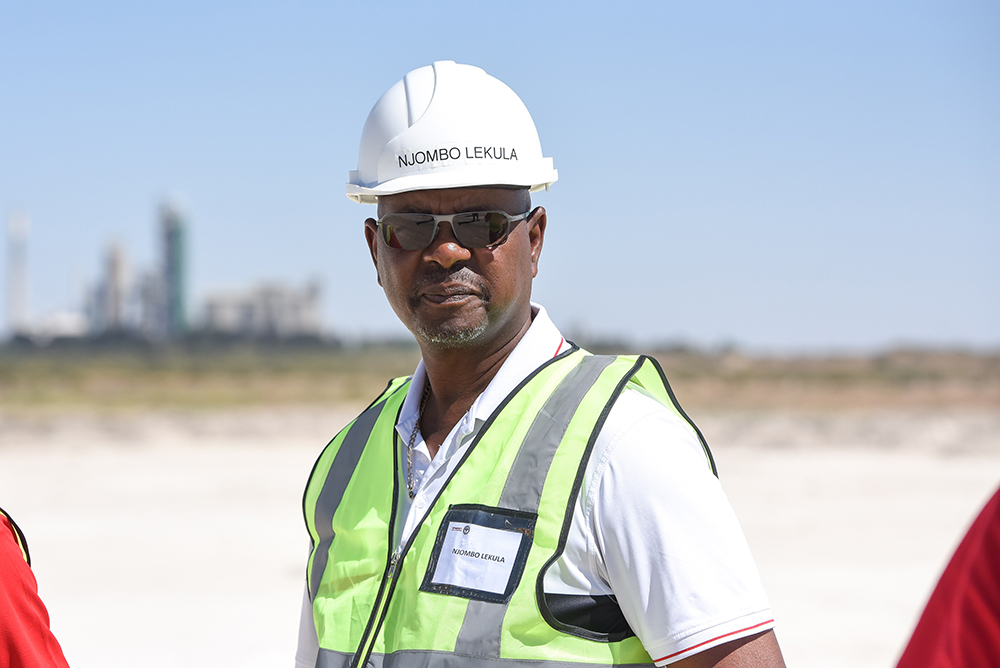
Explaining the strength-testing process, Lekula says the laboratory makes a standard cube of concrete and keeps it in a controlled condition for the prescribed two, seven and 28-day intervals. In any of those intervals, a cube is crushed to measure strength. If a product is a 32.5, for example, it means that in 28 days it should crush at 32.5 MPa. “To give an idea of the extent of the quality shortcomings, one of the products tested crushed at 3 MPa after a 28-day period,” says Lekula, adding that non-conformity of strength and weights of some products ranged from 11% to 73% of the sample set.
The third aspect of concern was the standard deviation. “When we talk about standard deviation, we refer to inconsistency in the product, where fluctuation of quality is a major concern,” explains Lekula. “The failure to conform to local standards not only has an impact on the structural integrity of buildings, but also poses a threat to possible damage of property and even loss of life should the walls come tumbling down.”
It was also found that most of the sub-standard cement products carry the SABS mark. The SABS stamp is a mark of regulatory approval, instilling trust in the product being sold and, if used in accordance with the instructions, will result in a structure that is robust and safe.
Lekula believes one of the challenges for the relevant authorities in policing the industry is that the two organisations that are responsible – the SABS and the NRCS – are seriously underfunded, which affects their capacity. “Both the SABS and NRCS should be conducting regular surveillance visits on sites to check if producers are compliant at all times. Unfortunately, the two organisations are basically funded by the levies that they collect from the SABS mark and the NRCS trade certificate, and it is not adequate for them to properly fulfil their duties,” says Lekula.
Following PPC’s findings, the results have been presented to both the SABS and the NRCS, and action has already been taken in some instances. “We know of one blender that has been shut down completely by the NRCS due to poor quality. We are also aware that another third-party blender is in the process of being shut down because of non-adherence to quality standards. The SABS is also taking this matter very seriously and is currently looking at random testing. Previously, the SABS would advise entities of dates and time of testing, which allowed companies to adjust standards for complying purposes only,” says Lekula.
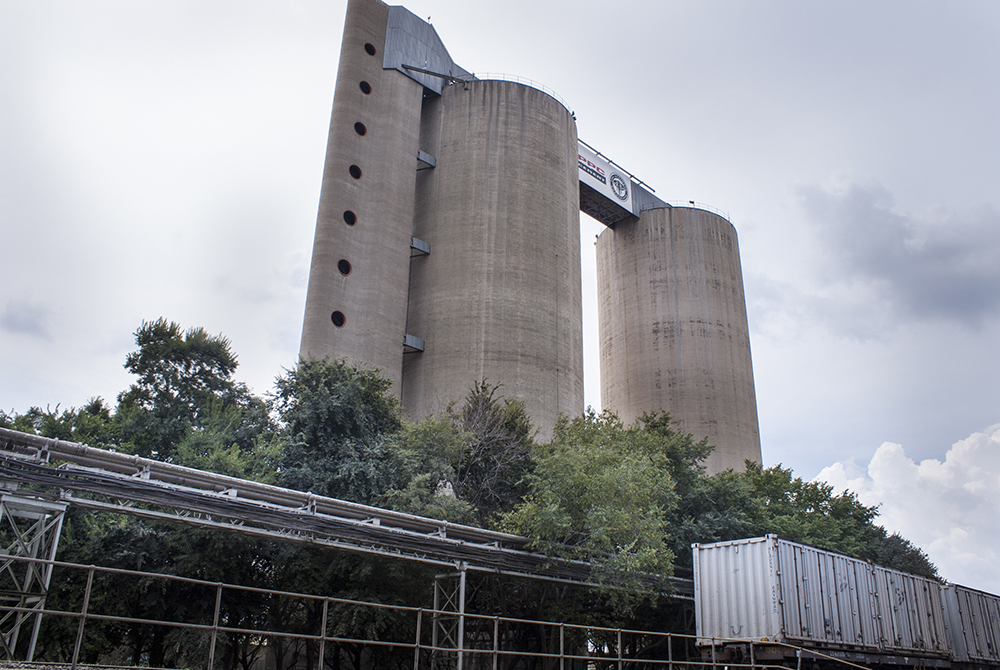
Following these actions, Lekula says there has been an improvement in the quality of the product from some of the non-integrated cement producers in recent months. However, to ensure consistent quality going forward, PPC is lobbying the South African cement industry to self-police. One of the ways of doing that is through capacitating an independent lab like Beton-Lab to randomly conduct tests on every cement producer’s product in the market to ensure sustained compliance with quality standards.
PPC believes that its actions are in the best interests of the South African consumer and the cement industry at large. Lekula says the motive to conduct this exercise was never driven by a monopolistic agenda of a large cement producer trying to “bully” small players in the market. In fact, he is of the view that it was a matter of moral responsibility on the part of PPC.
“We believe that part of our mission as a business is to better the quality of life within the communities we operate. We have a responsibility as an industry leader, and part of leadership is to always do the right thing. Keeping quiet about this non-compliance would have been irresponsible on our part. This non-conformance doesn’t only paint a bad picture on those caught on the wrong side of the law, but the cement industry at large. So for PPC, it was about protecting the industry image and the end user,” says Lekula.
More importantly, Lekula says PPC felt it had the responsibility to protect the vulnerable markets where these low-priced, poor quality cement products are mostly sold. He reasons that these products are mostly destined for price-sensitive markets like rural areas and townships. These are areas where poor workmanship is also commonplace. Poor workmanship and a sub-standard product are a recipe for disaster, reasons Lekula.
The danger also spreads to the integrity of civil infrastructure builds in the country. Lekula notes a recent trend whereby infrastructure projects are being packaged into smaller lots as a means to grow the upcoming contractor fraternity. “There is far less infrastructure development in South Africa at this point and it’s no secret that construction companies in the country are disintegrating into smaller entities. There is rapid growth of what we call ‘bakkie builders’ (medium-sized contractors) because most of the available work is in infrastructure maintenance and renovations,” reasons Lekula.
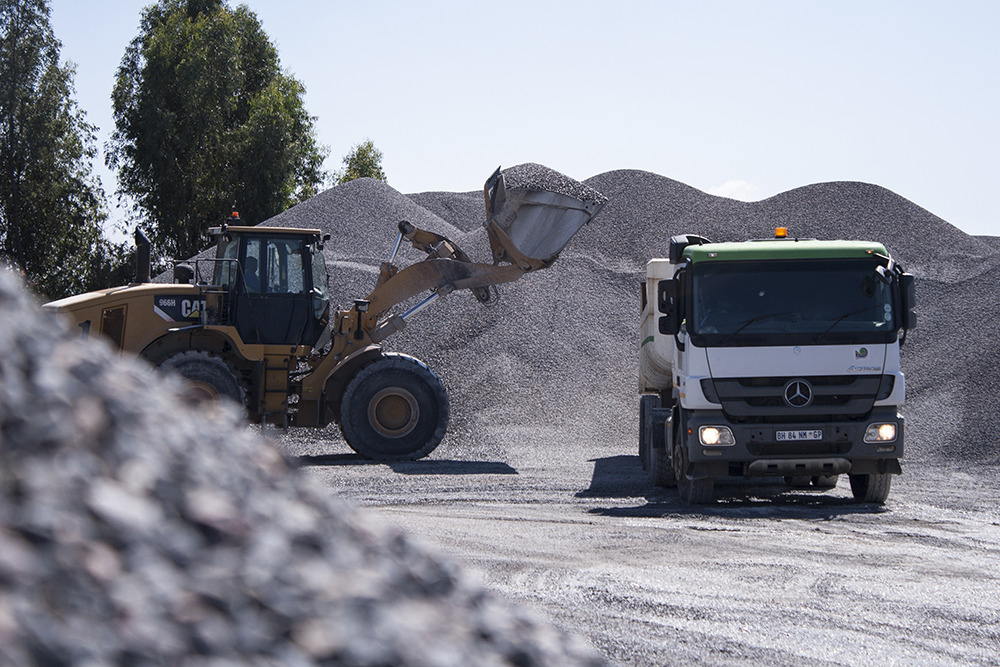
Unlike the big construction companies that had resources to check the cement products they used, the smaller companies don’t necessarily have that capacity to test their own materials, and that’s where the sub-standard cement products are infiltrating significantly. These companies also generally have an insatiable appetite for cheaper products to maximise profits, which places the country’s infrastructure builds at risk.
“The unfortunate part is that this small contractor market also accounts for a big chunk of government-subsidy housing (commonly known as RDP houses), which places the lives of people at big risk. We have already seen some of these houses collapsing in recent years as a result of sub-standard materials, and if this continues, we will see more of these disasters in future,” concludes Lekula.